Extracting forms from my photography in 10x10cm boxes
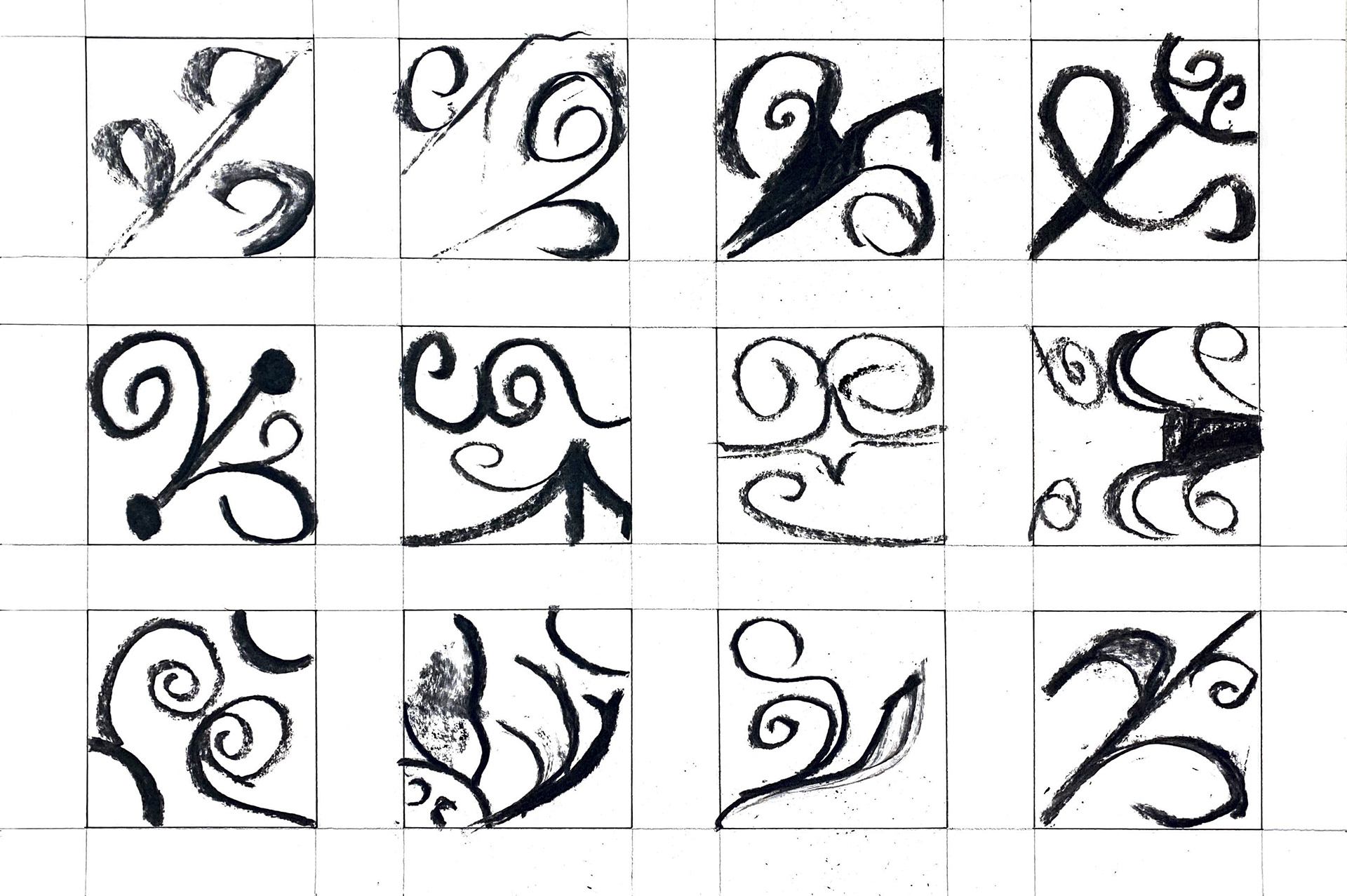
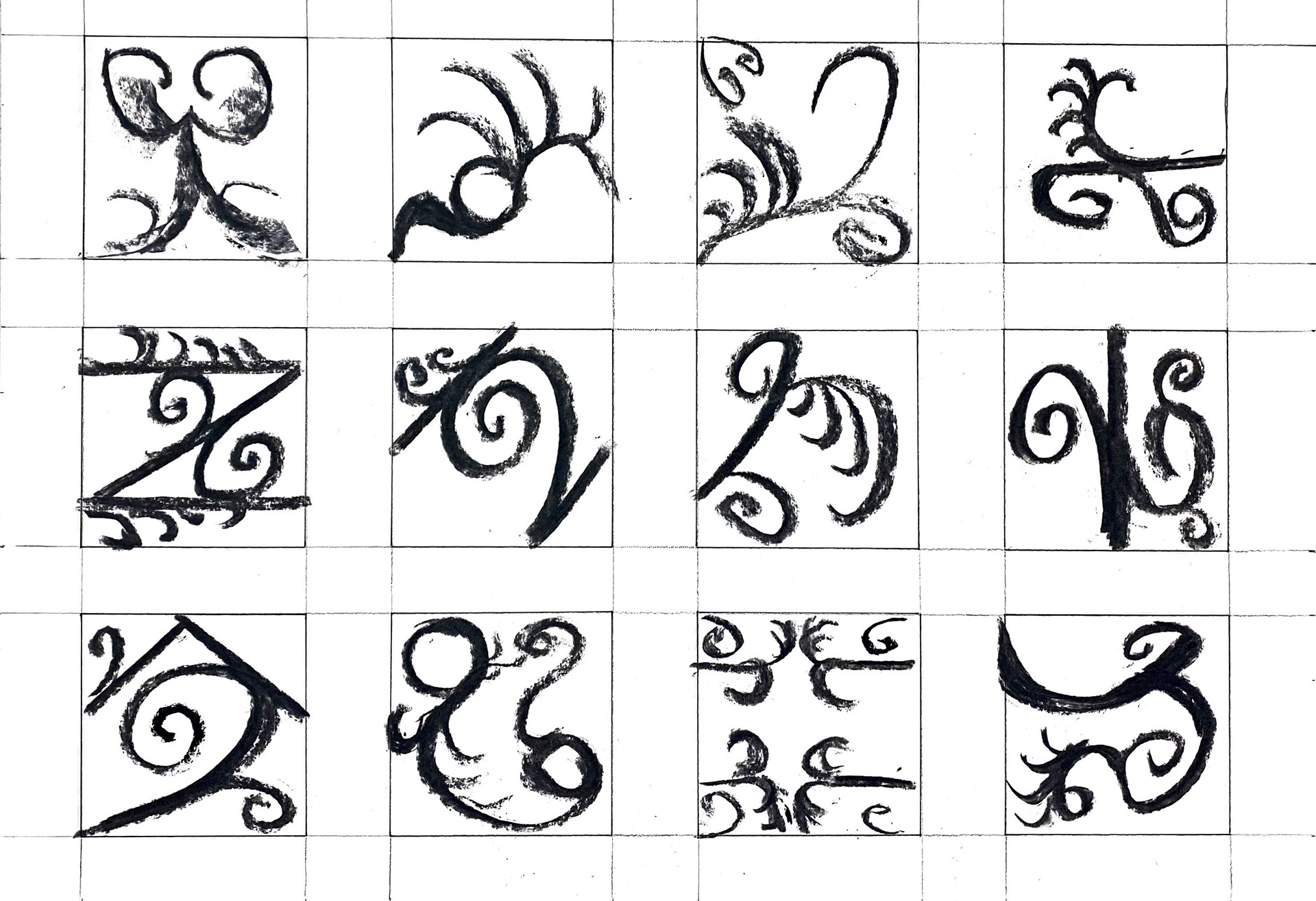
Progressing from my model box I looked at extracting forms from my photography of the iron work at the Parsonage. I wanted to explore the effect of a physical border using squares. I used a fast-twisting motion from the wrist to create fluid and natural curves with a stick of charcoal.
Experimenting with repetition, reflection, and rotation
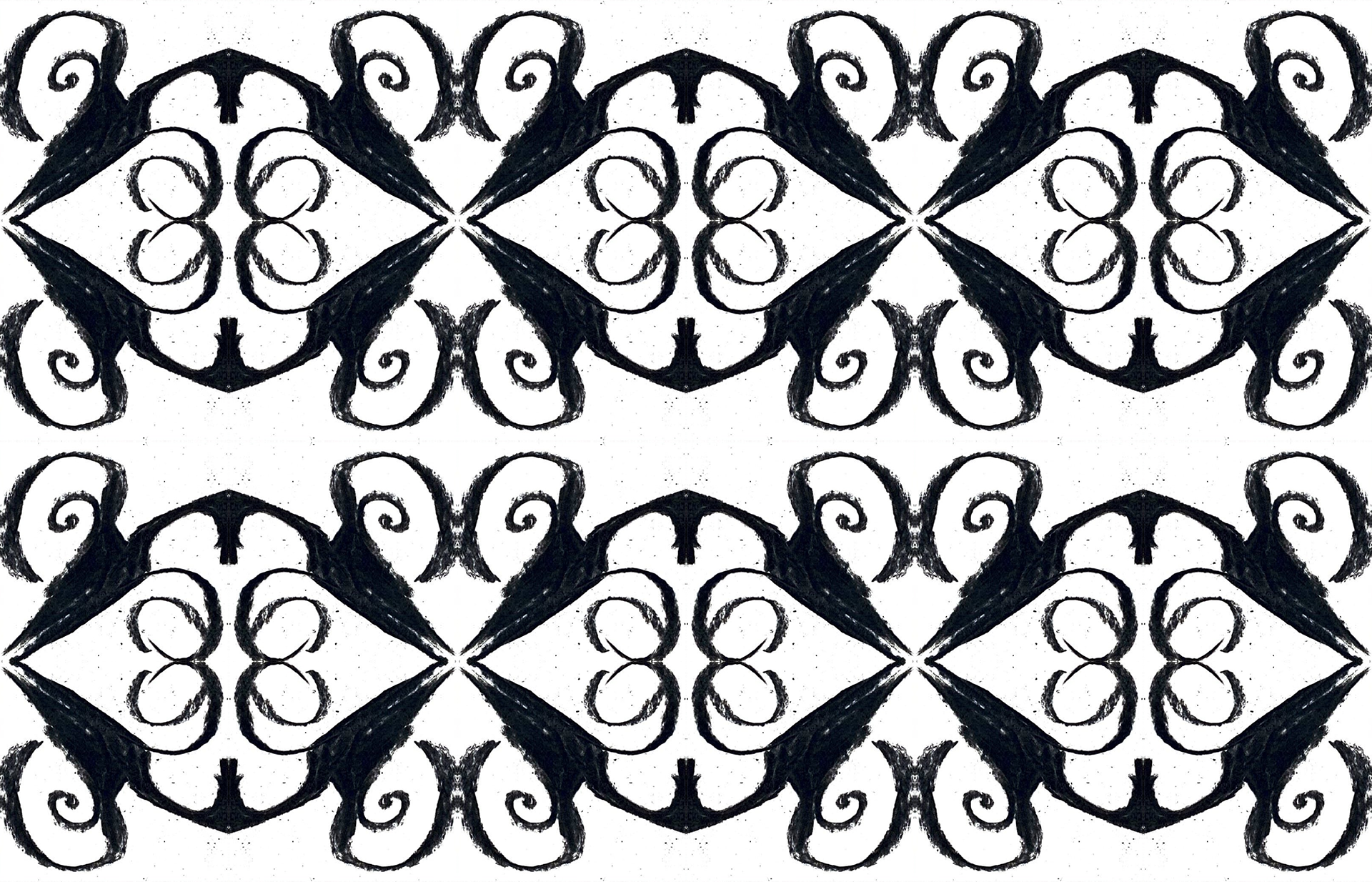
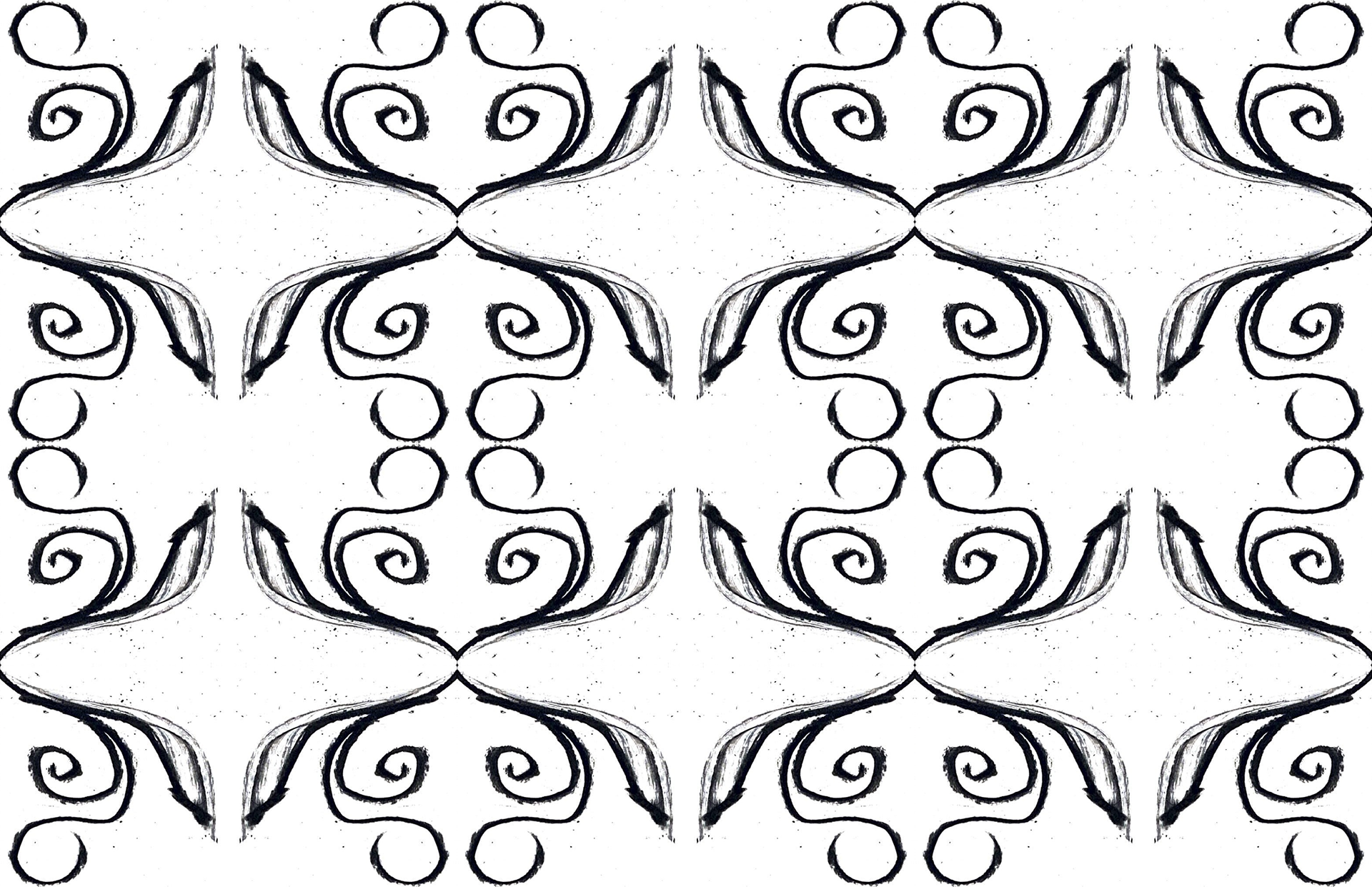
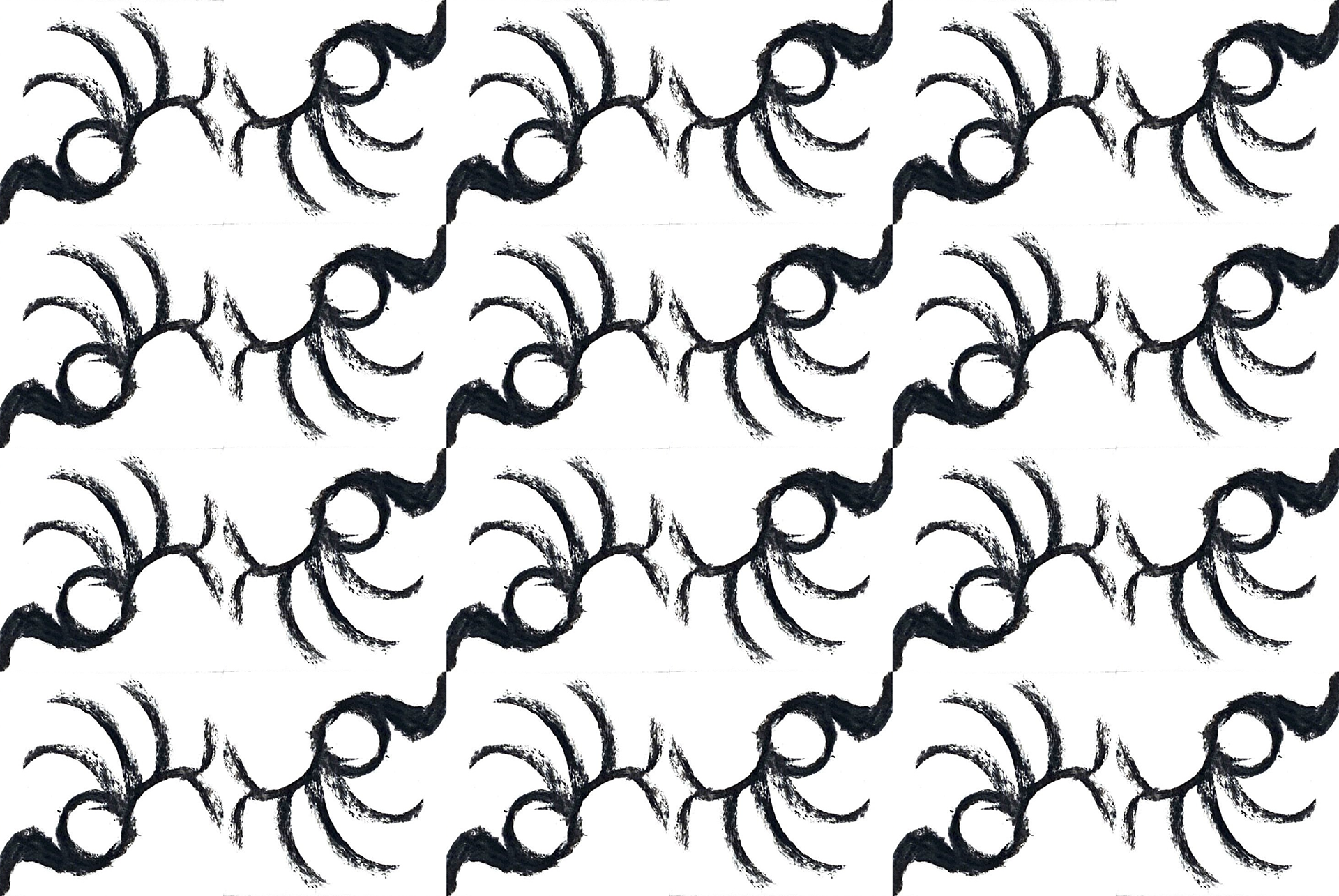
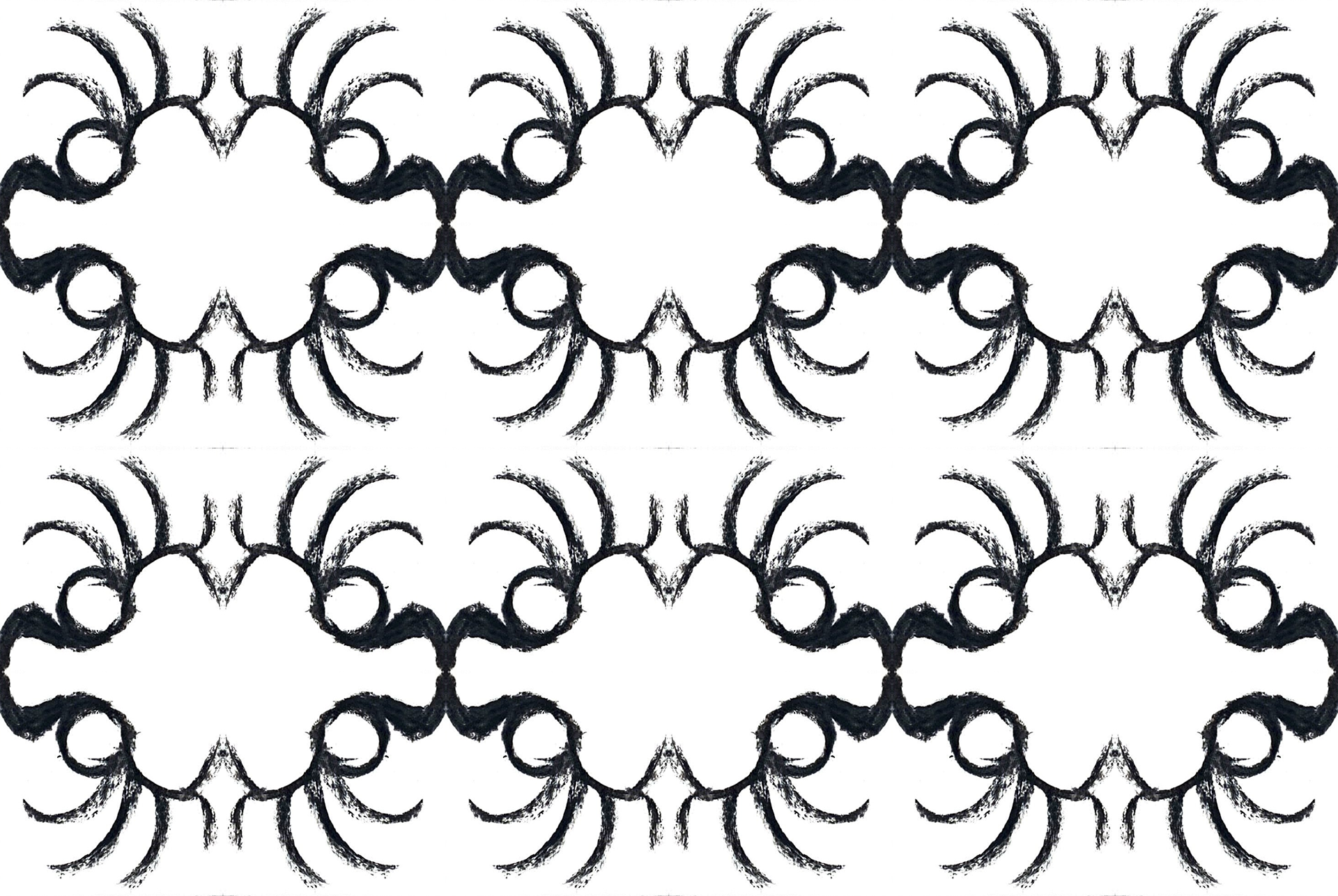
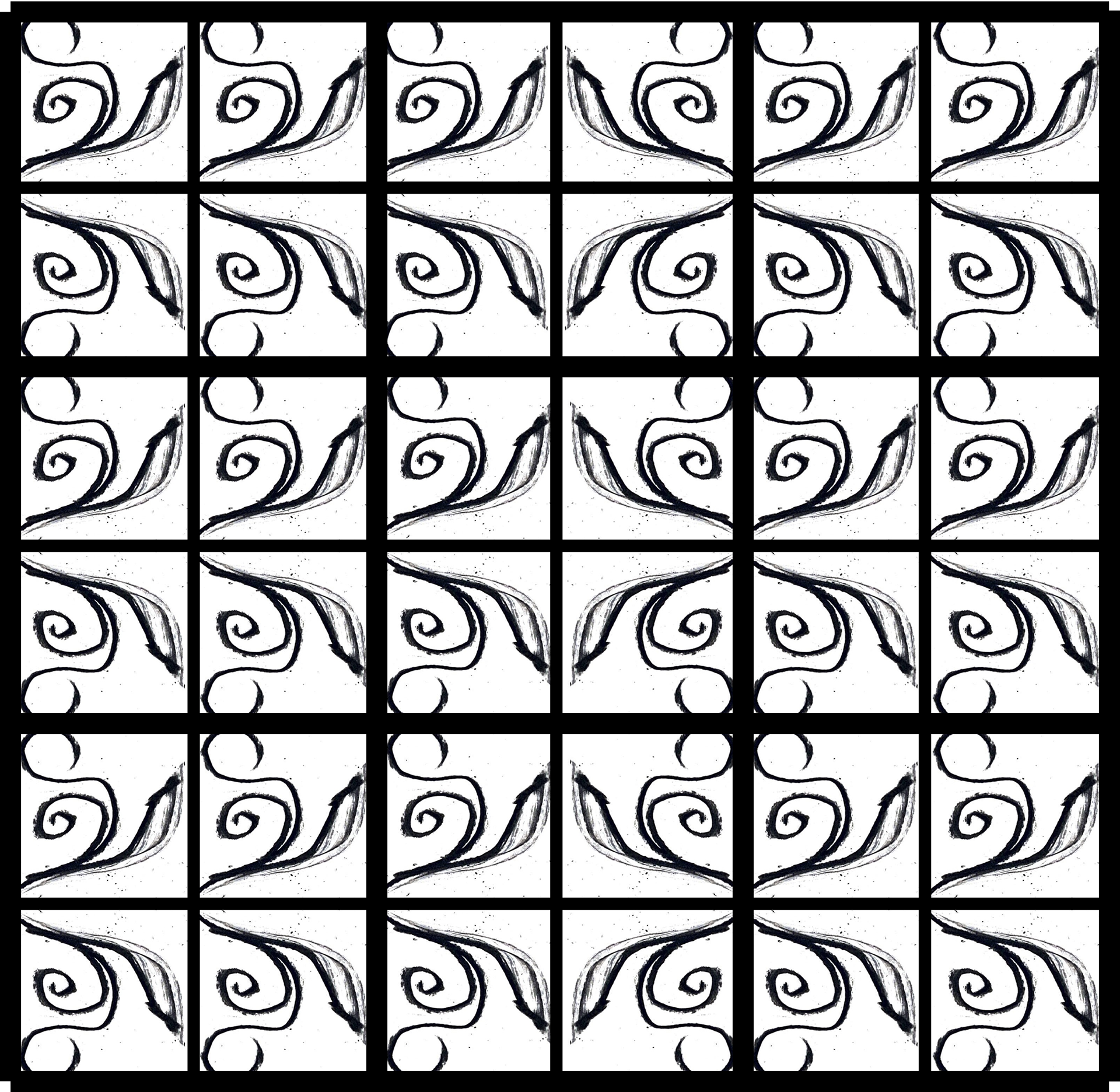
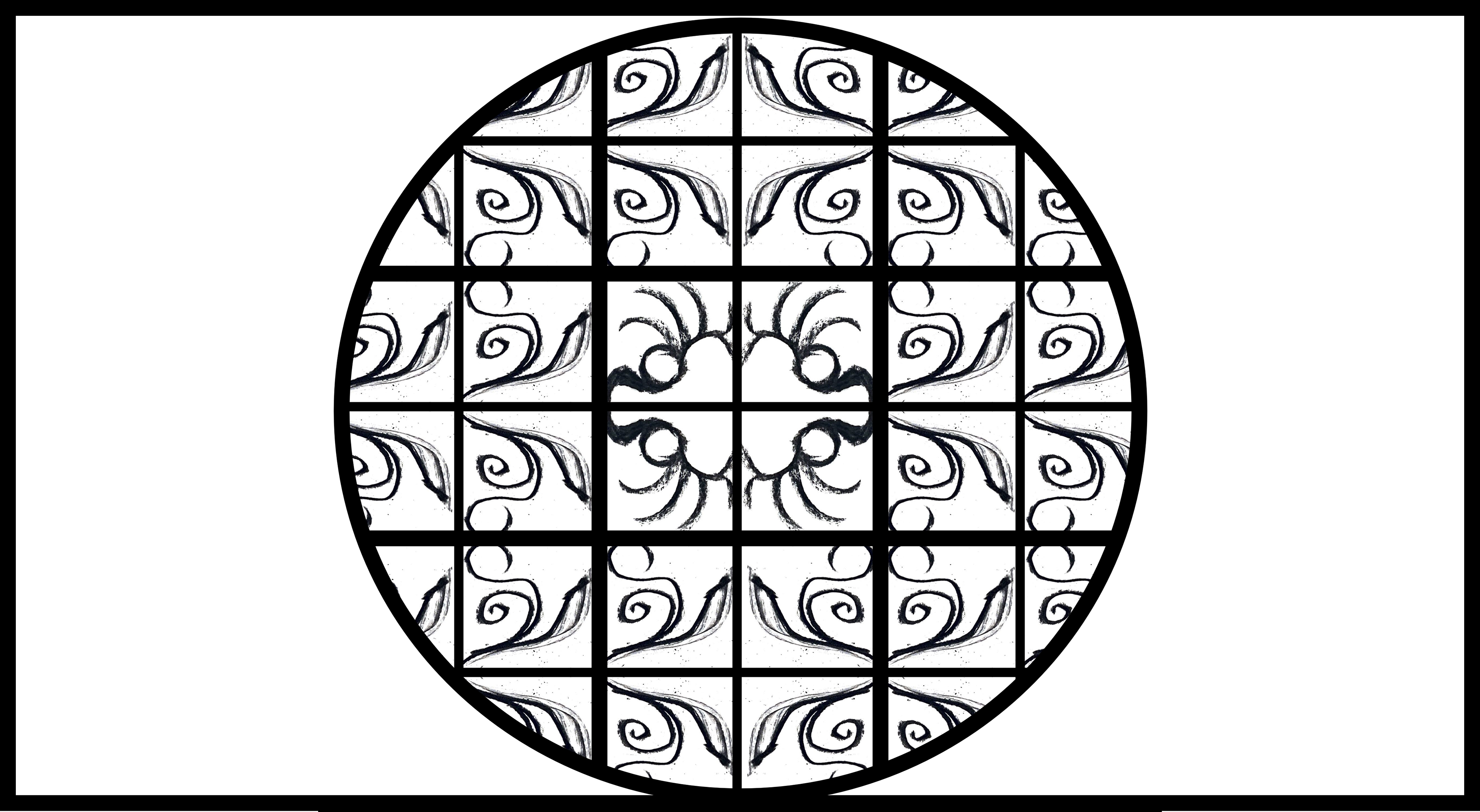
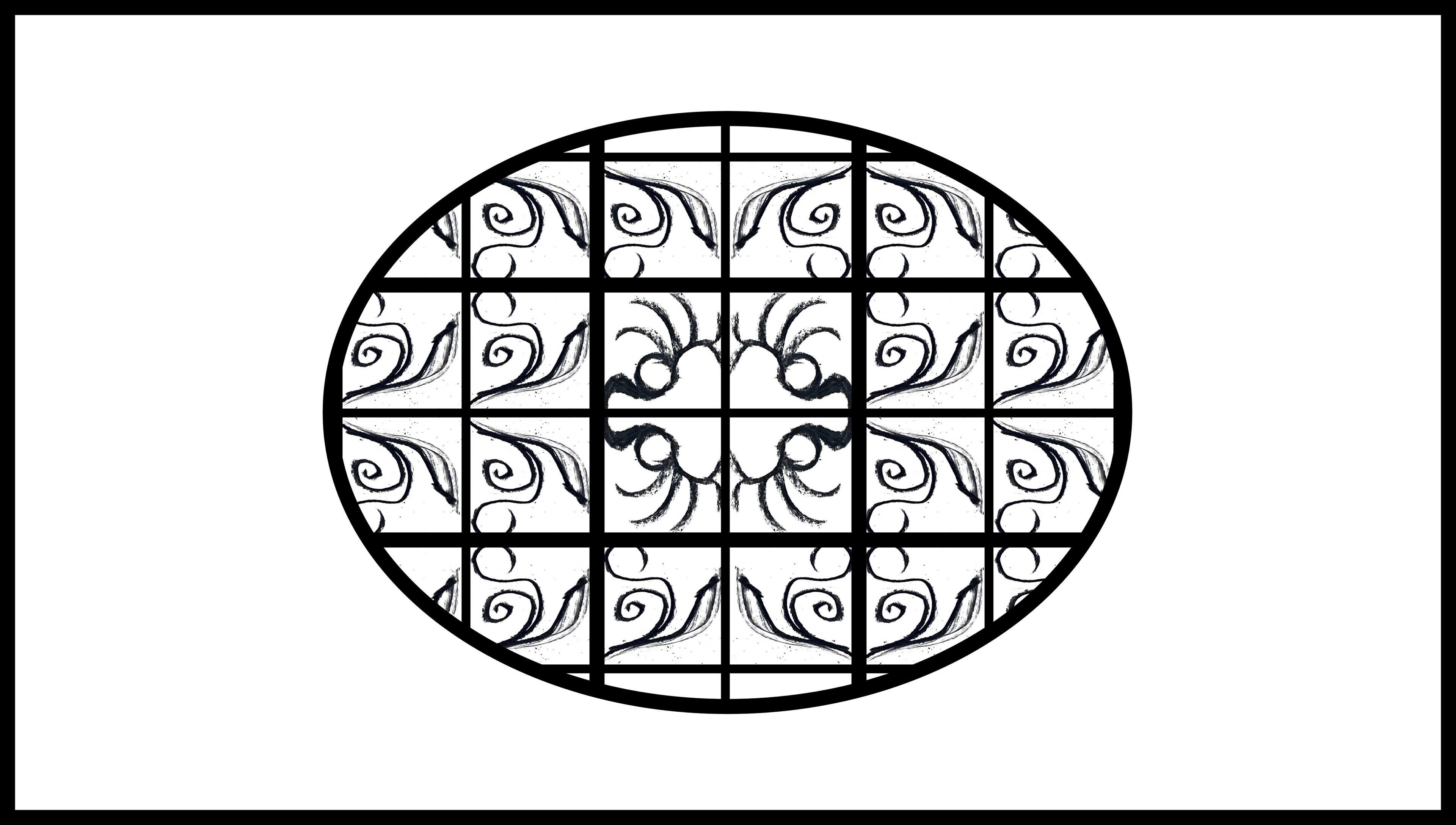
I took the most successful designs and explored rotation and reflection to create pattern. I trialled larger patterns and began to explore different shapes, broadening the constraints. Whilst making these, I started to think about how I could use the forging process using flat bar. I added in the grids to join the repeating forms together. These would need to be adjusted and scaled to allow enough room for connections such as rivets. I felt that these patterns posed too many challenges to make consistently using the forging process. Additionally, the patterns I have created lack not only purpose, but also narrative.
Testing different forms by forging
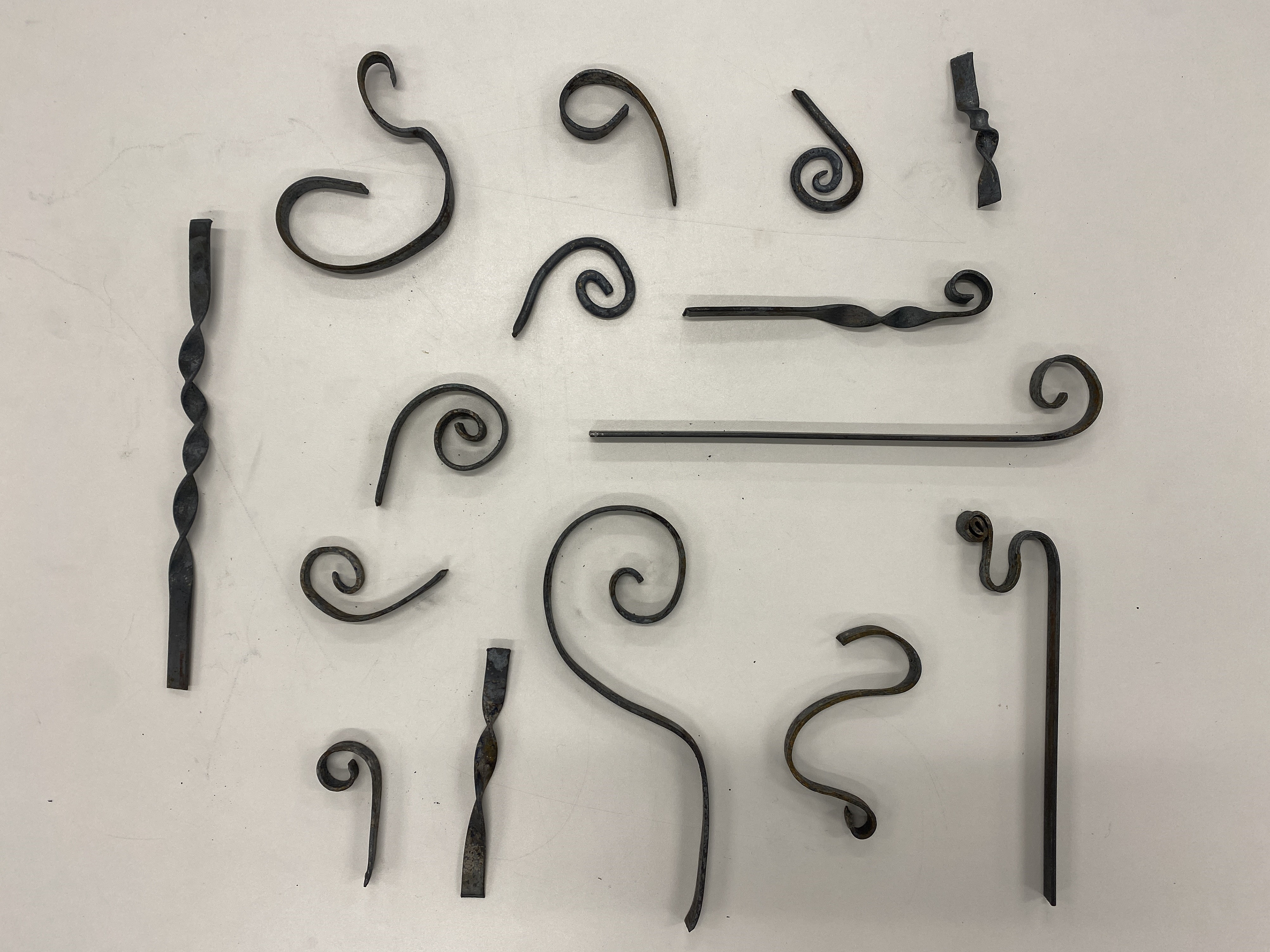
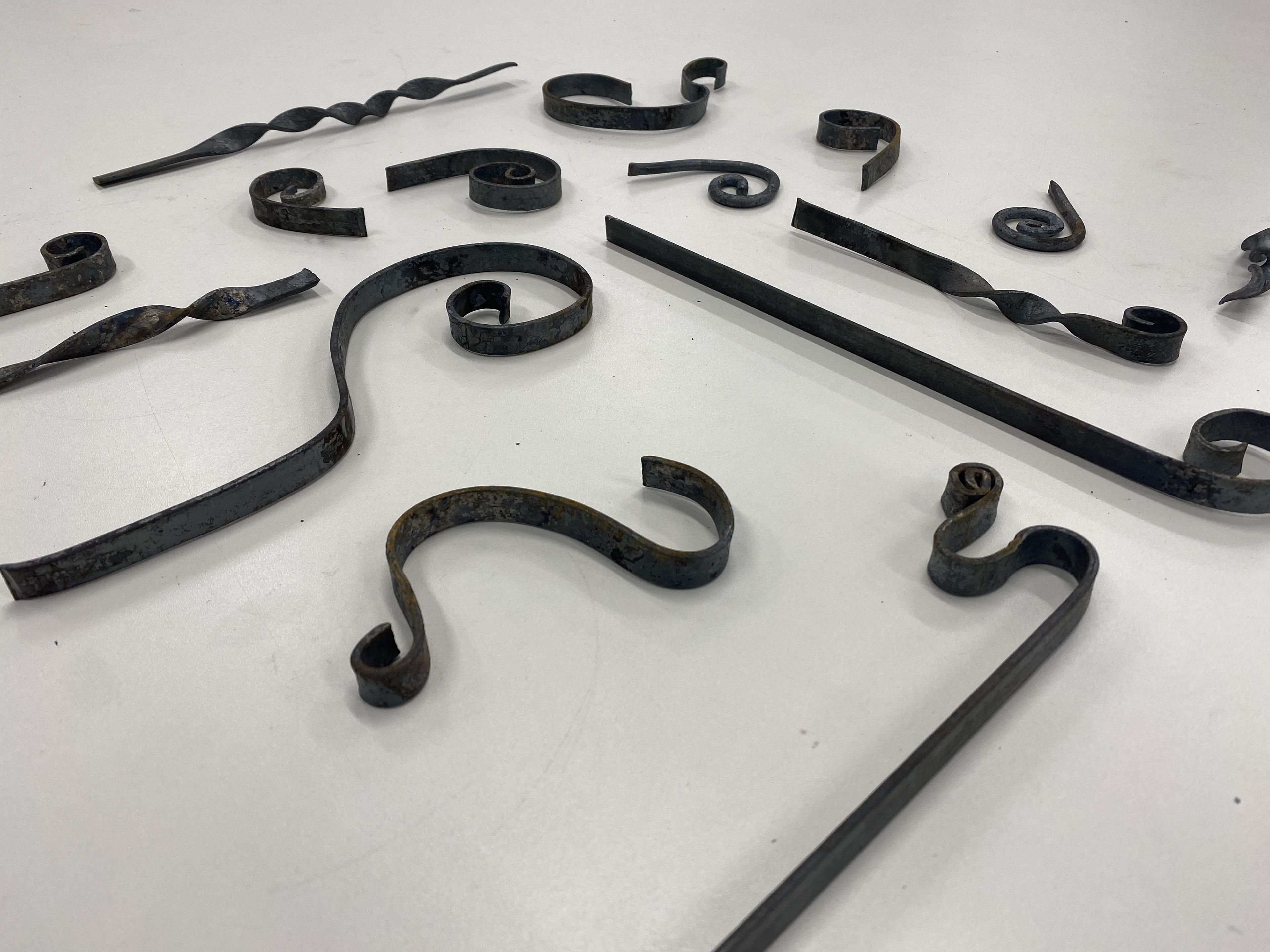
Reflecting on my previous design work I wanted to explore the possibilities of the forging process to make different sizes of scrolls using the horn of the anvil.
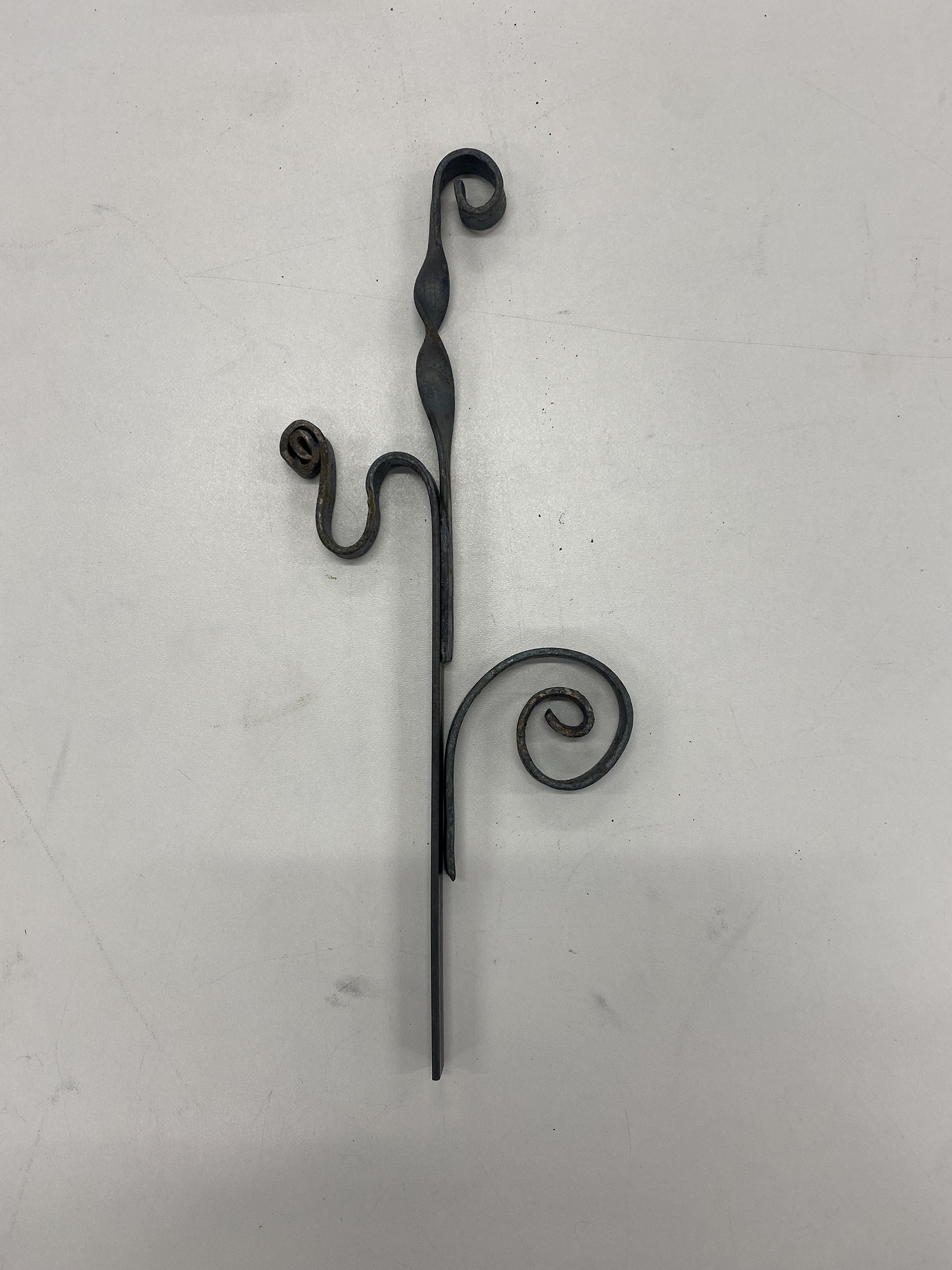
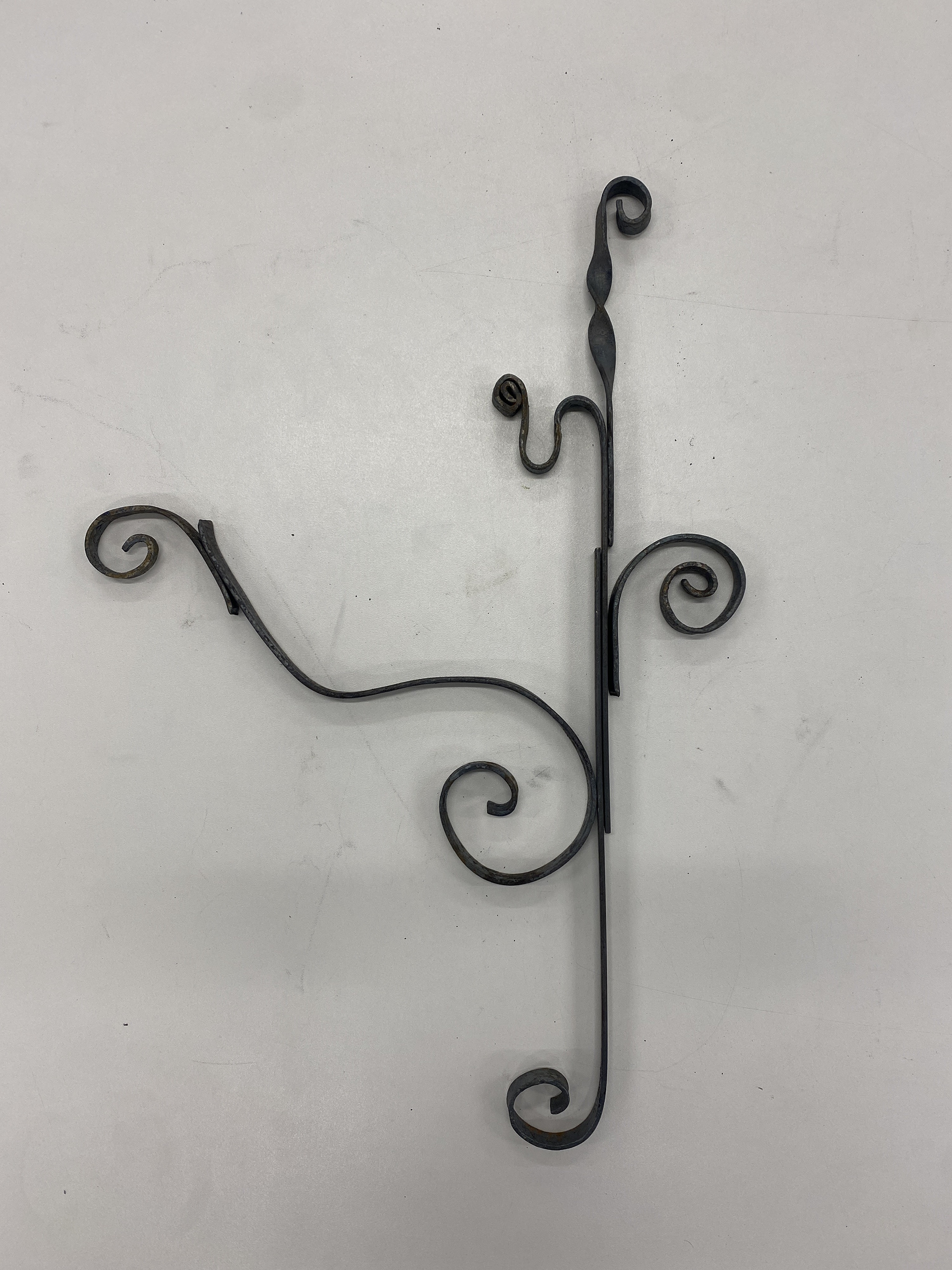
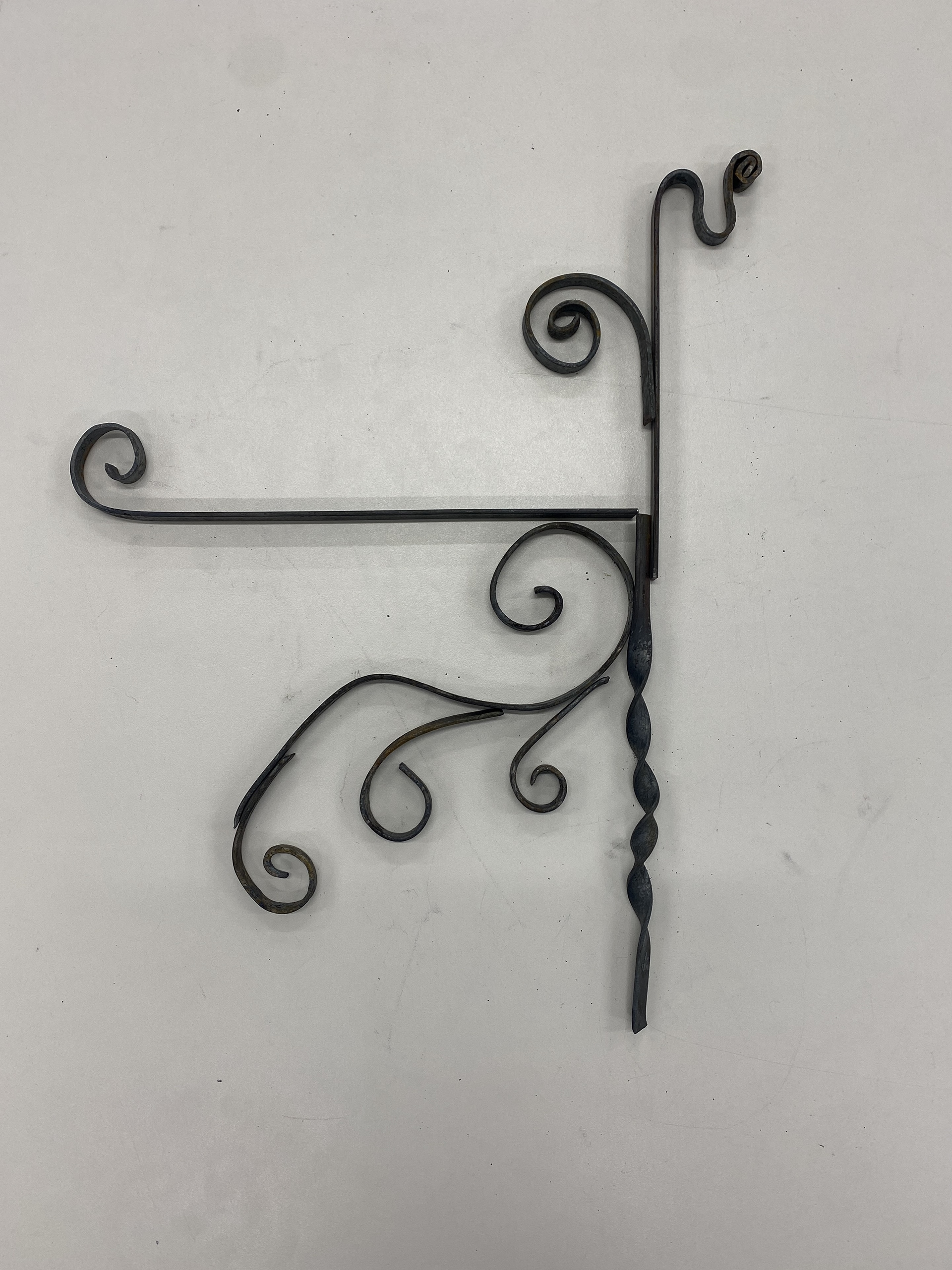
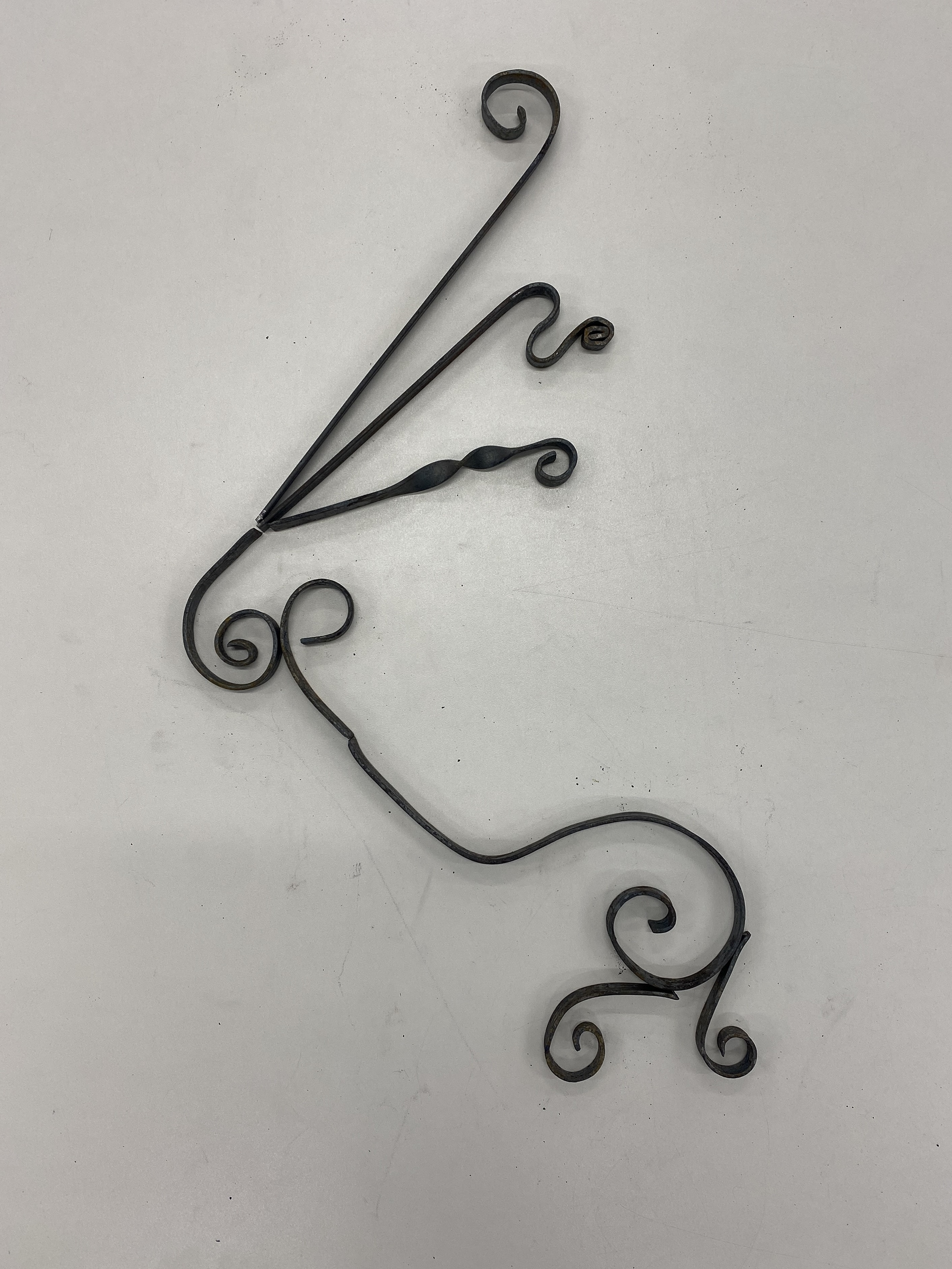
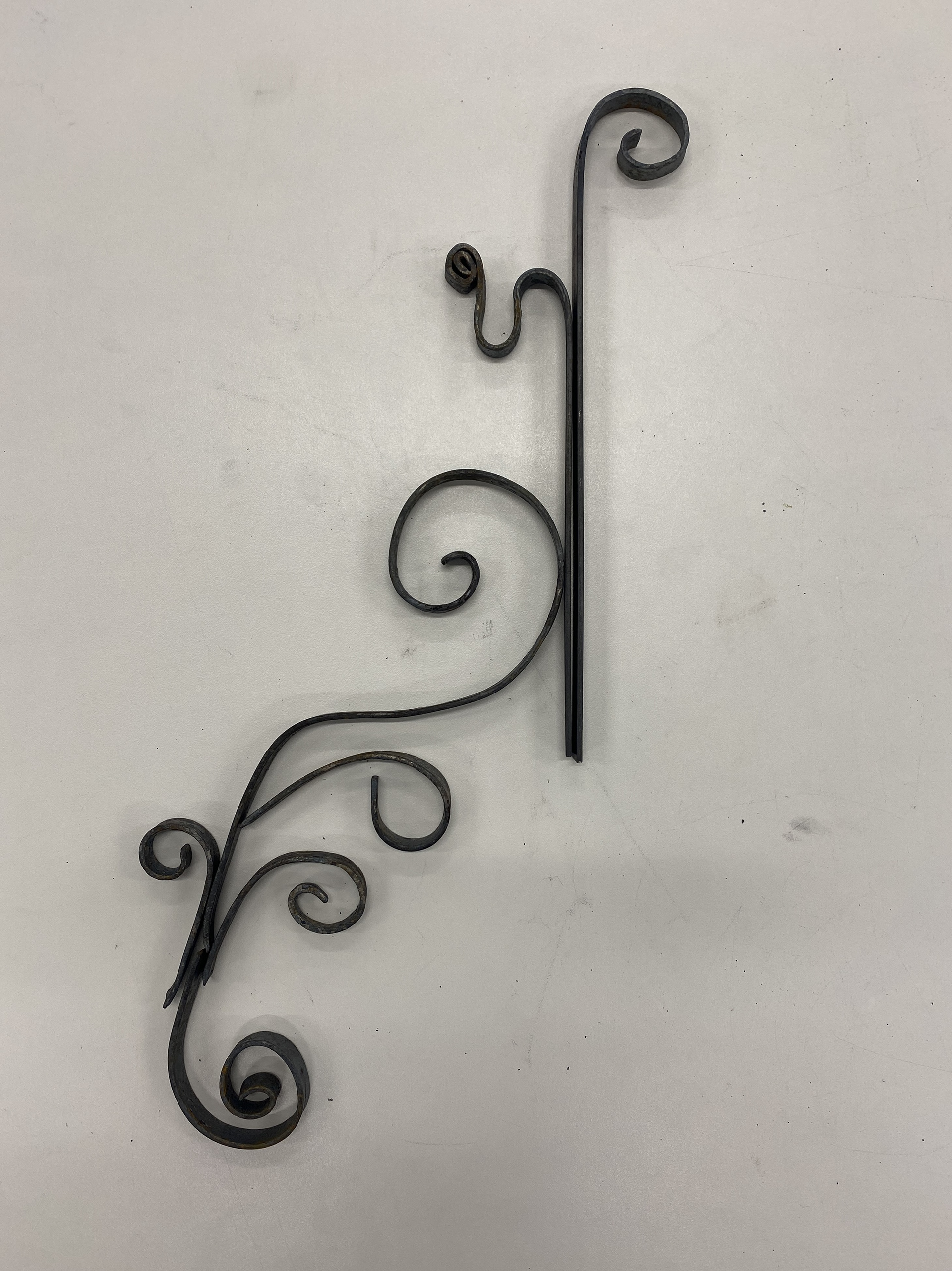
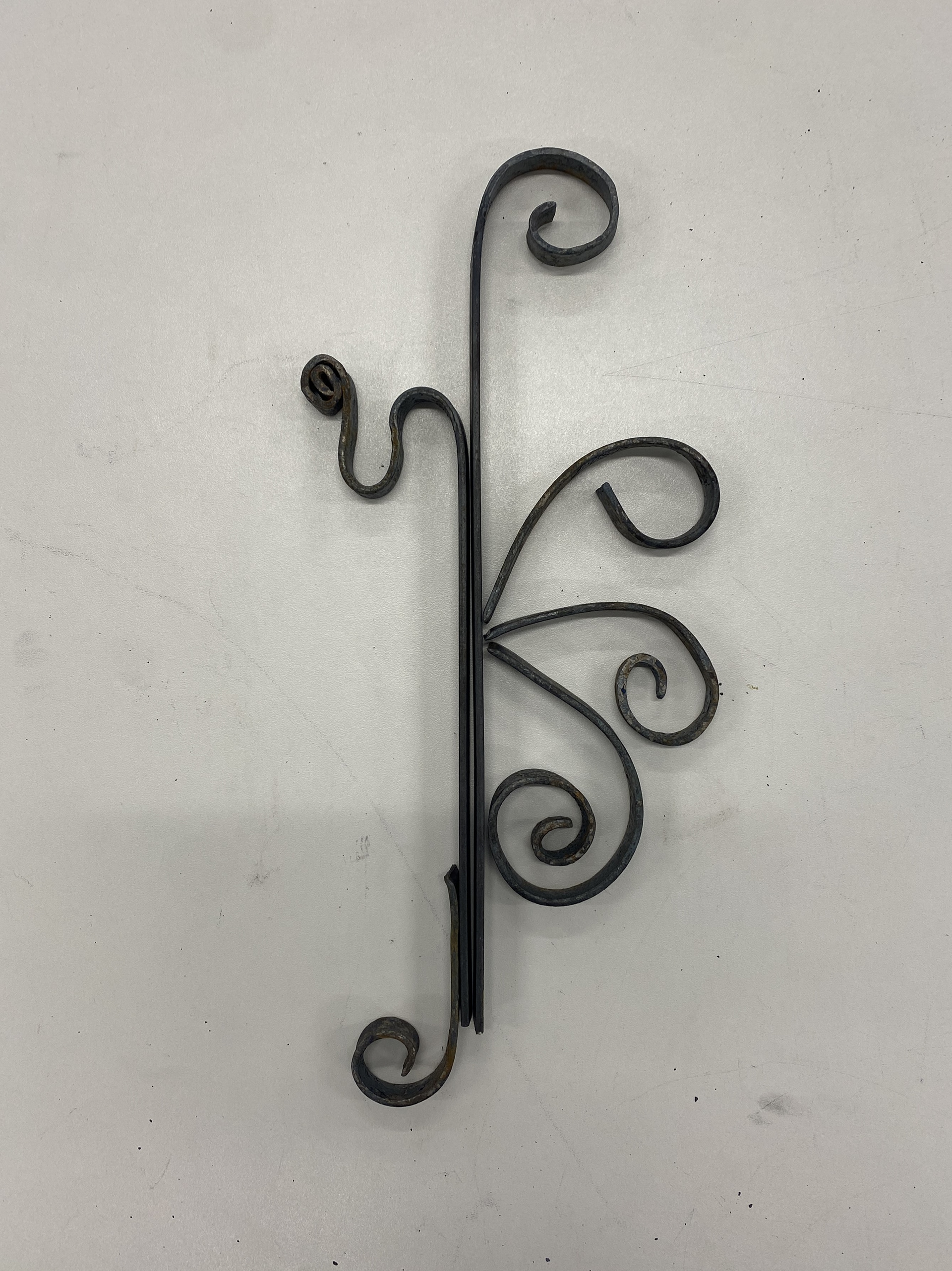
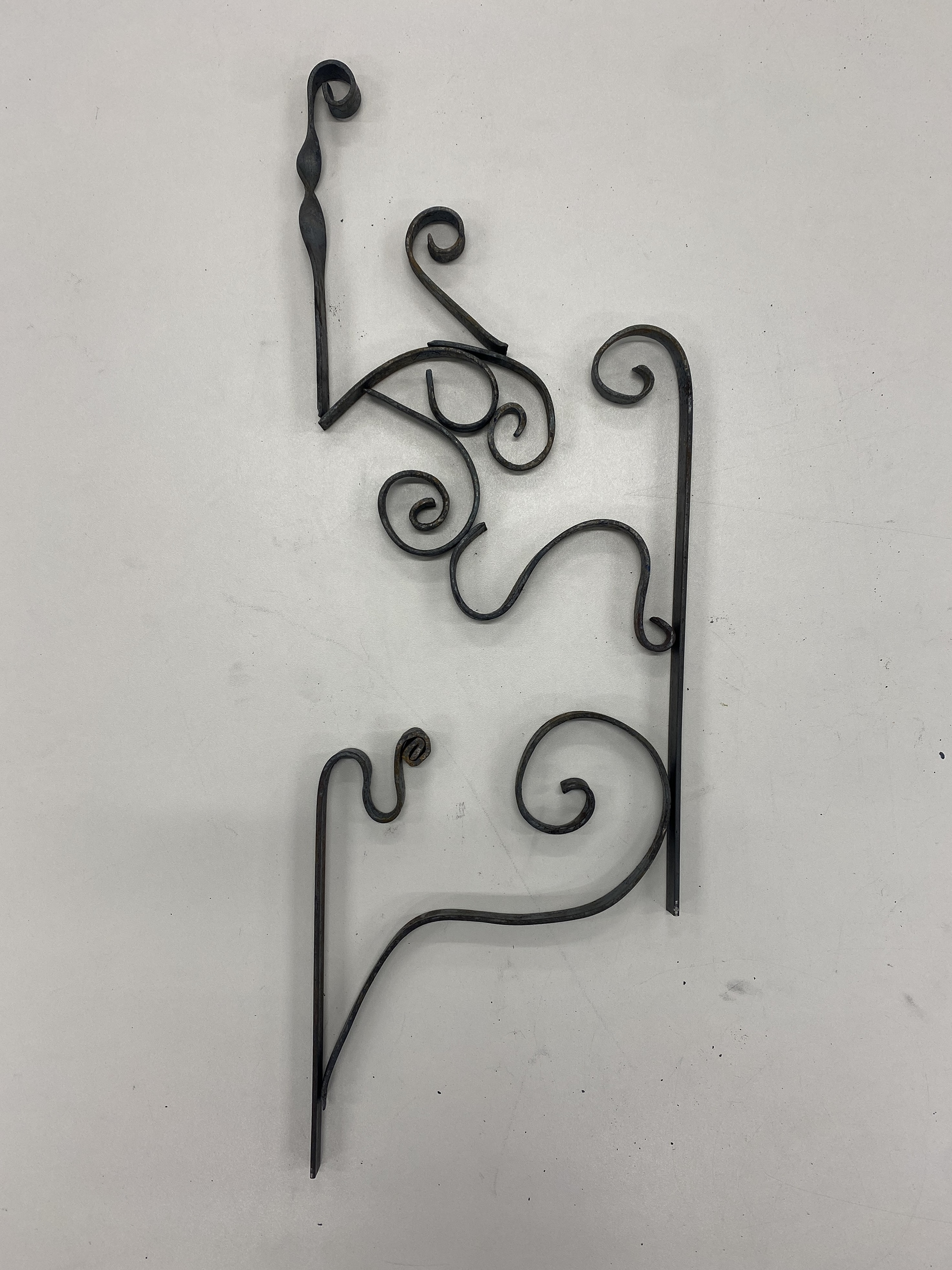
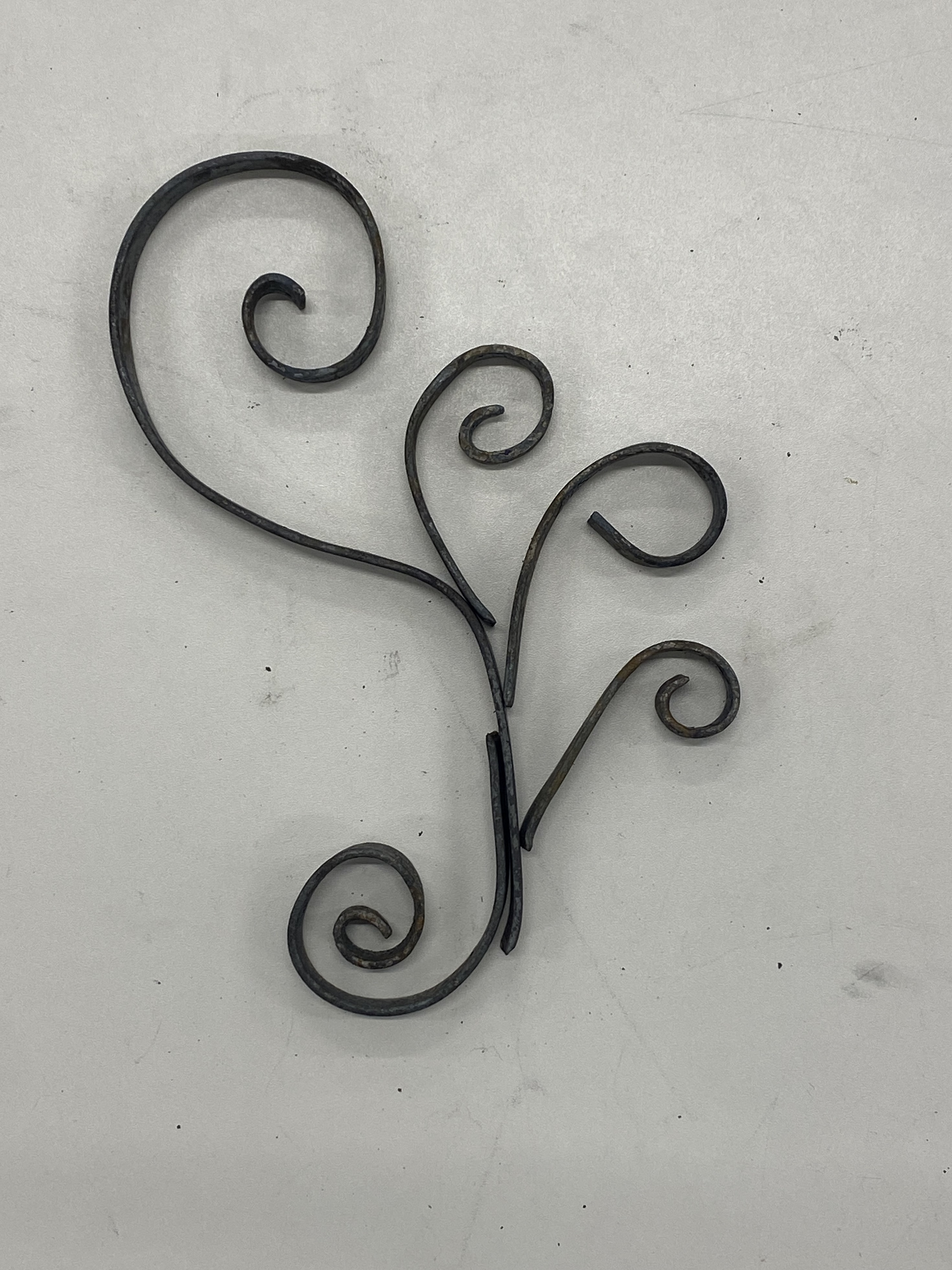
I took these samples and explored different compositions by laying them out on a table. However, these compositions have no connection to the location both in form and narrative. Therefore, I have decided that these will serve as inspiration, and a guide in the future which I can reference when producing work that has a relationship with Didsbury Parsonage.
Investigating the parsonage through abstraction
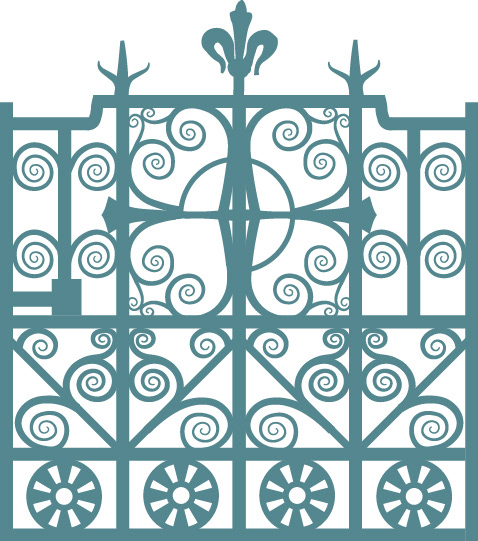
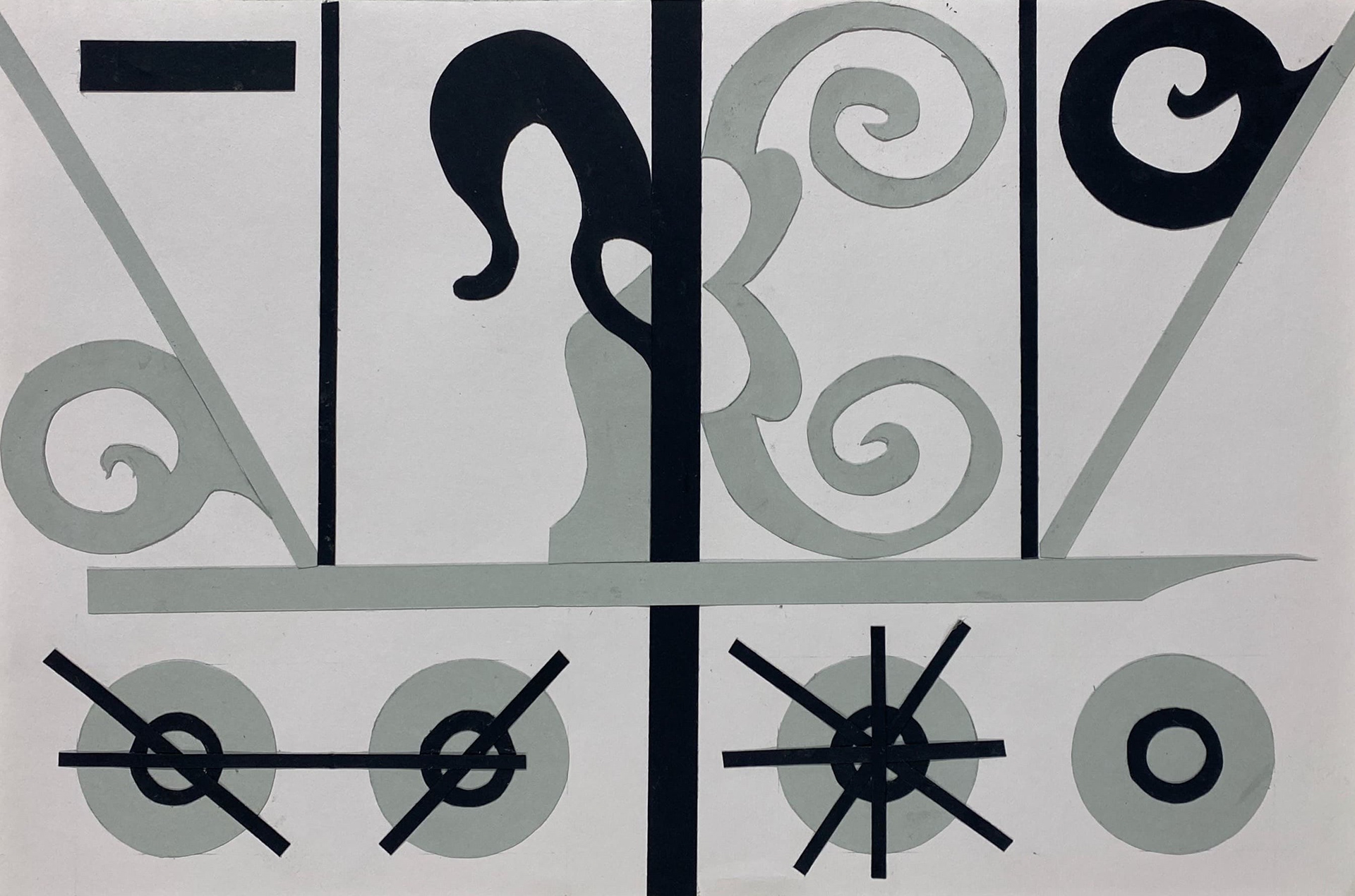
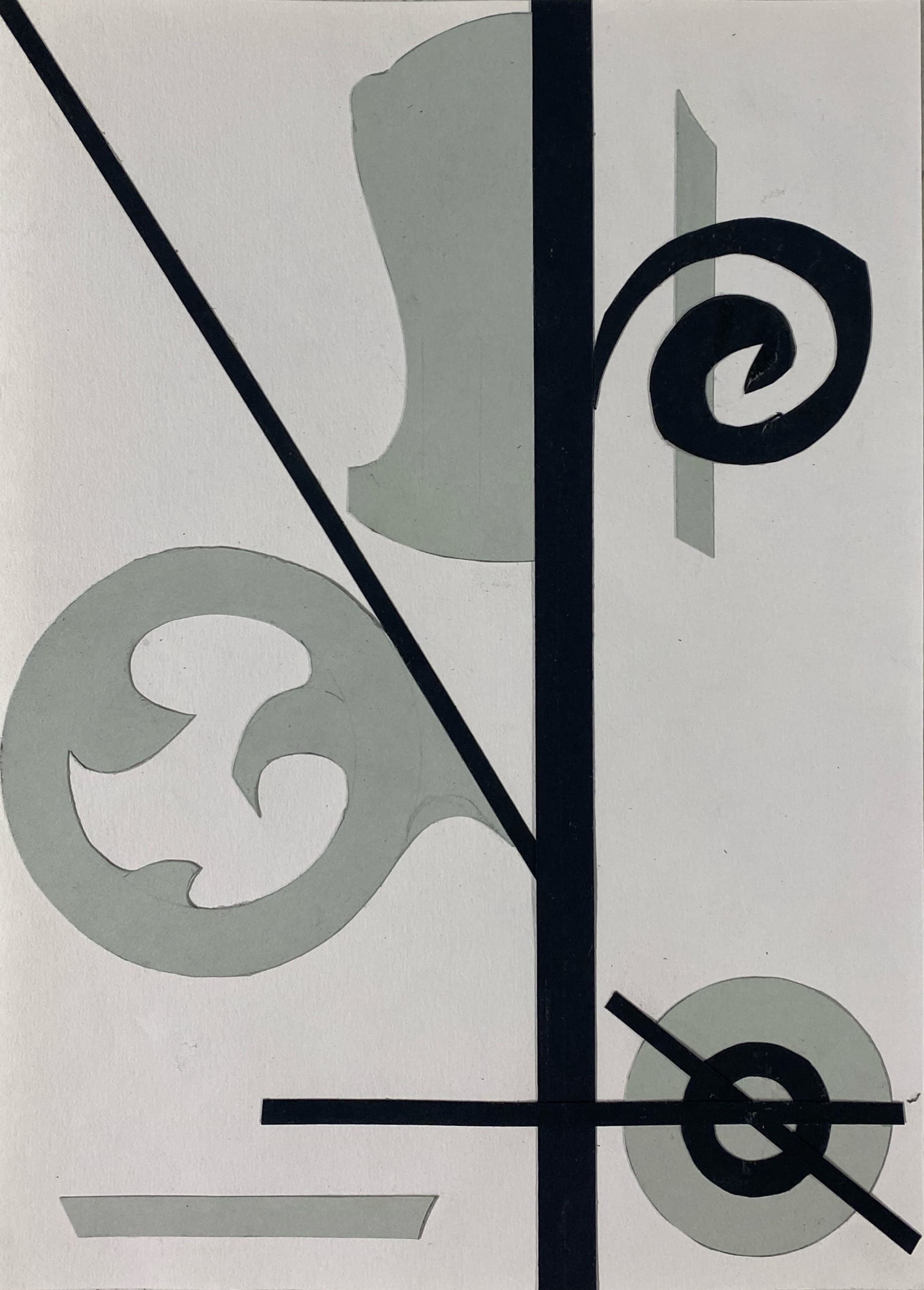
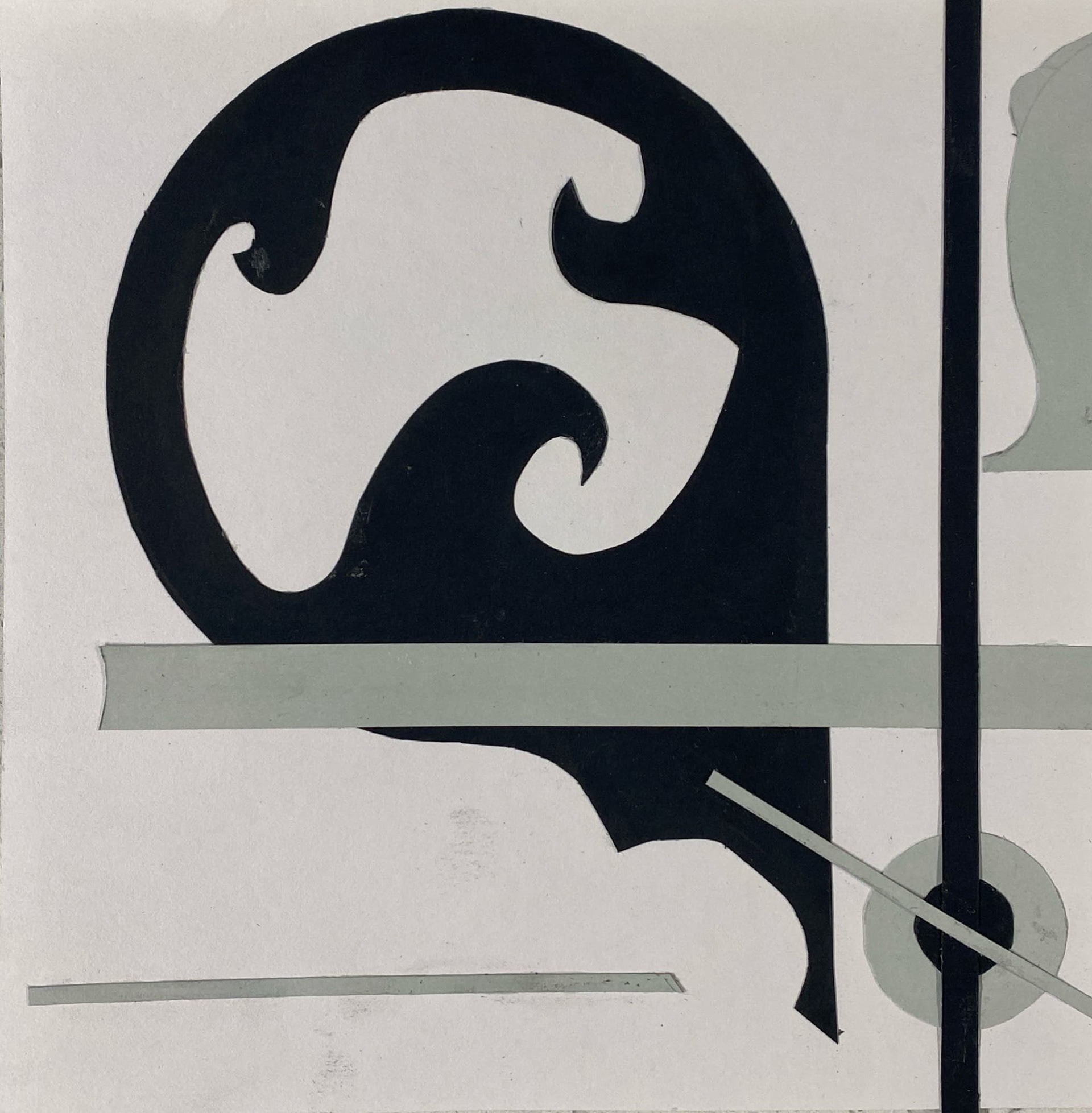
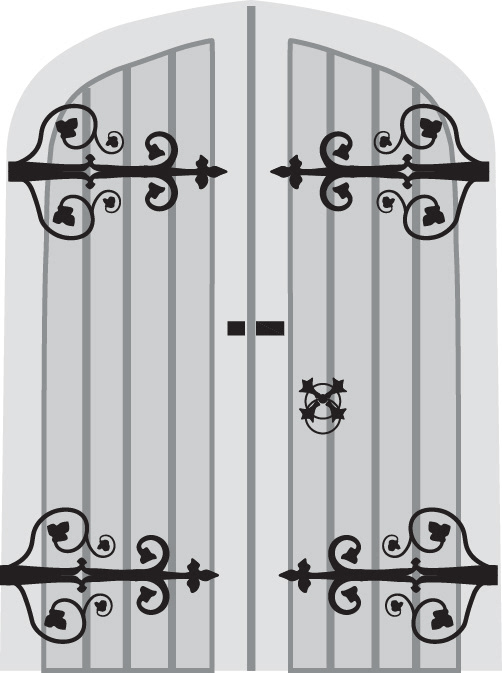
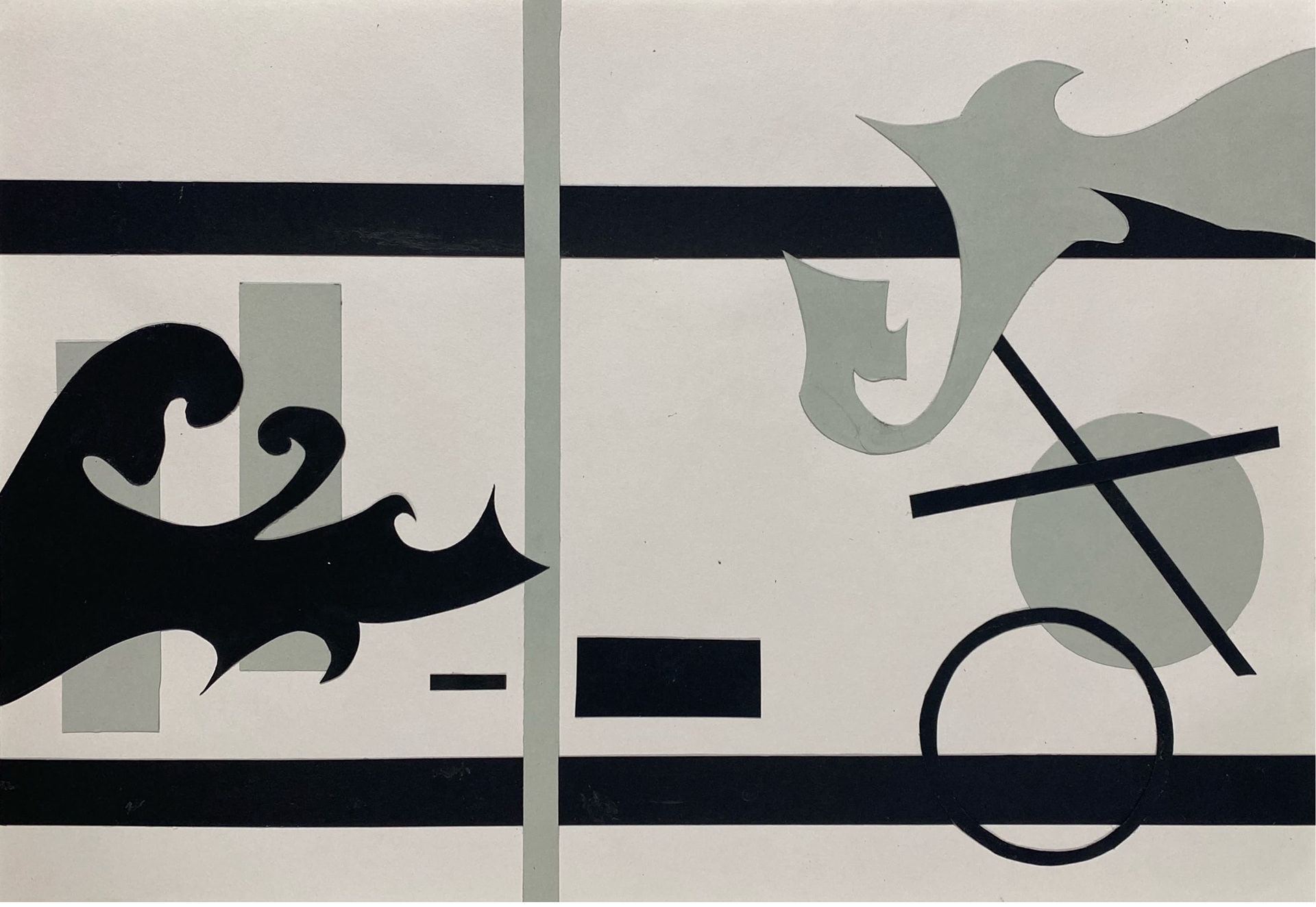
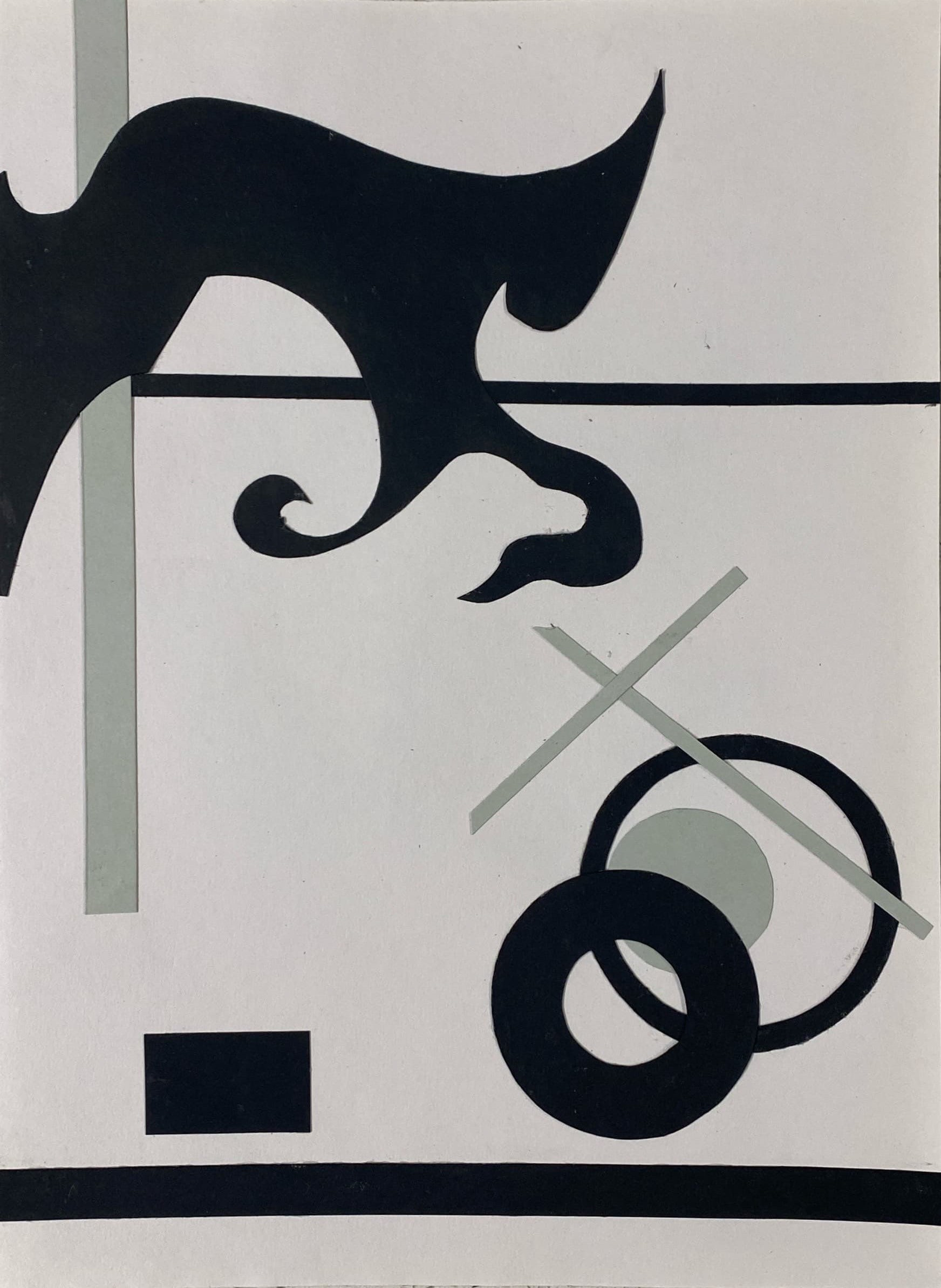
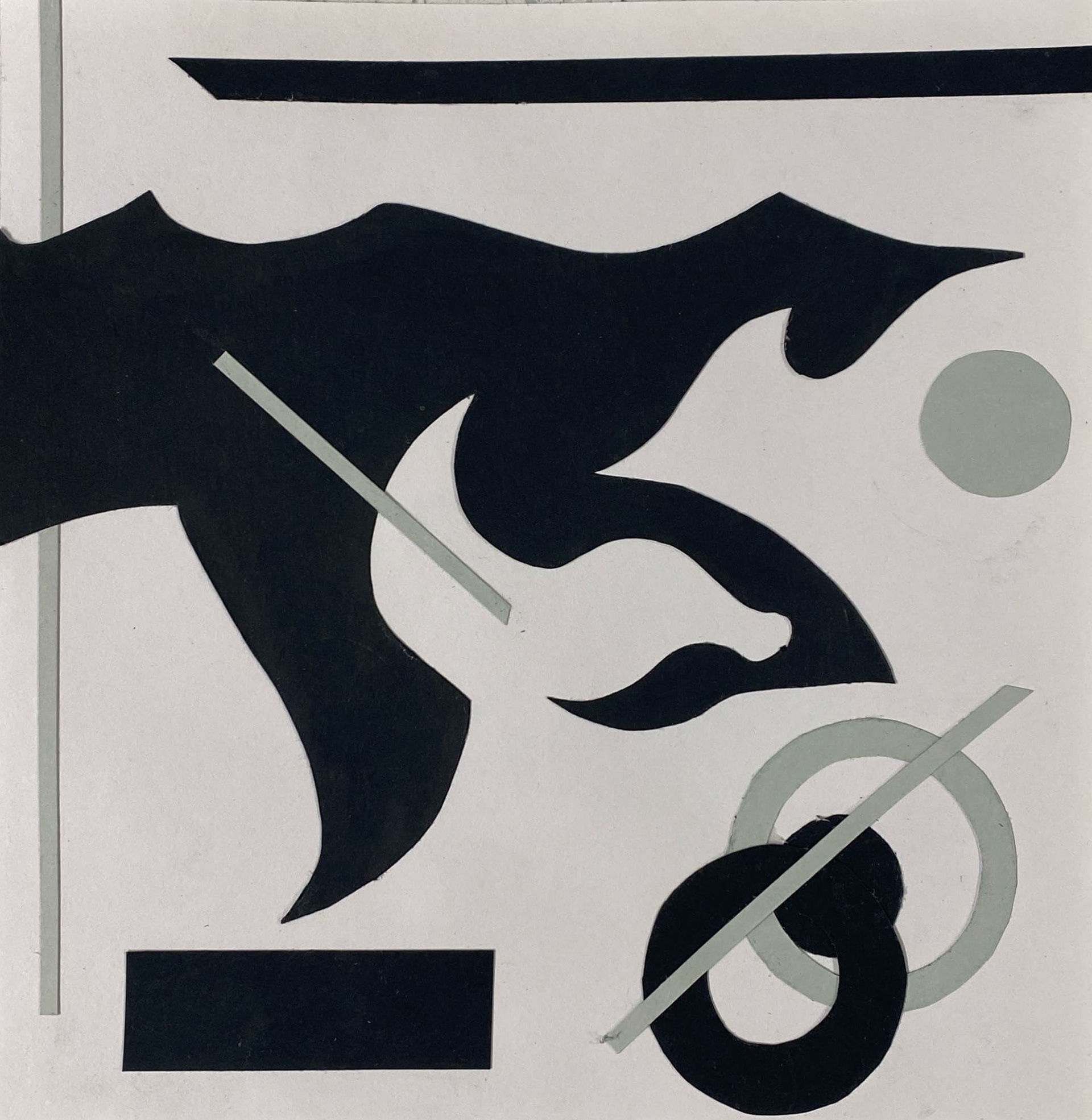
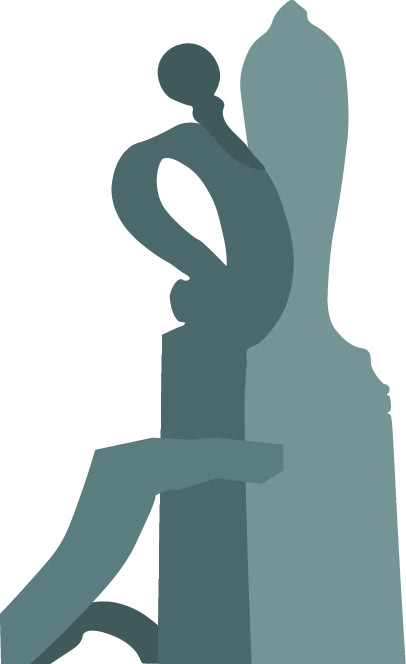
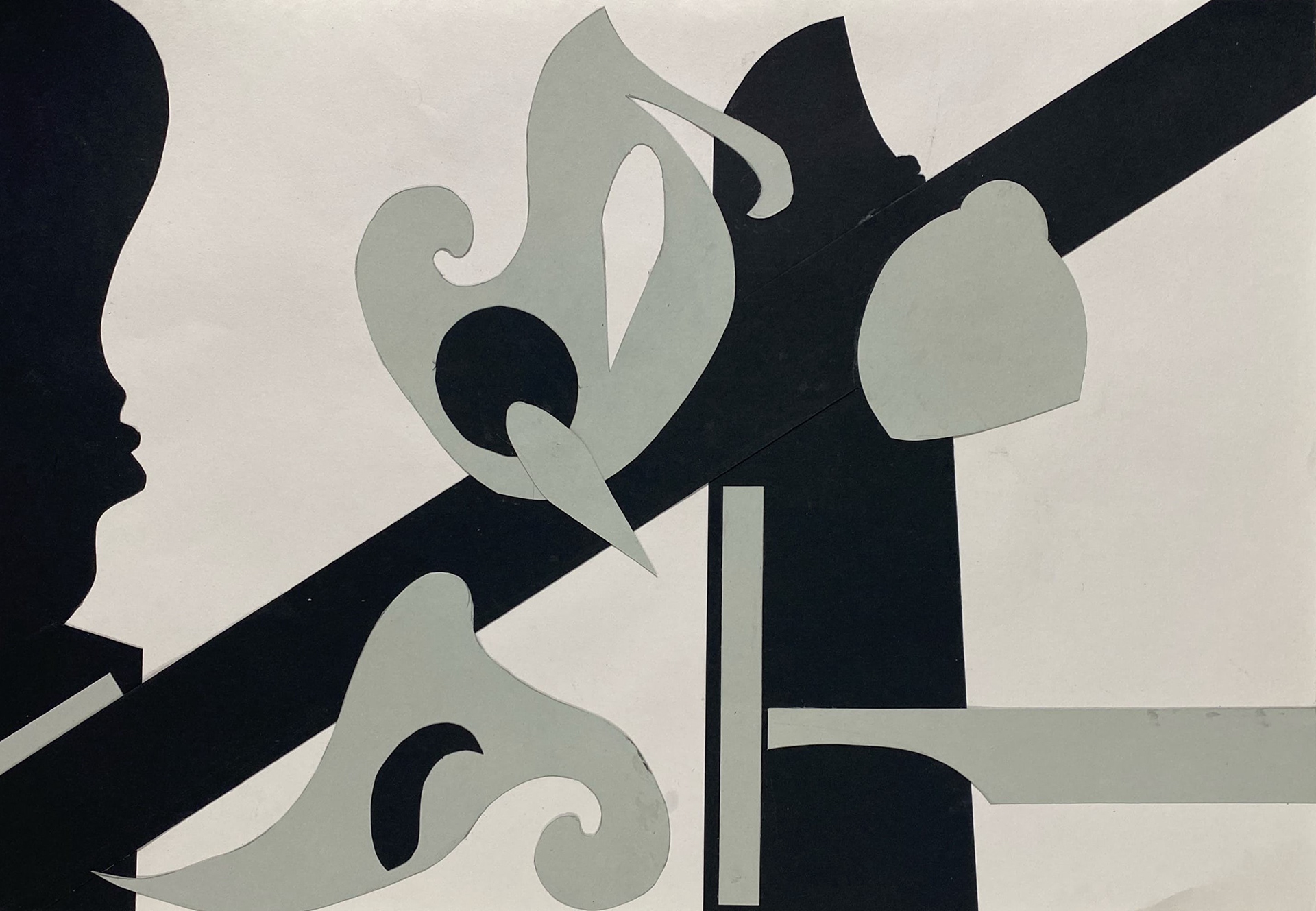
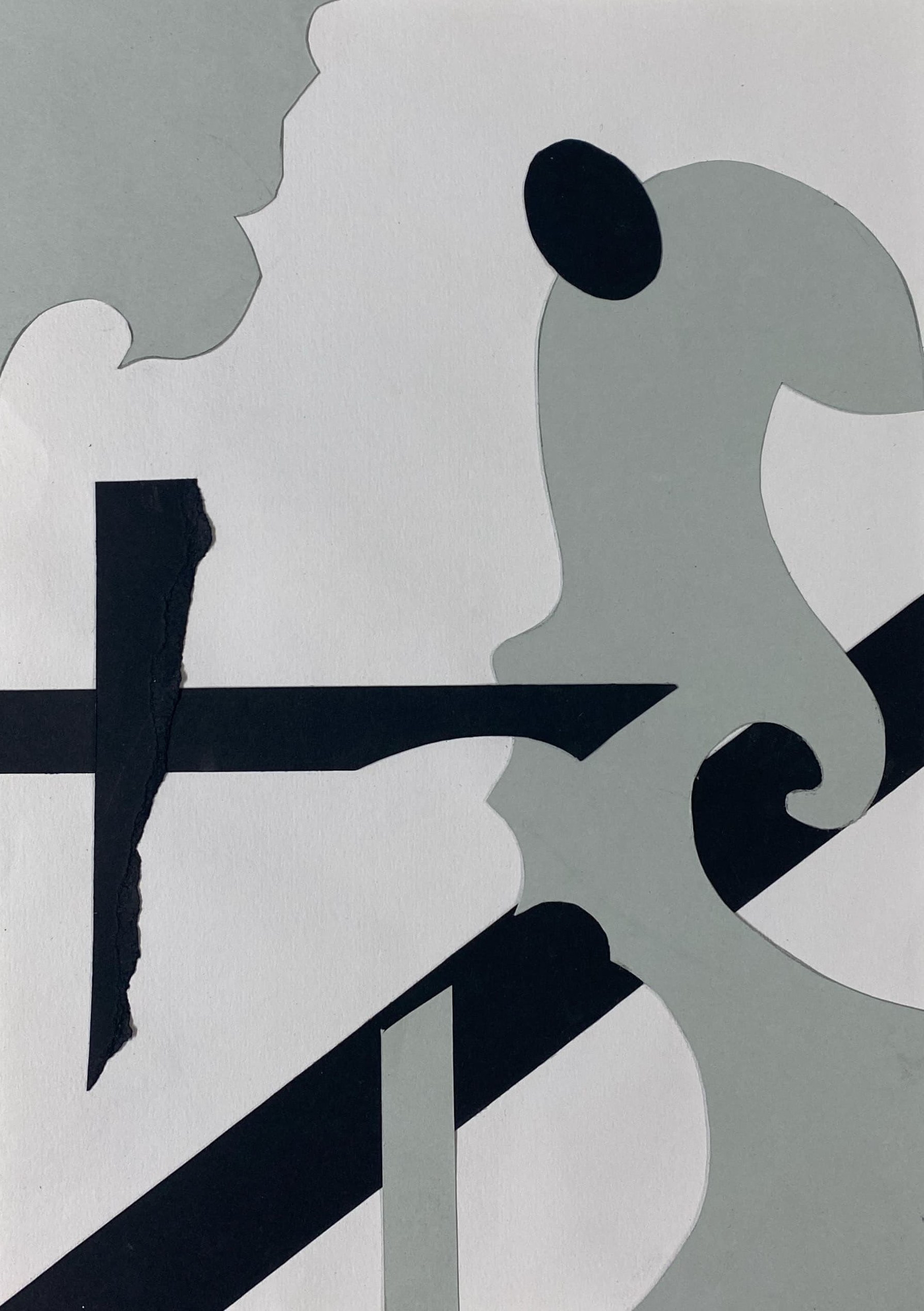
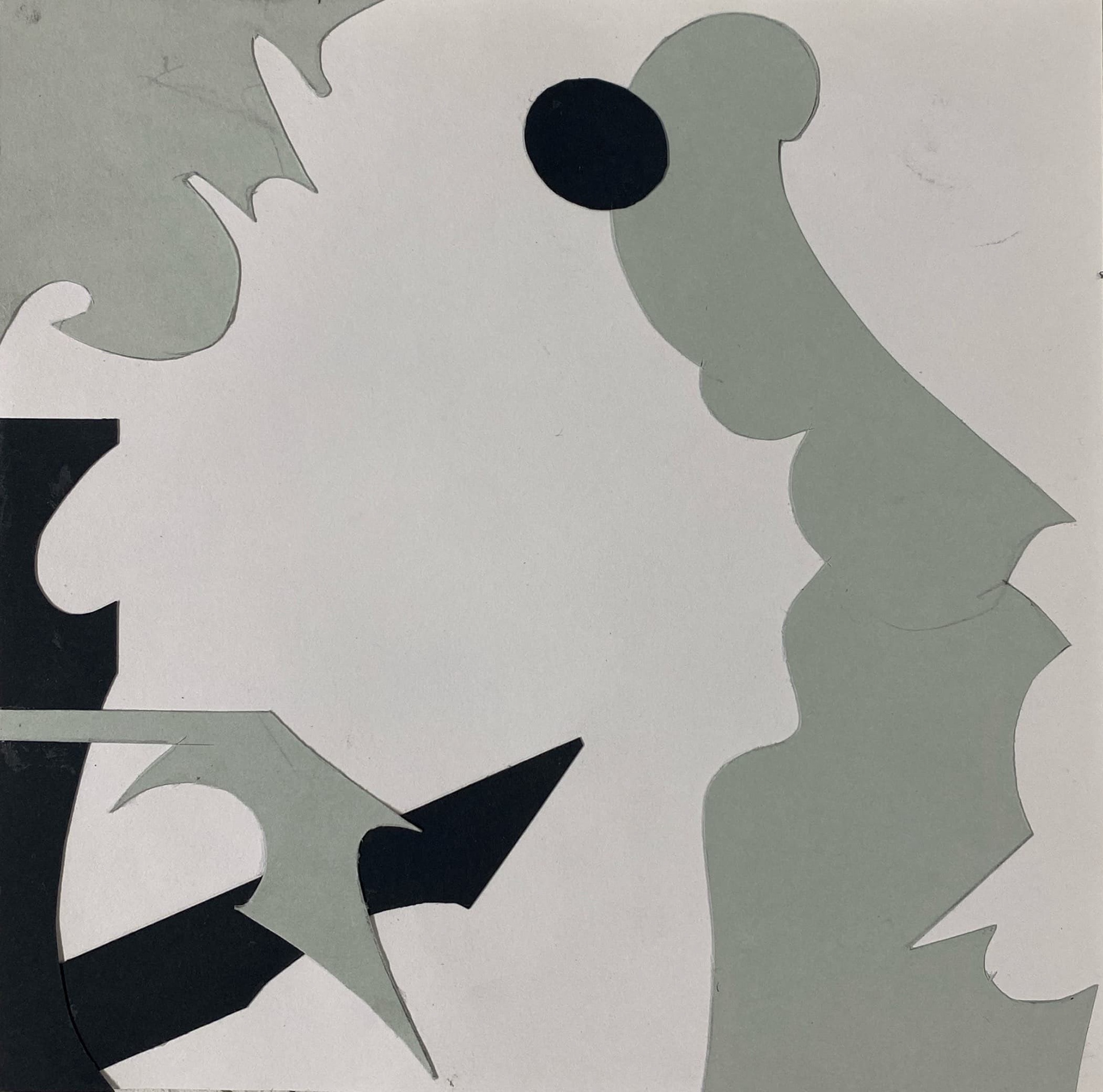
To generate compositions that are linked to the Parsonage I returned to my original photography. I then went through a series of processes of abstraction, firstly making a digital simplification of the picture focusing on key forms and colour. I then used card and papers to create multiple collages changing both the orientation and size of the page. This forced me to extract only the most important forms and explore combining or distorting different elements. I purposely only referenced the previous piece in the series to keep the composition loose. Additionally, this meant that the only constraints were the size of the page.
I feel that these were a success as there are still links to the Parsonage, however, this is my interpretation rather than a direct extraction of information.
Taking key shapes to create decorative details
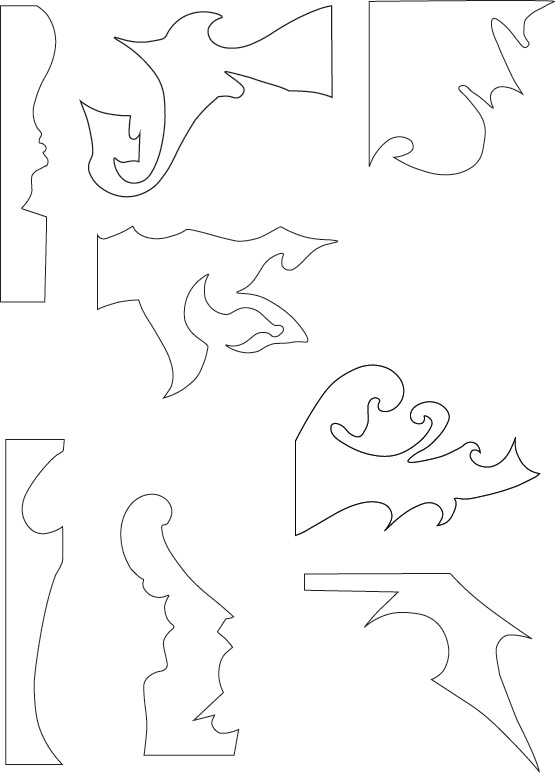
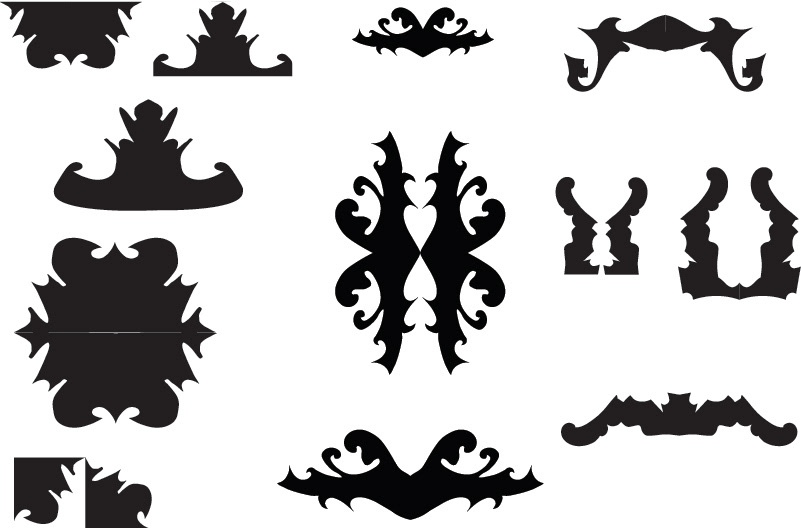
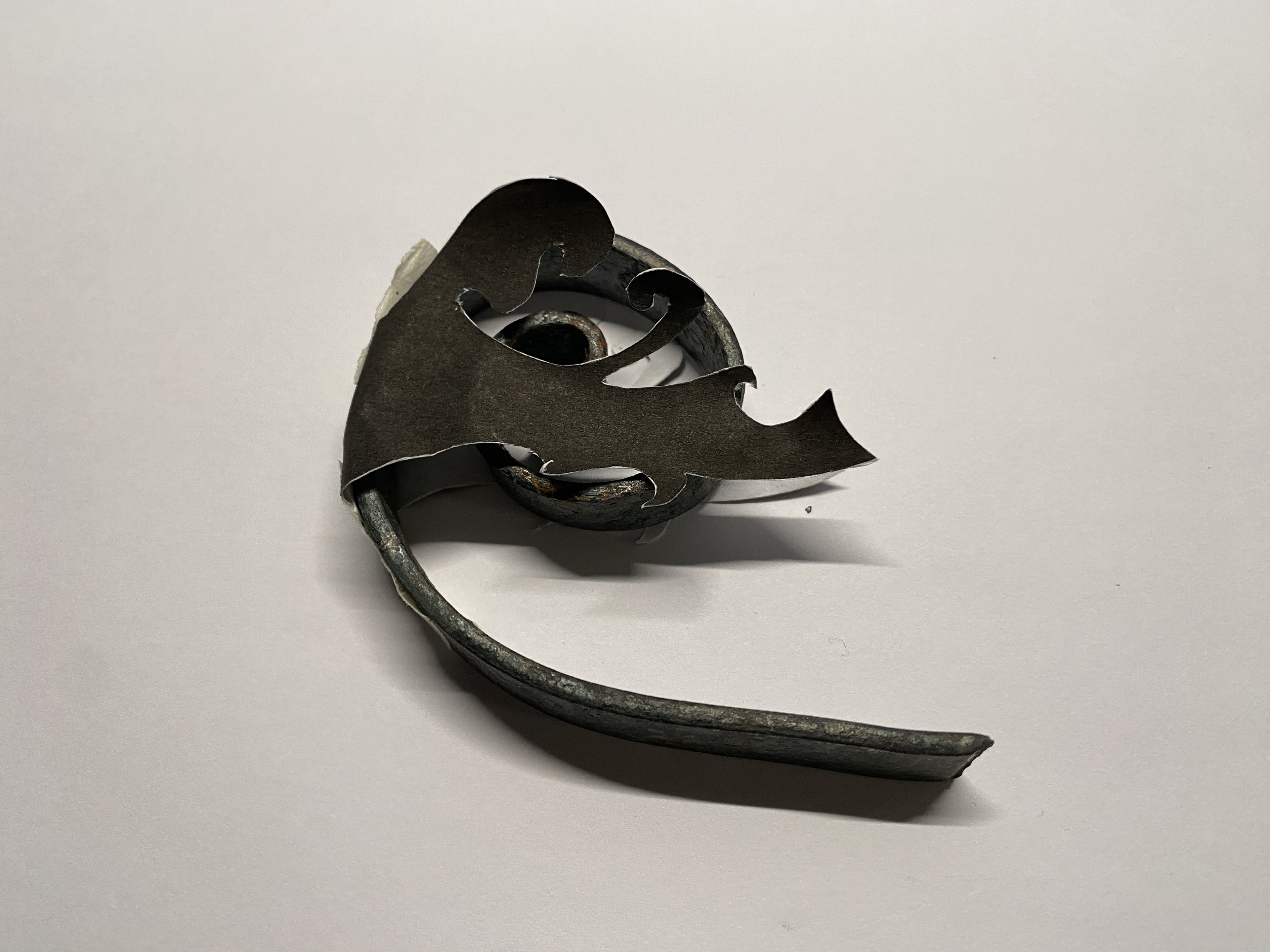
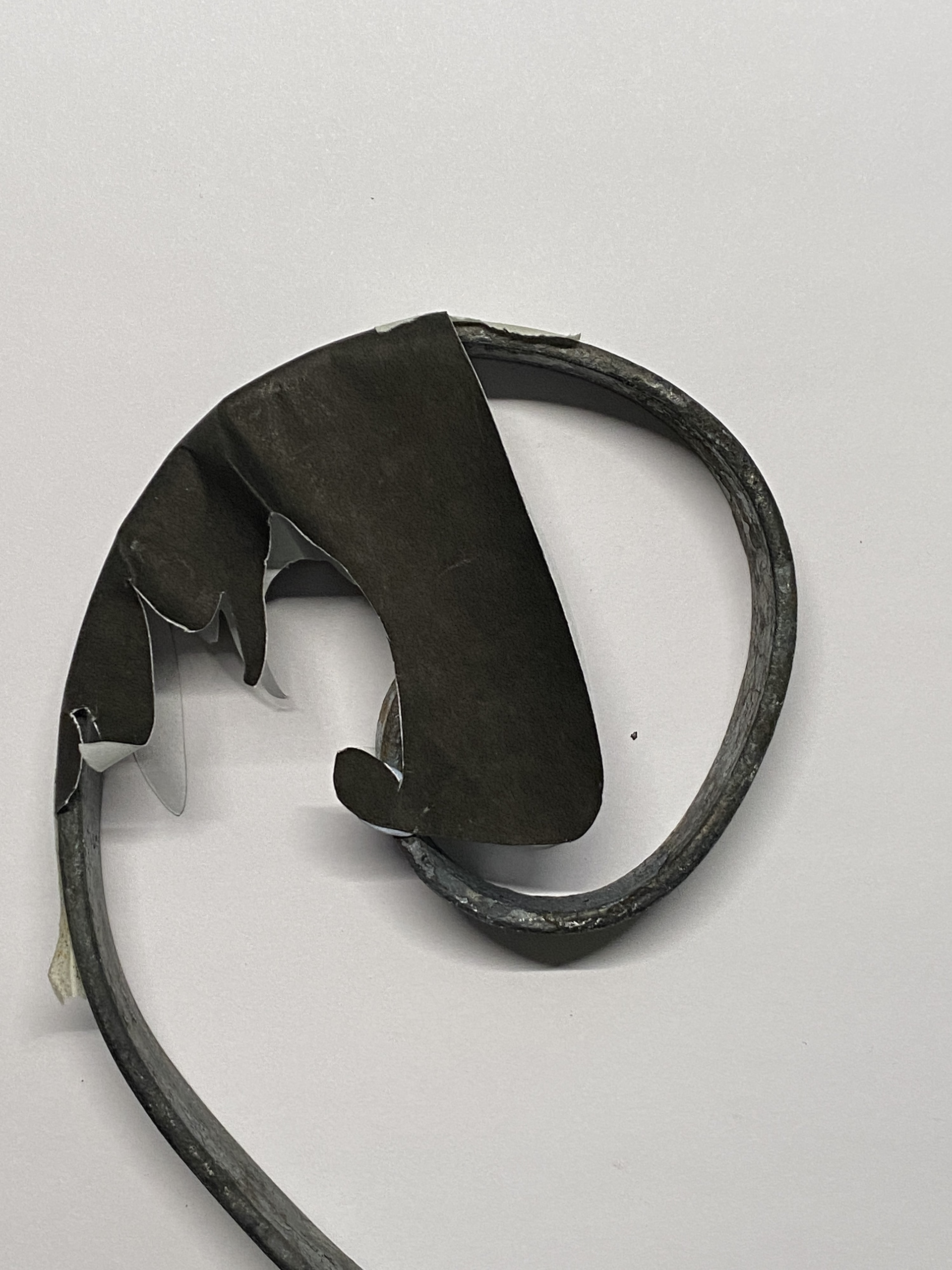
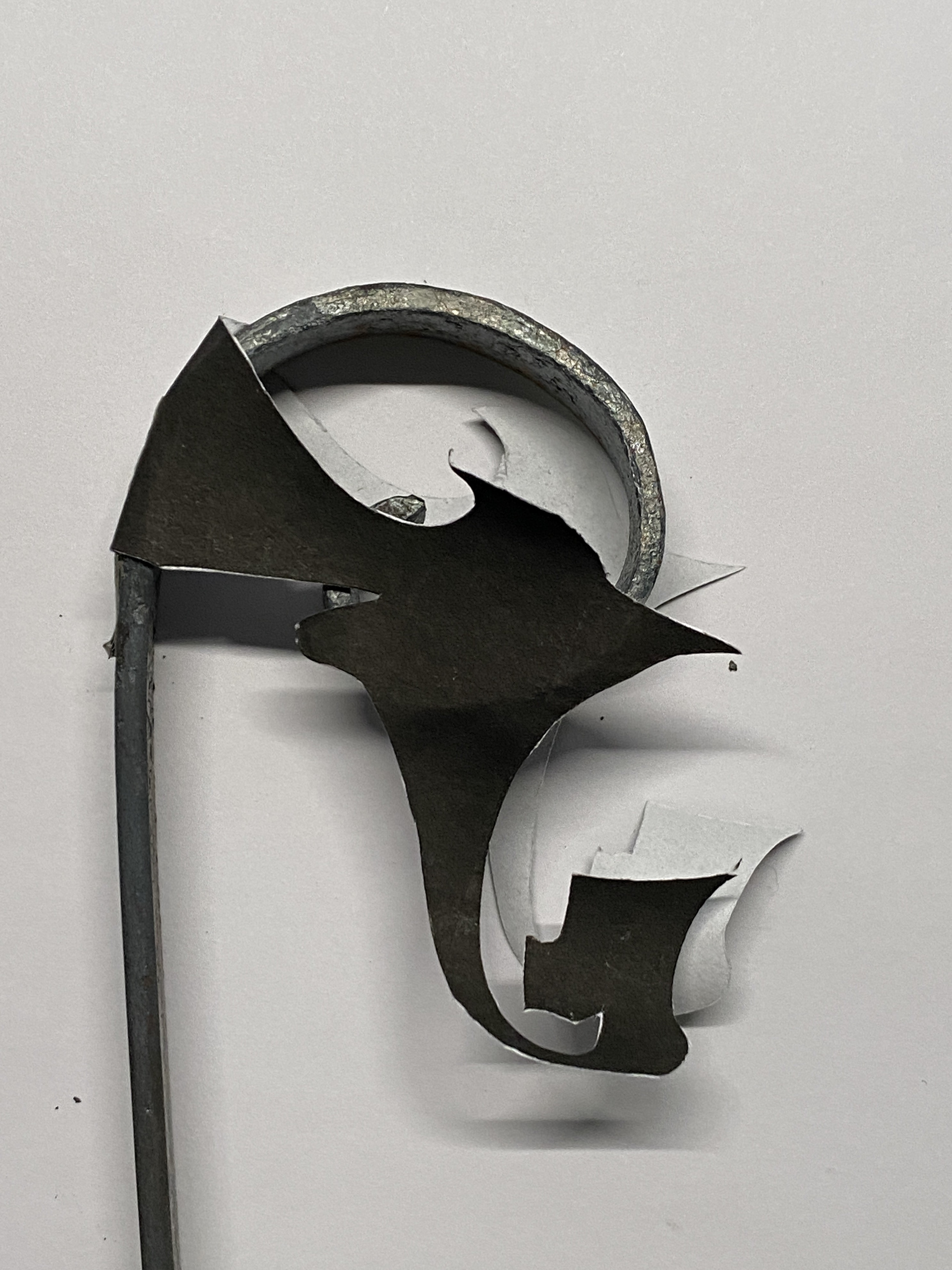
I extracted the most successful shapes and experimented with creating patterns that can wrap around the sides of the forged scroll samples. I took inspiration from my research looking at the interaction between scroll and decorative element. I felt that these were a partial success, I like the symmetry and enclosure of the paper shapes. However, they cover too much of the scroll work. Also, the current size of the shapes would be too difficult to cut out of steel, so I would need to scale this up to use larger flat bar.
Progressing into 3D to generate form
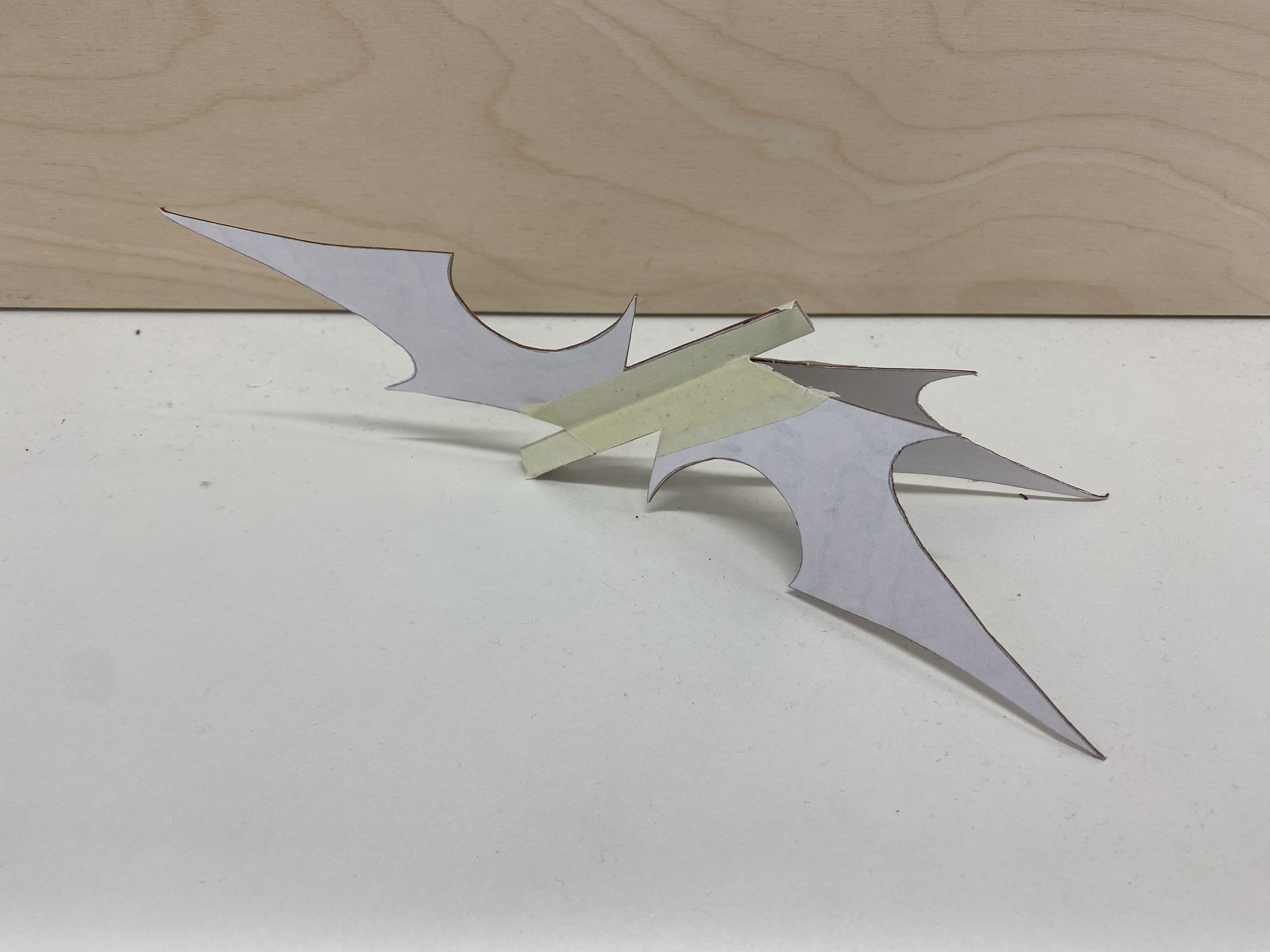
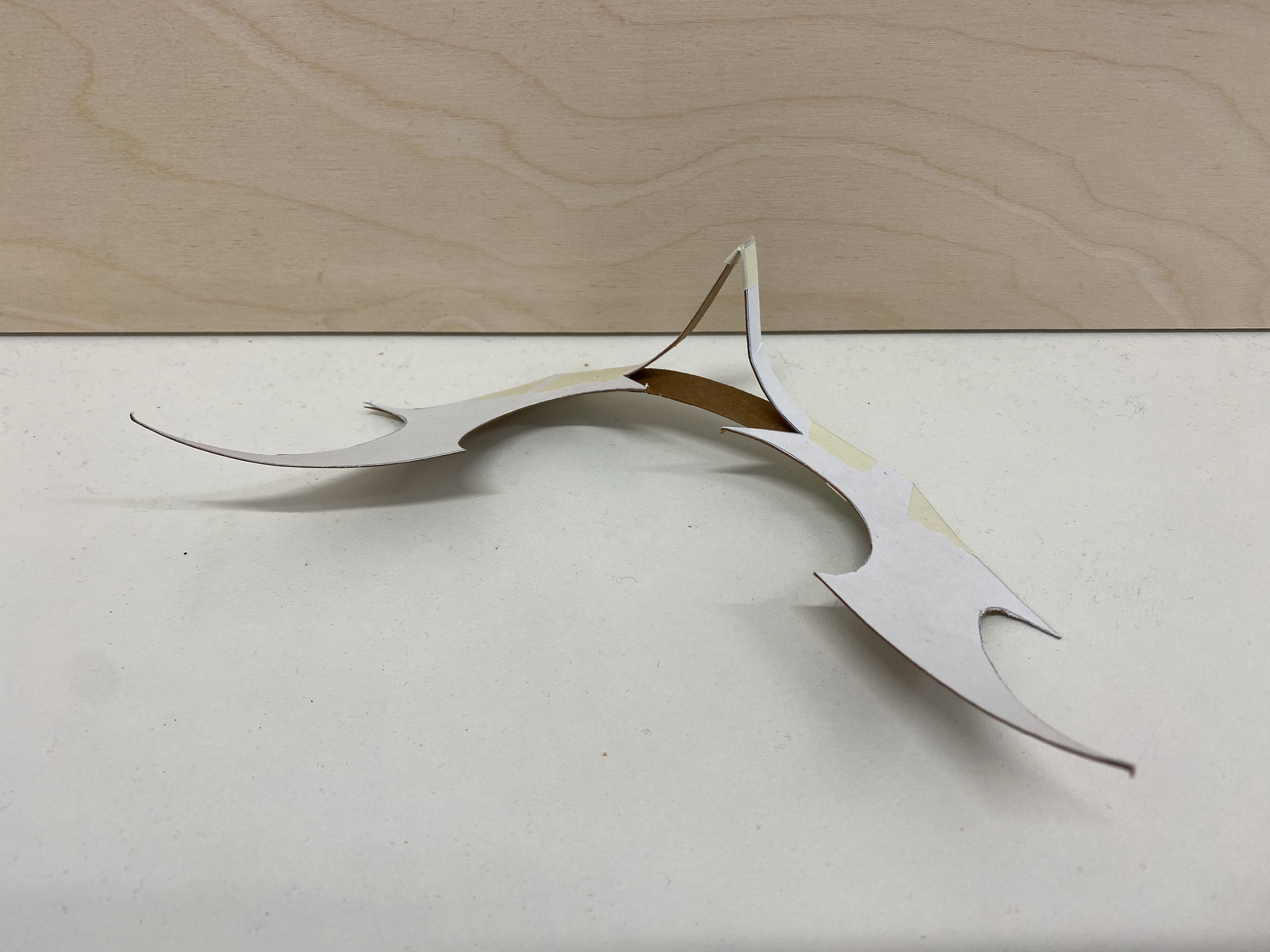
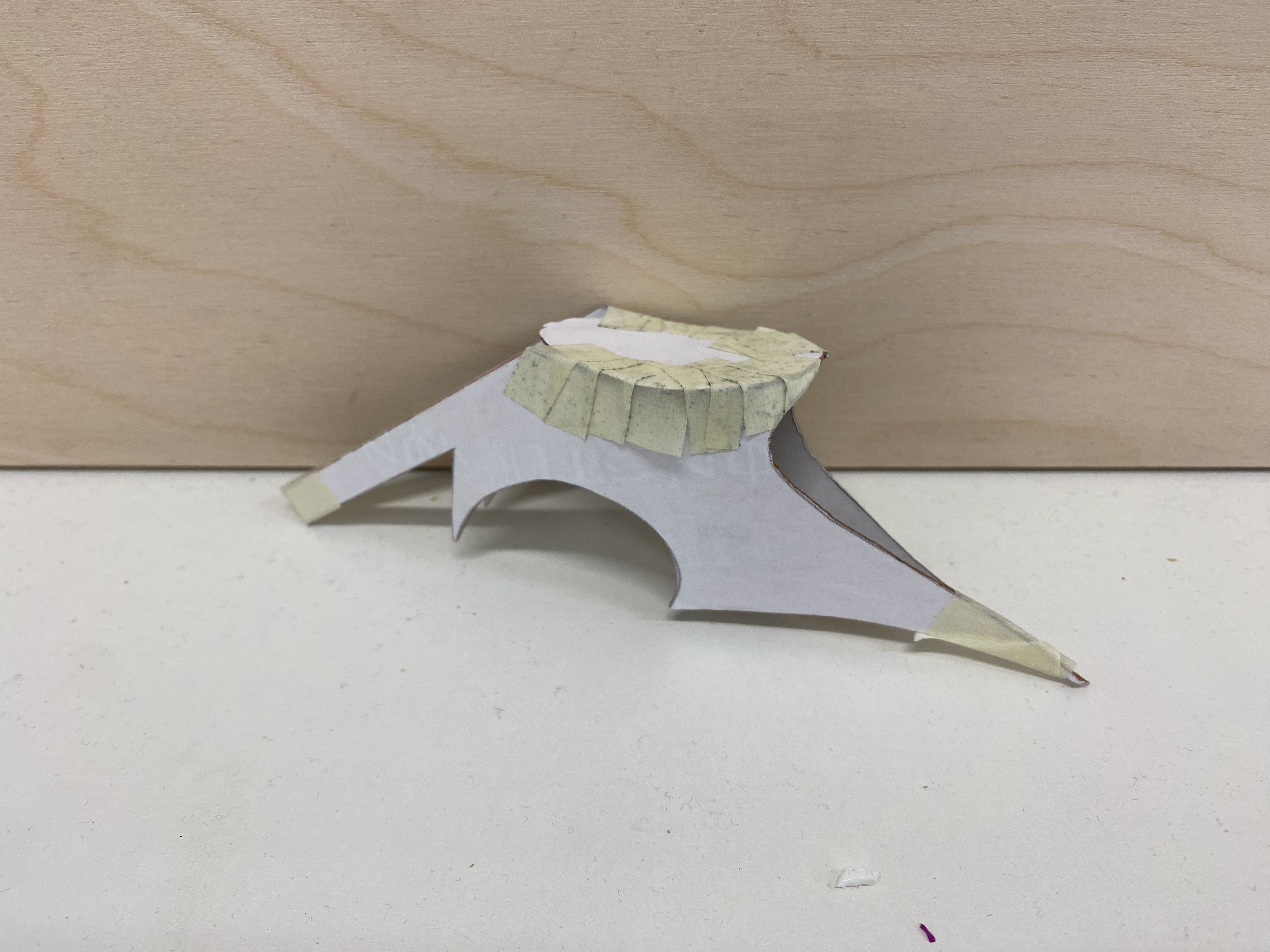
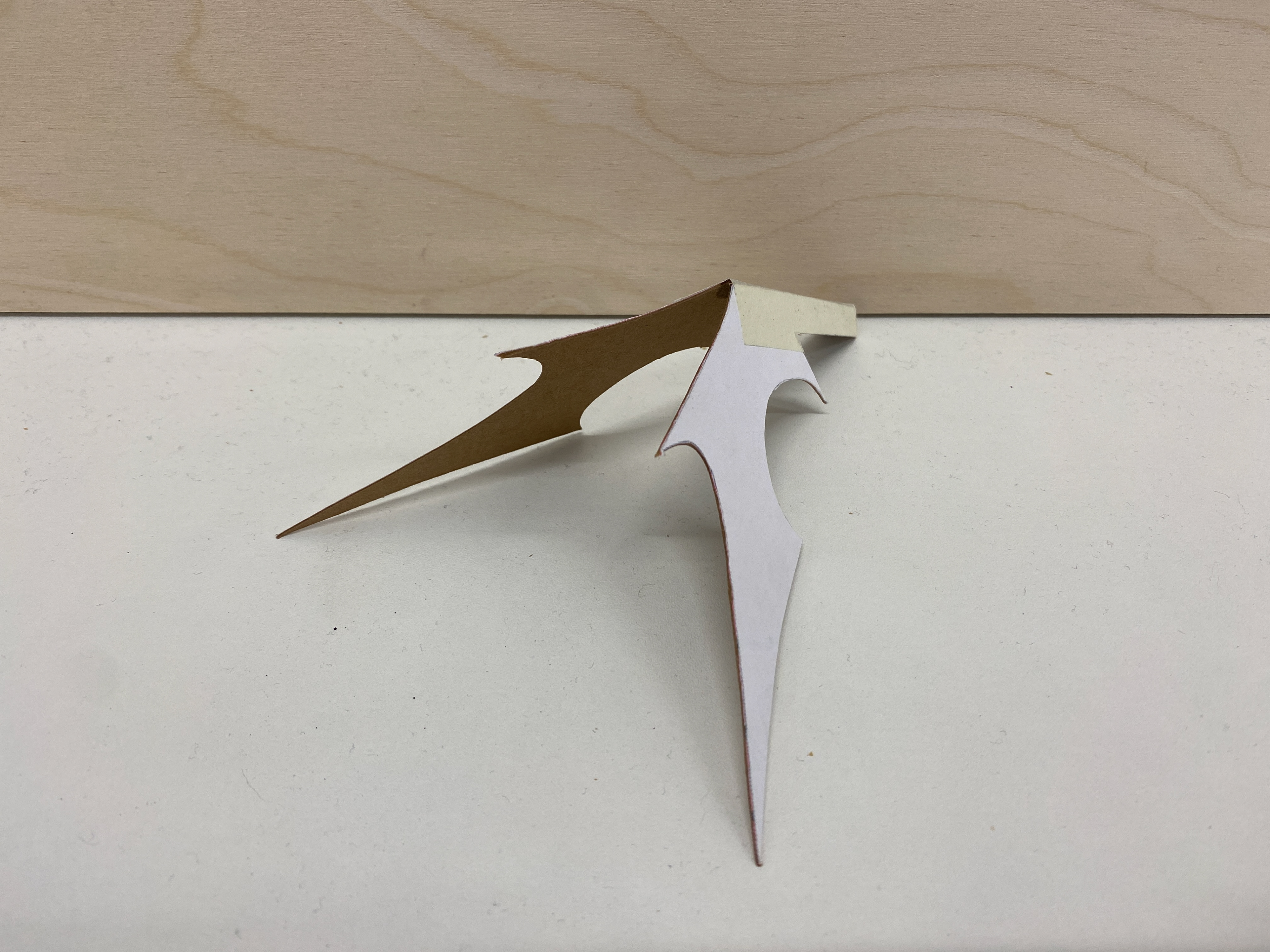
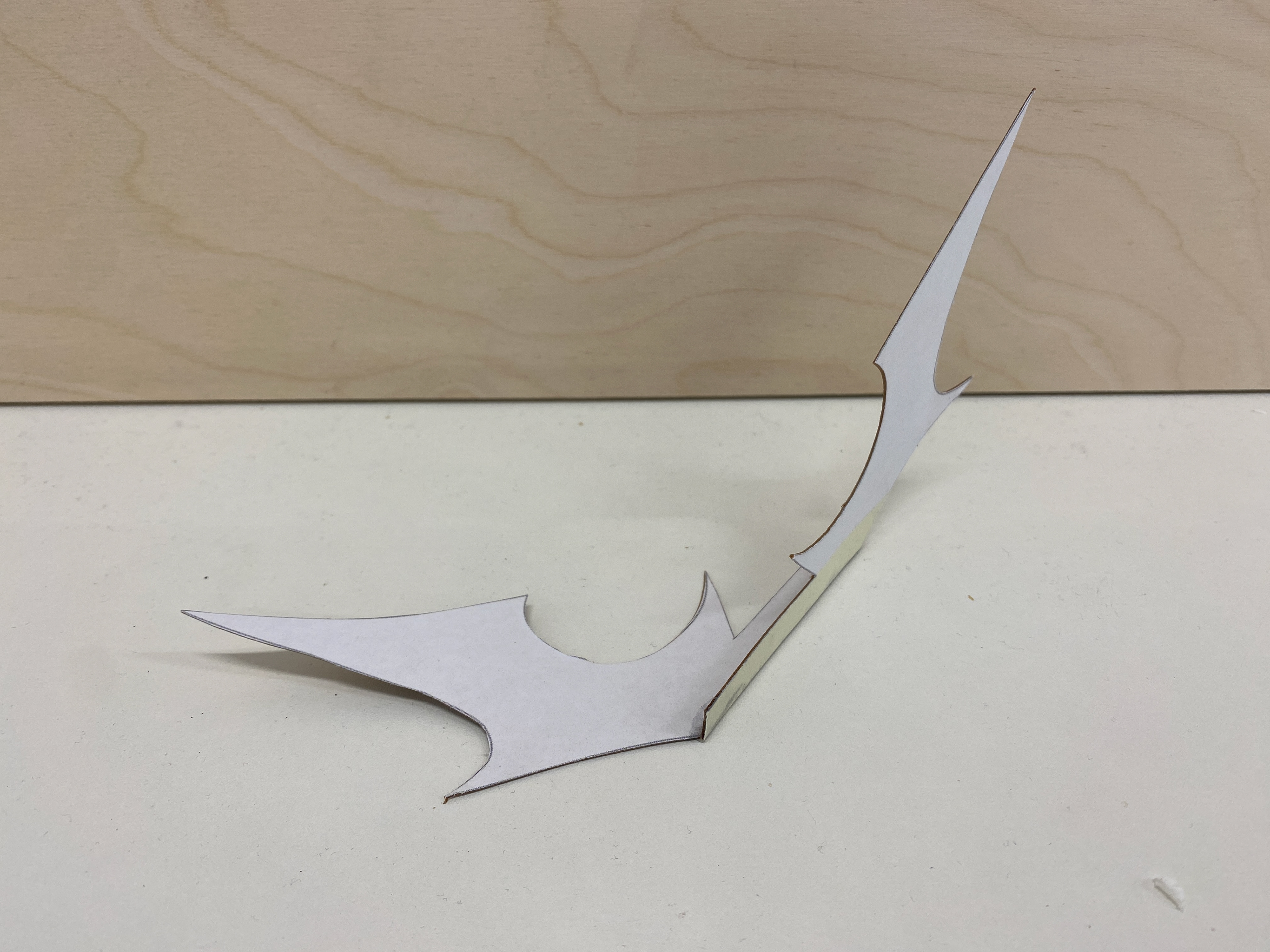
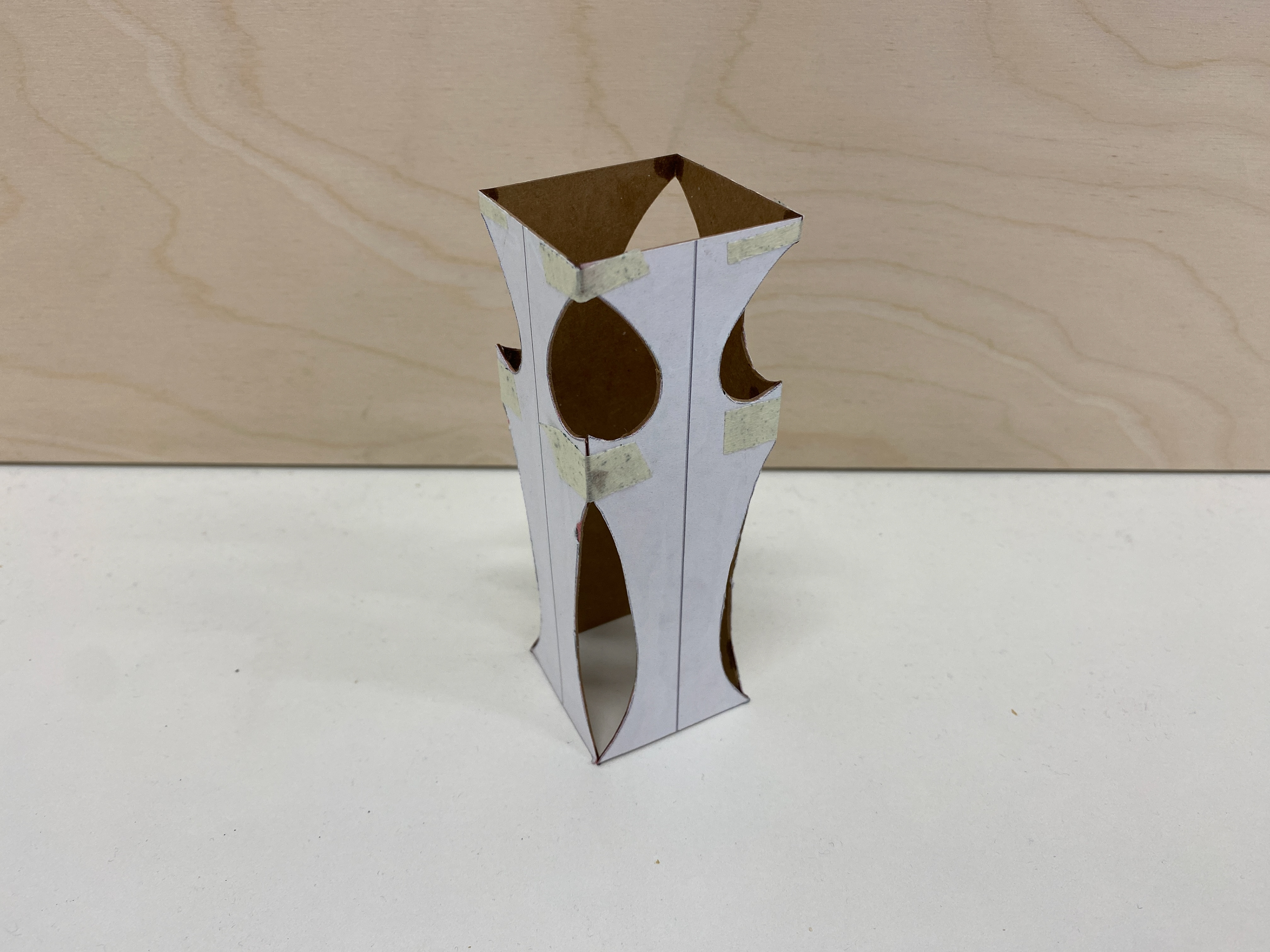
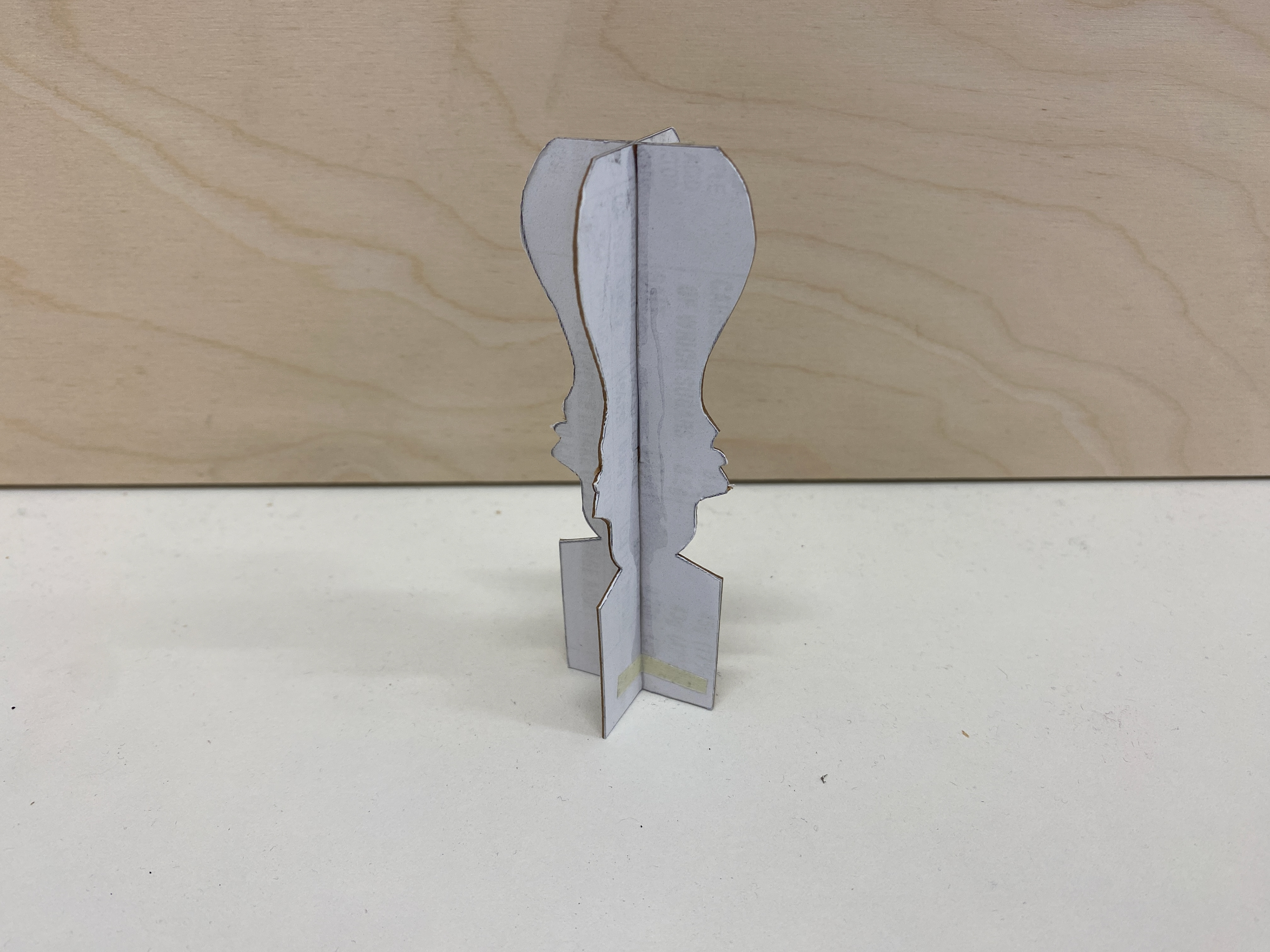
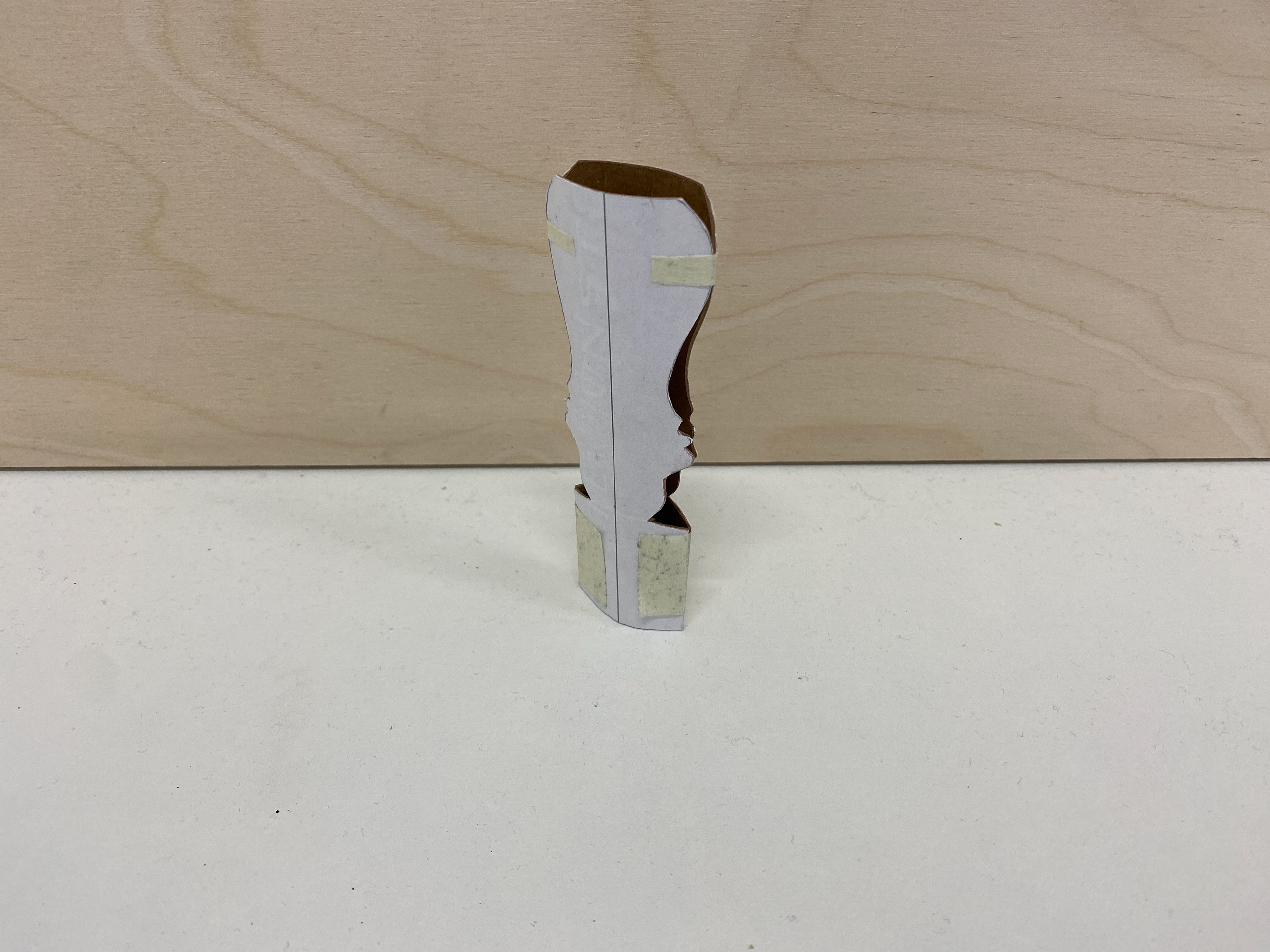
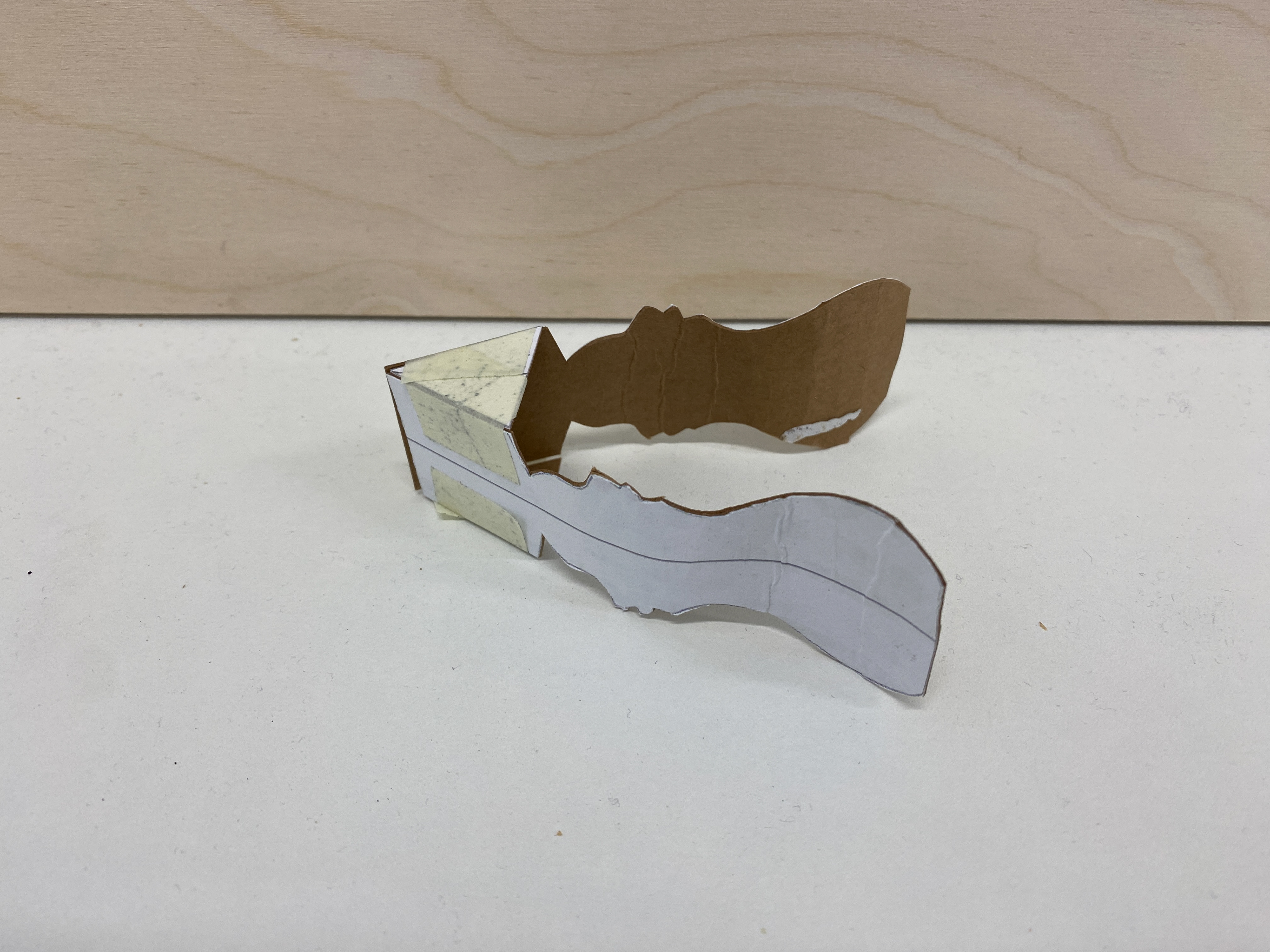
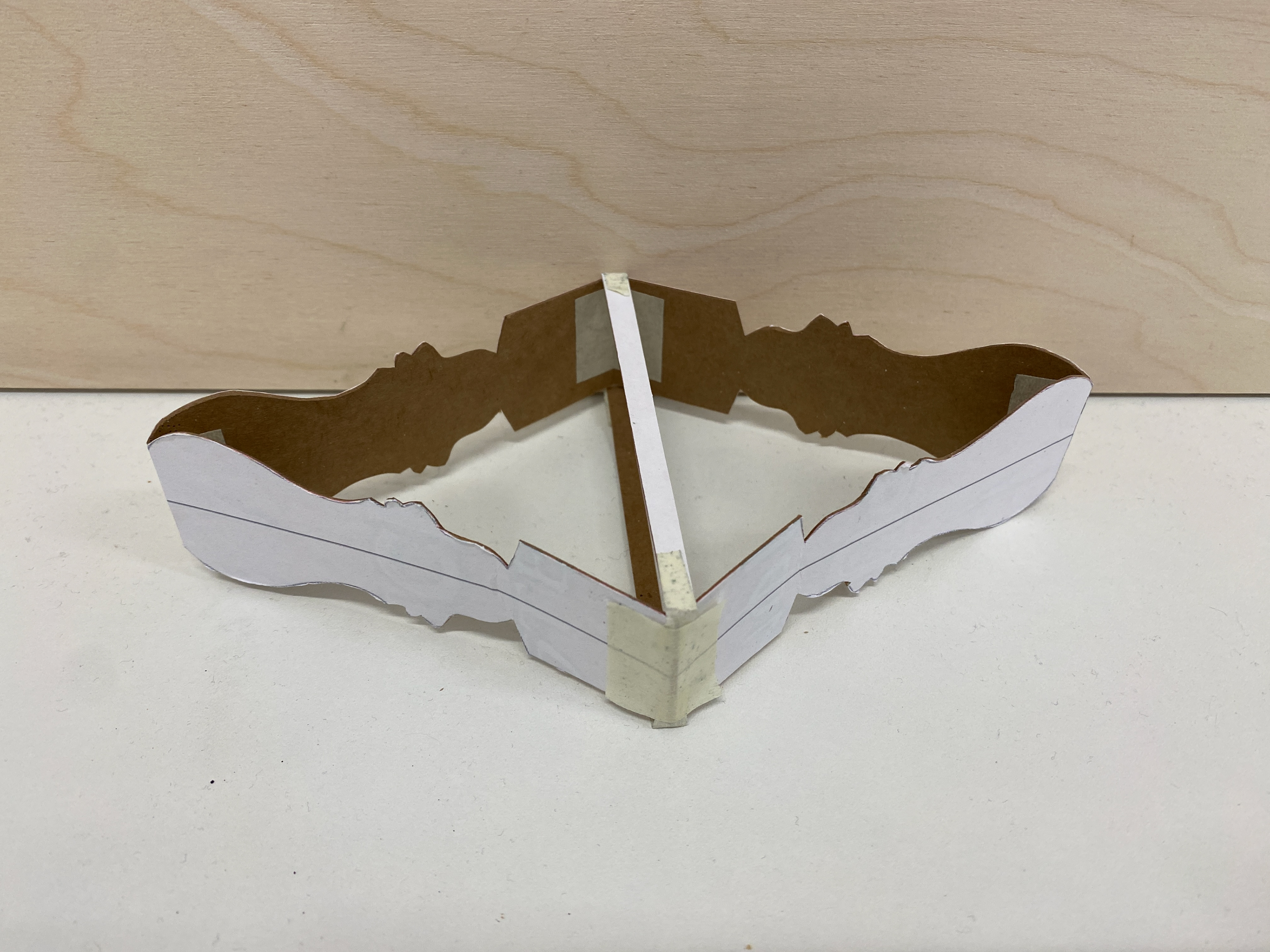
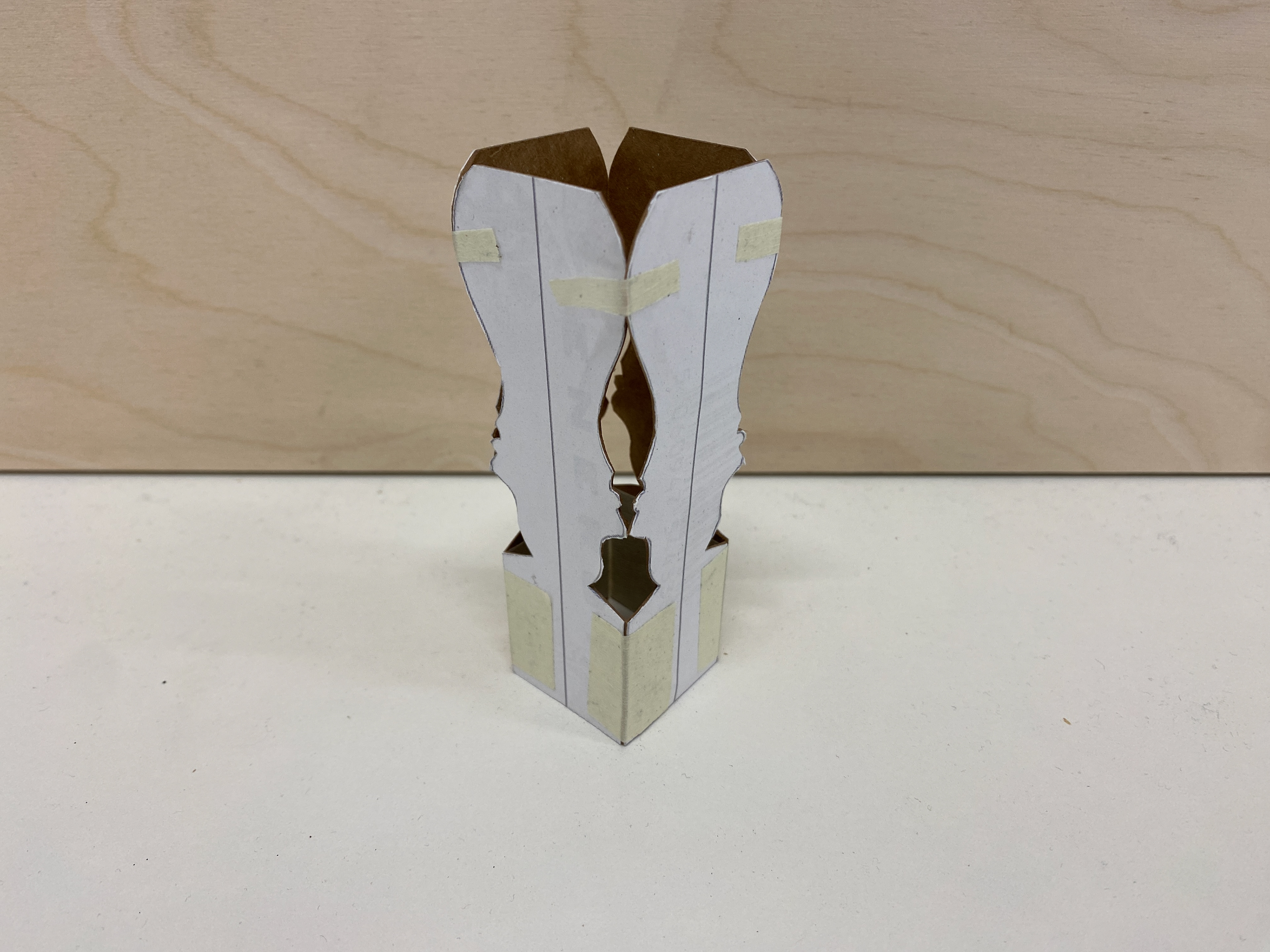
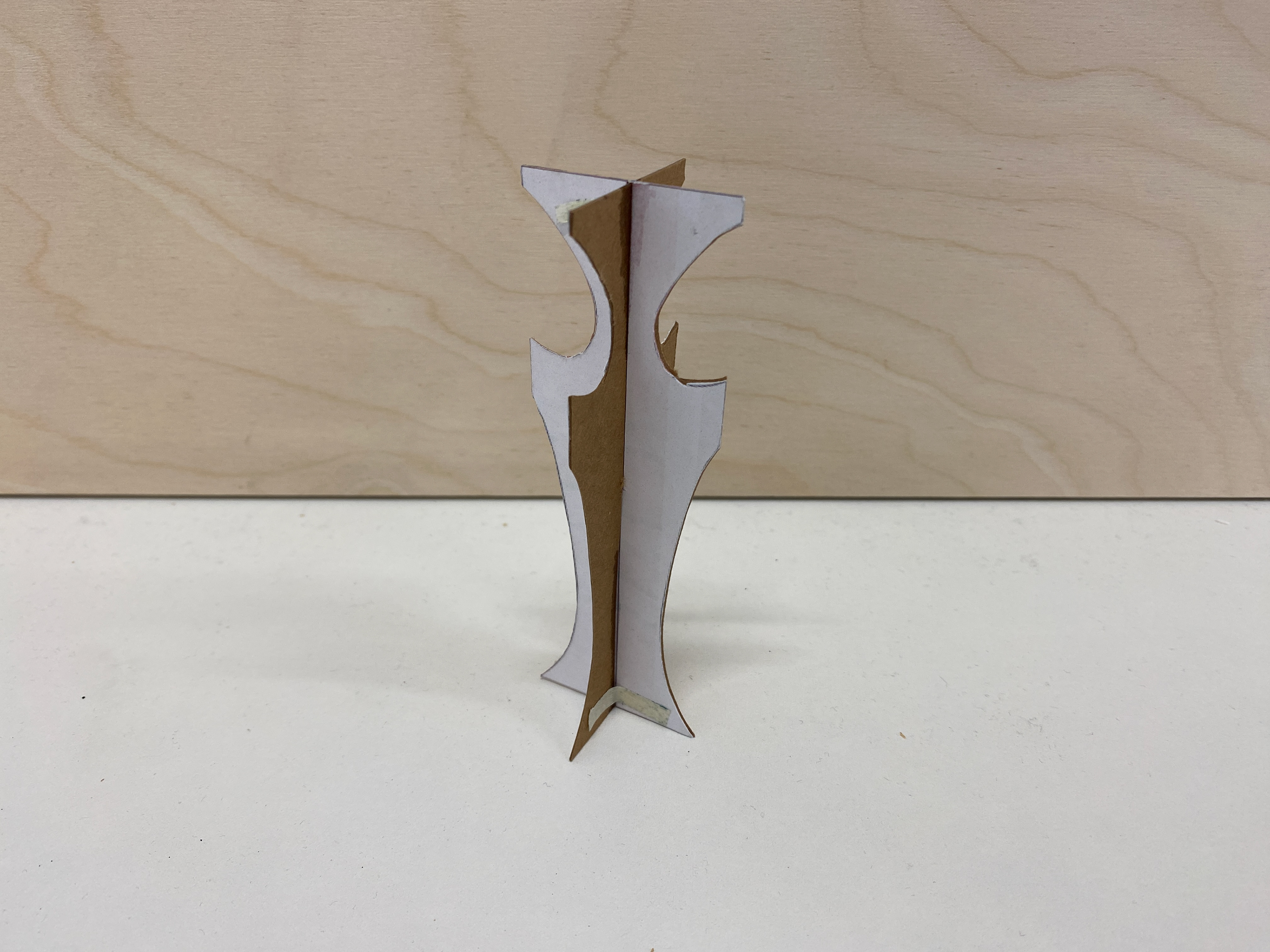
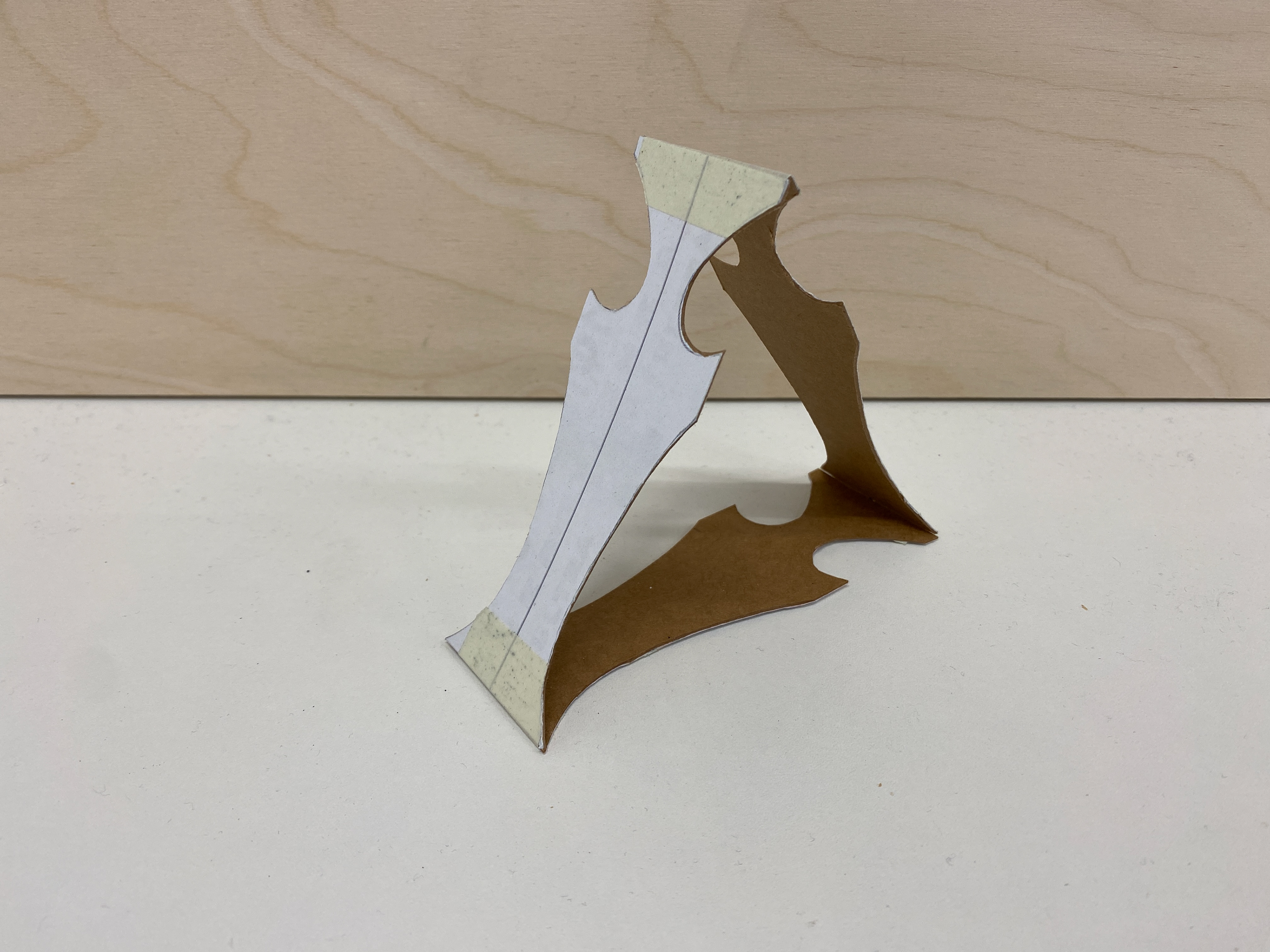

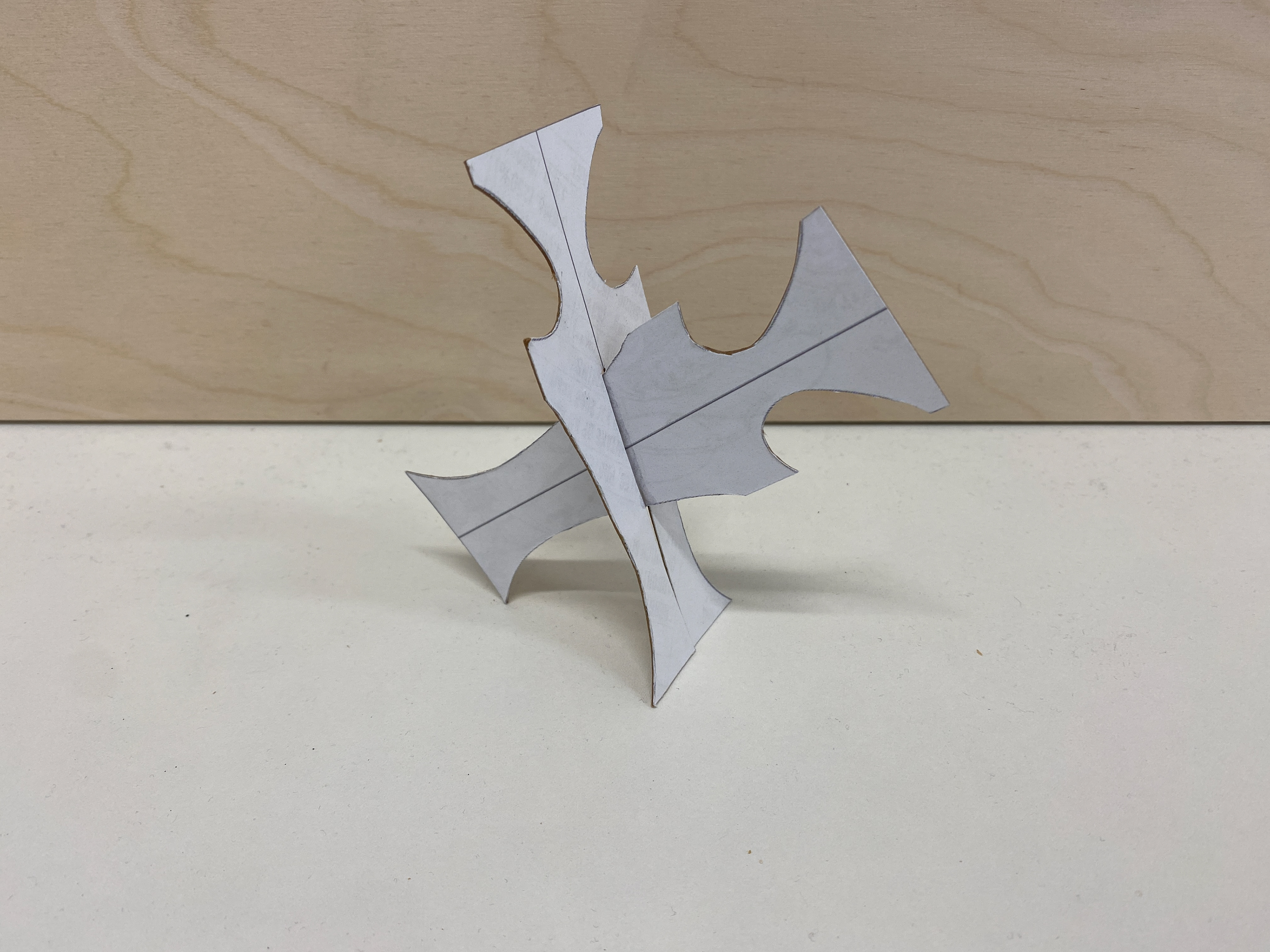
I experimented with a different approach, taking the extracted shapes and cutting them out of thick card and constructing quick 3D compositions. I wanted to bring in the idea of the repeats and rotations from the pattern work at the Parsonage. Furthermore, to study the interactions between each shape on different planes, taking inspiration from the weather vane that I saw at the V&A.
Experimenting with light and shadow
Initially, I had envisioned my 3D models to become rough designs that could be constructed using sheet steel, with scroll detailing added in. However, I found the interactions and negative space between the shapes intriguing and decided to explore using light and shadow to create new abstractions. Through, moving the singular light source around the space I manipulated the forms. I enjoyed the process and feel that using light and film is a good way to convey and direct the emotion and atmosphere of the work.
Using shadow to design
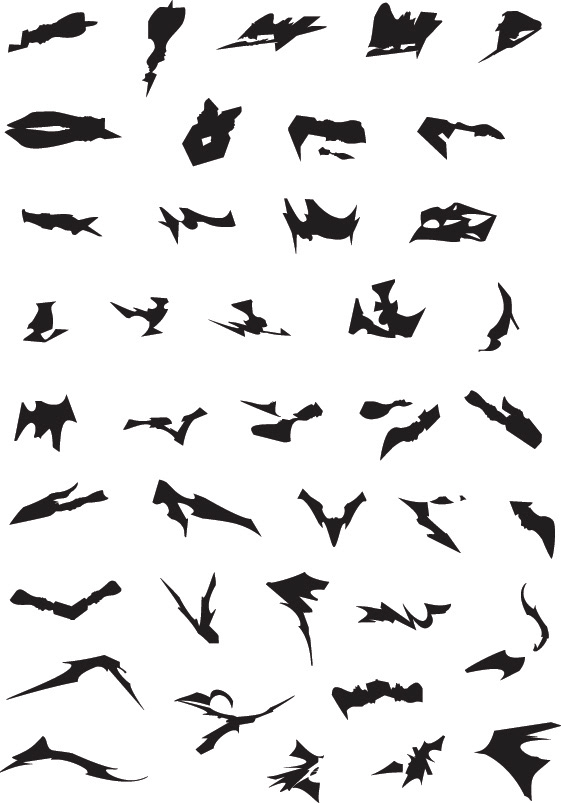
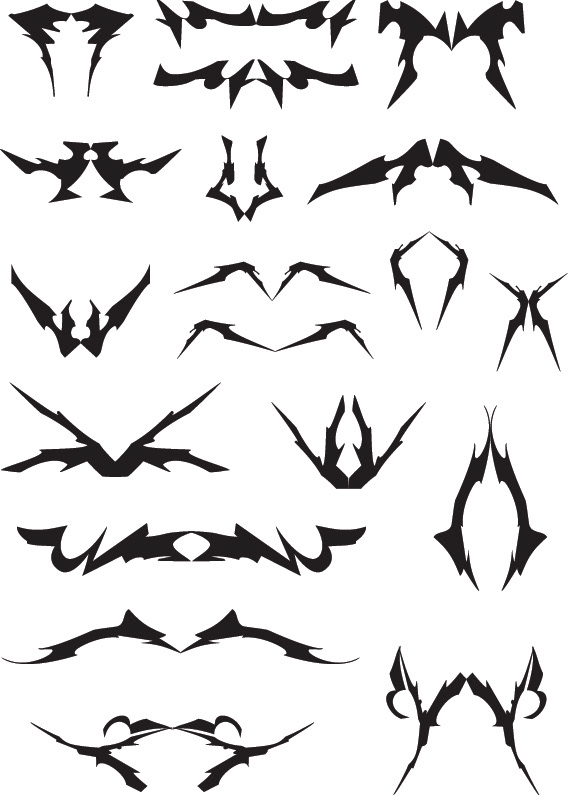
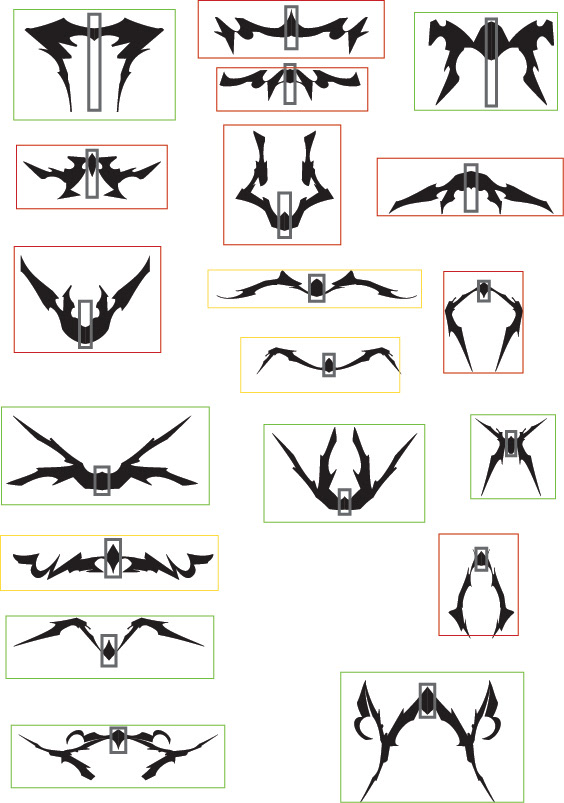
I traced the shadows of from the film taking the shapes that I thought would look best wrapping over the scrolls. I then tested multiple different ways of rotating and reflecting the shapes, to create mirrored designs, that meet in one central point which will attach the forms to the scrolls. I added in the width of the flat bar and tested which shapes interacted best with the scrolls. I found that I needed to scale this up like previously mentioned to use 25mm steel rather than 13mm, as the intricate elements would be too hard to cut out in steel.
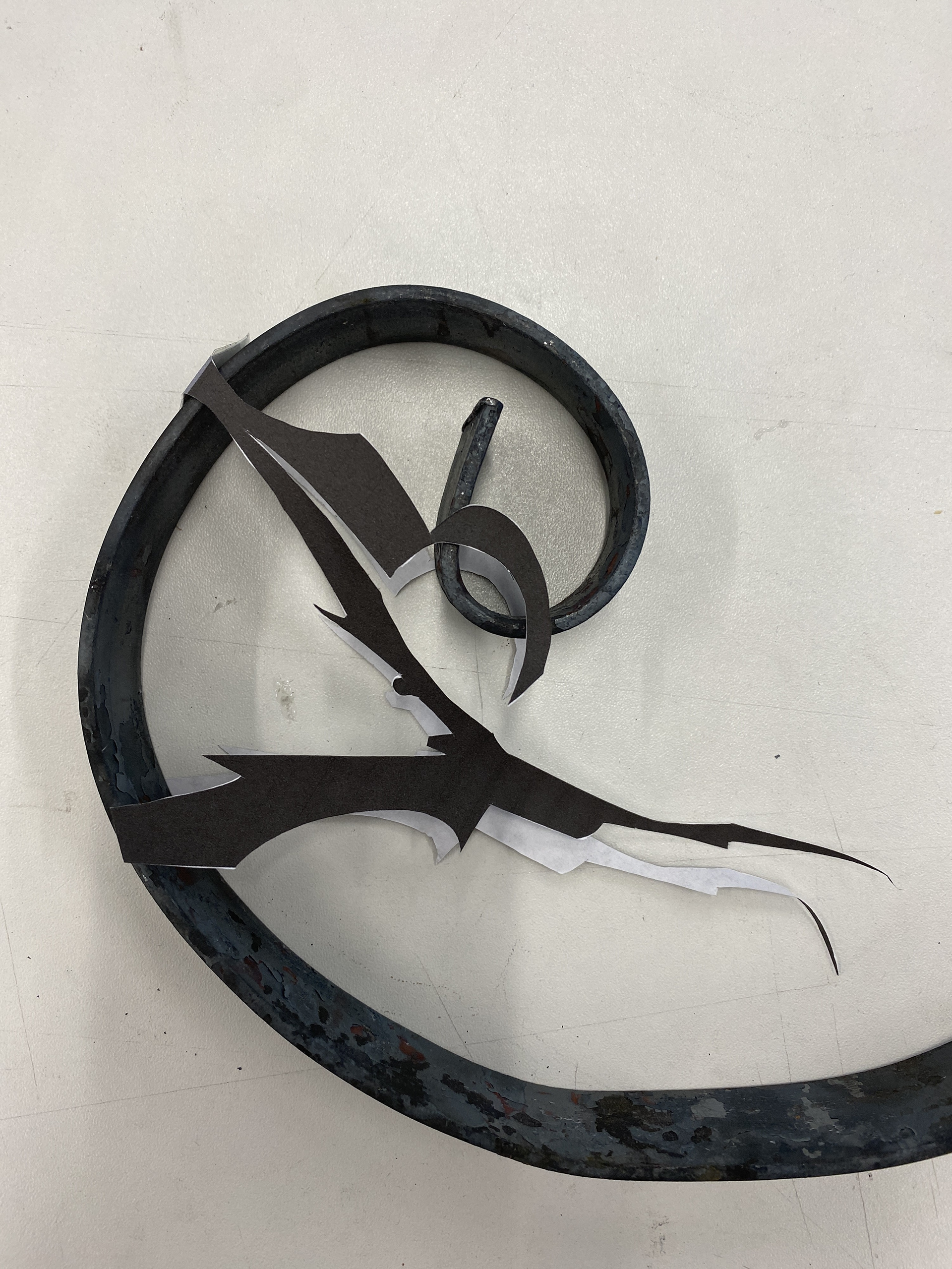
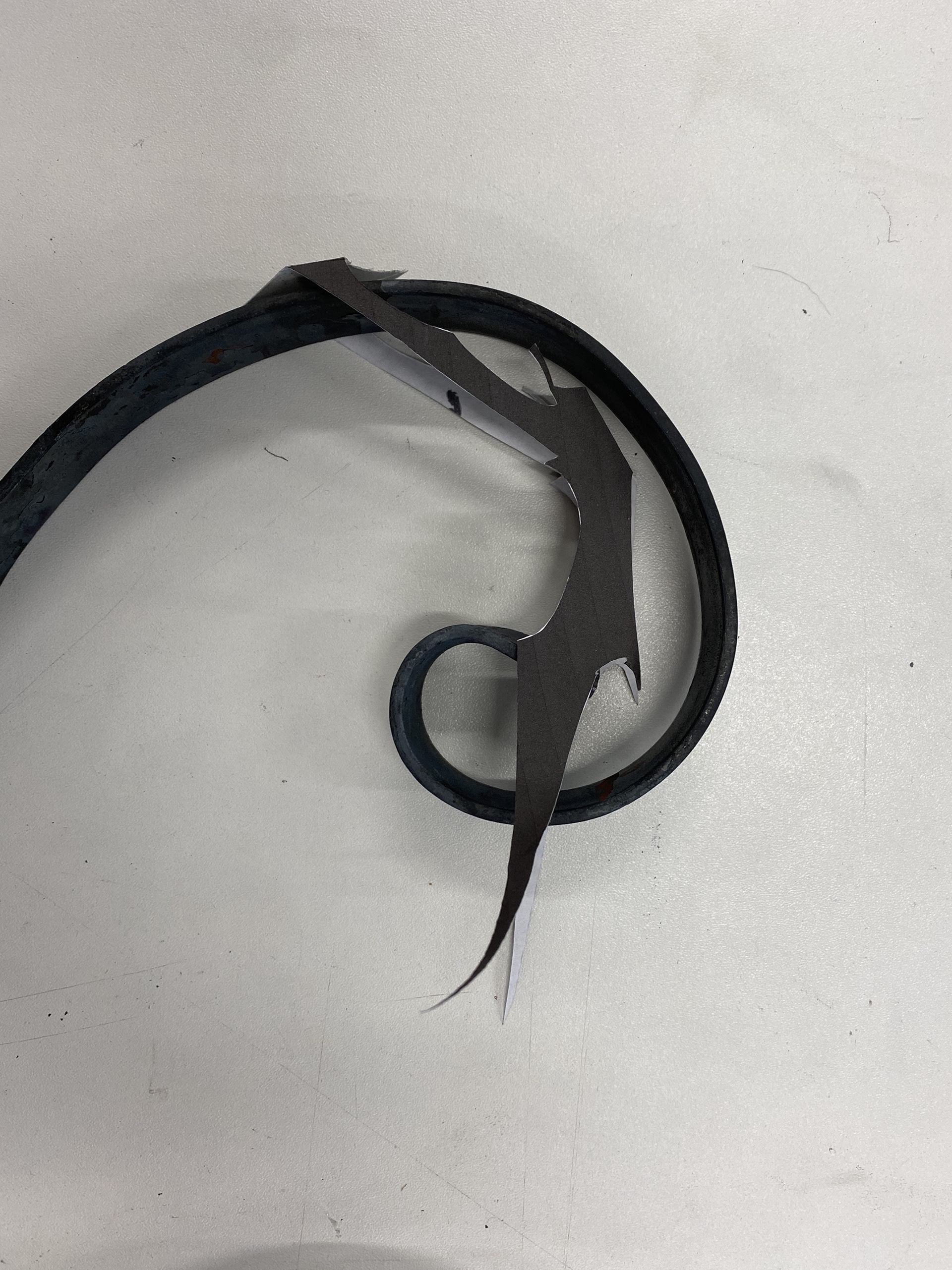
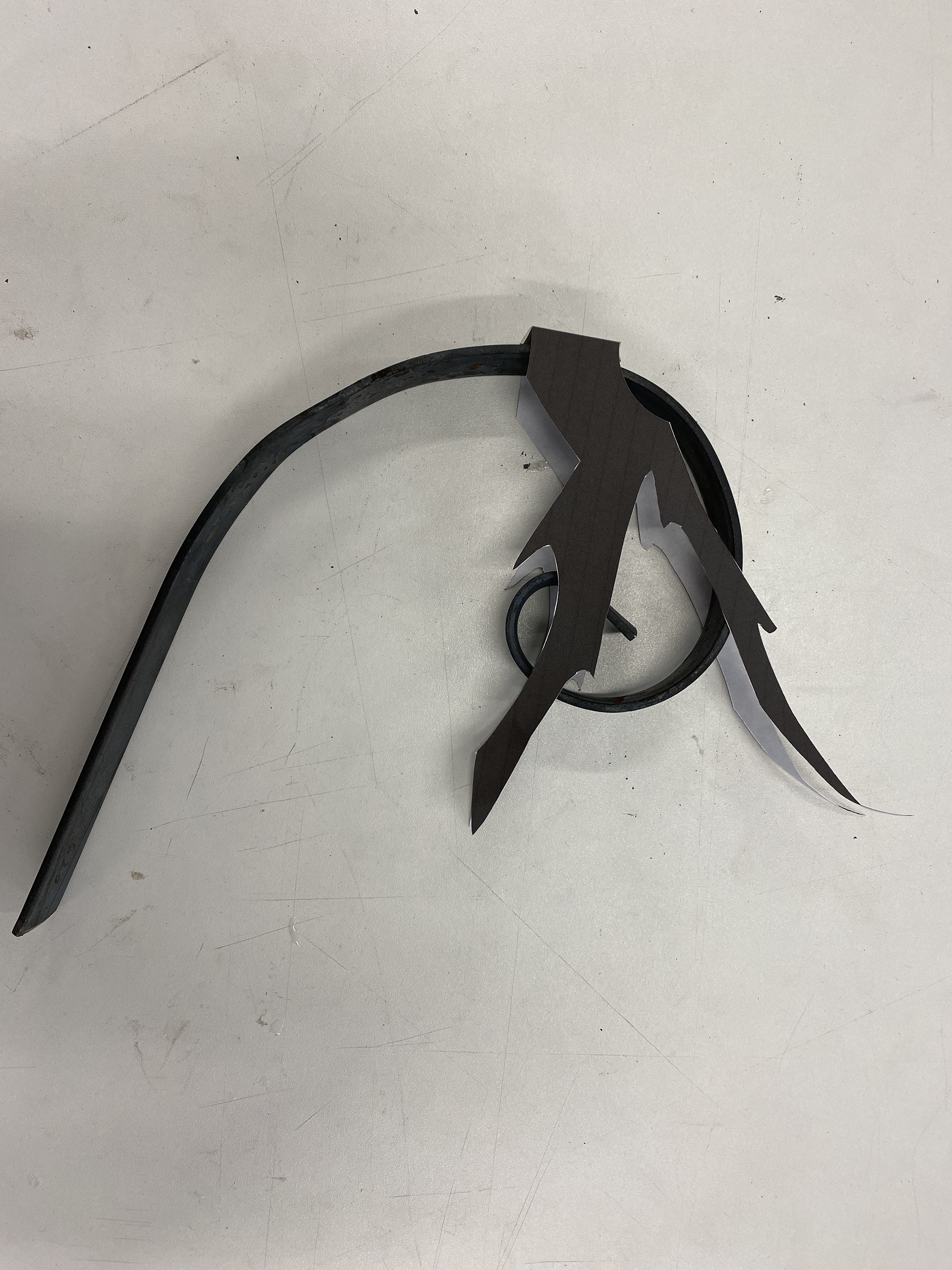
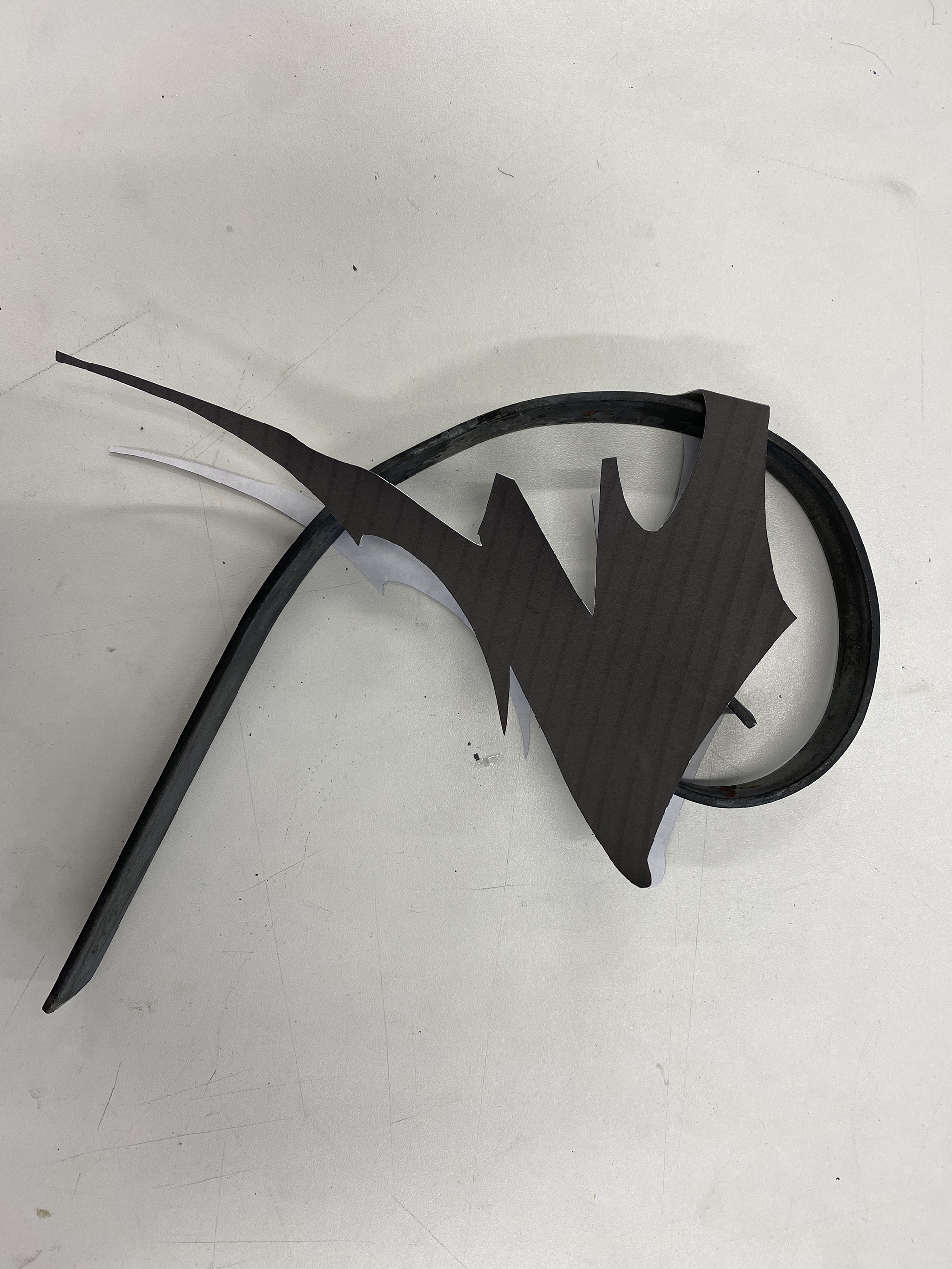
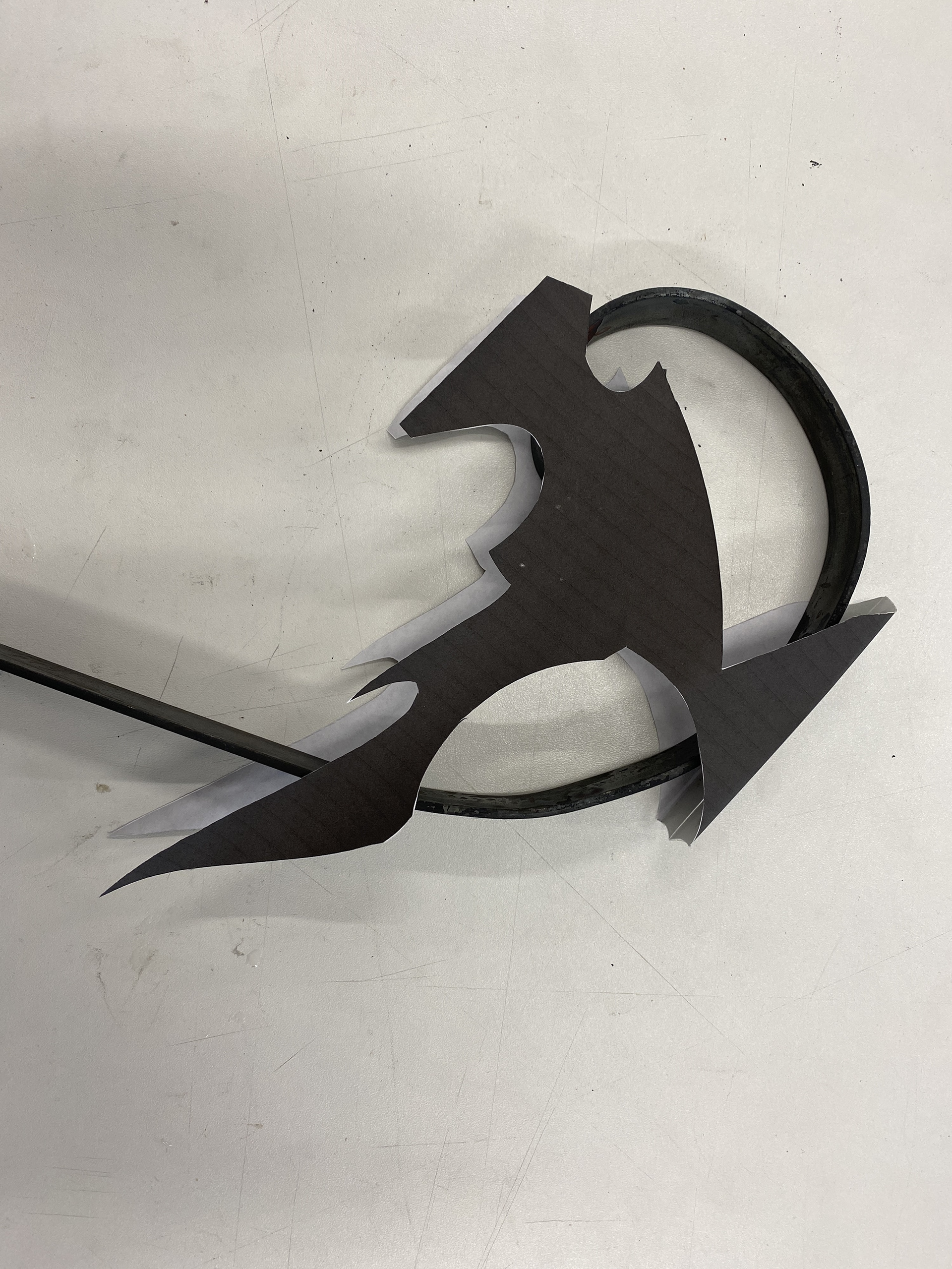
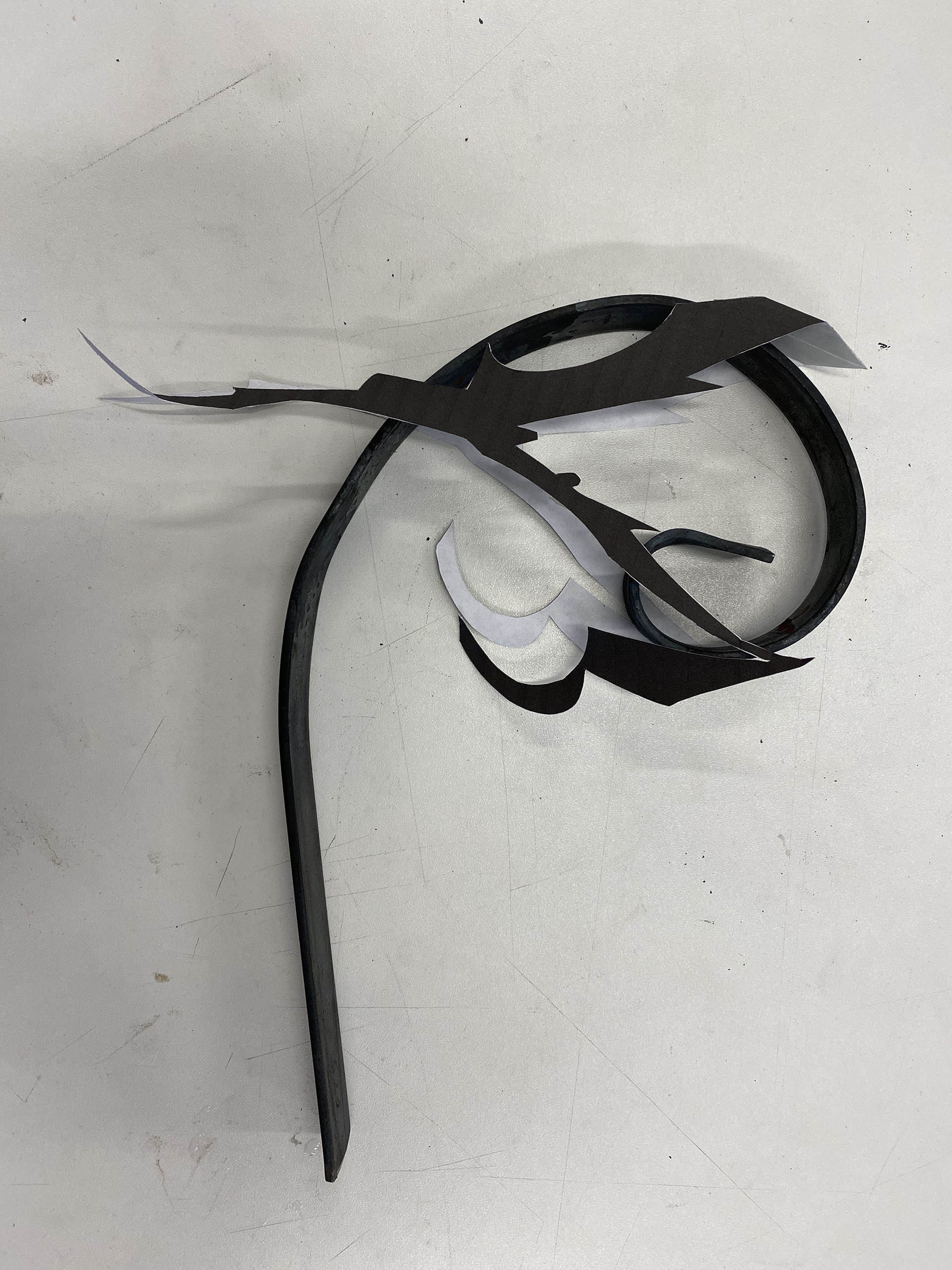
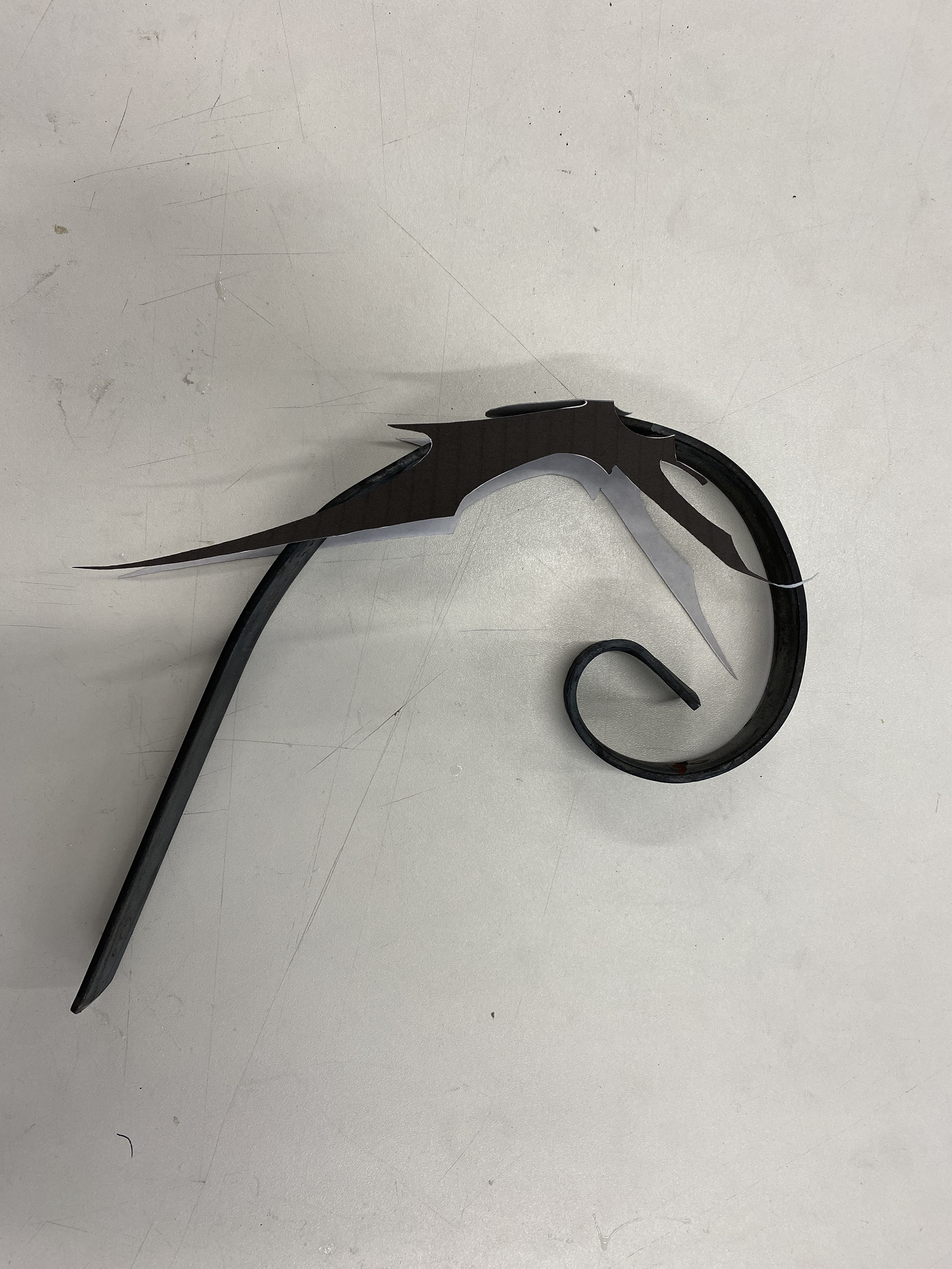
I tested the paper shapes over scrolls made from the 3x25mm flat bar and found that the 4 shapes on the left above worked the best.
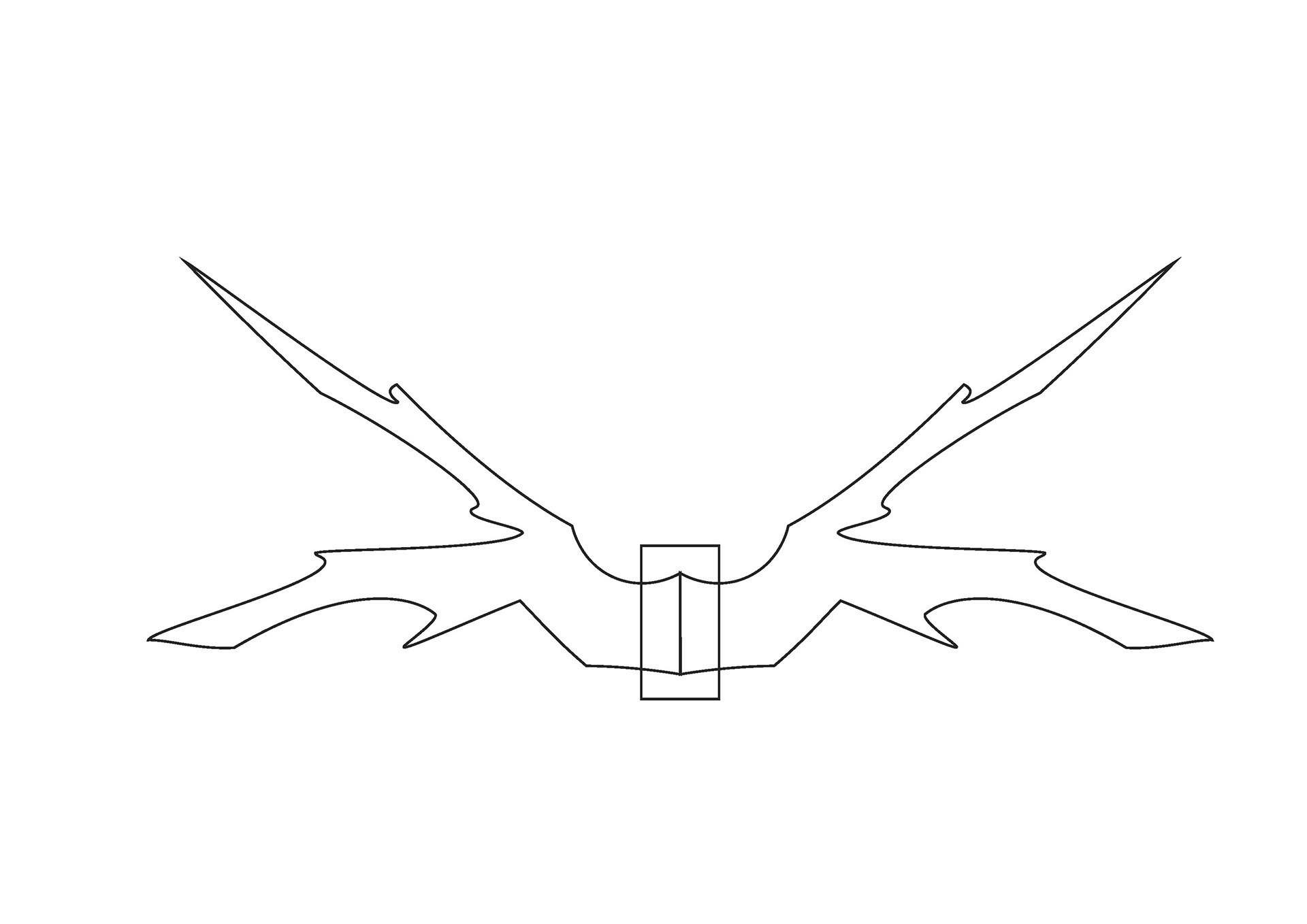
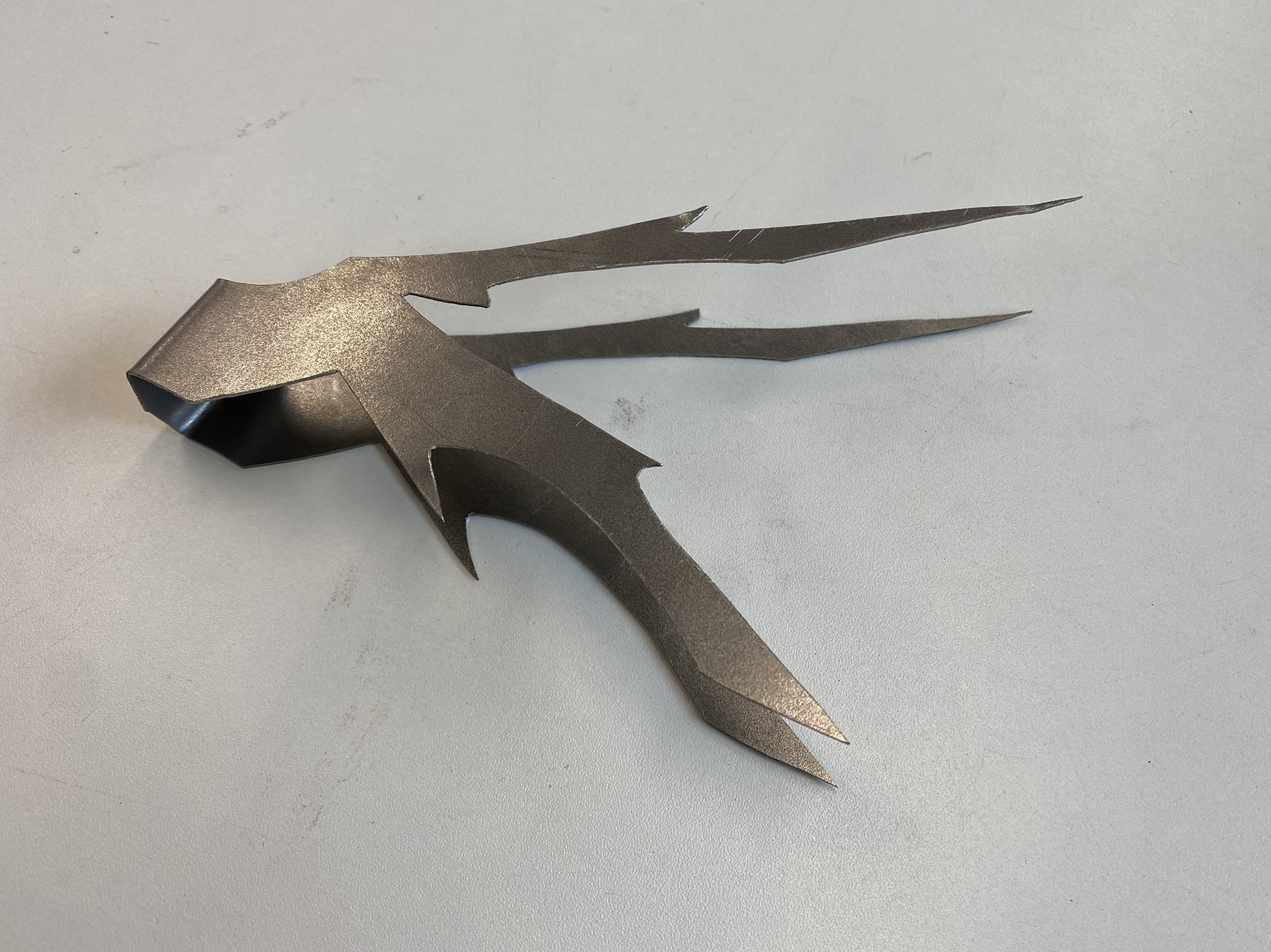
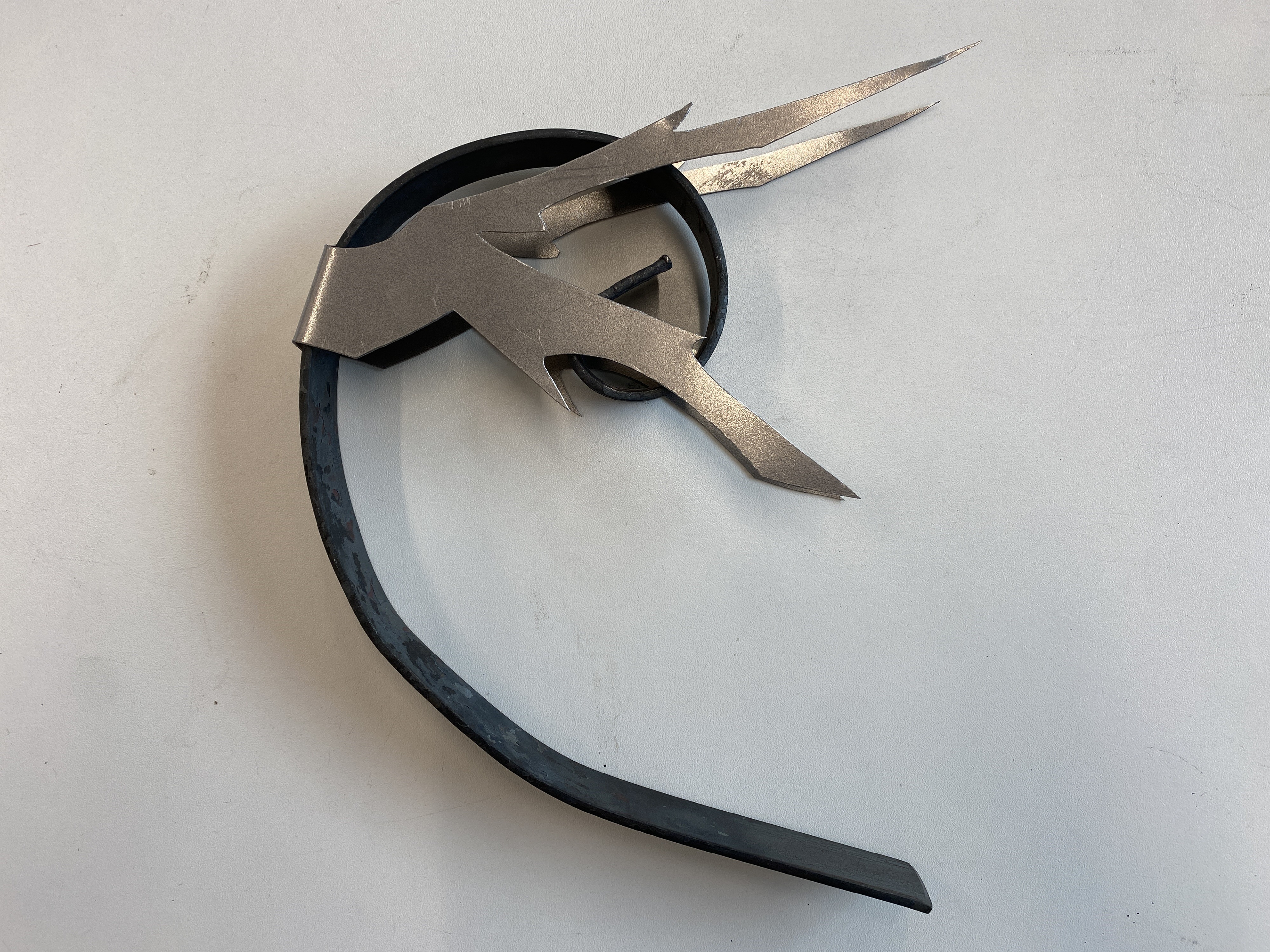

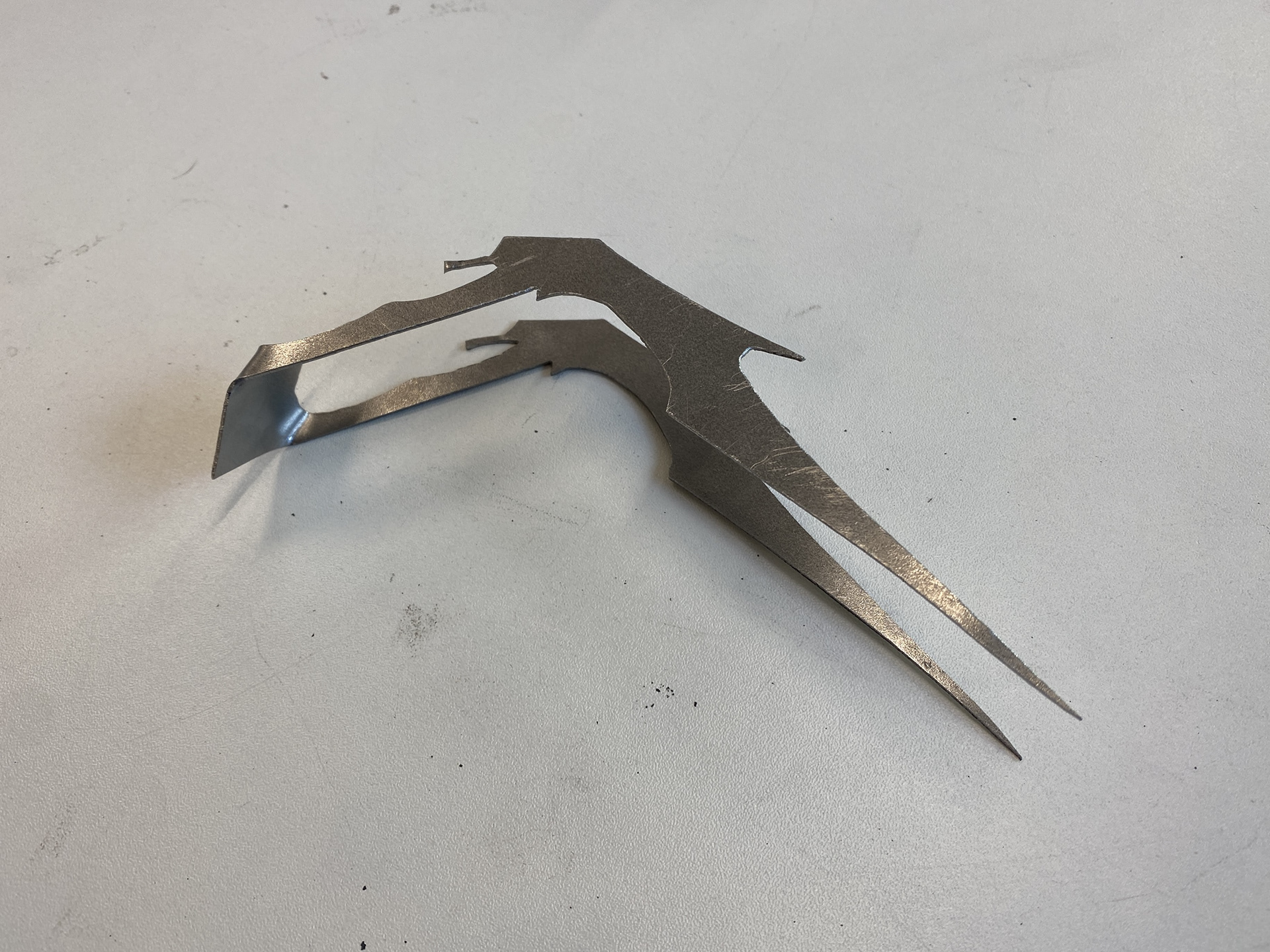
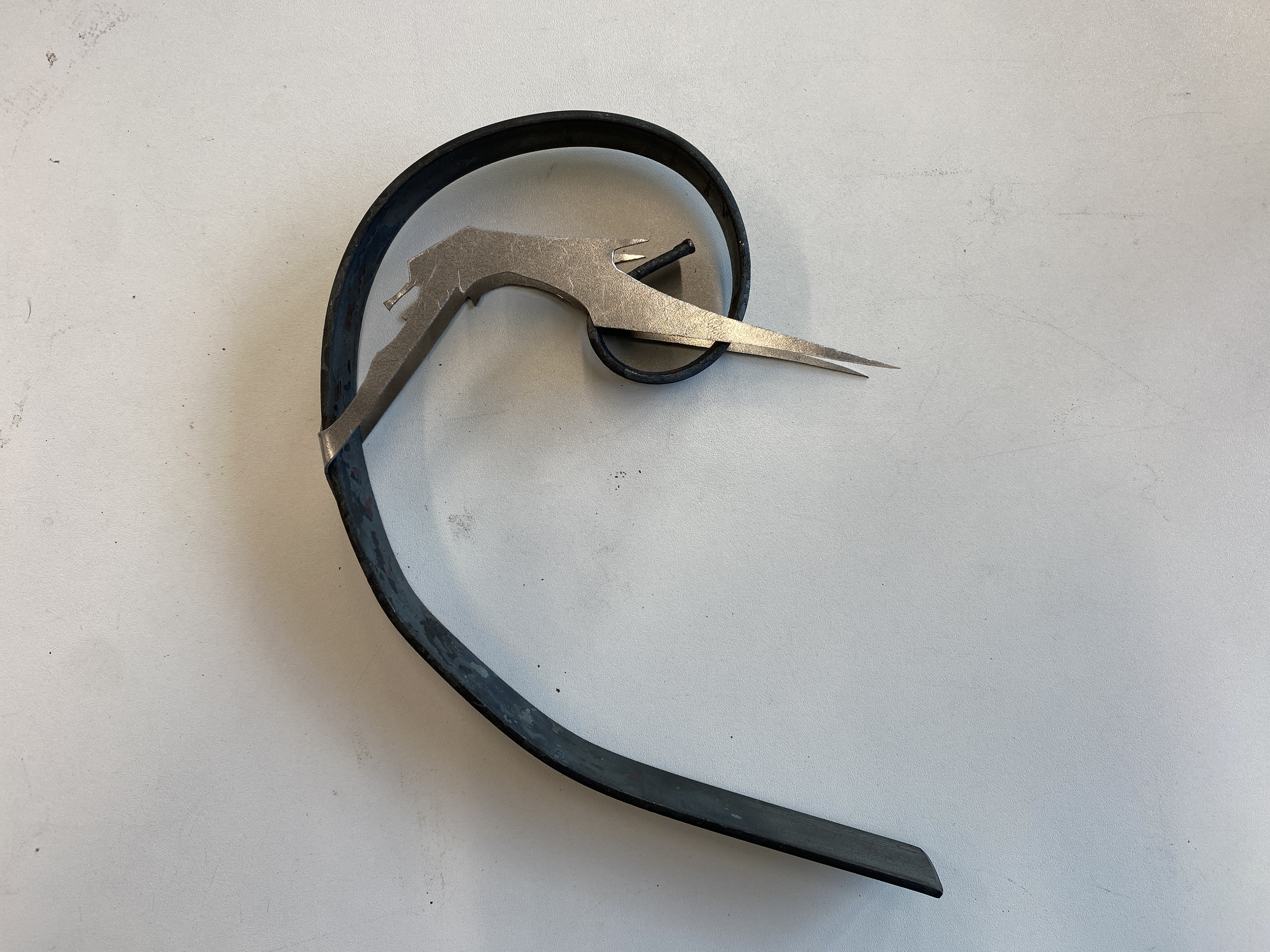
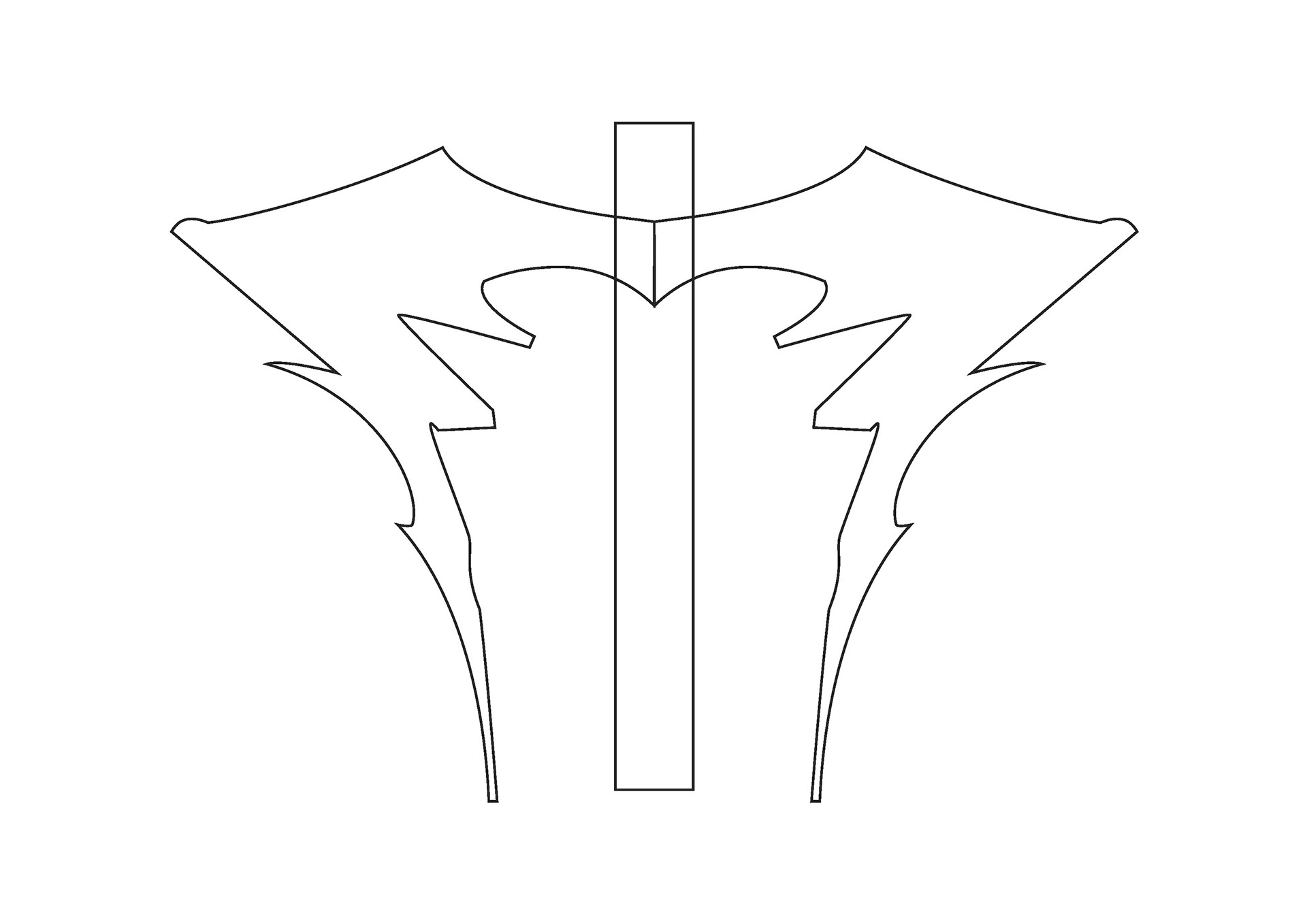
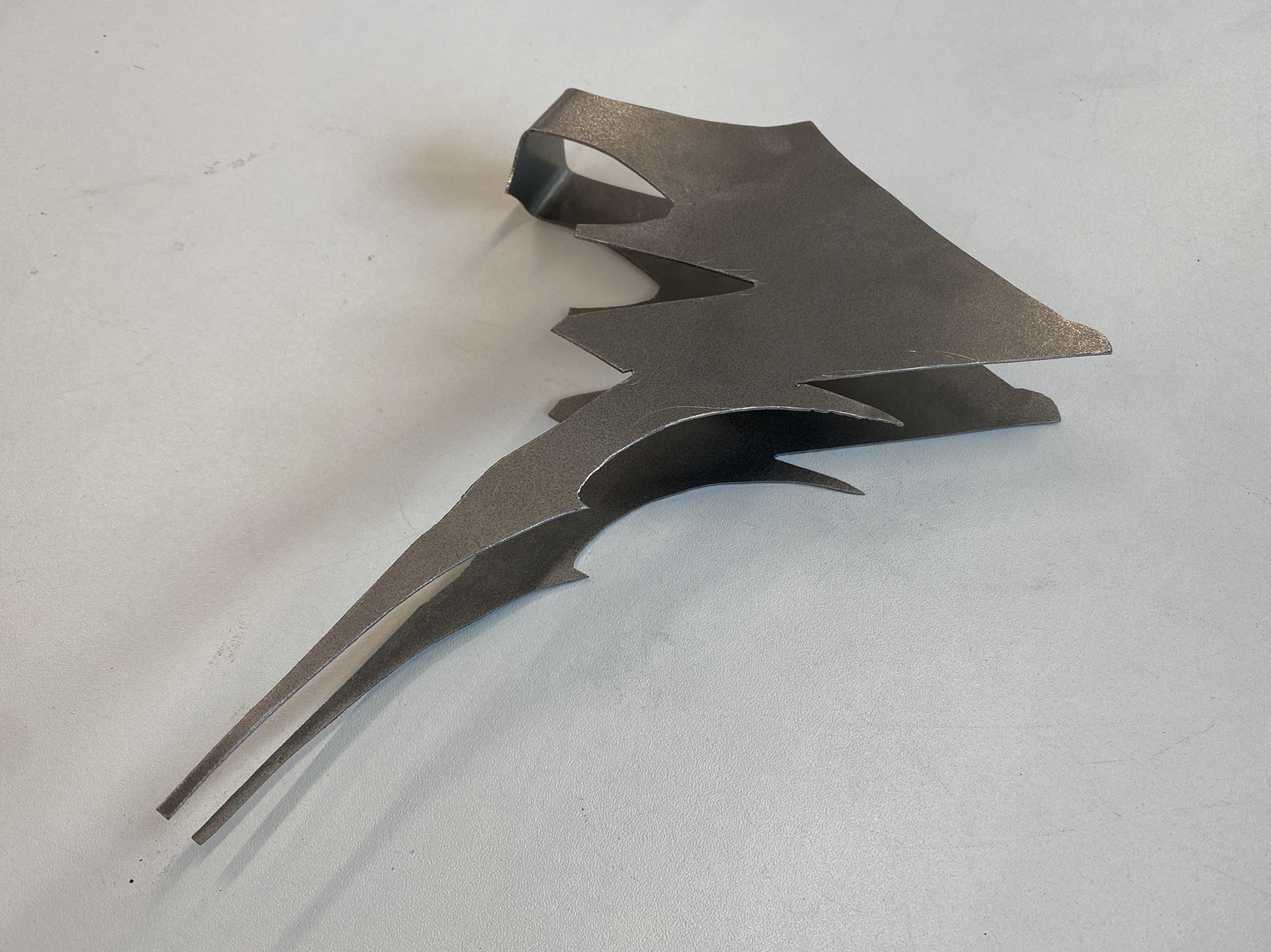
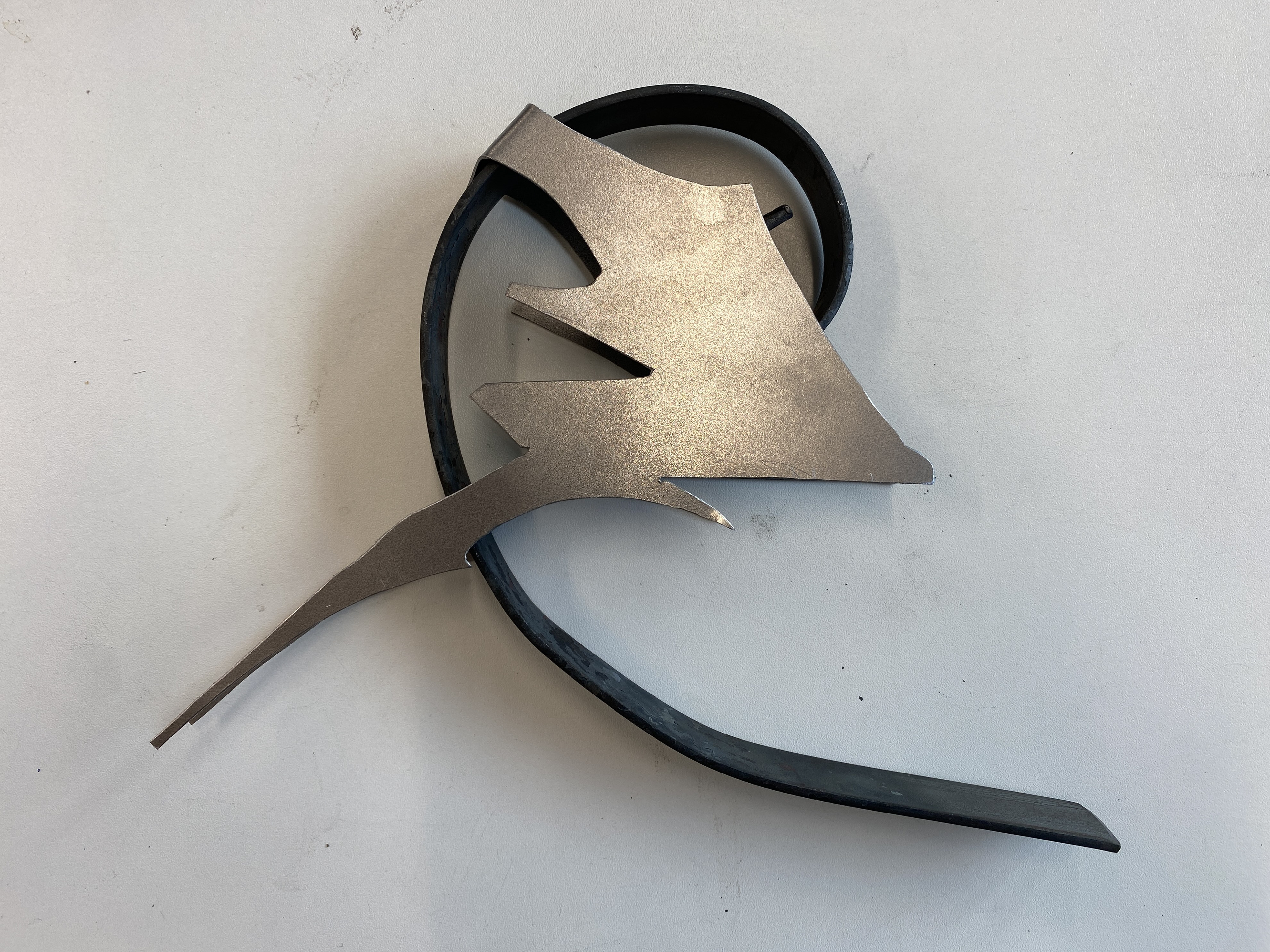
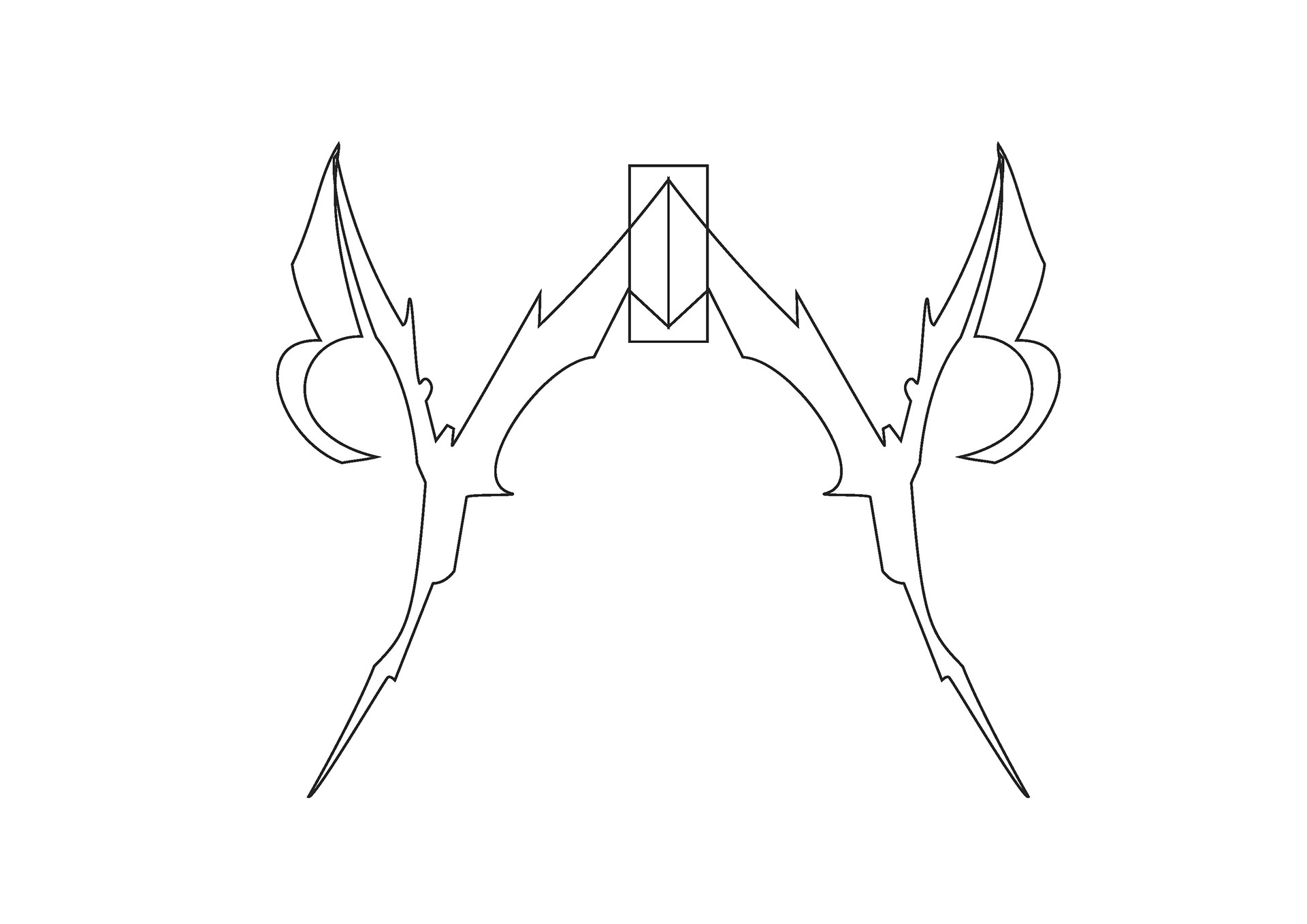
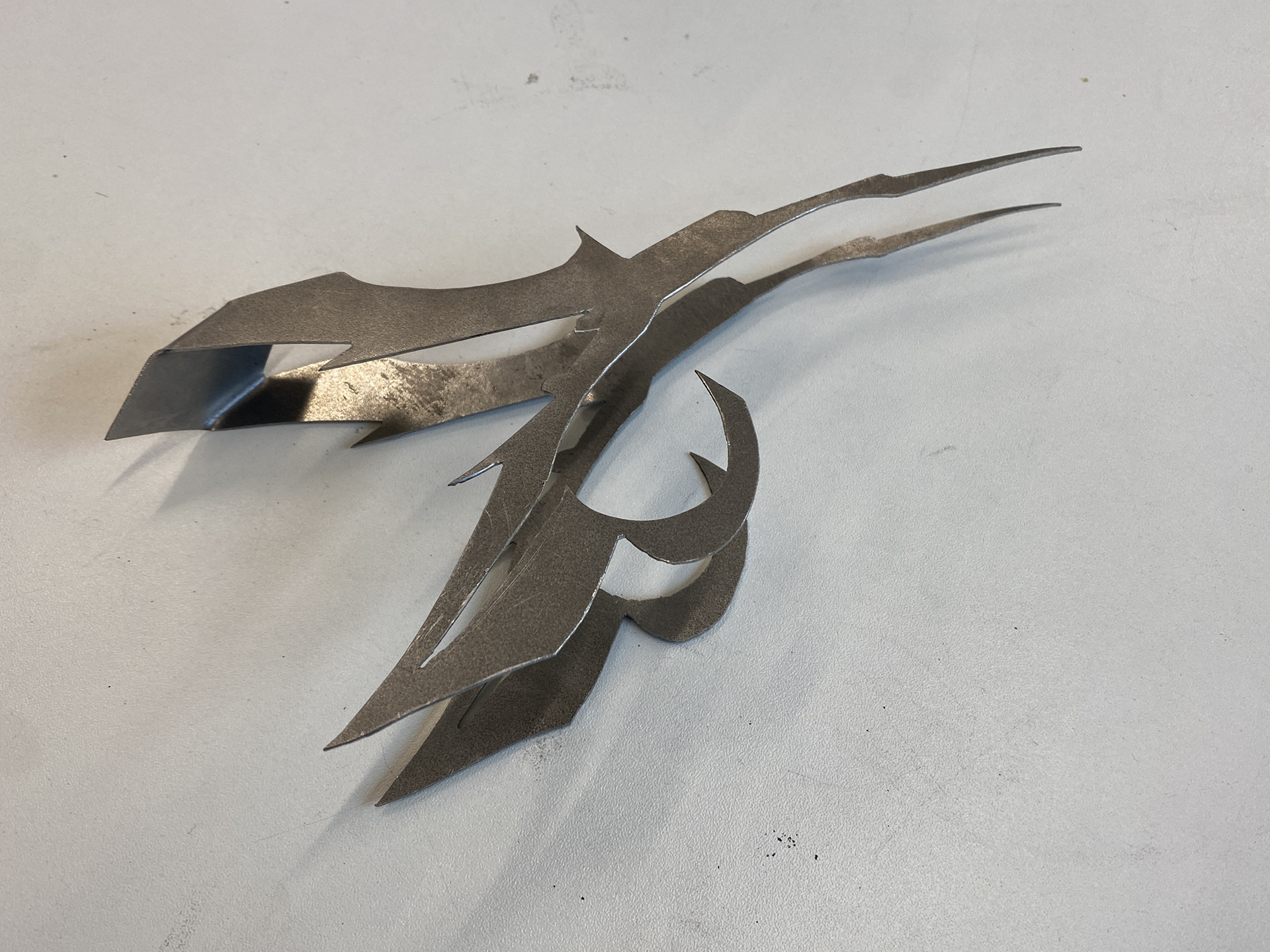
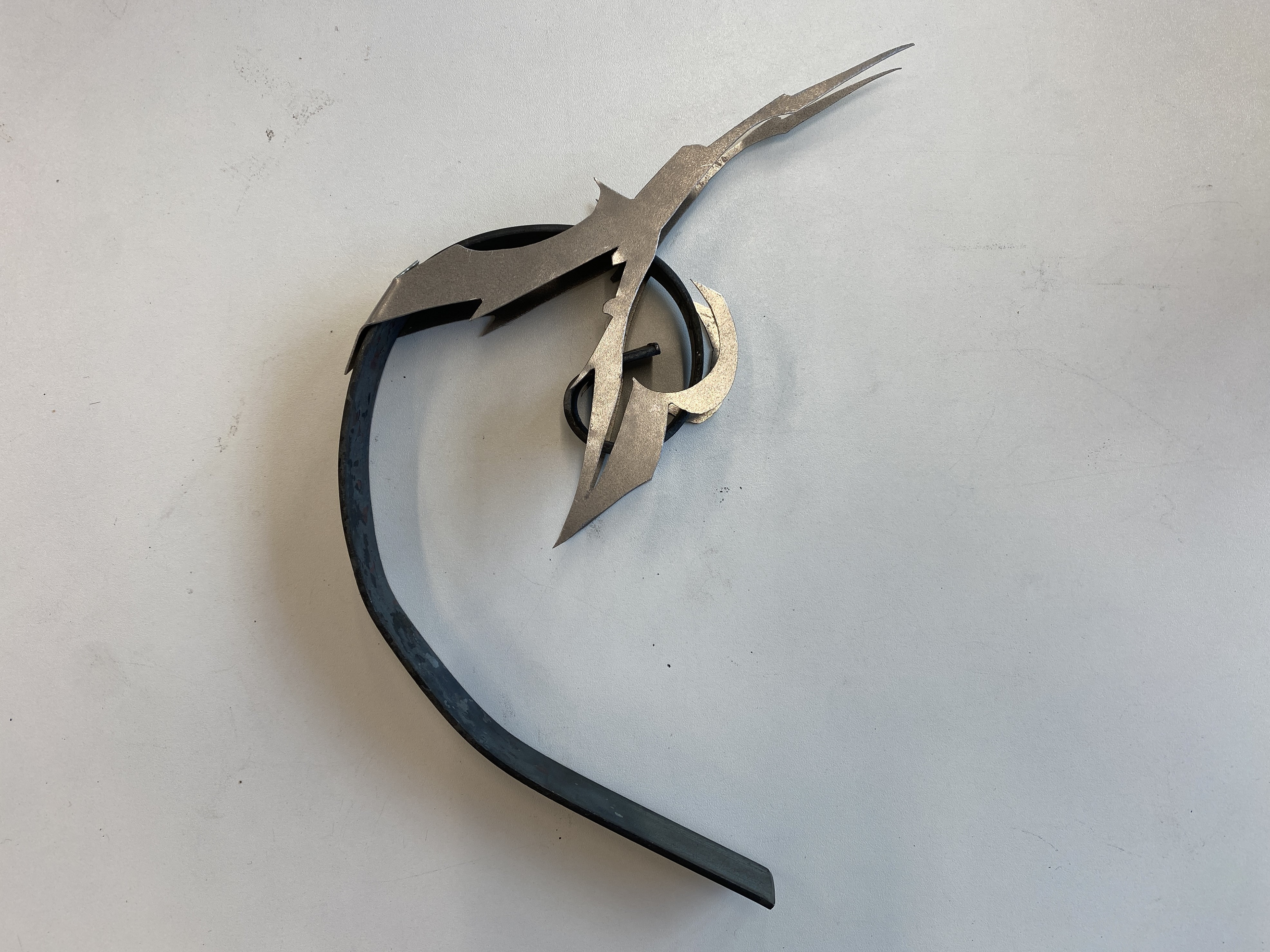
I took these into 0.7mm steel by cutting them out using the bandsaw and folding them in a vice. During the making process I felt that there was too much of a contrast between the bright reflective sheet steel and the blackened flat bar. I was thinking of experimenting with different ways to colour or alter the sheet steel's appearance but decided I like the idea of using raw unaltered material. I don't want to apply any finishes and purposely want to encourage the development of rust. This will bring through the narrative of impermanence of ironwork and its inevitable return to nature.
Designing the main structure using the Golden Ratio
To create the main structure of the piece I decided to use the Golden Ratio. This keeps the idea of rectangular constriction. The system can easily be rotated, reflected, and scaled to ensure the scrolls line up. Additionally, I like the fact that it brings an element of nature into the design which contrasts well with the highly angular and stylised decorative pieces. This is in contrast to traditional ironwork which mainly uses nature as decoration through leaves and flowers.
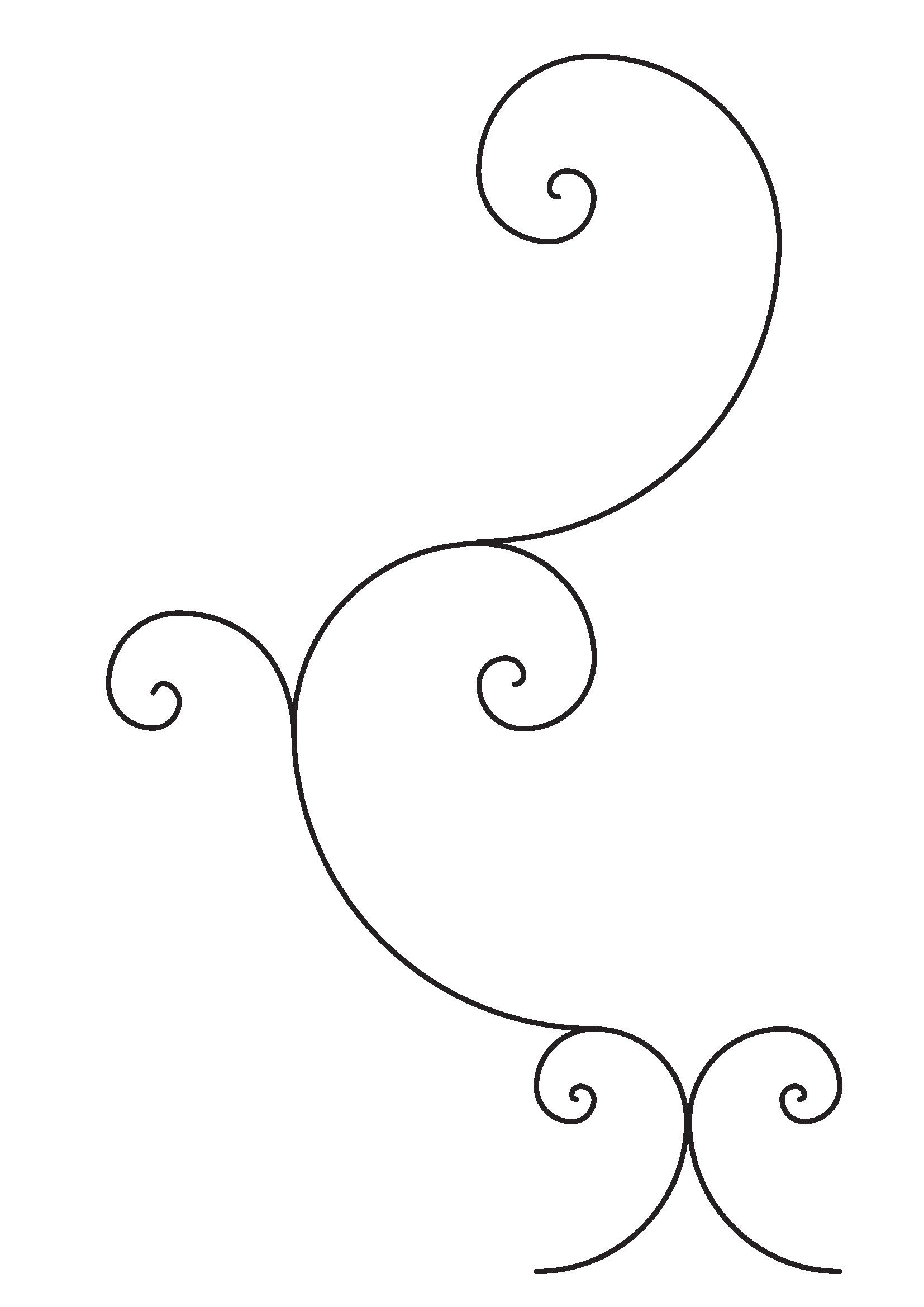
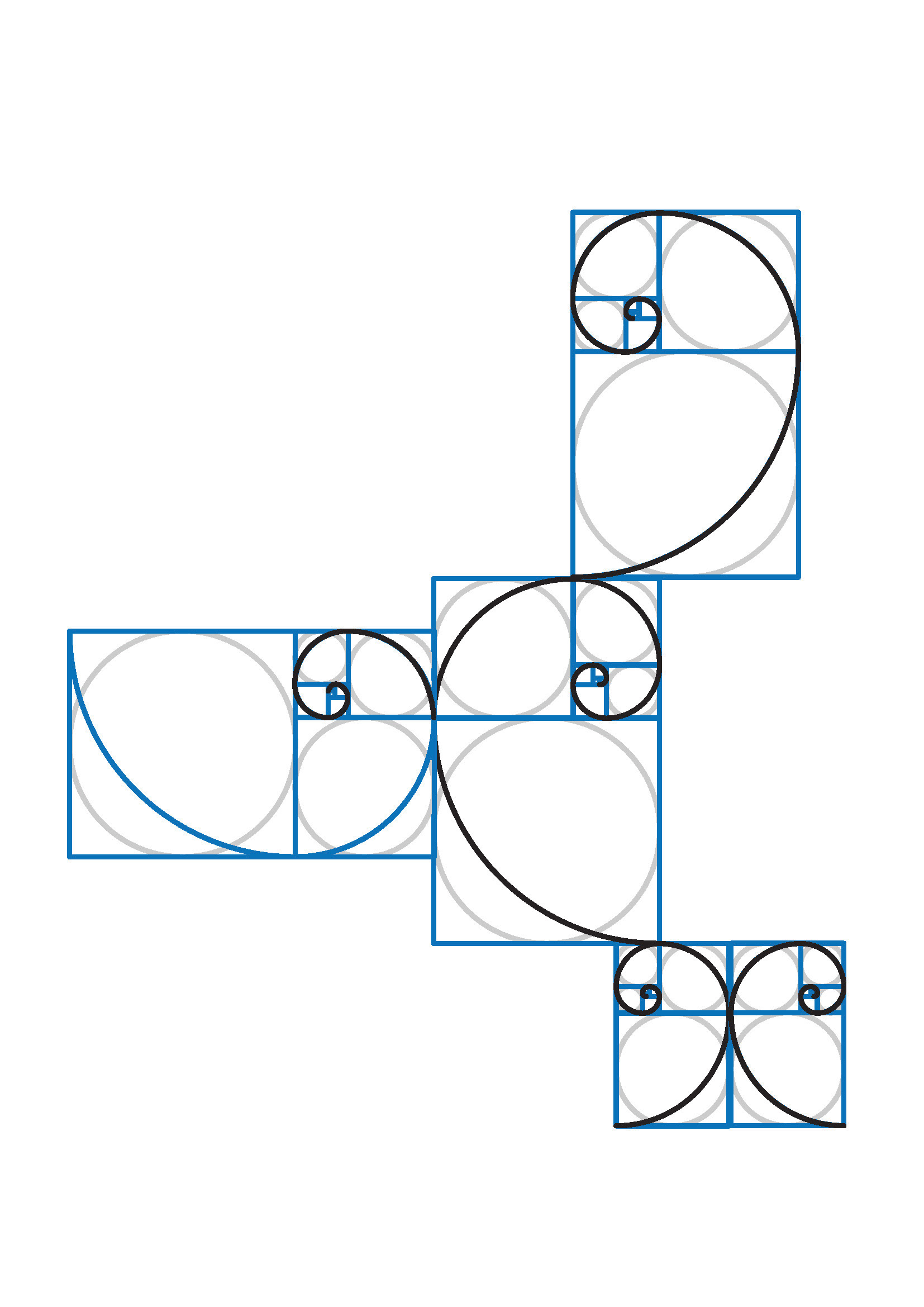
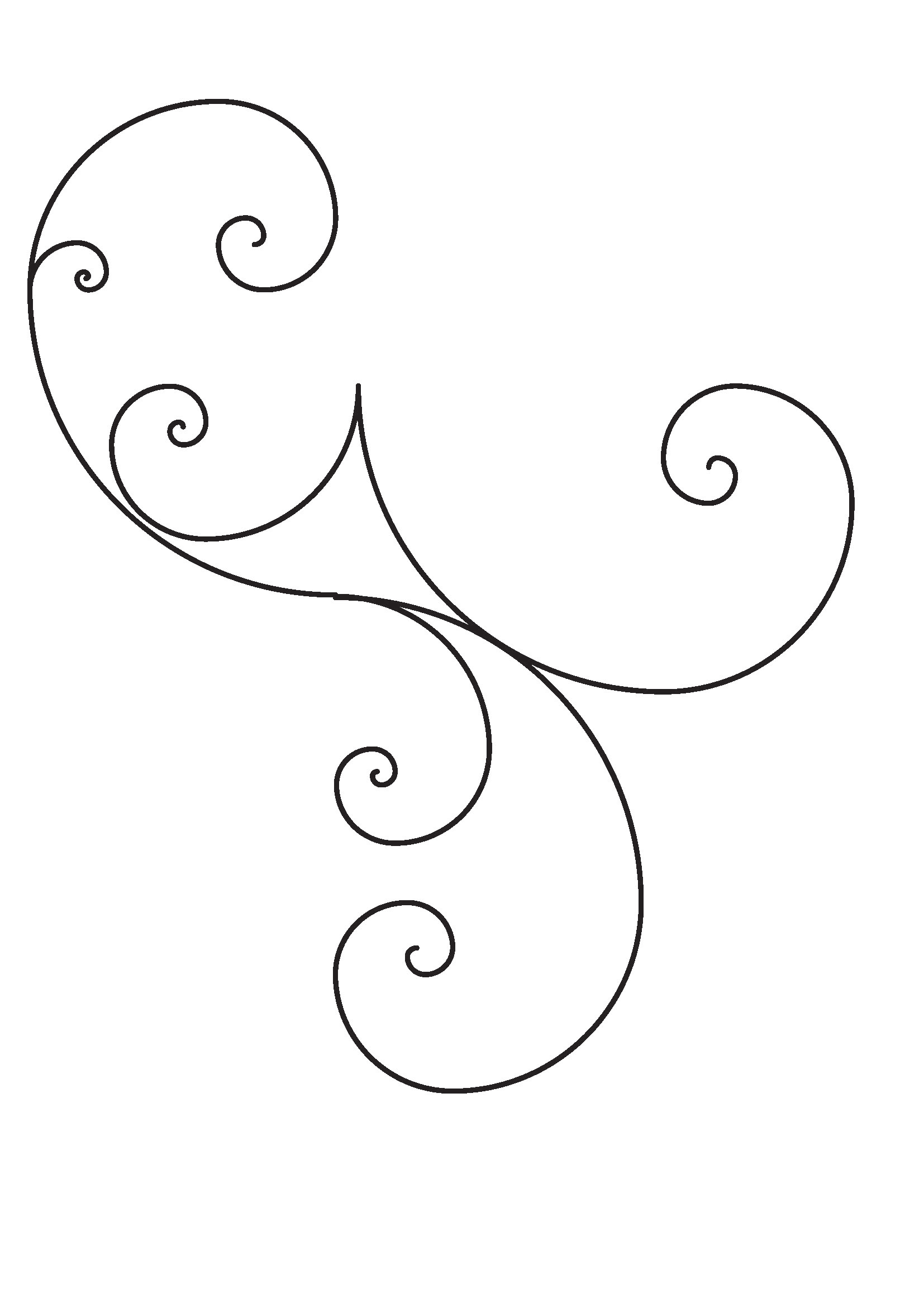
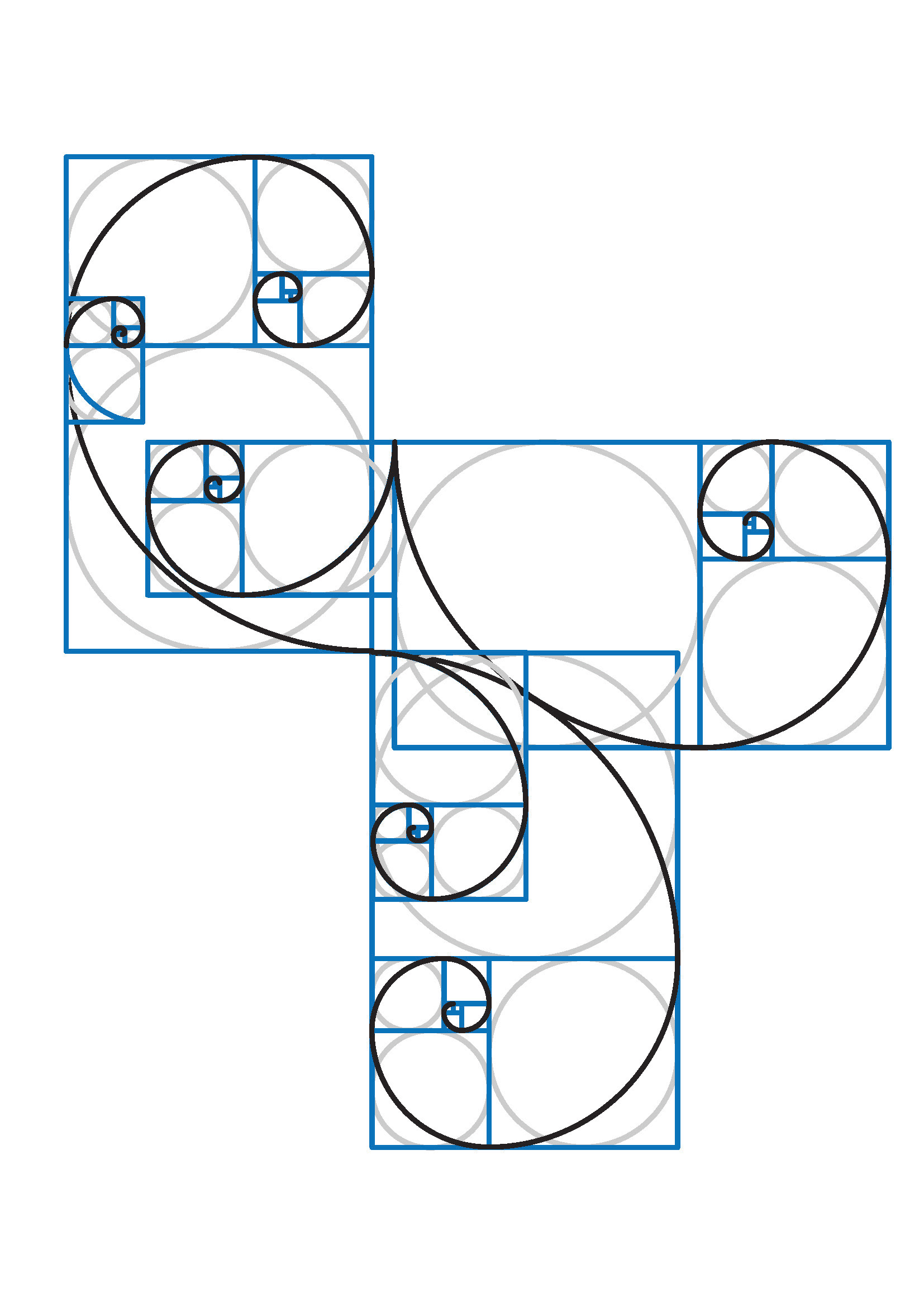
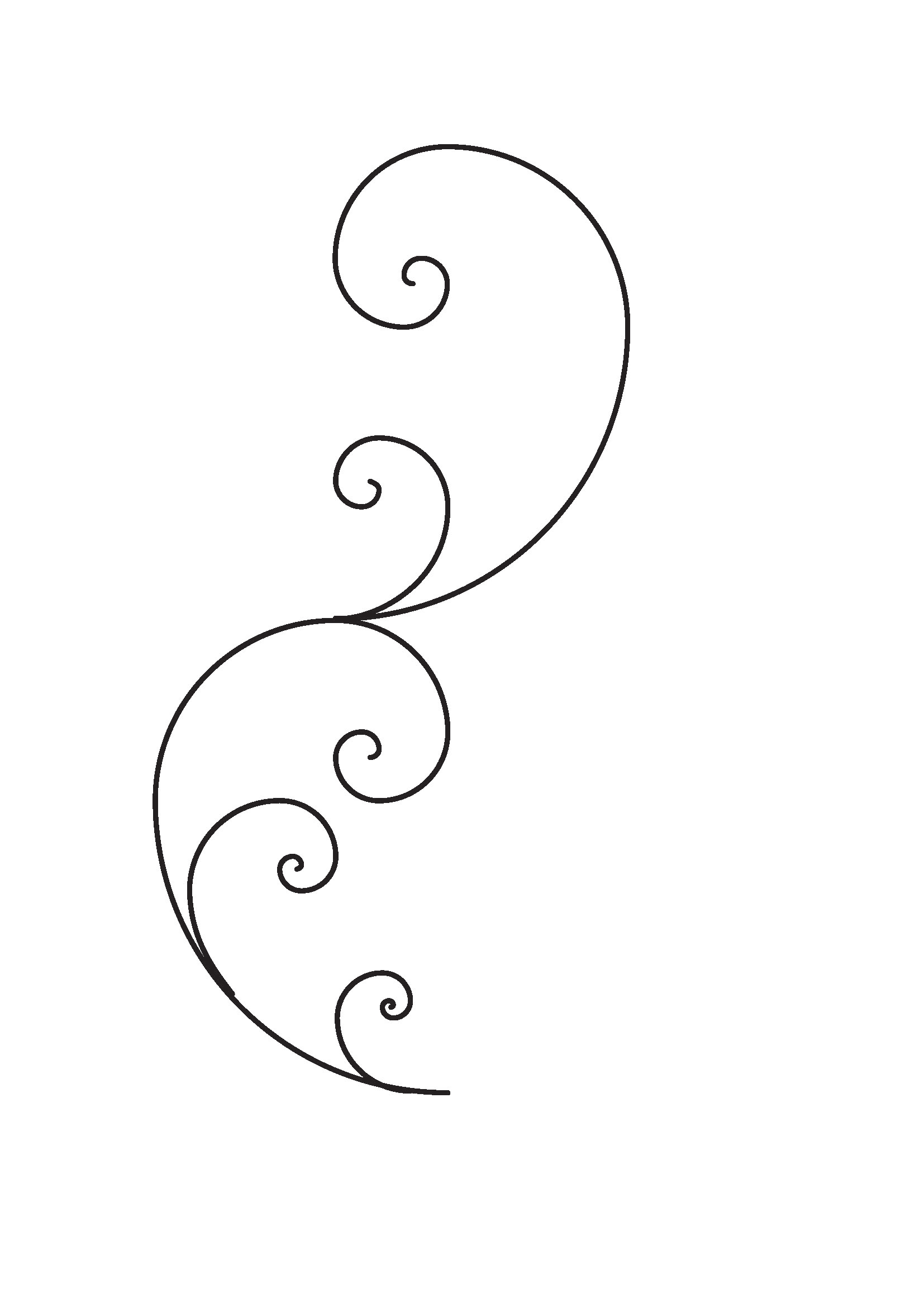
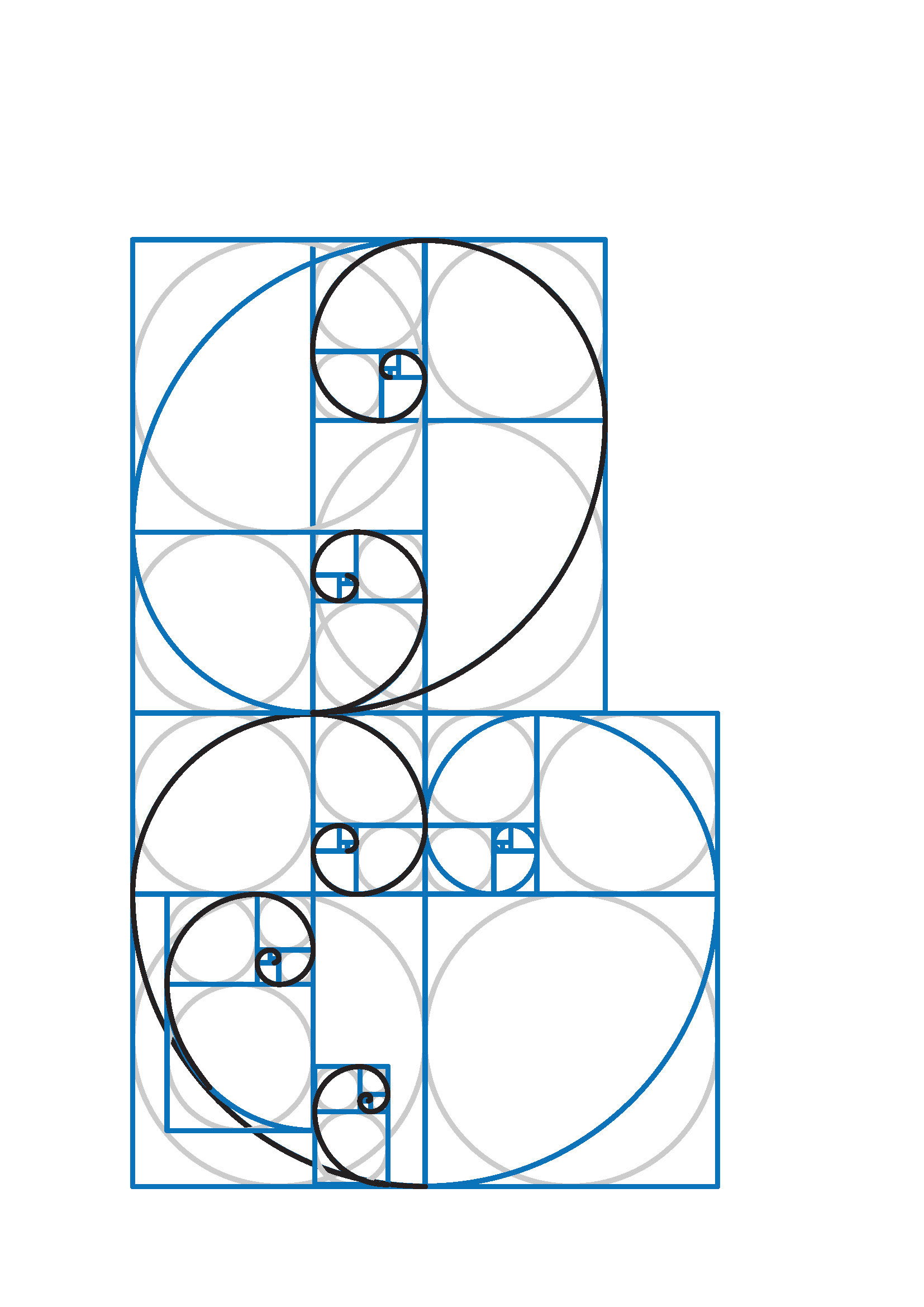
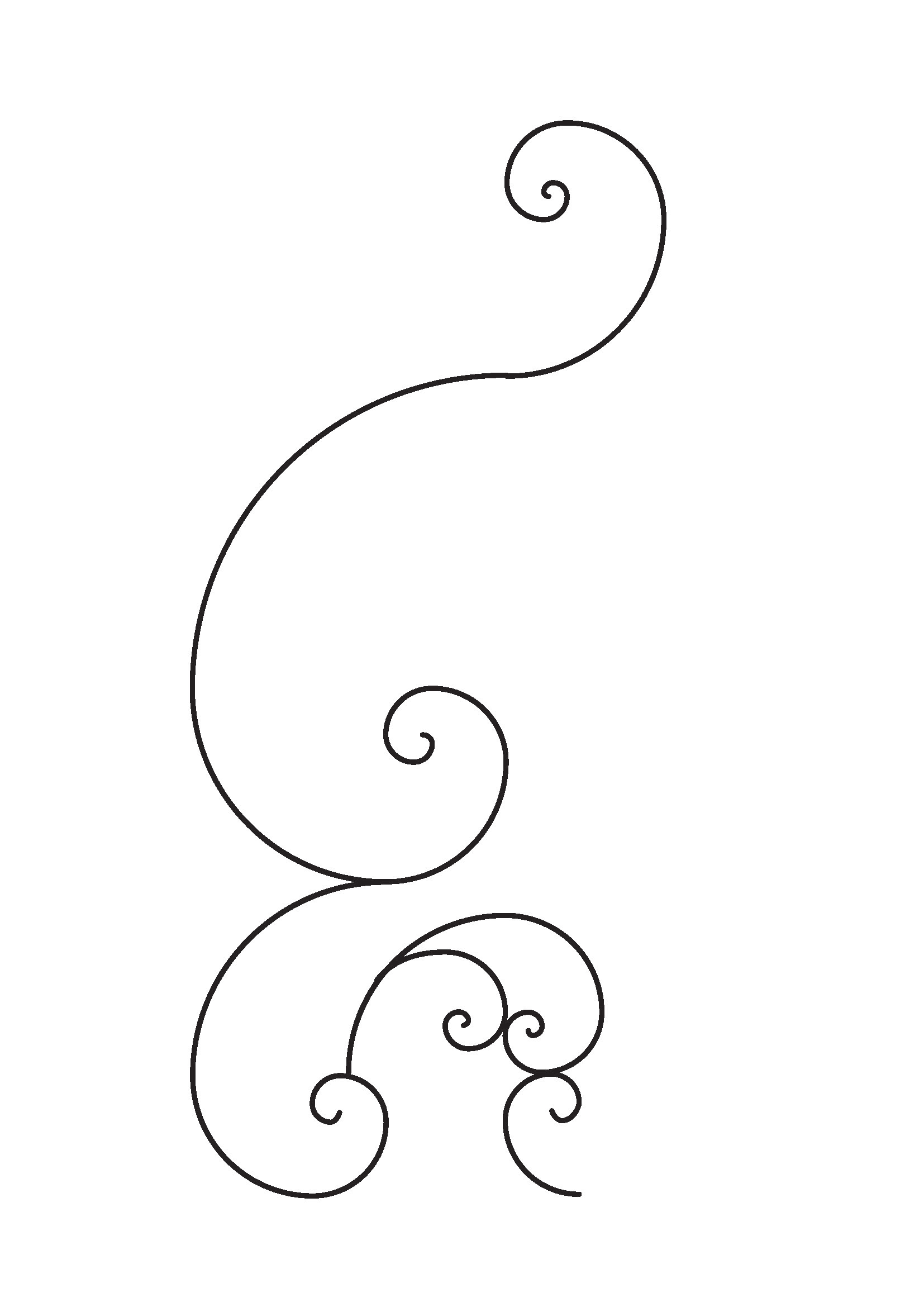
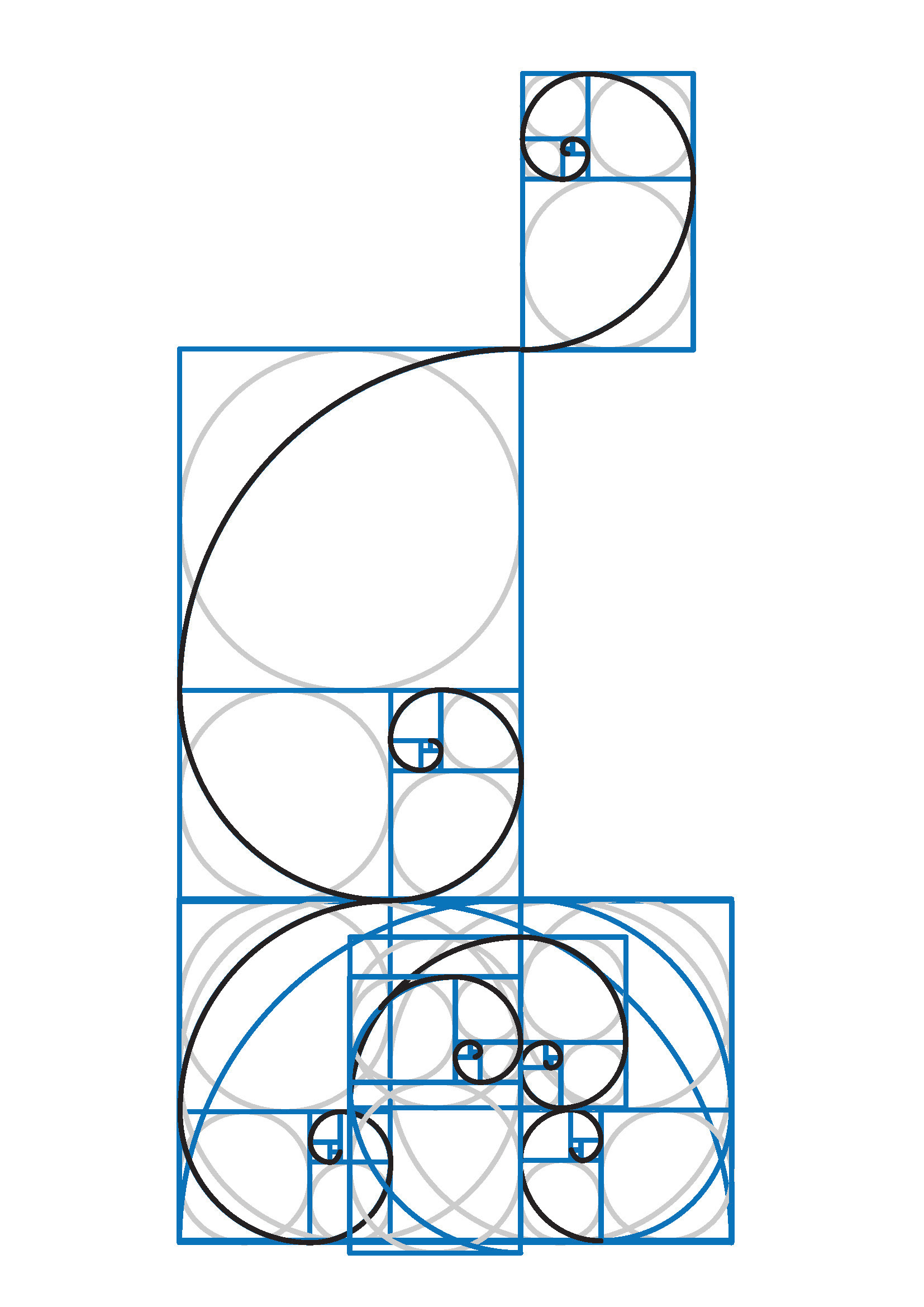
I like the bottom left design the most due to its balanced and simple composition. Also, I wanted to keep the connections between the scrolls simple not to distract from the overall composition or decorative details. This design will only need riveting together with simple stacked curves.
CAD modellin
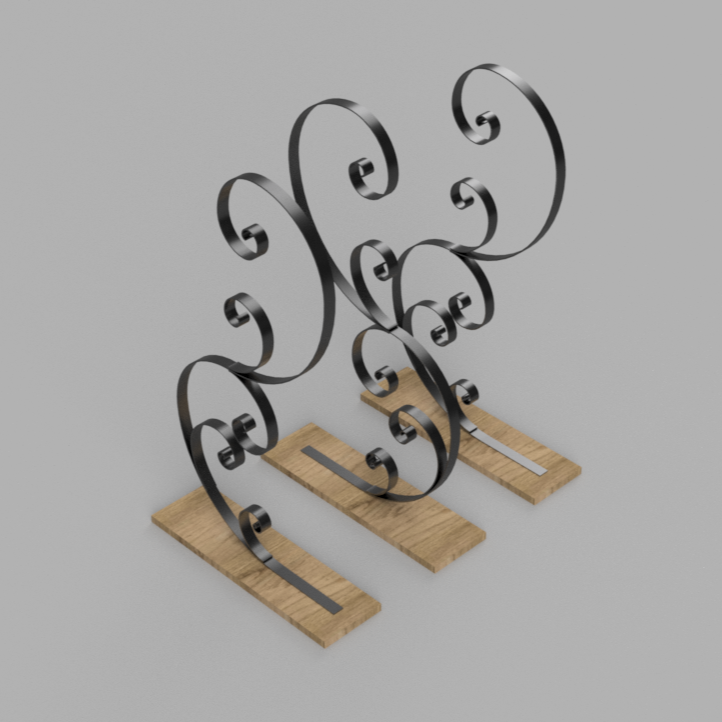
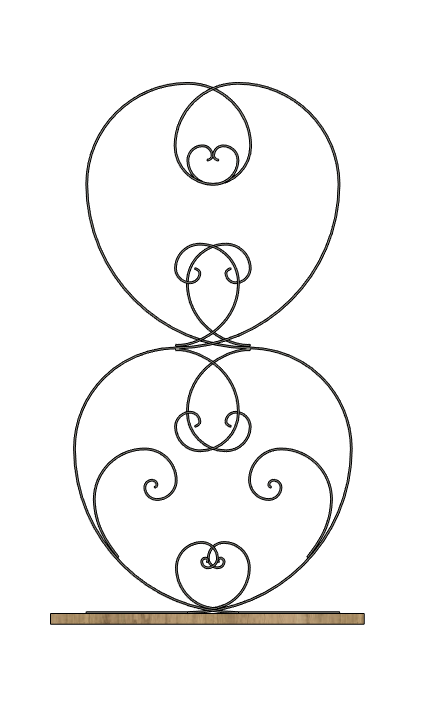
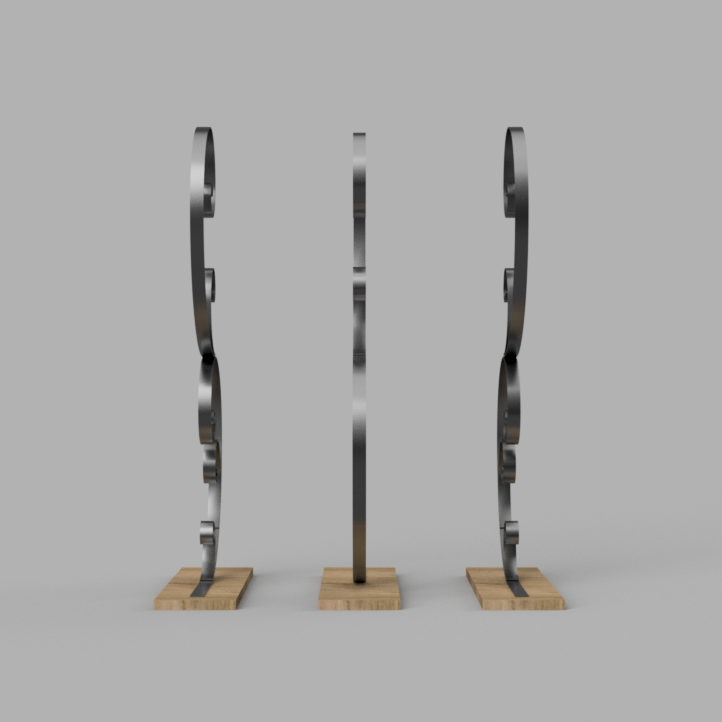
I took the design into Fusion 360 and refined the design. I extruded it to use the 3x25mm steel flat bar and explored duplicating the design. I discovered that I wanted to bring back the interaction between repeating forms and encourage the viewer to explore this through moving around the piece.
Testing forging the scrolls by hand
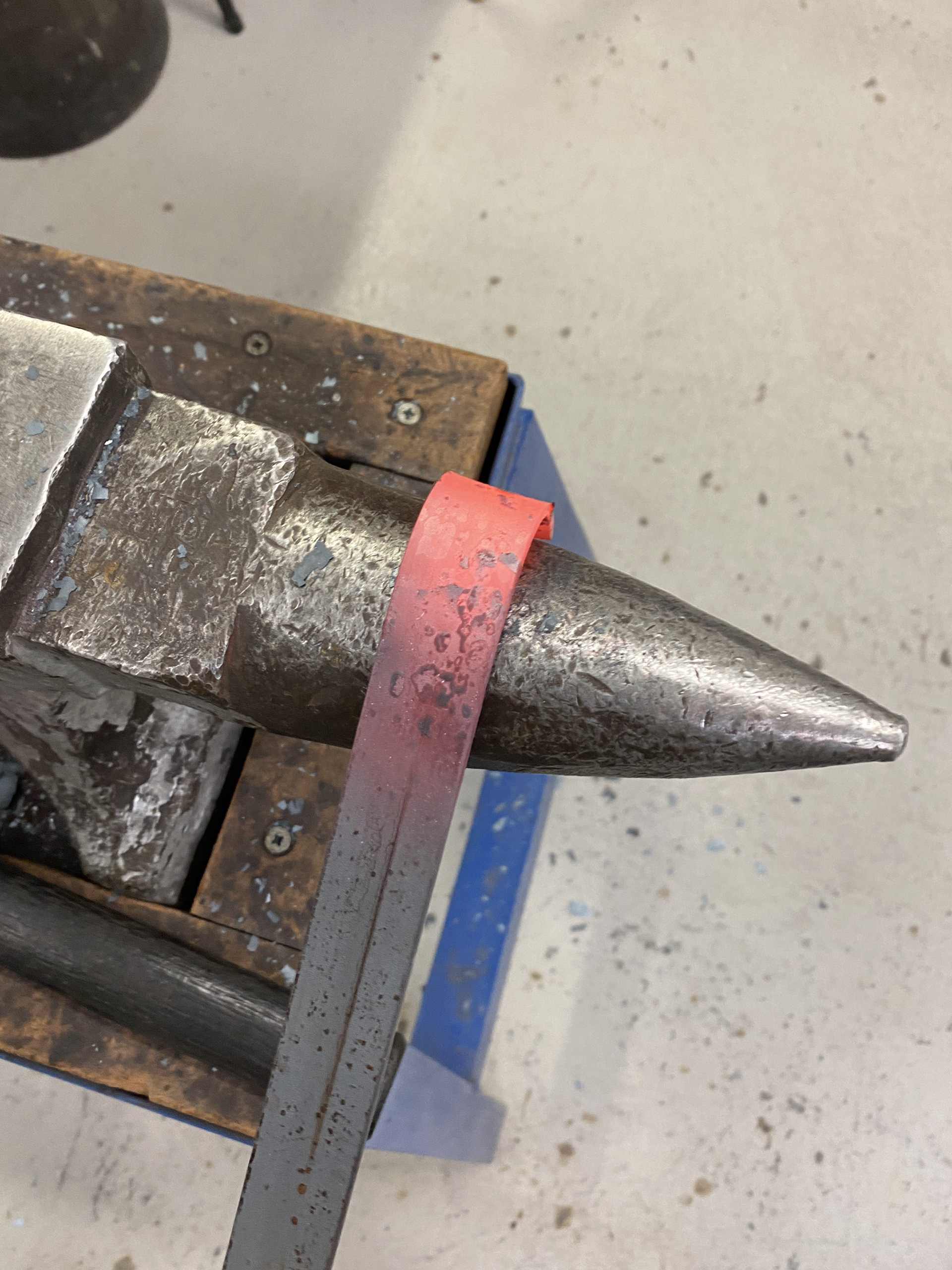
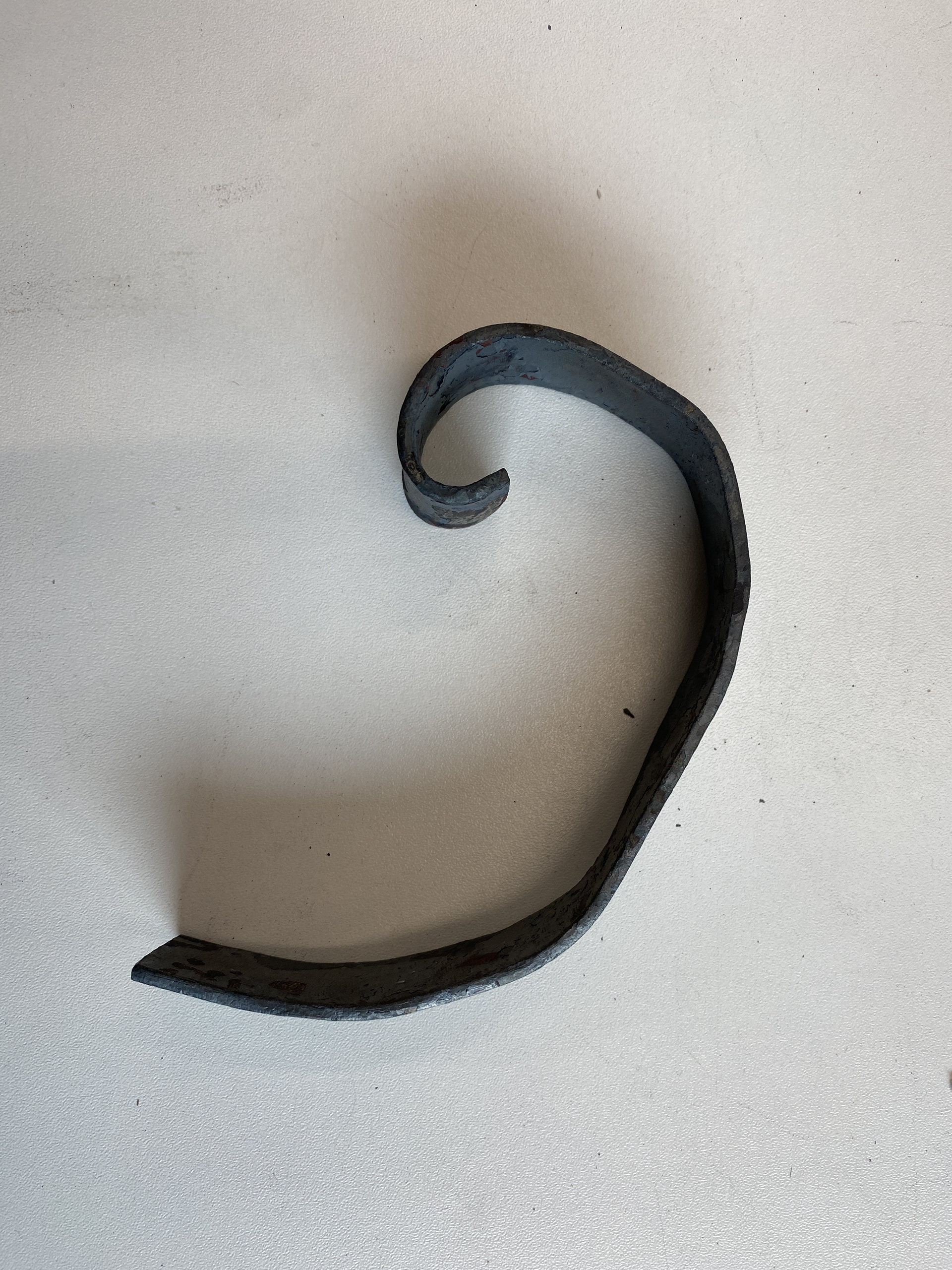
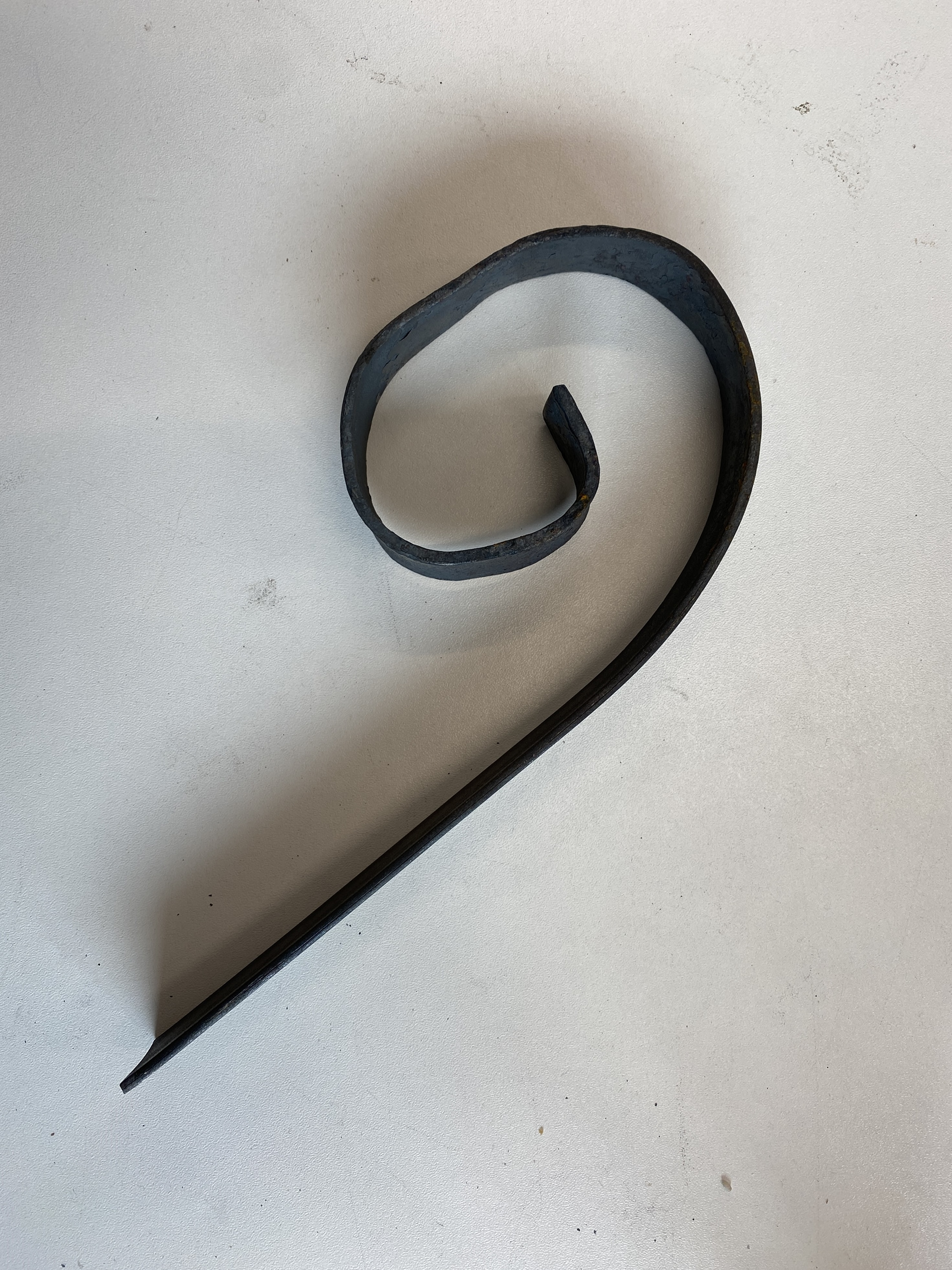
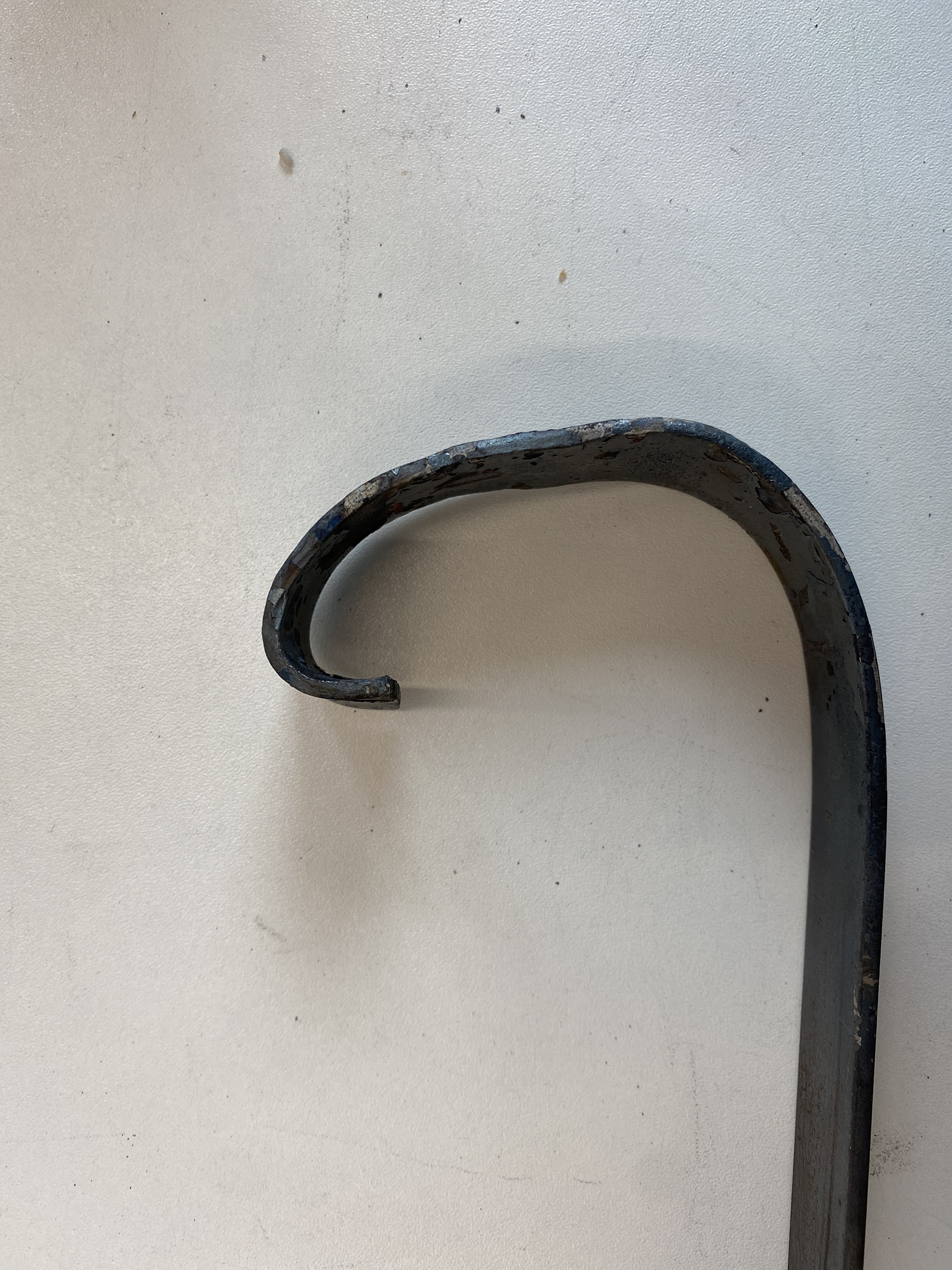
Initially I started to try and shape the flat bar into the separate scroll shapes using my previous technique of forming it over the horn of the anvil. However, due to the shape of the Golden Ratio scrolls not being a traditional spiral I found it almost impossible to create an accurate replica of the design.
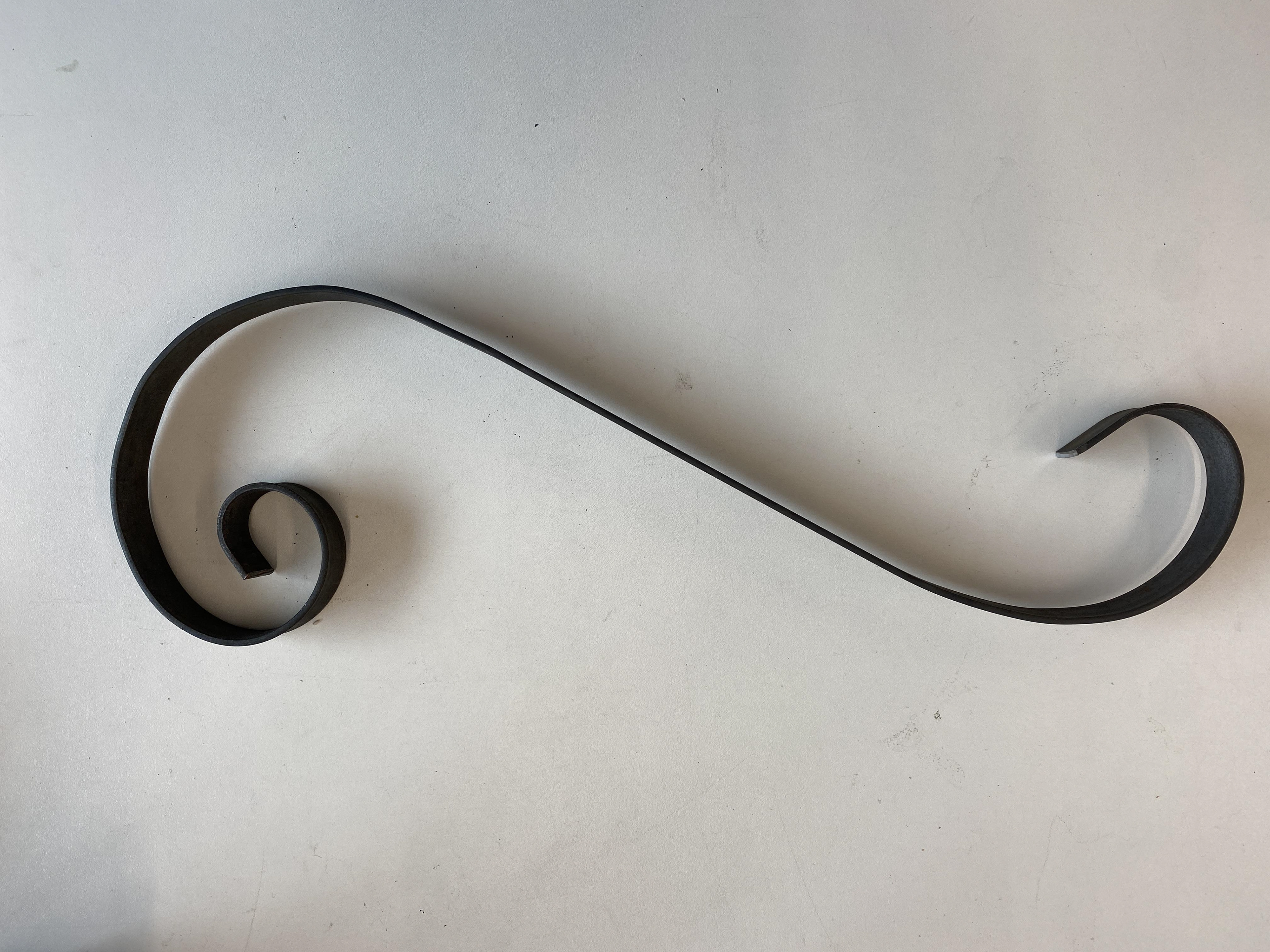
I then attempted cold bending the steel between a scrolling fork. This process allowed me to put exact pressure in the desired location to form the curve evenly and slowly. However, due to the low malleability of the steel I couldn't get the tight curves at the start of the scroll. Therefore, this process will only work for larger radius curves such as most of the main curve.
Developing jigs
To bend the tight curves consistently and repeatedly I designed a series of jigs in Fusion 360.
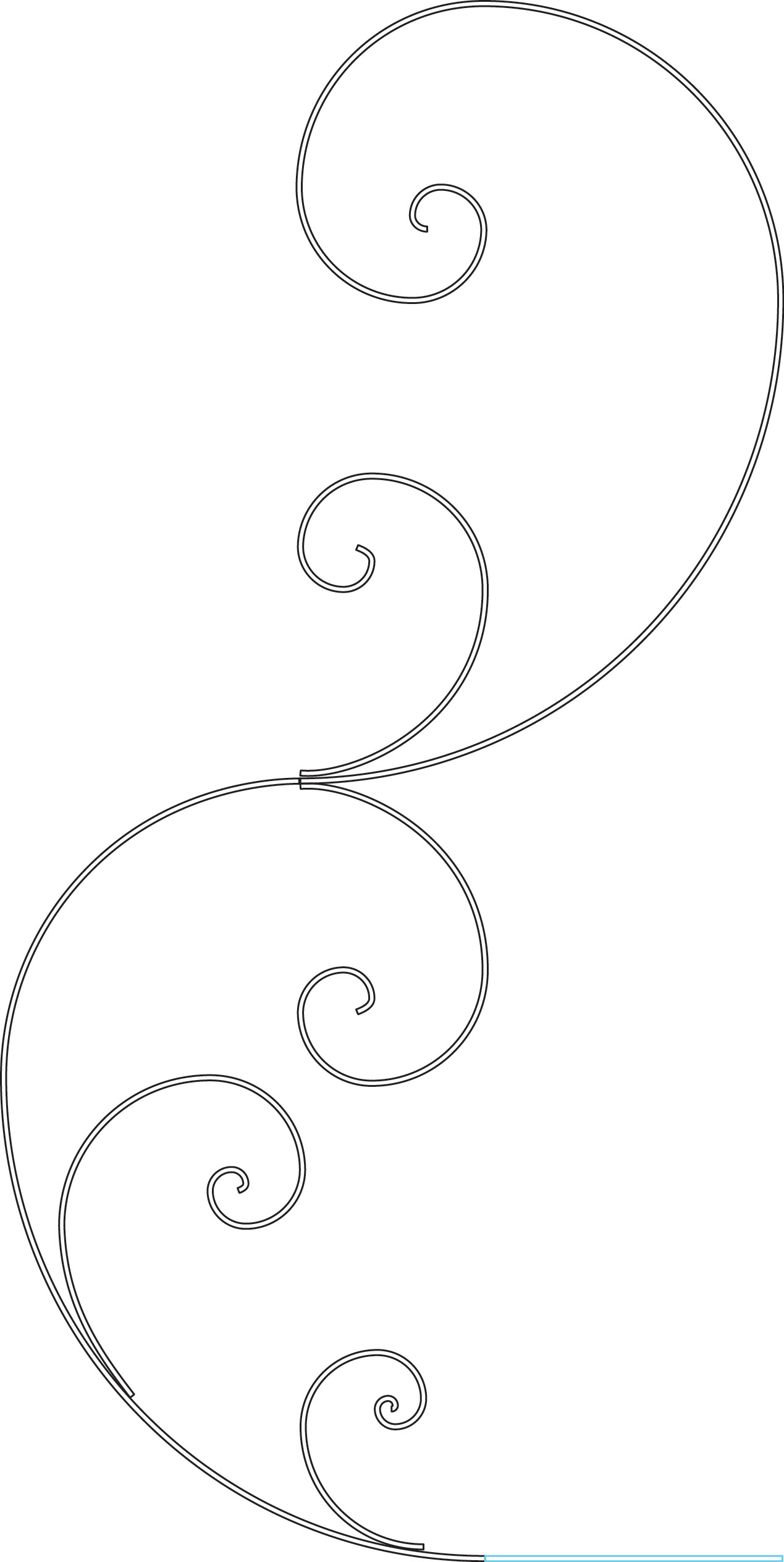
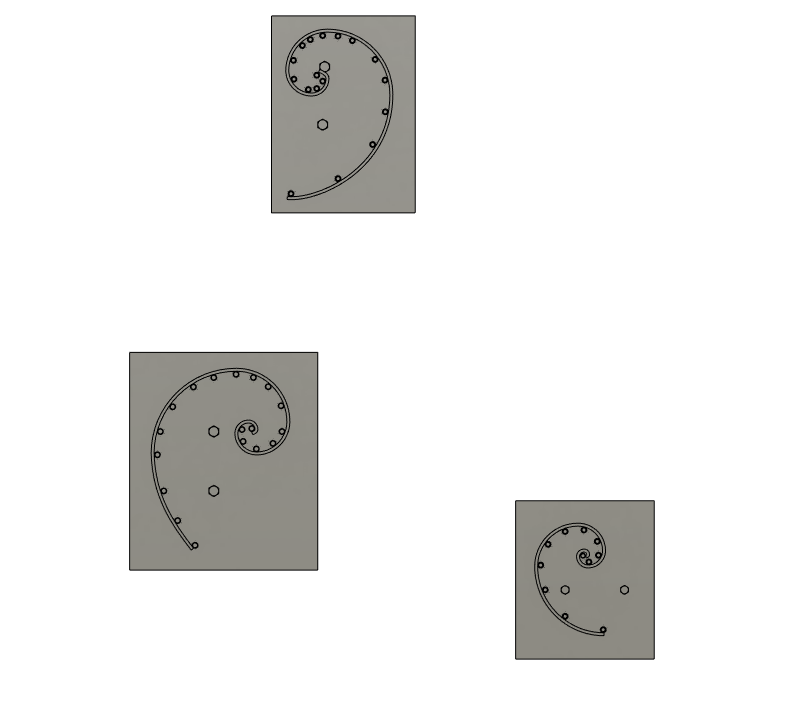
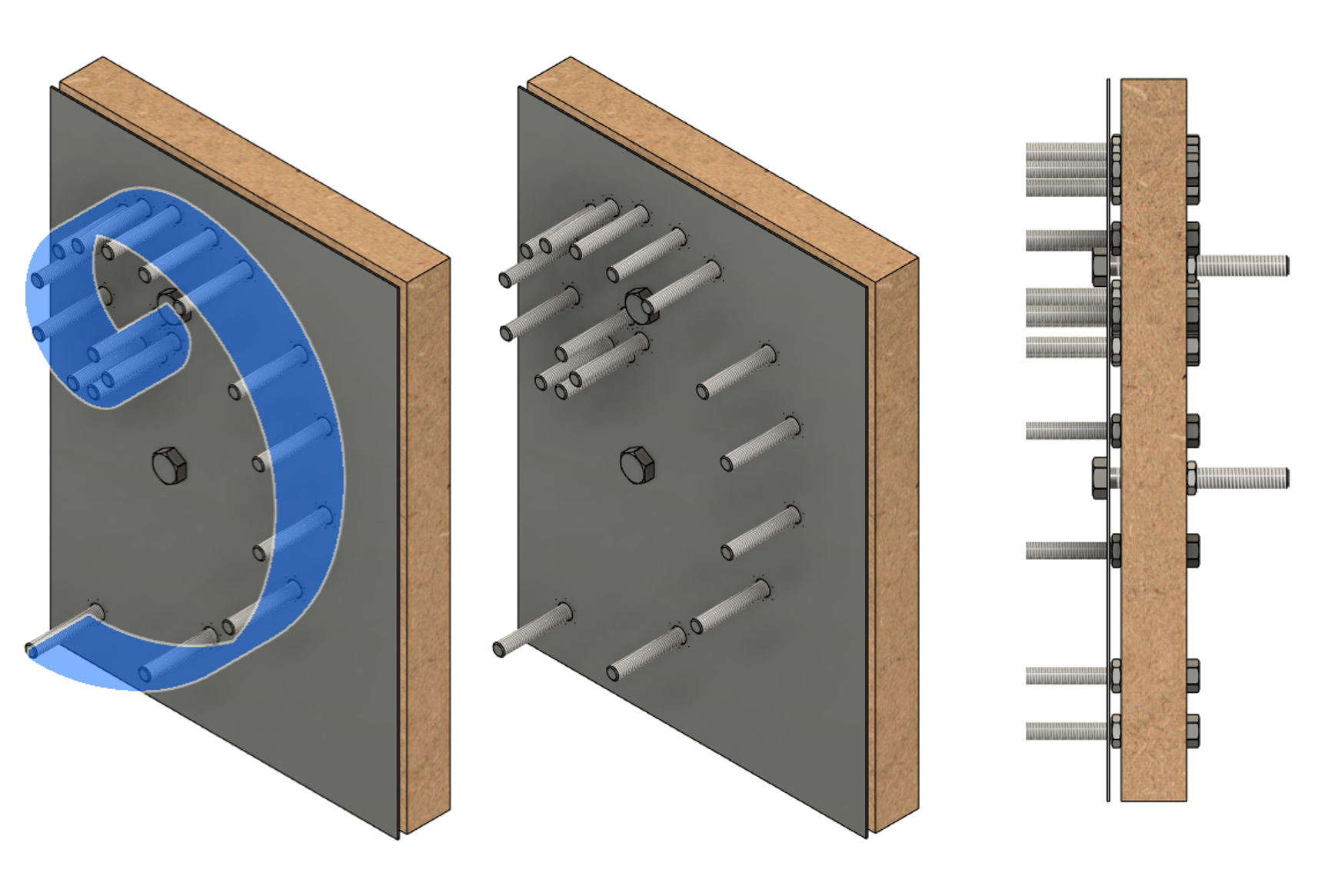
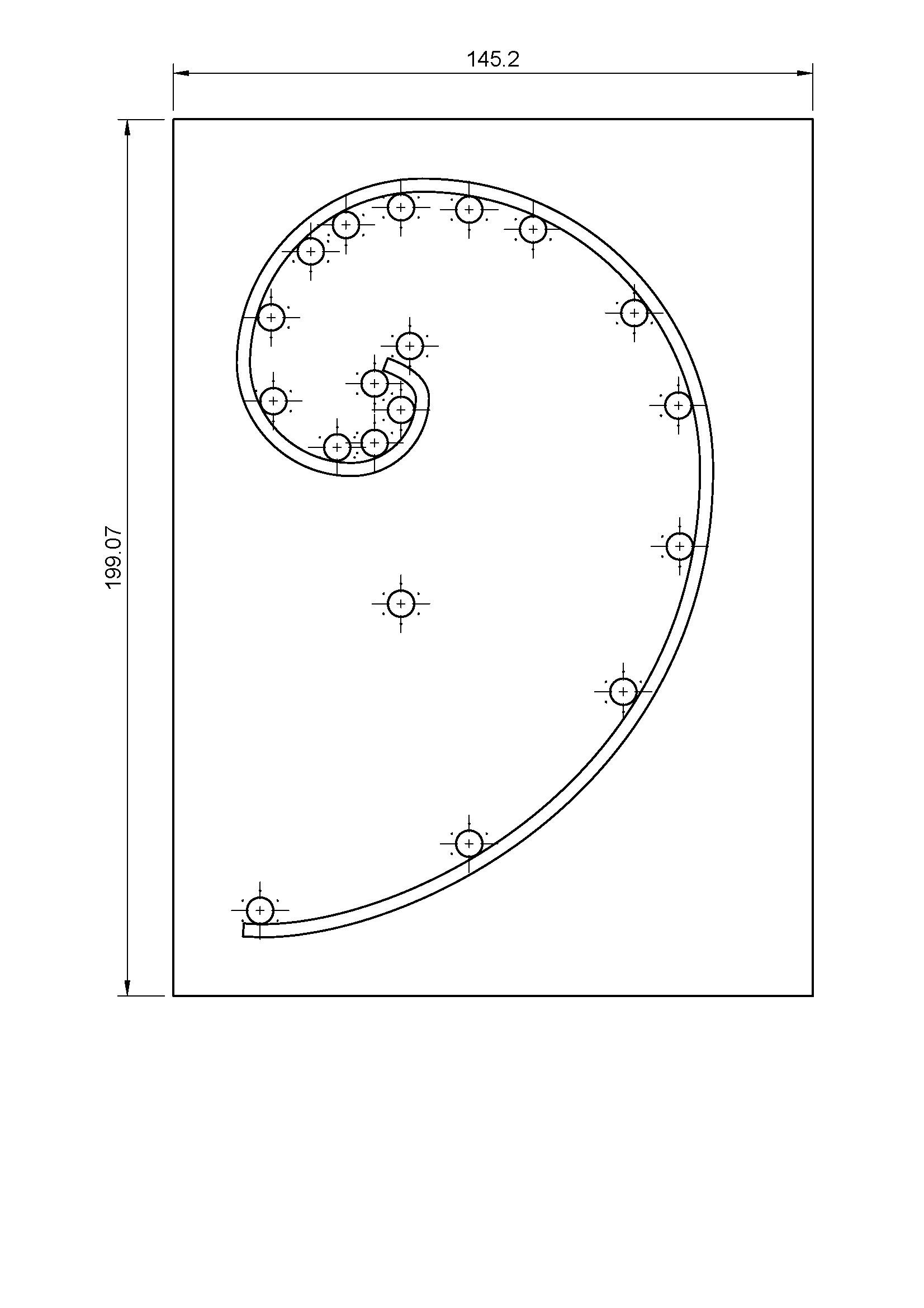
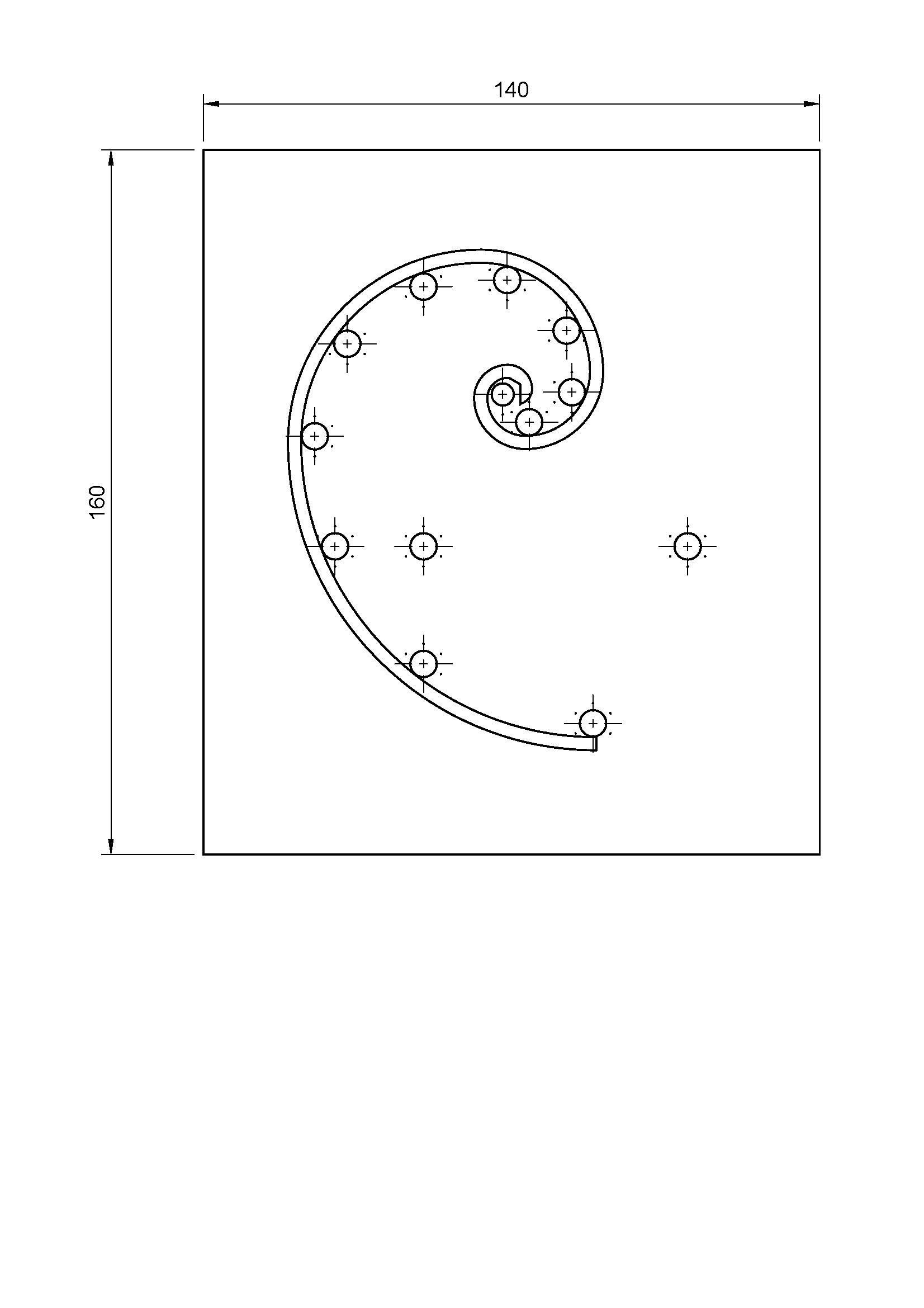
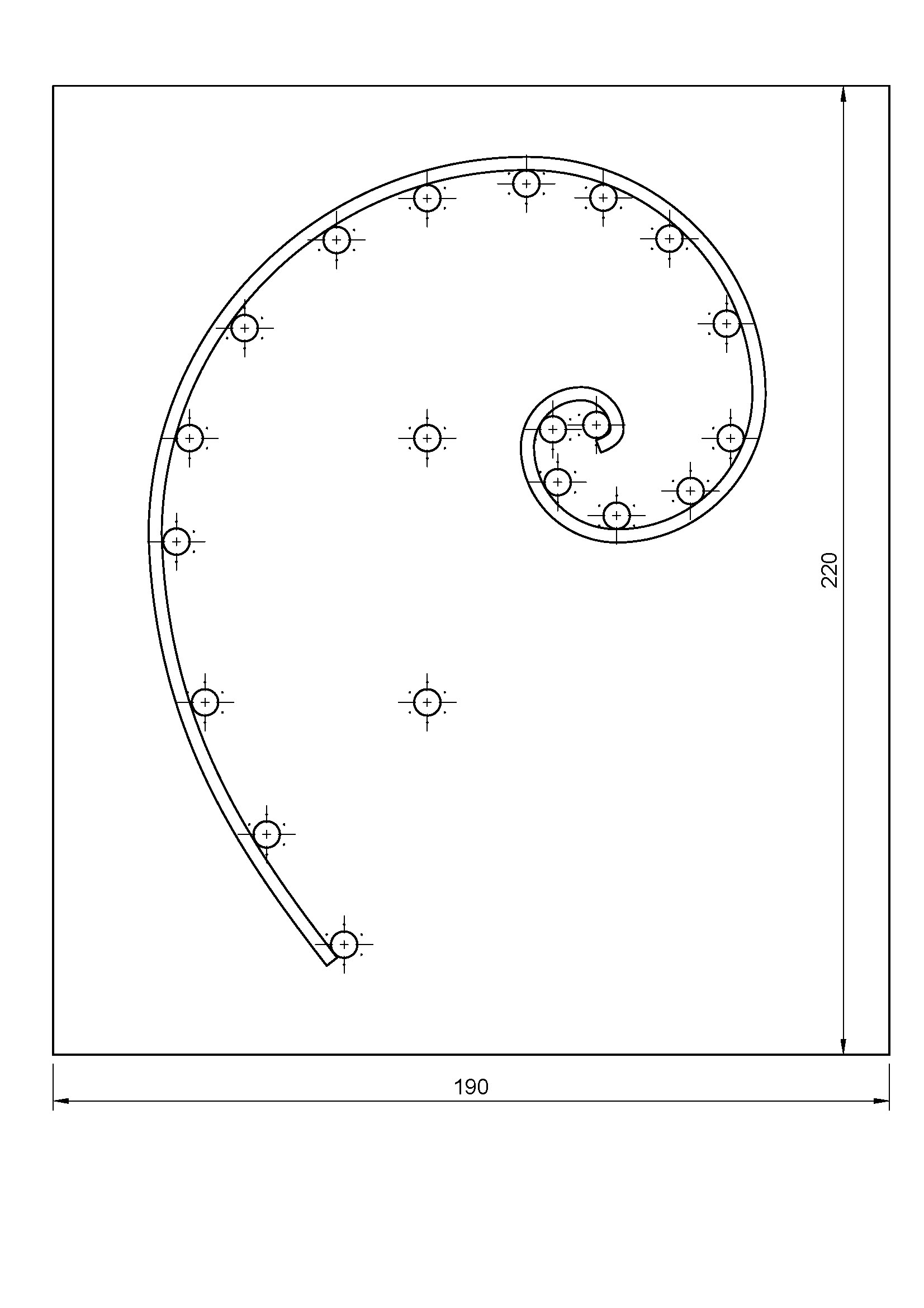
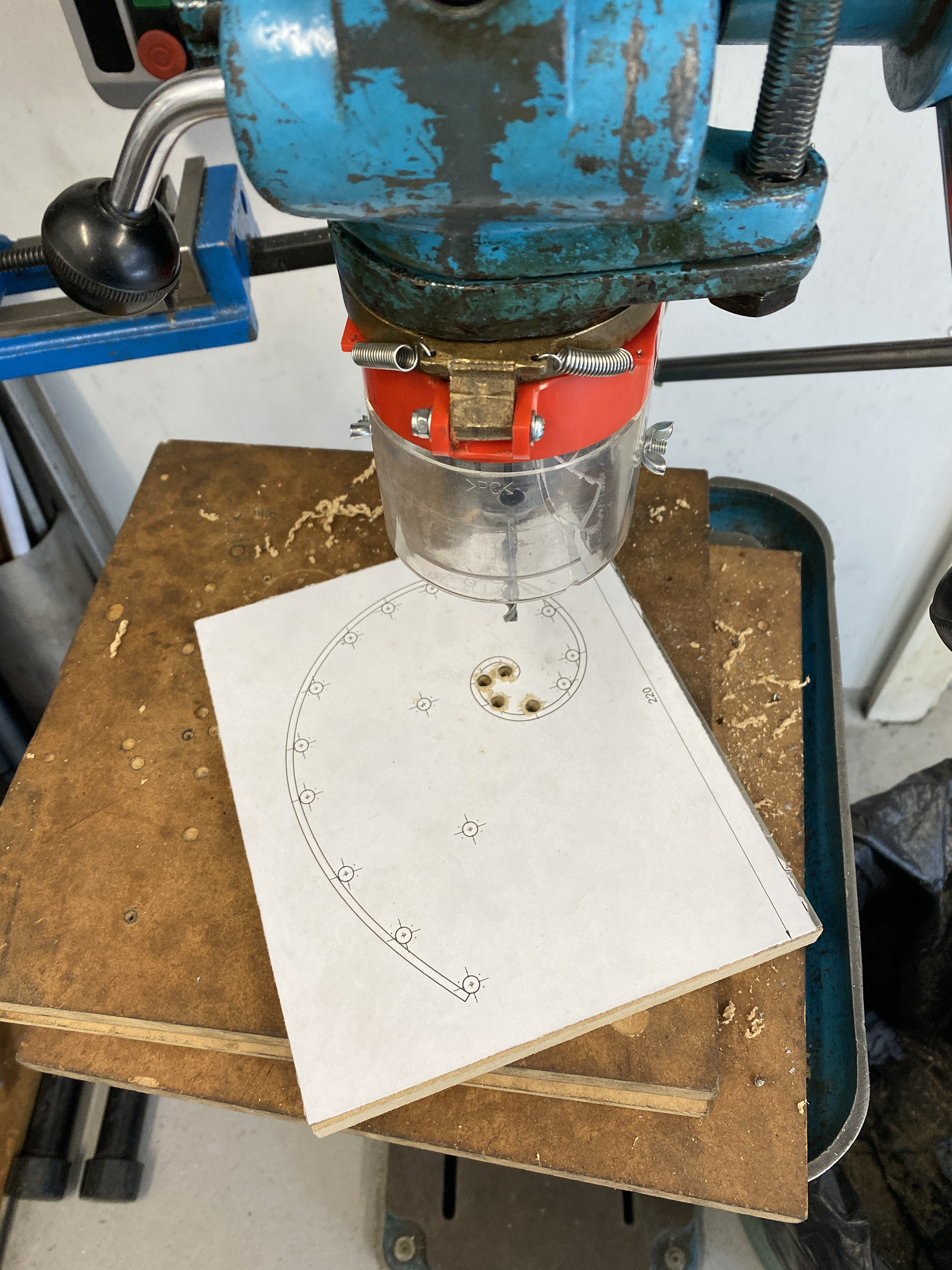
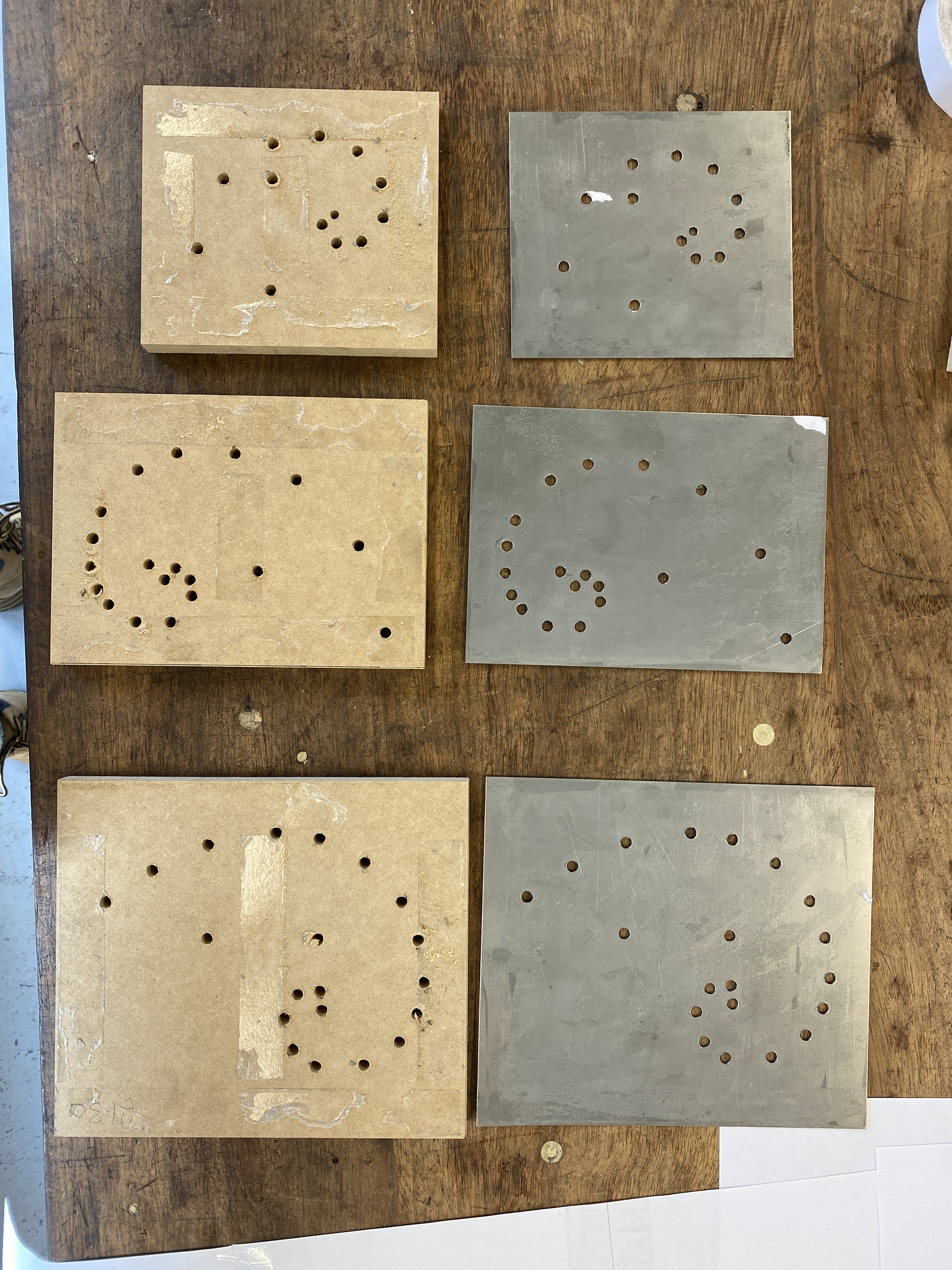
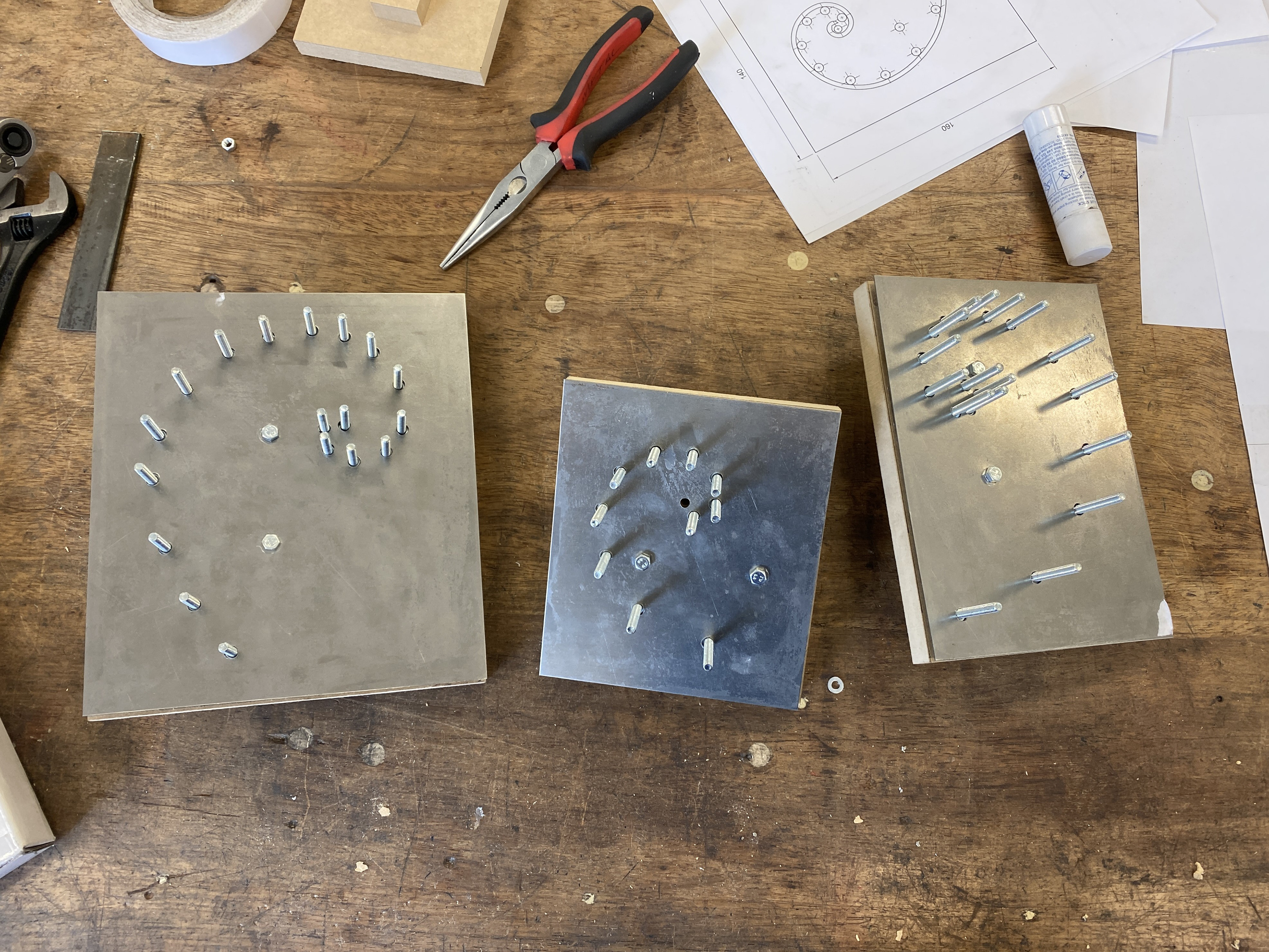
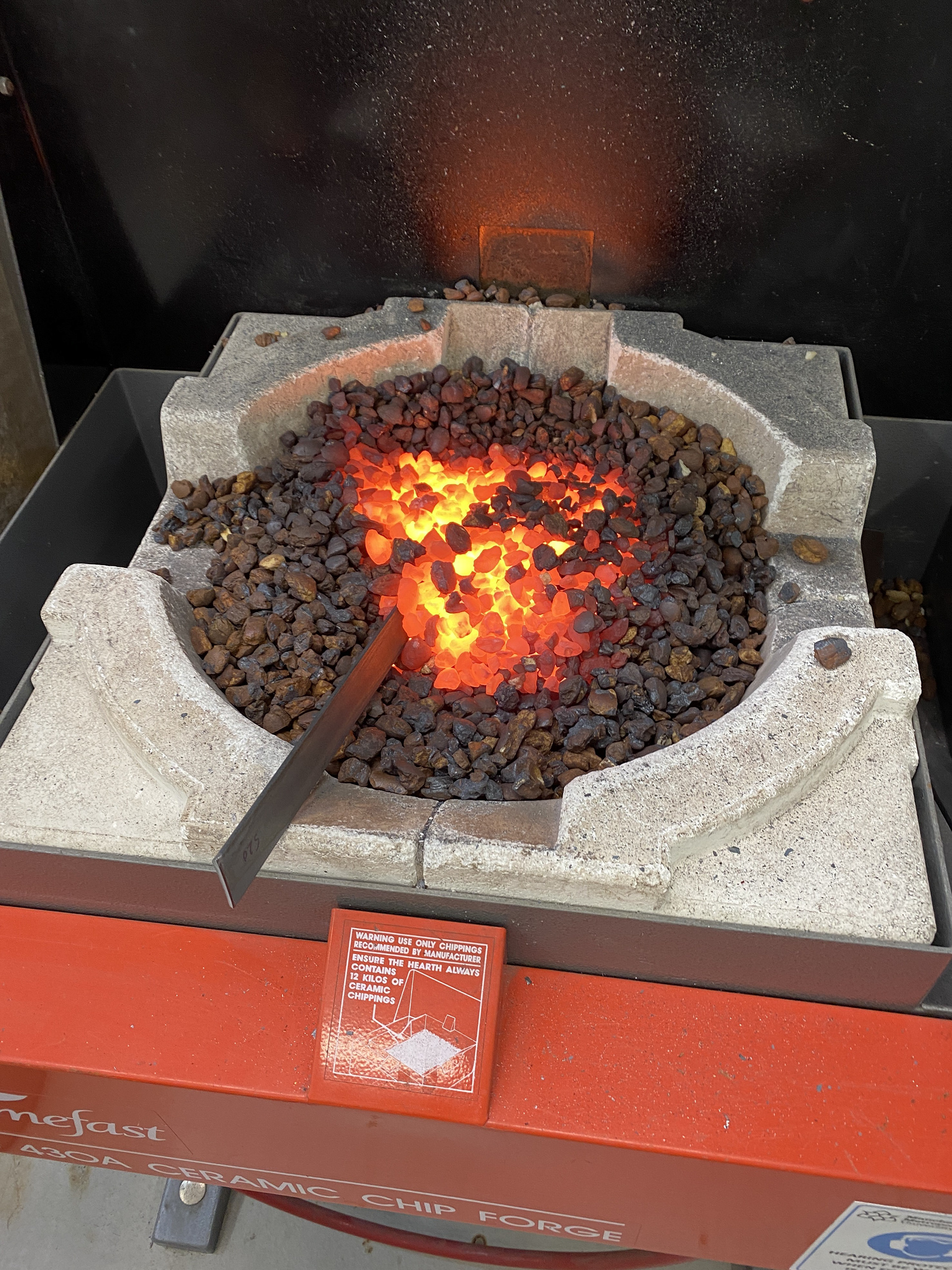
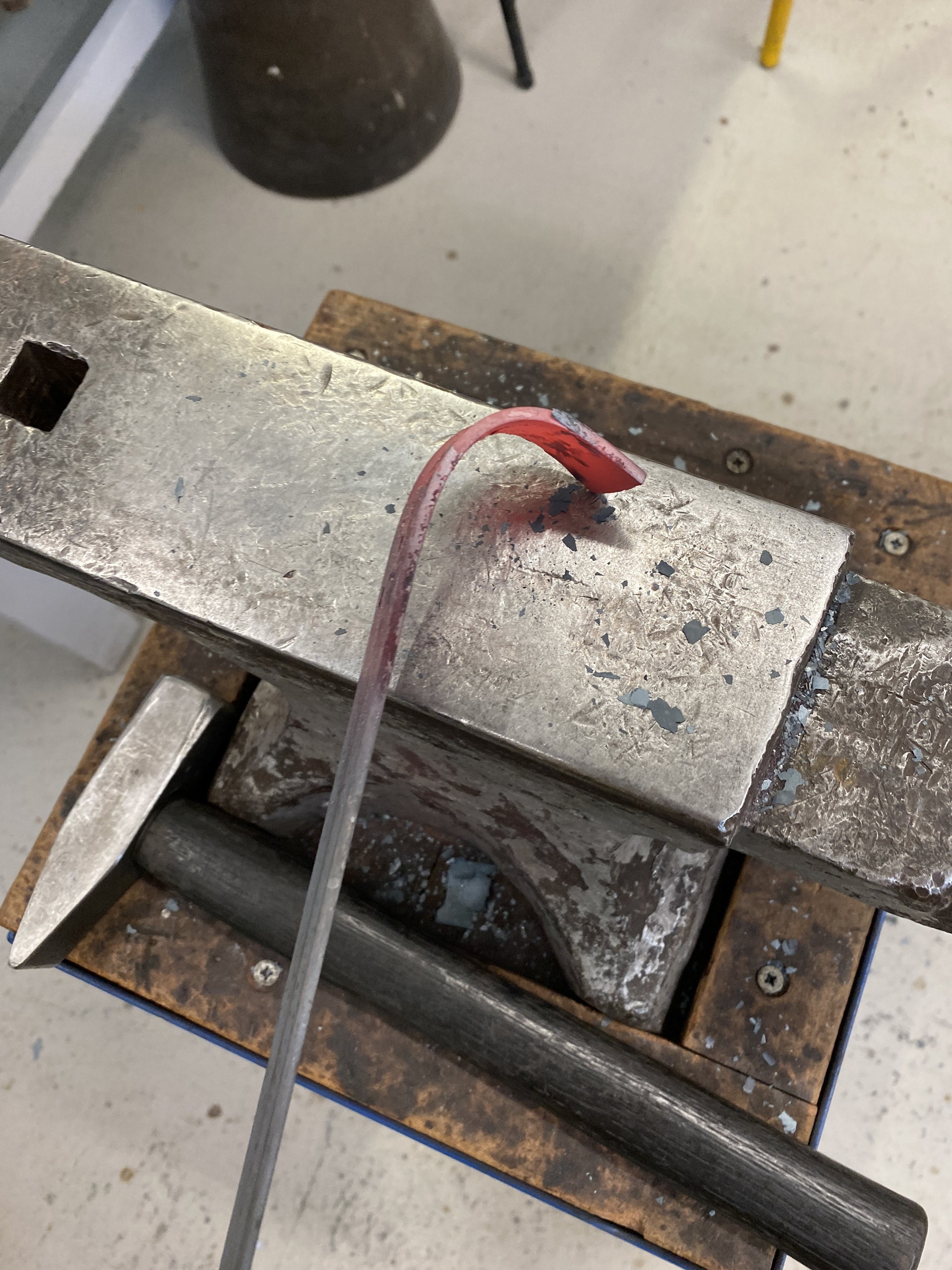
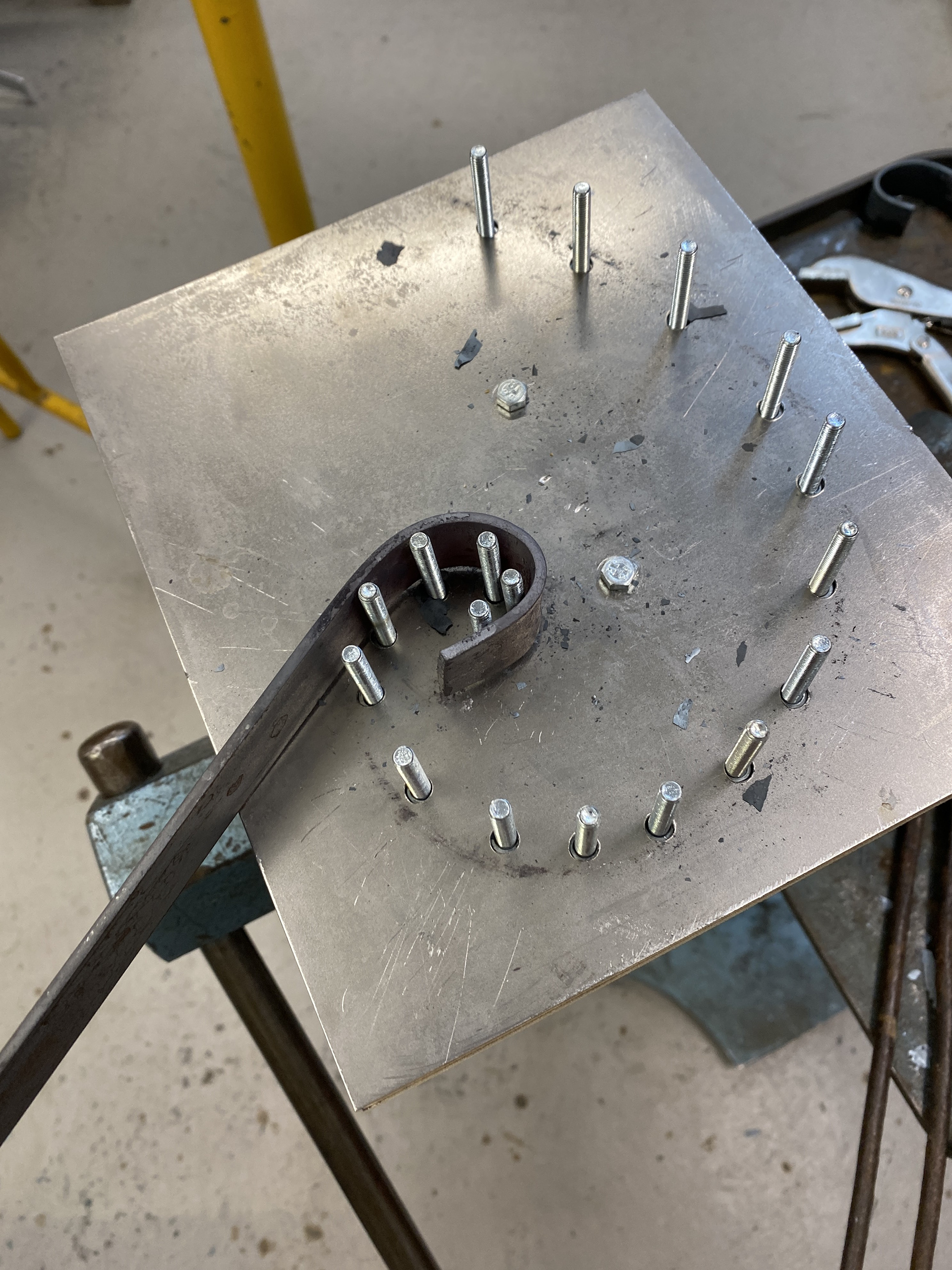

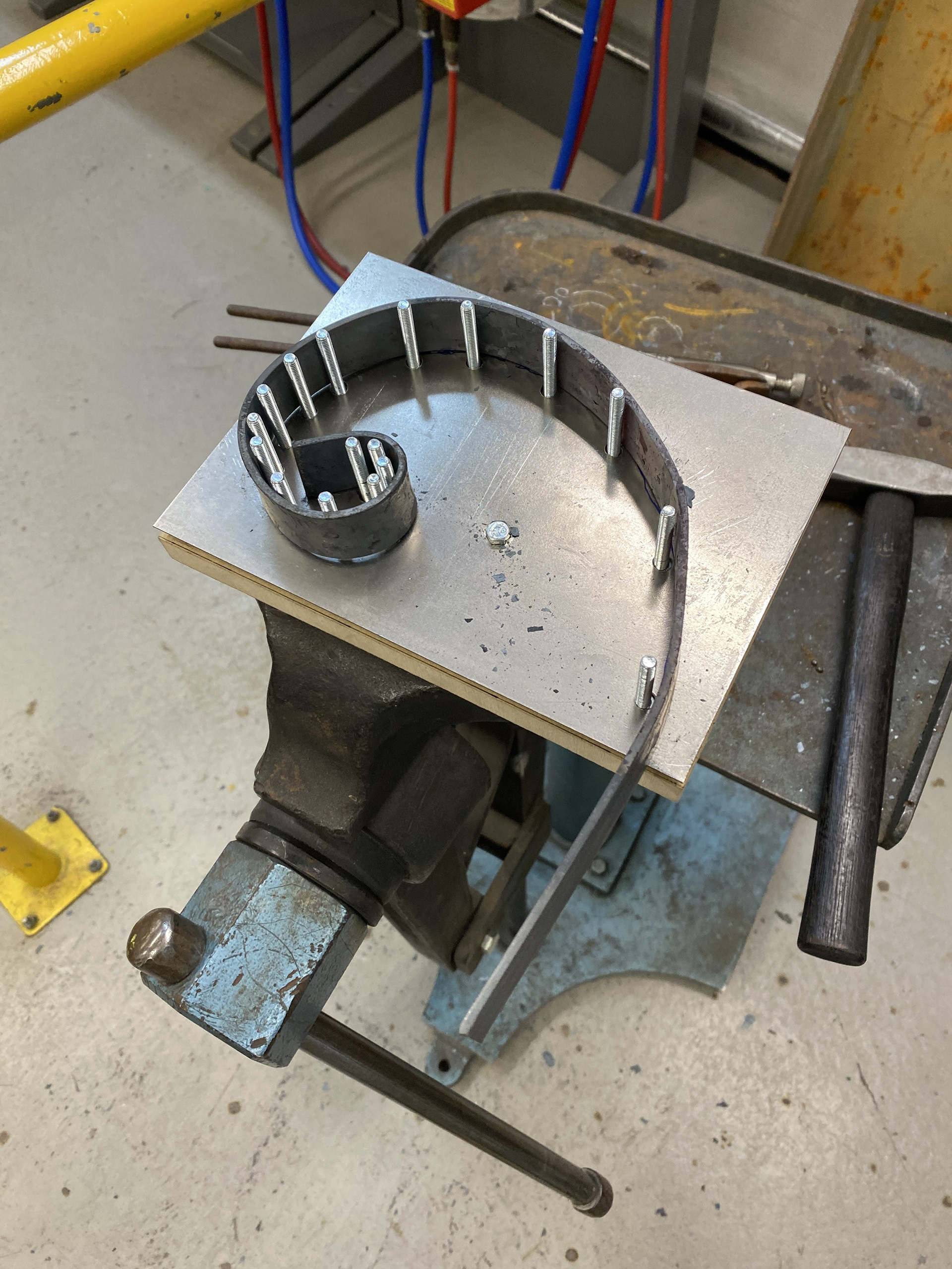
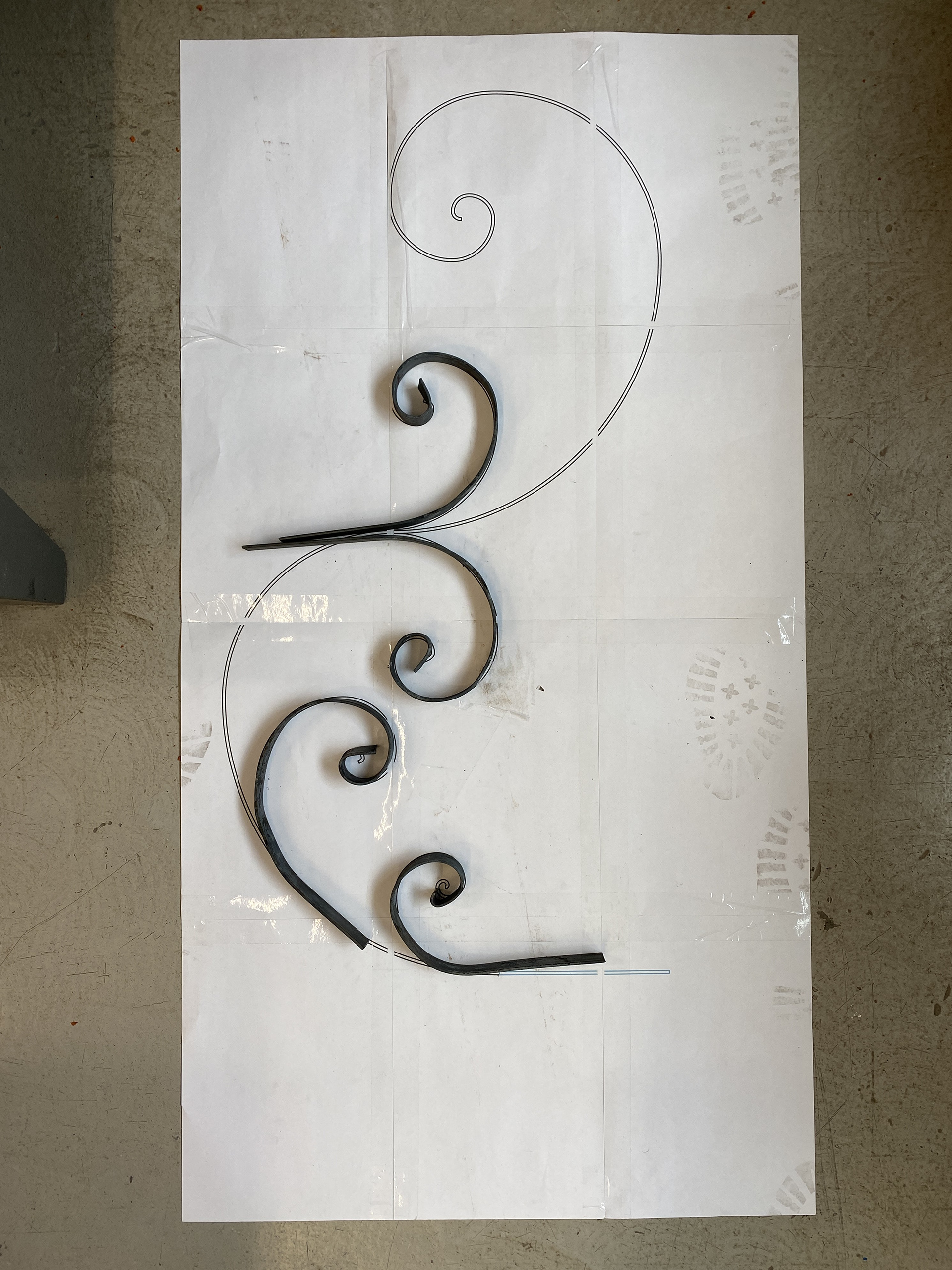
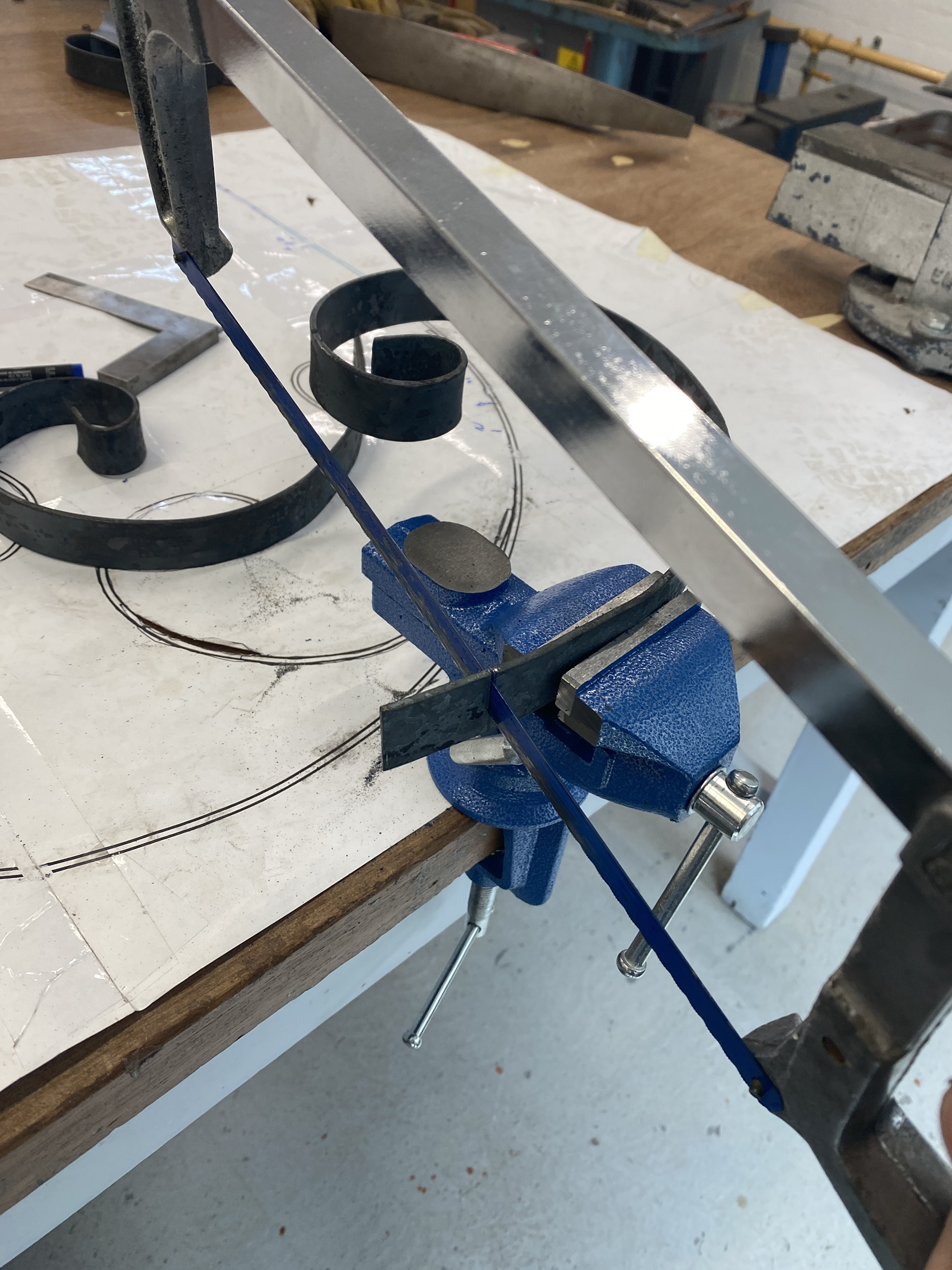
From my CAD drawing I created a design drawing which I used as templates to mark the exact location of the holes to be drilled. I then threaded bolts through the steel, which provided a flat and inflammable base, and 18mm MDF which ensured the bolts would stay vertical when hammered on.
I forged the start of the curve over the face of the anvil so that I could lock this into the jig. I then bent the flat bar around the jig using the forging tongs, ensuring to keep a constant red heat on the section I was bending so that sharp bends didn’t appear. I added 10cm extra to the length of the scrolls to help with the leverage of bending and cut the excess off after making so that all three sets were uniform.
Cold bending the main scroll
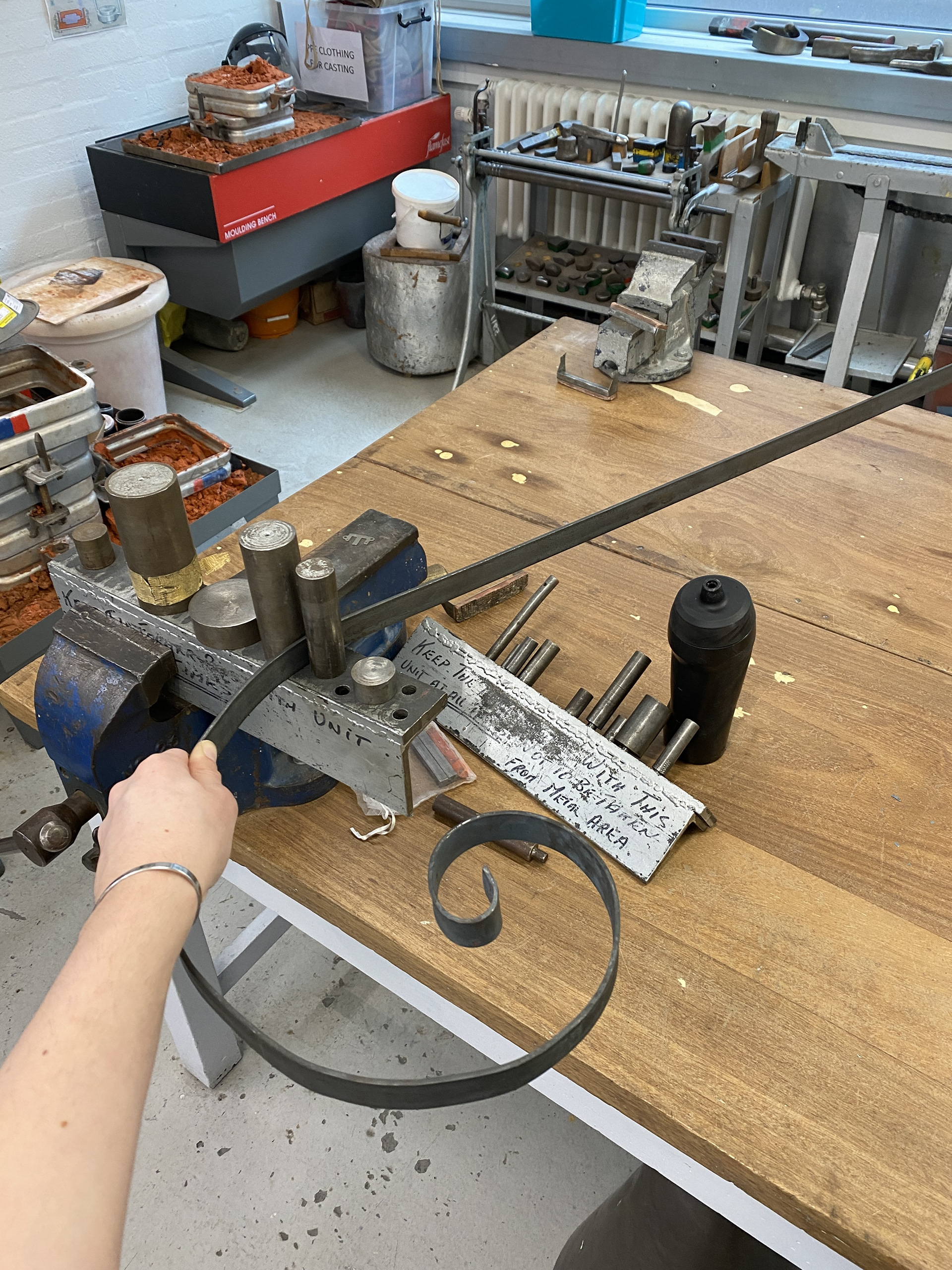
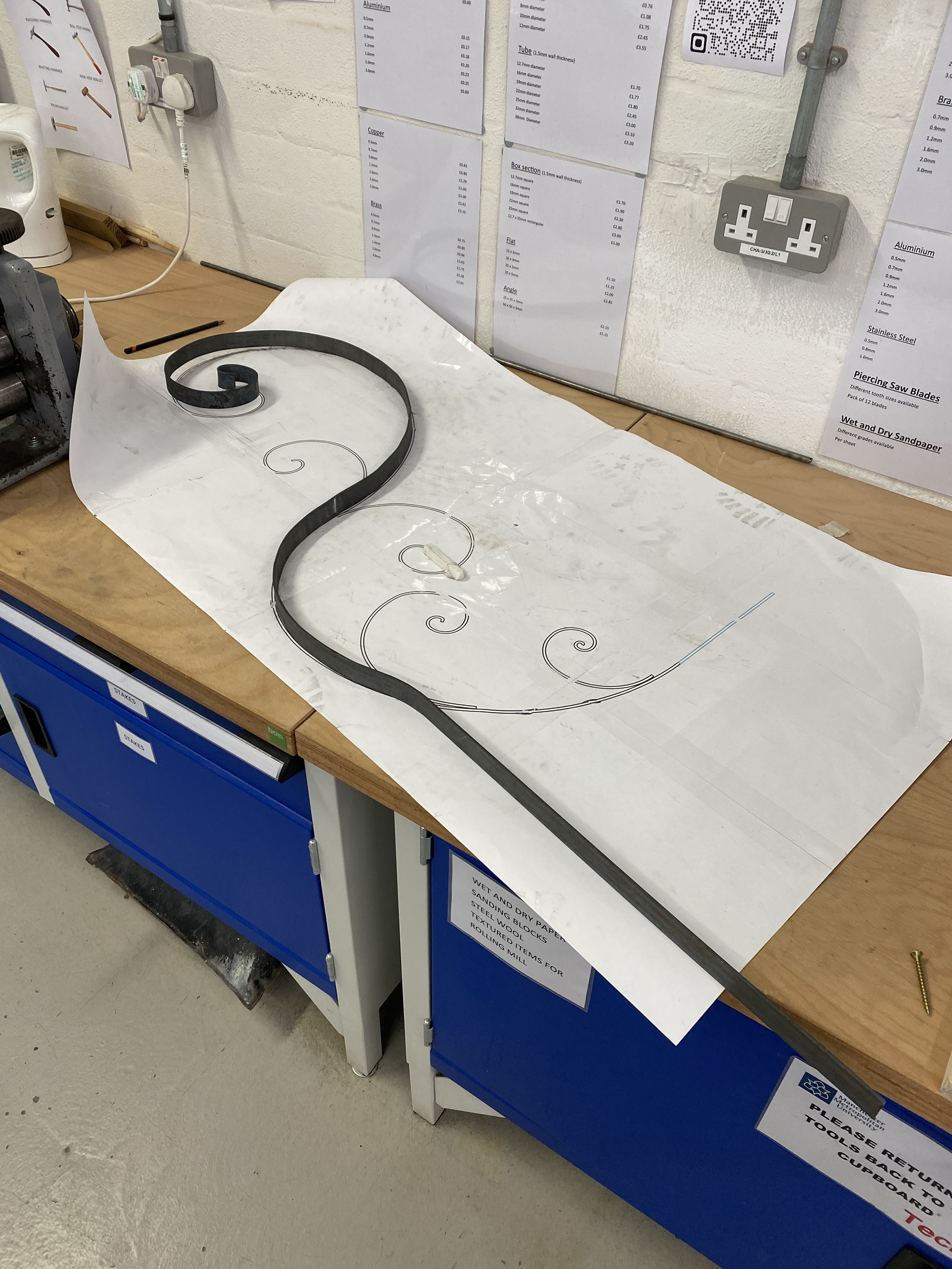
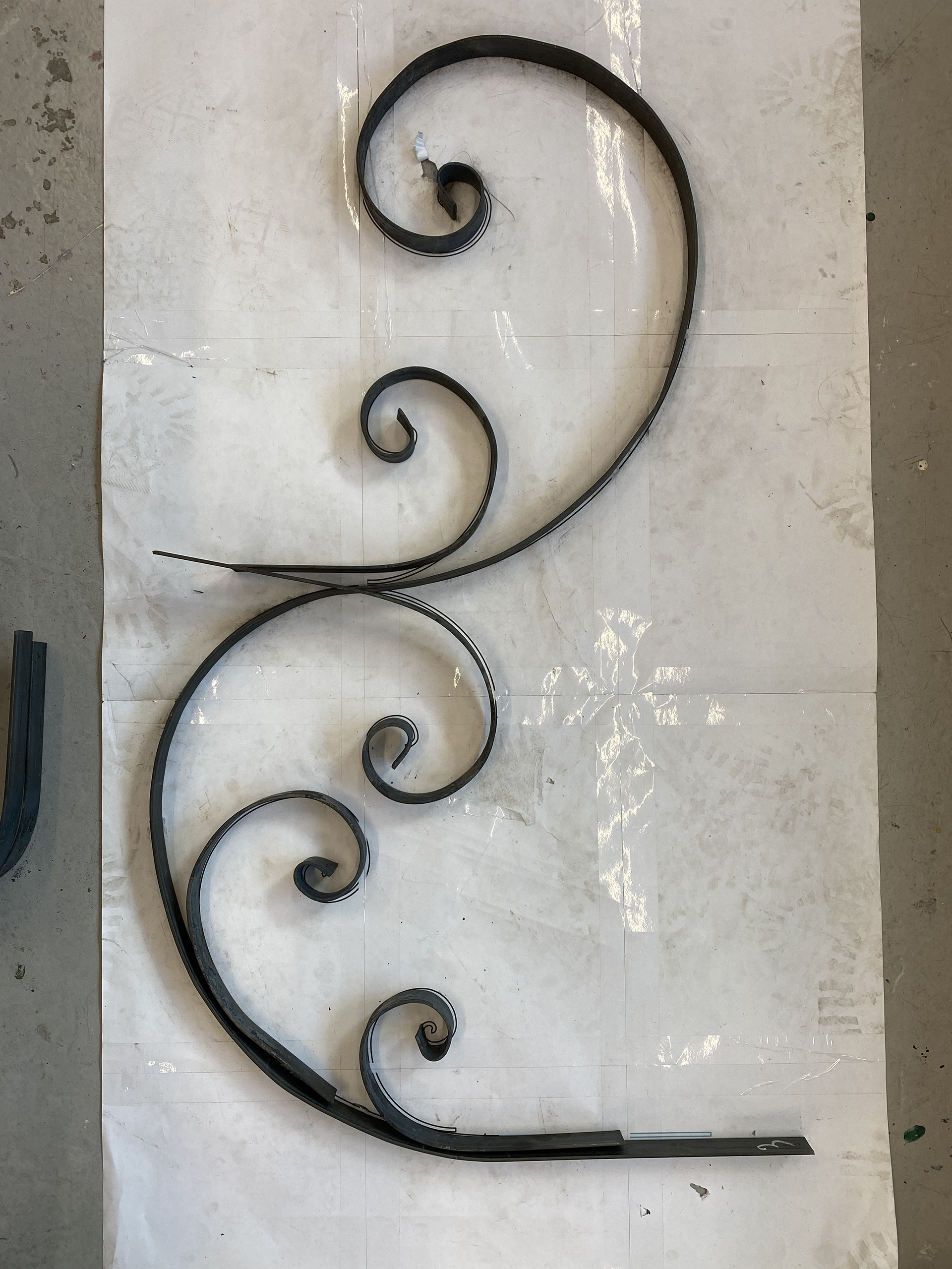
Once I had forged the small radius of the main curve I used a metal bending jig to cold bend it to the final shape.
Testing rivets
To connect both the scrolls and decorative components, I will use rivets to lock them together permanently and securely.
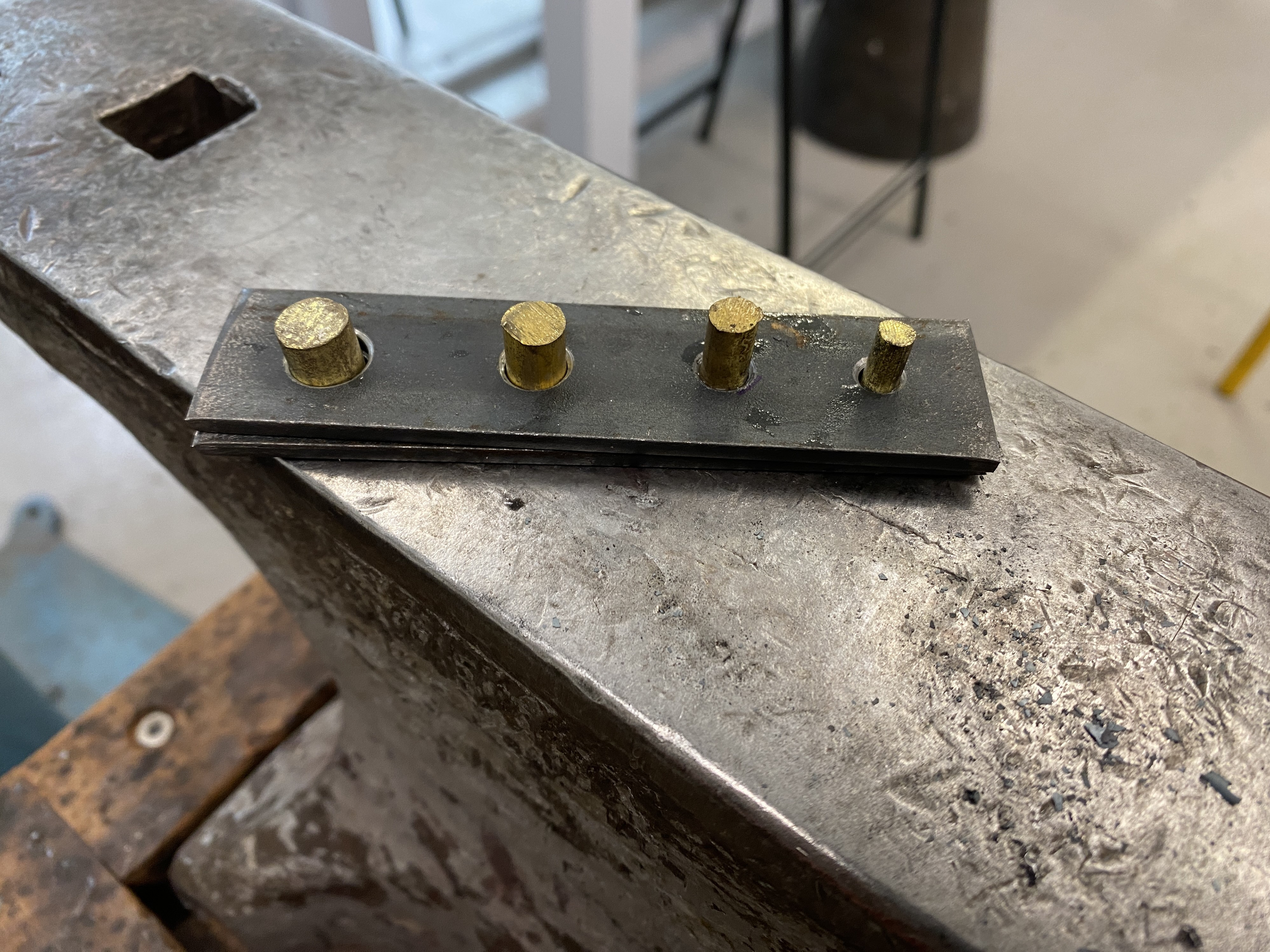
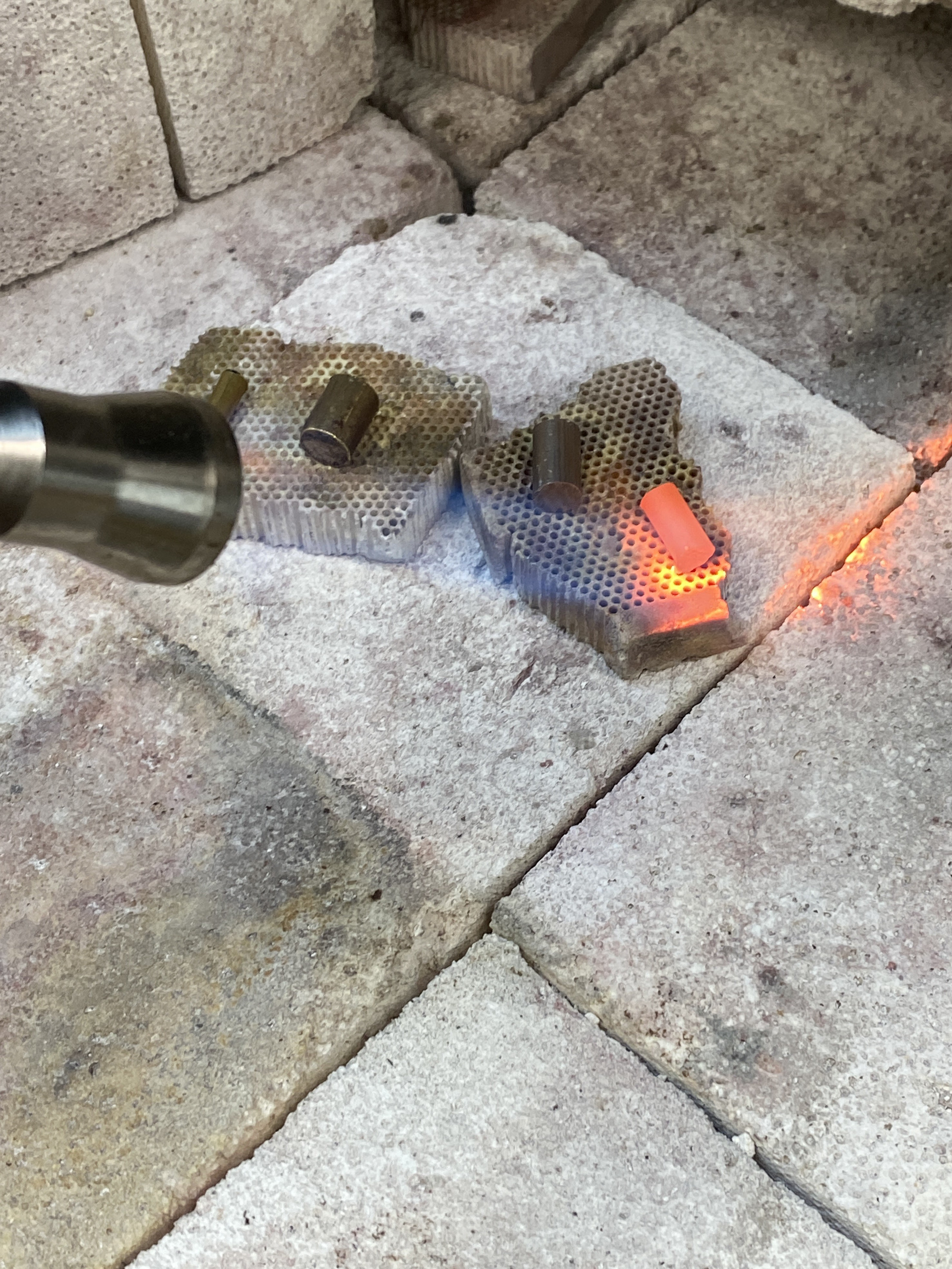

I tested brass for the rivets, which I annealed before hammering them cold on the anvil to mushroom over both sides. The brass I have available in the workshop is designed for machining and thus it is too brittle and led to the rivets cracking if hit on the edges incorrectly.
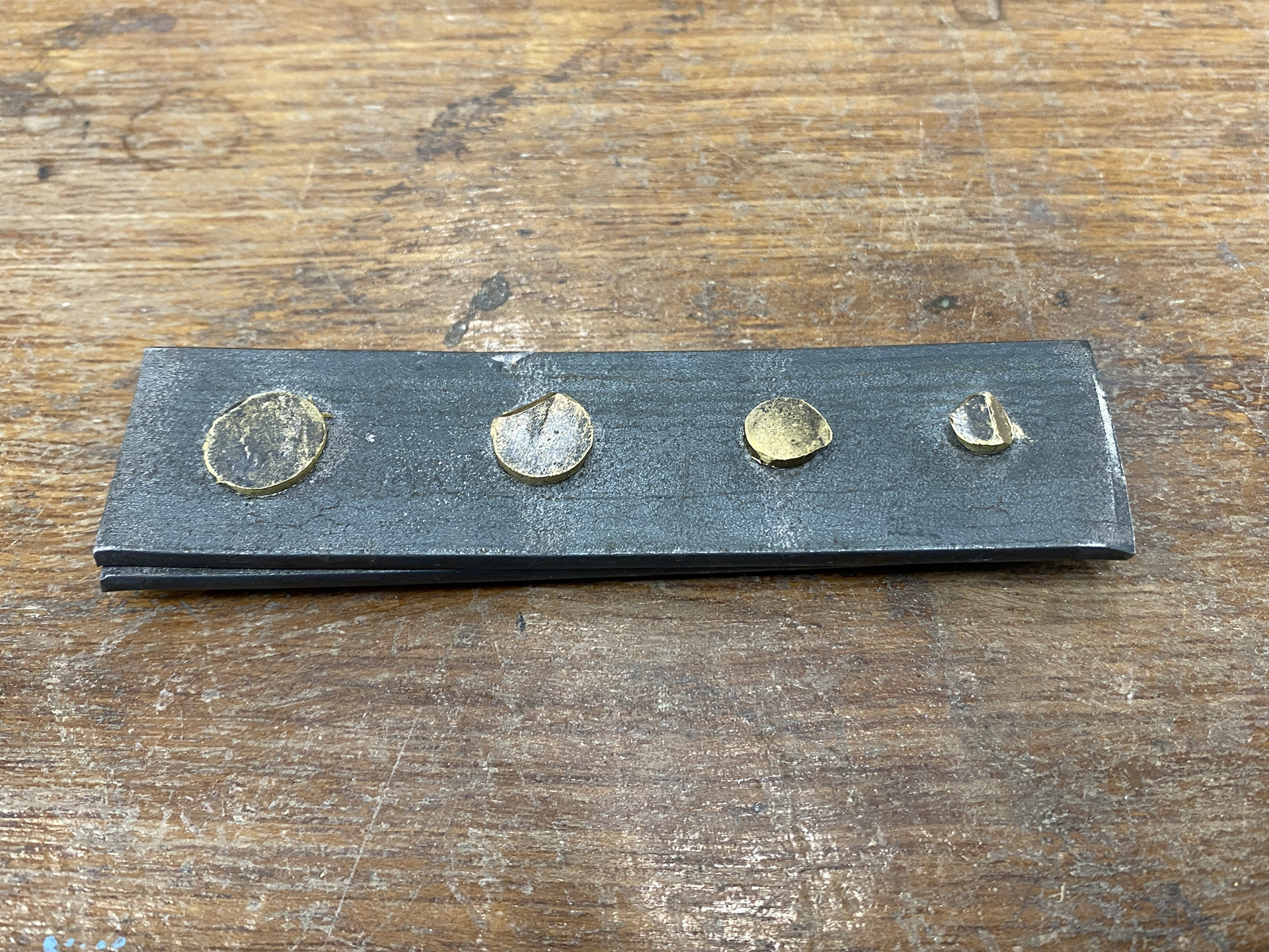
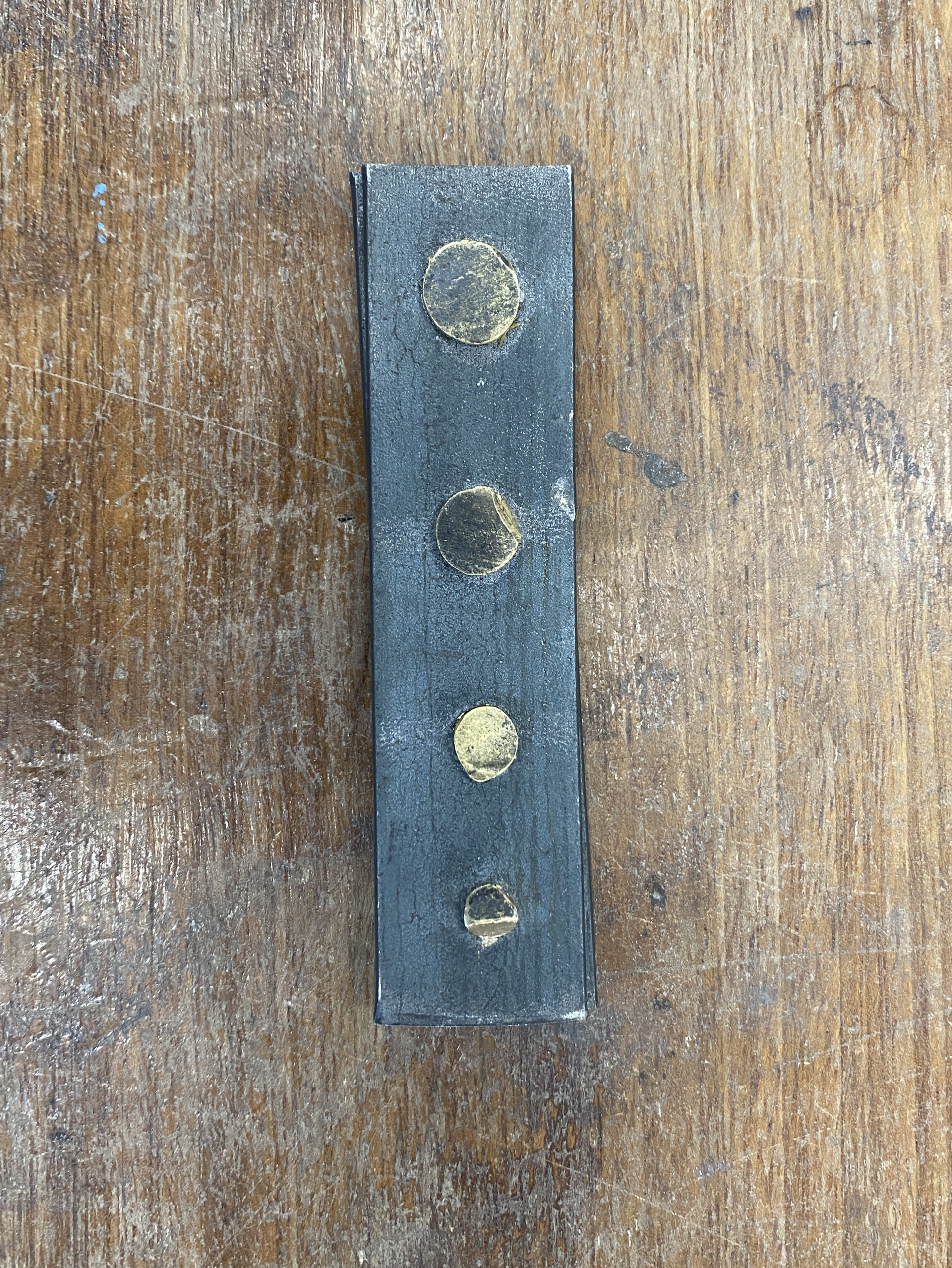
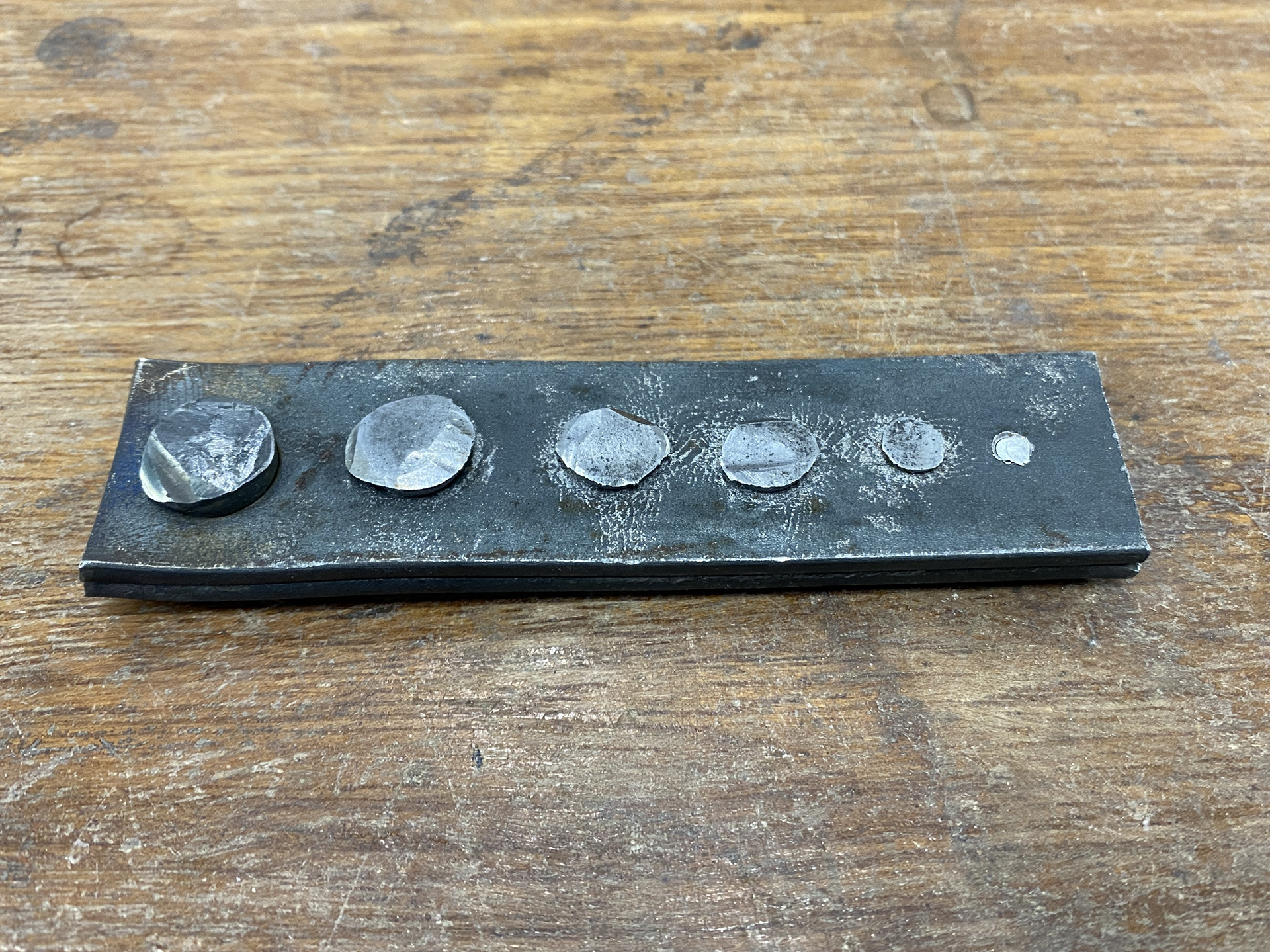
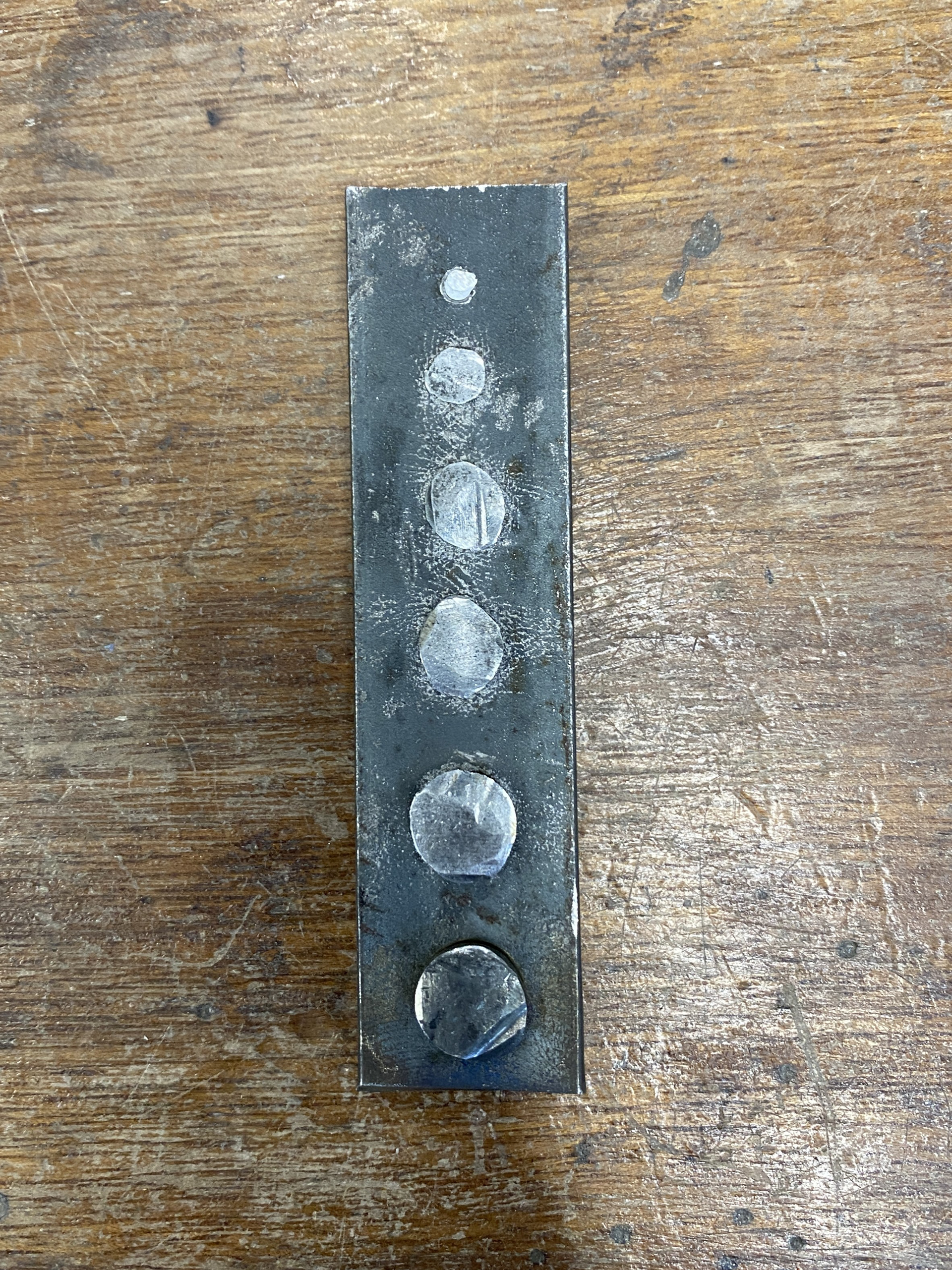
I tested different diameter brass rods (5,6.5,8,10mm) and steel rods (3,4,5,6,8,10mm) and found that I liked the 8mm the best when using the 25mm wide flat bar. I also tested riveting the steel hot using the traditional method but found that I didn't have the tooling and experience required to create a uniform and secure connection.
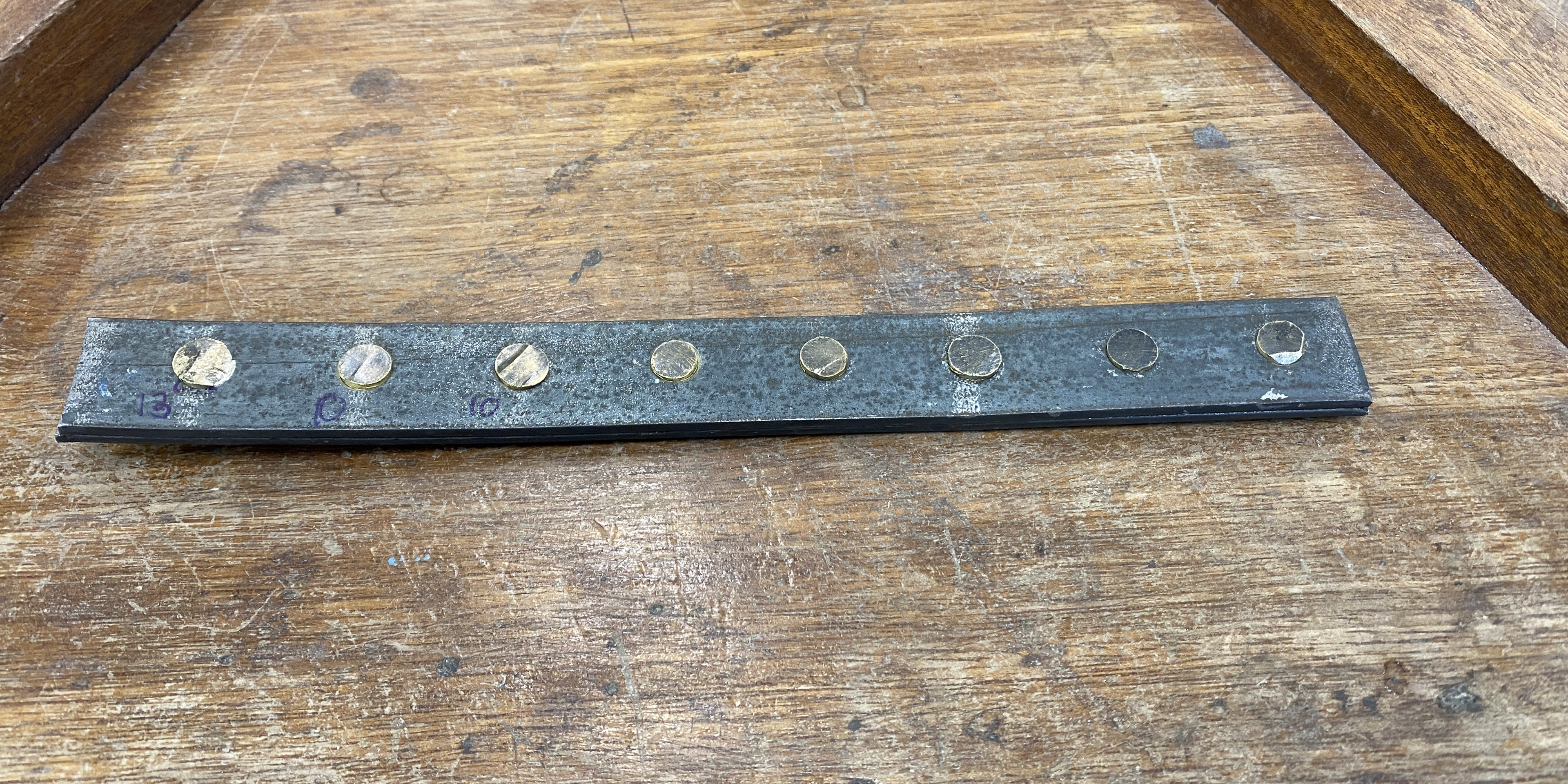
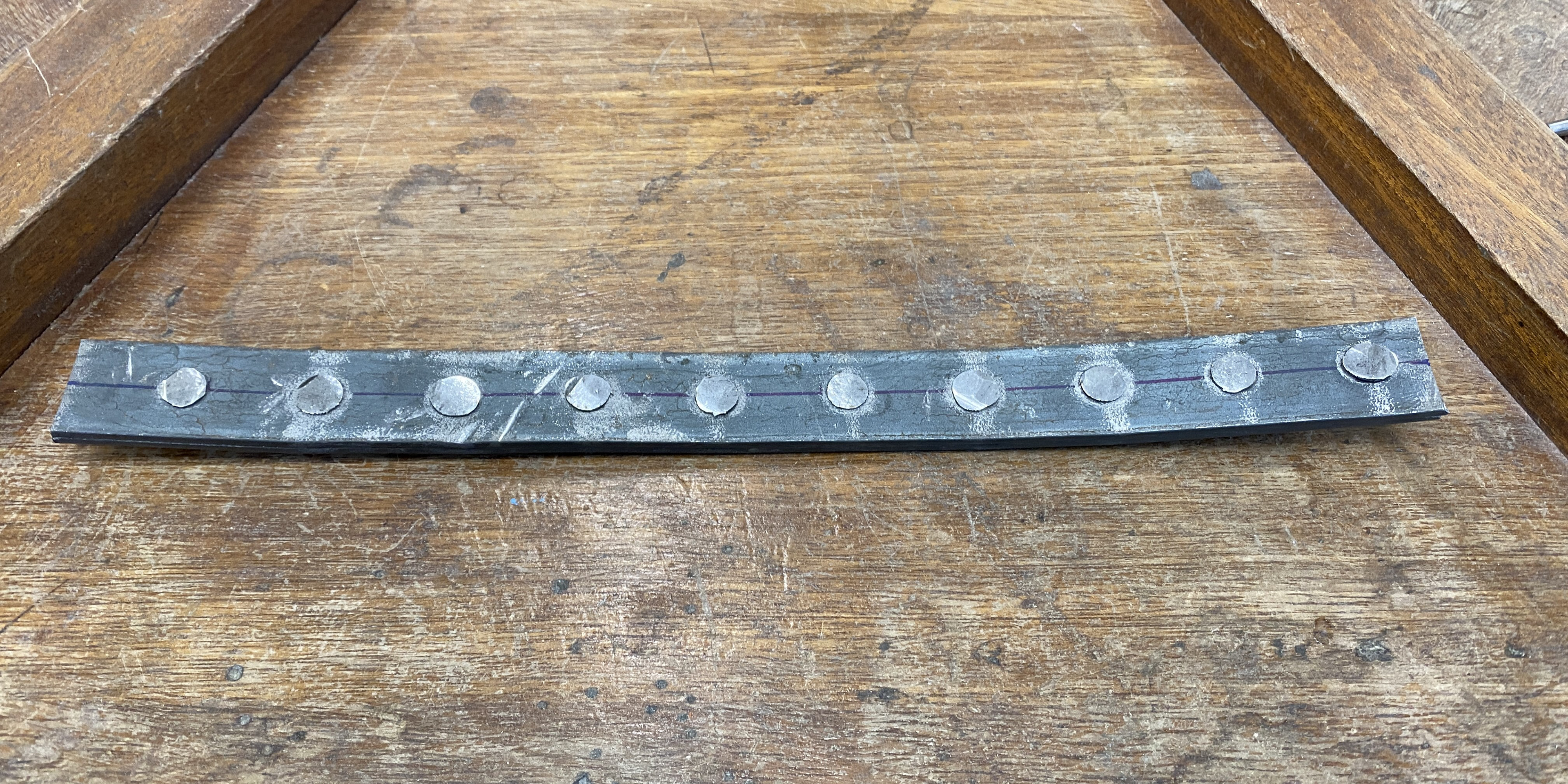
I tested the 8mm brass and steel further and found that I couldn't achieve a consistent brass rivet without it cracking. Additionally, I preferred the steel rivets as they don't draw attention away from the overall design or decorative detailing.
However, I found it hard to do the steel rivets cold when connecting sheet for the decorative details. Therefore, I need to preform one side of the rivet.
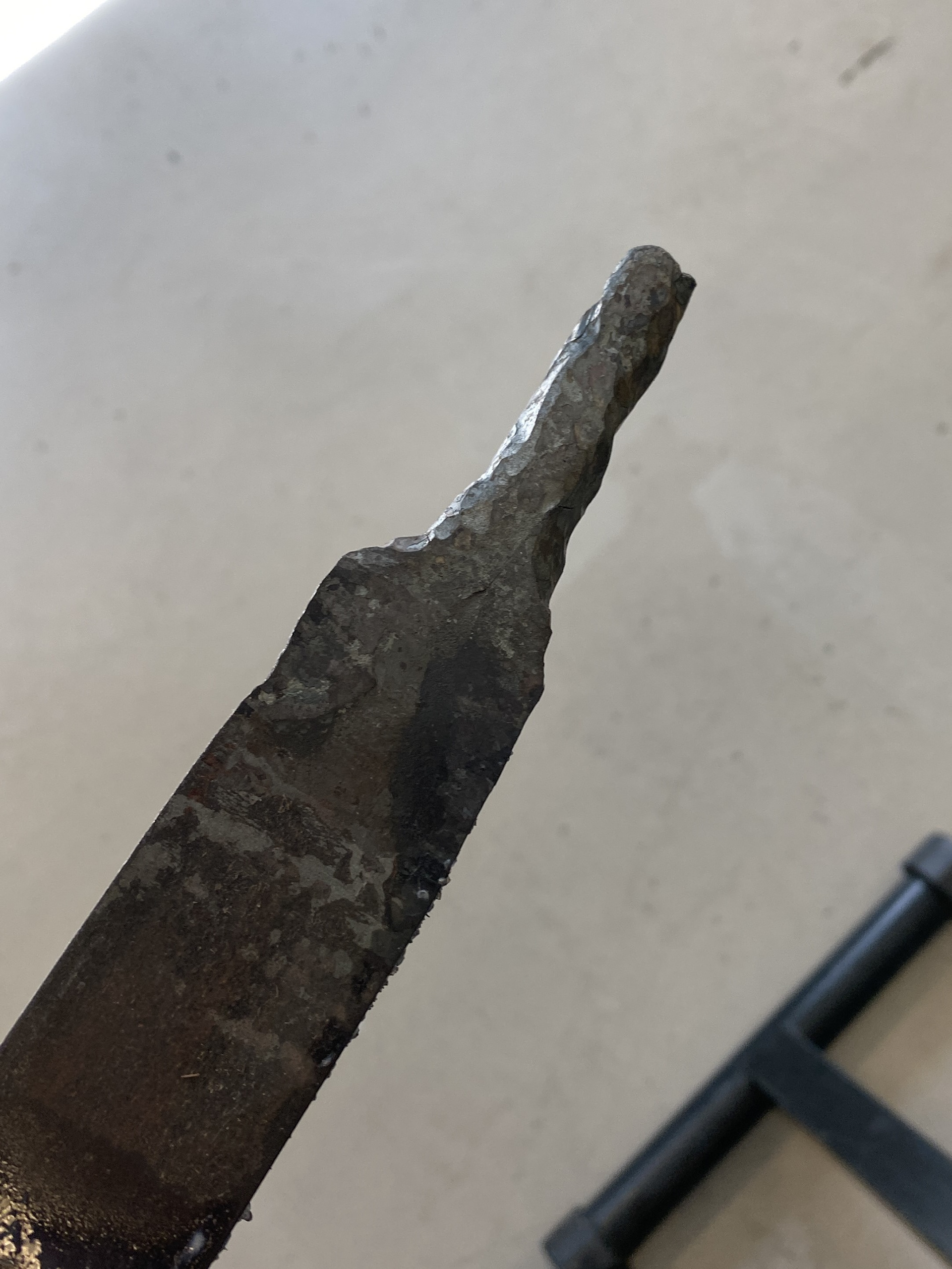
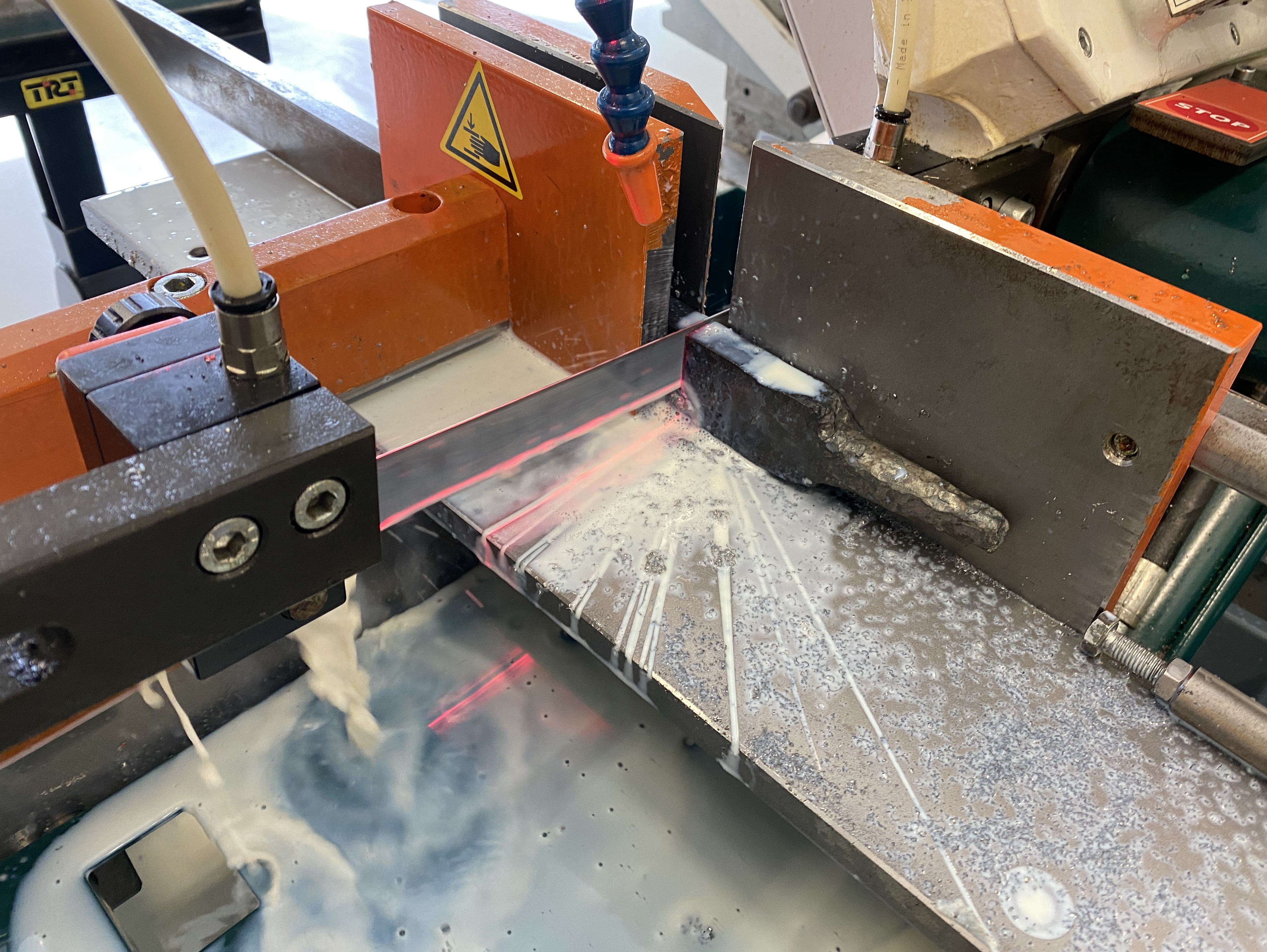
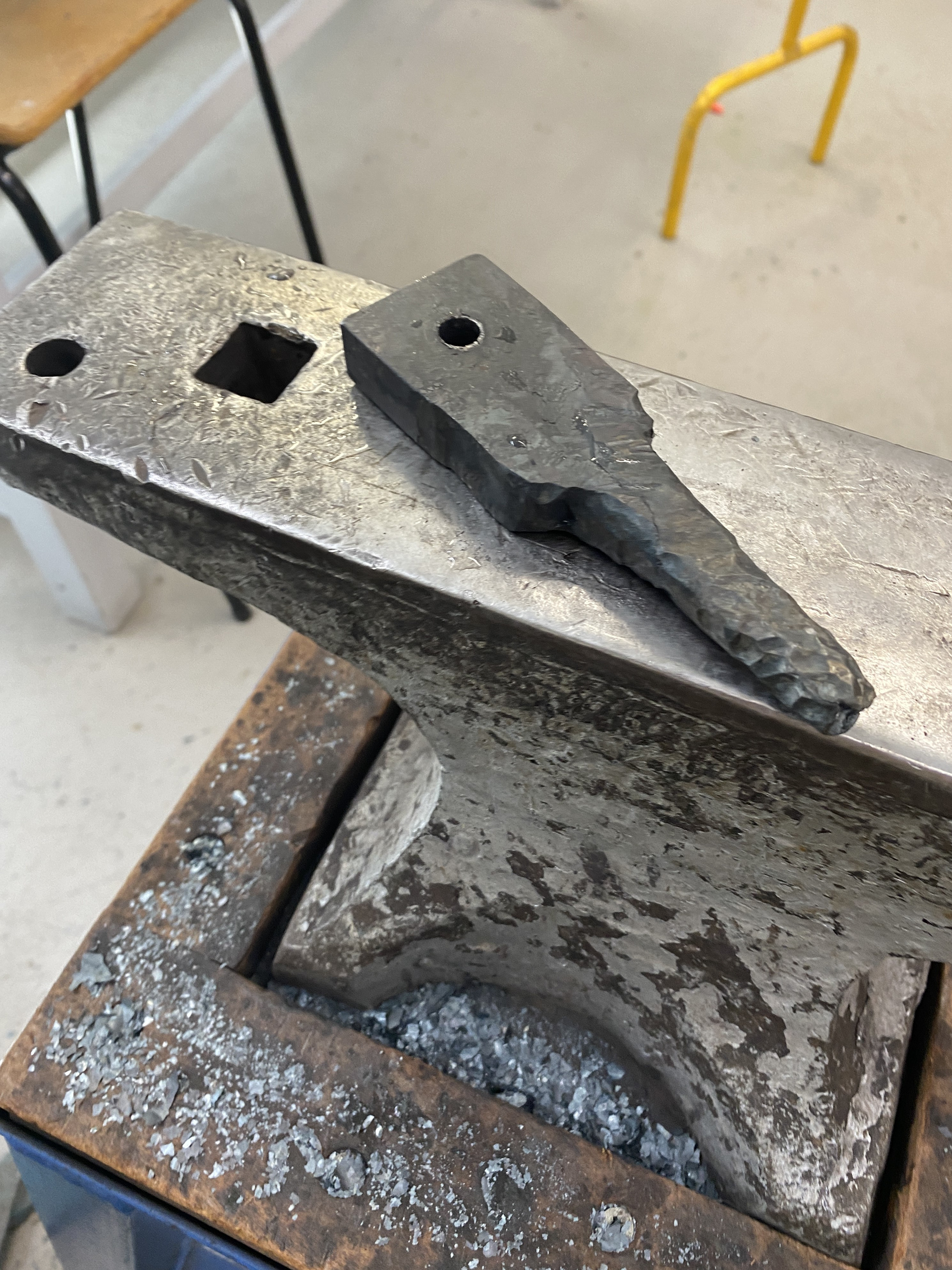
I developed a tool to help me mushroom over one side of the rivet. I forged out a handle by isolating the material over the face of the anvil and drew it out into a rounded profile. I then cut the required material off in the horizontal bandsaw and drilled a 8.5mm hole using the pillar drill.
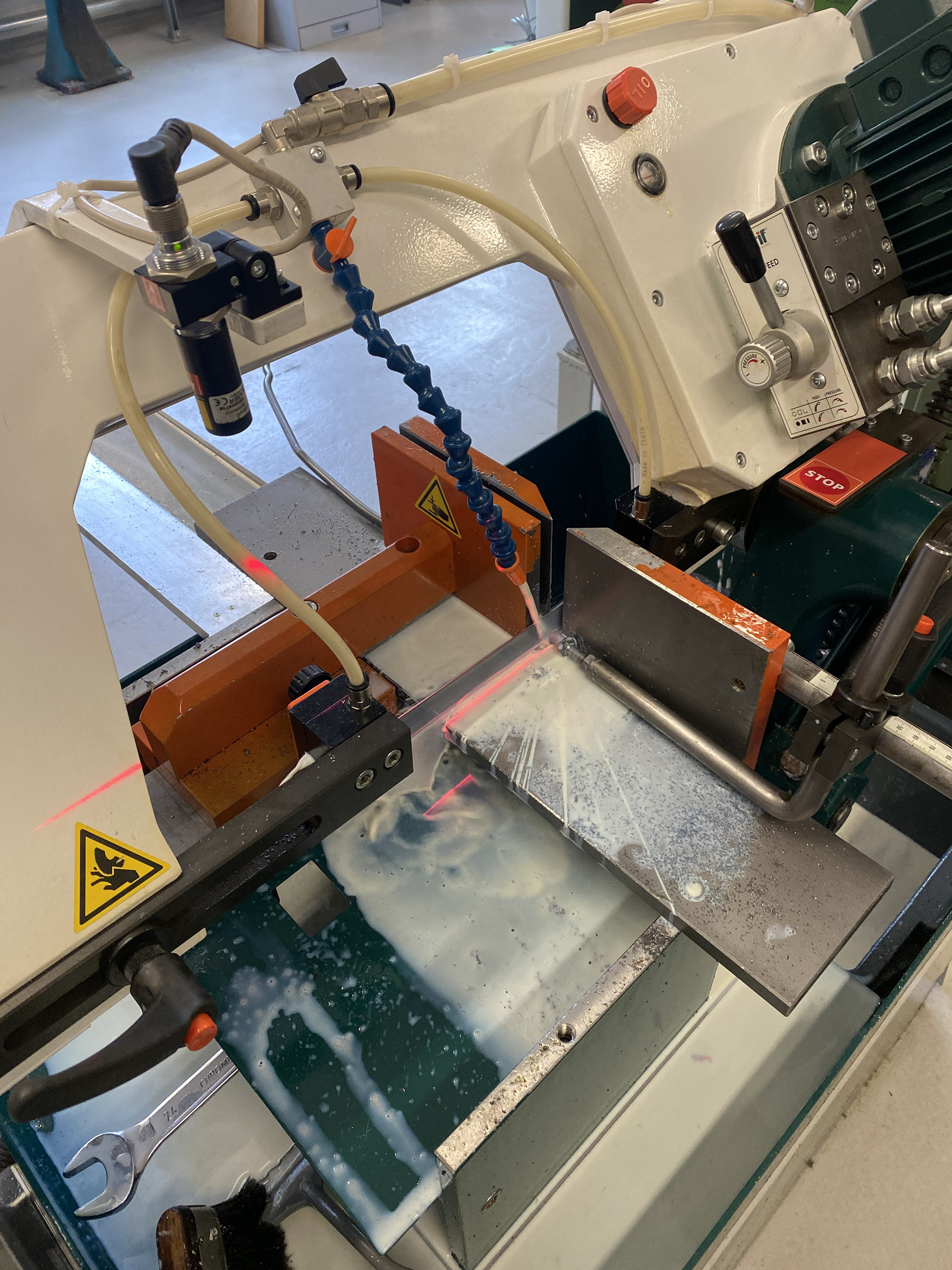
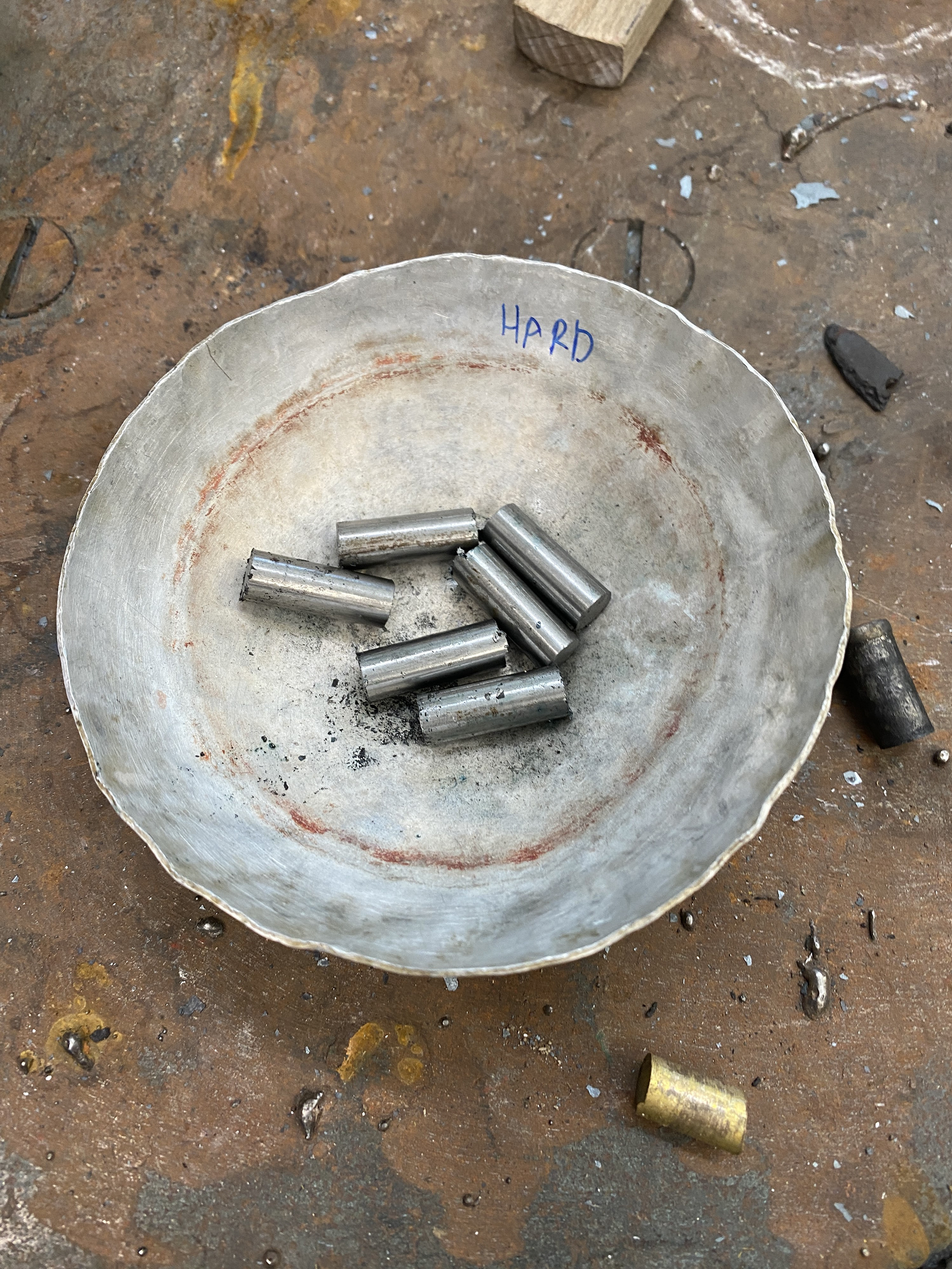
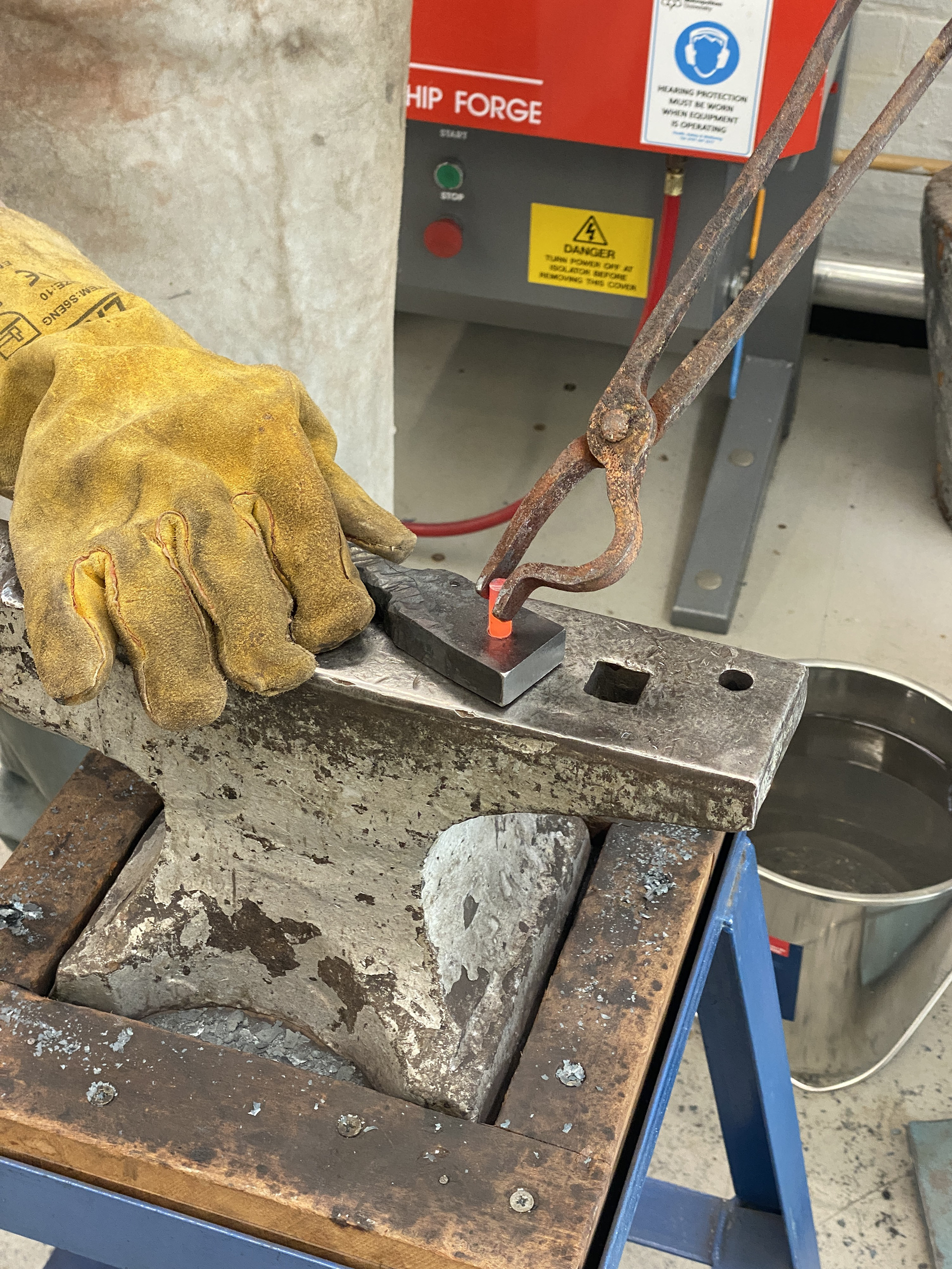
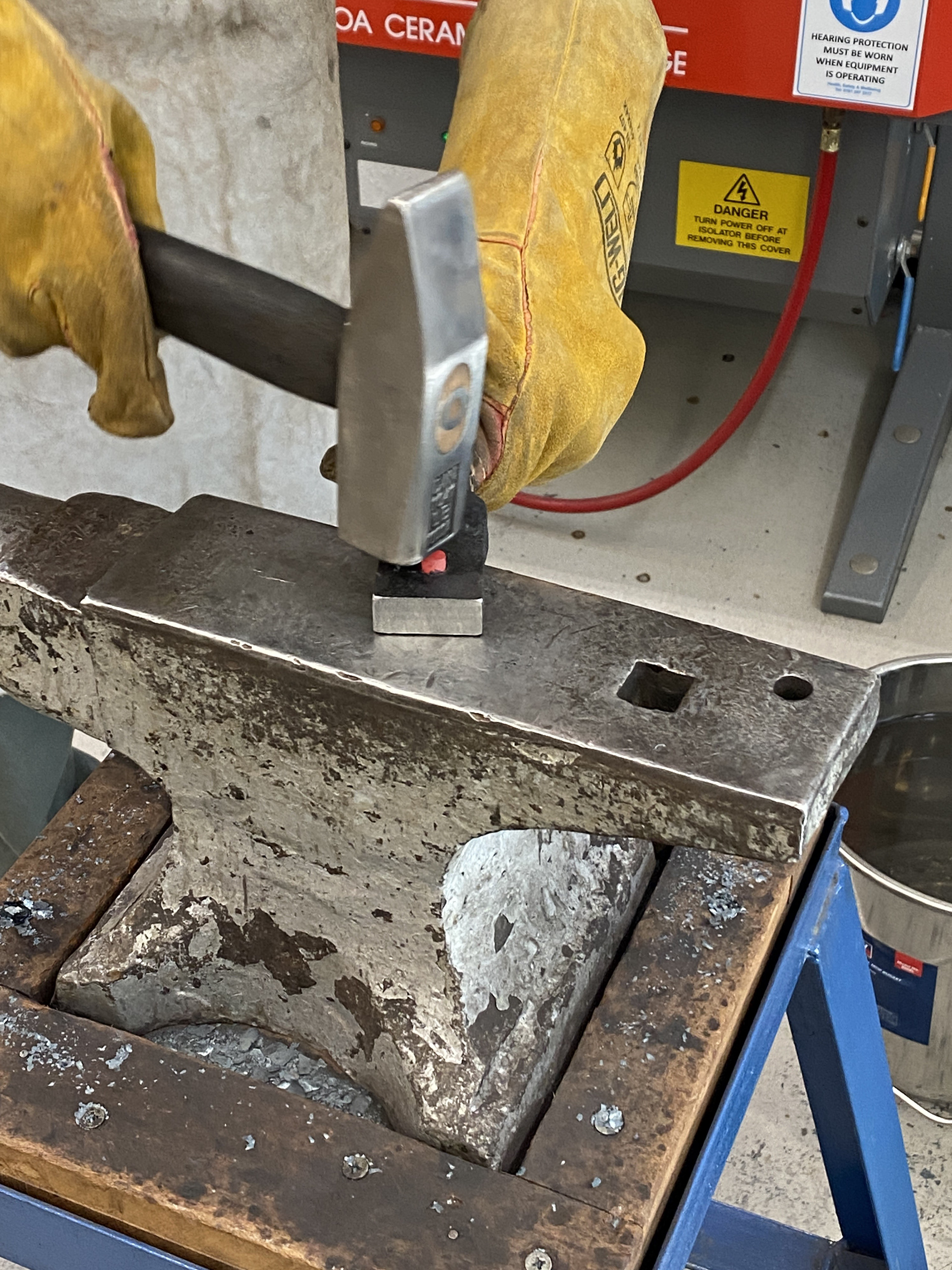
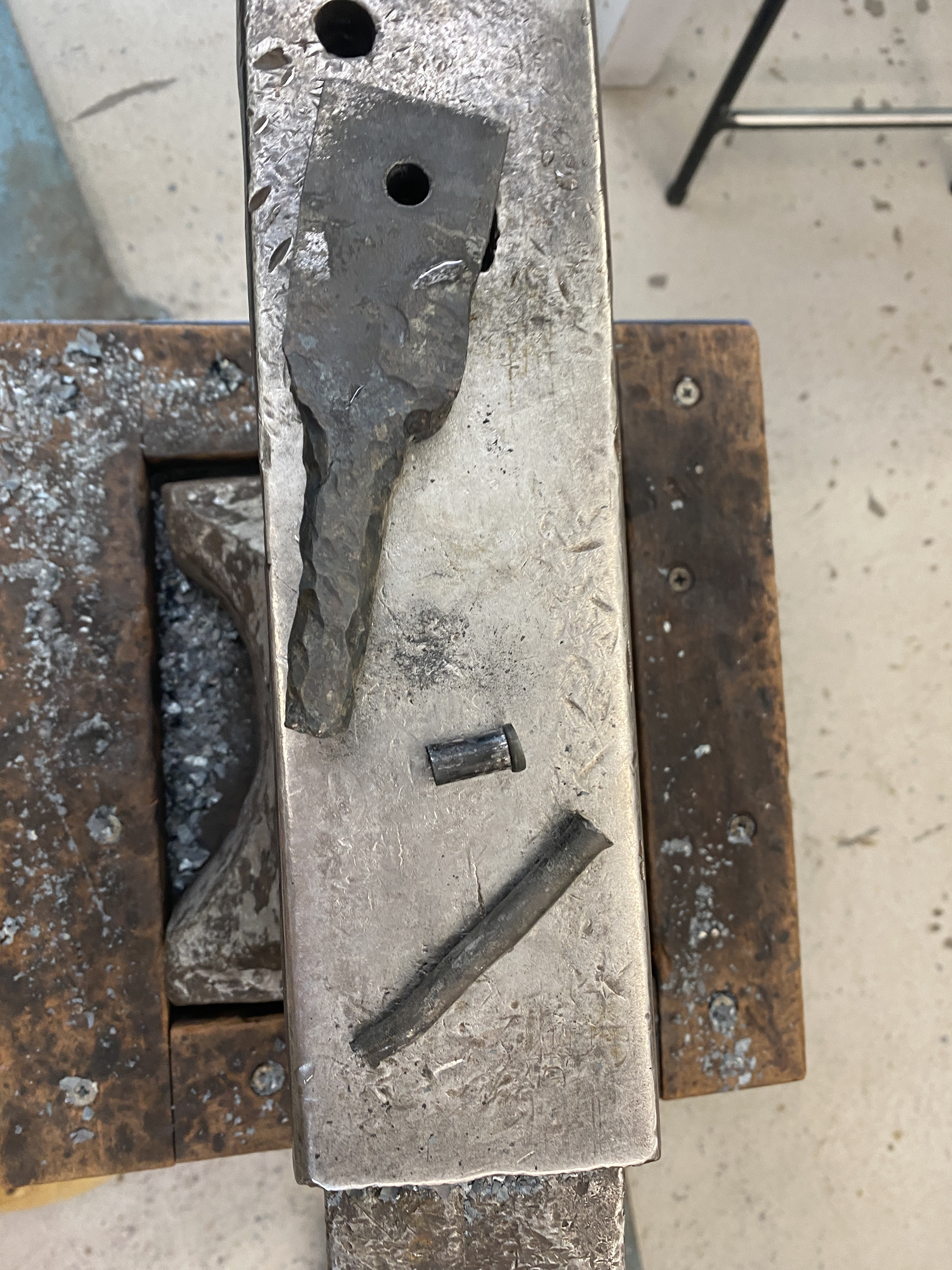
I cut 22mm long steel rod that I then heated in the forge and mushroomed over. I also forged a punch to help hammer out the rivet.
Refining decorative details
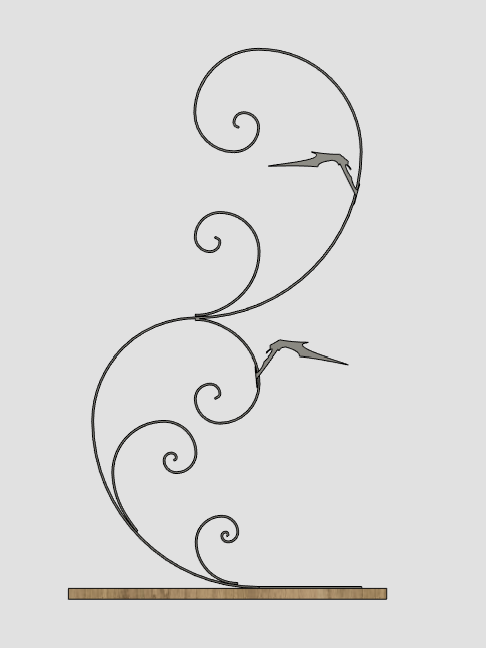

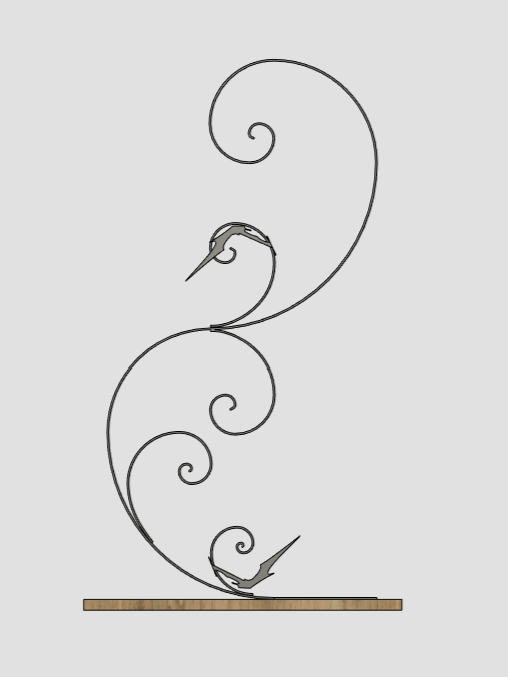
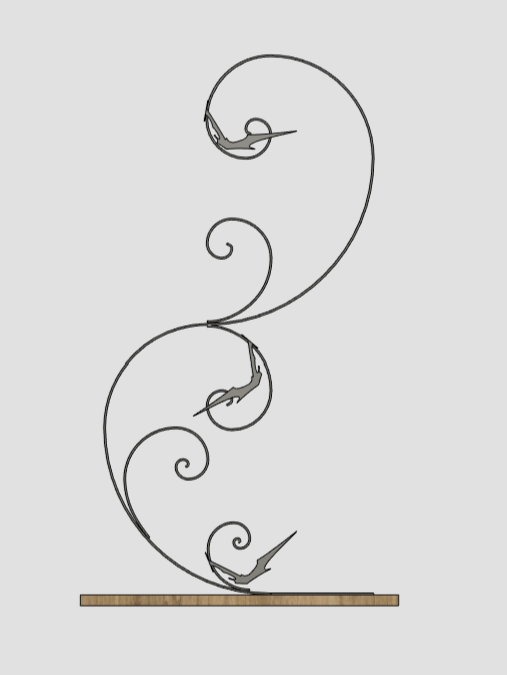
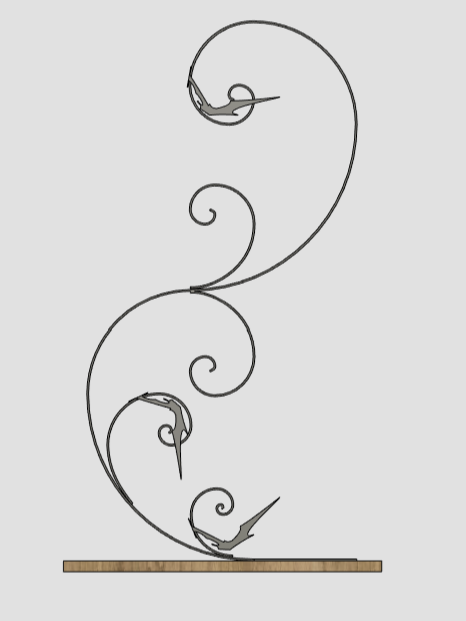
I used my CAD model to experiment with different placement and combinations for the decorative details. I found that I needed to stick with using sets of three to keep a uniform design. I think the design on the right is the most successful as it is both balanced but also placed the weight at the base, grounding it.
Riveting the scrolls and decorative details together
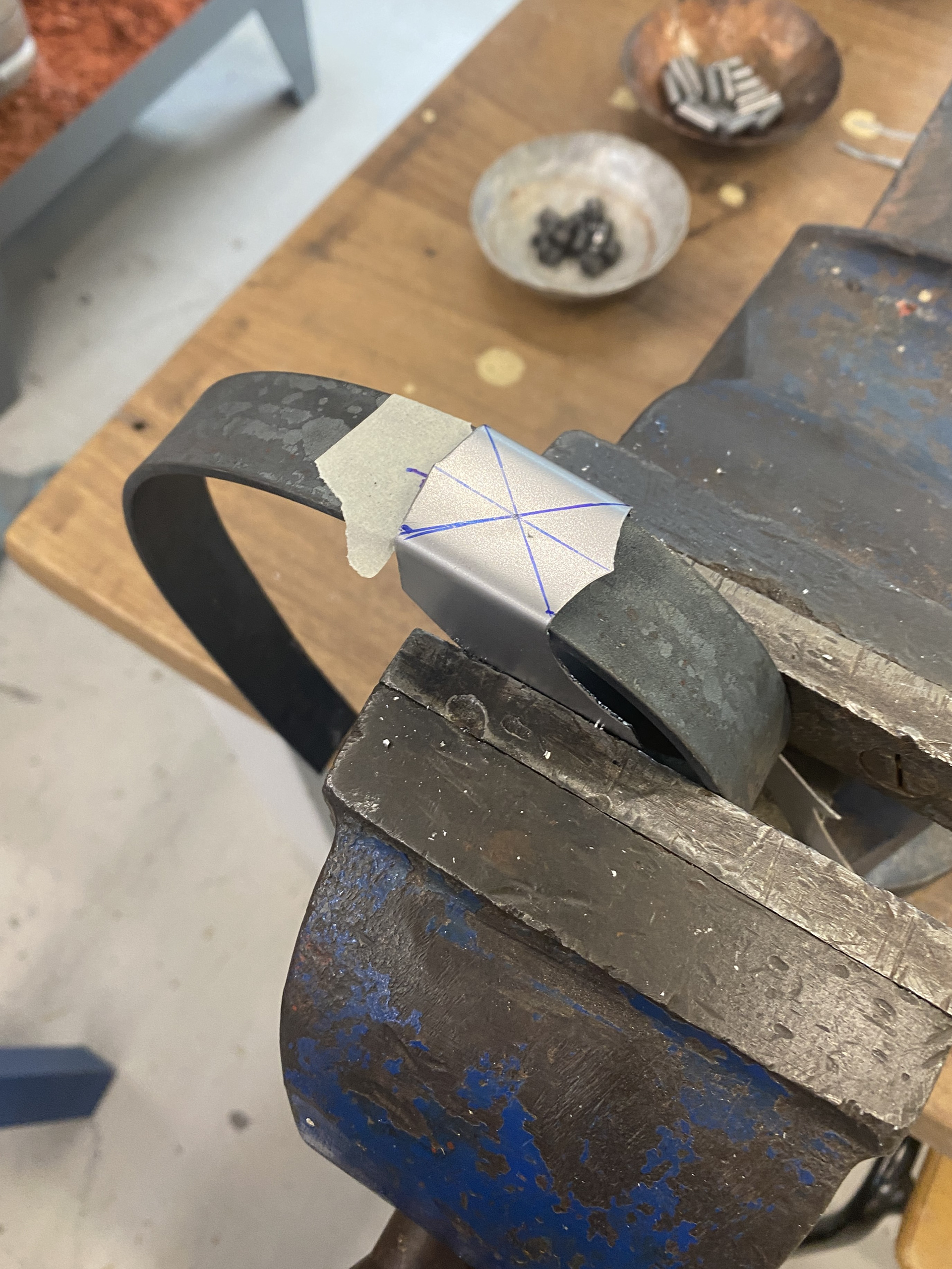
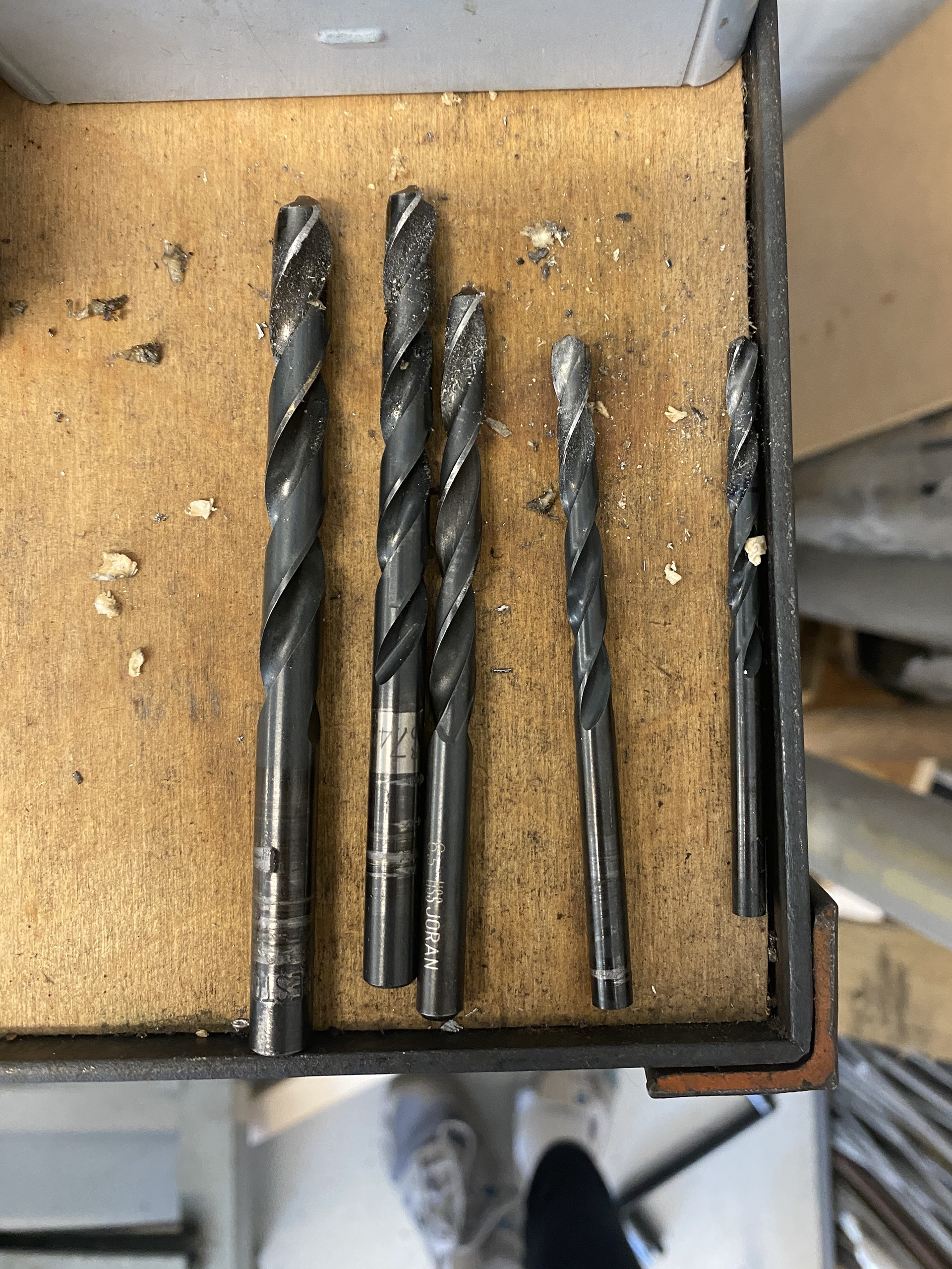
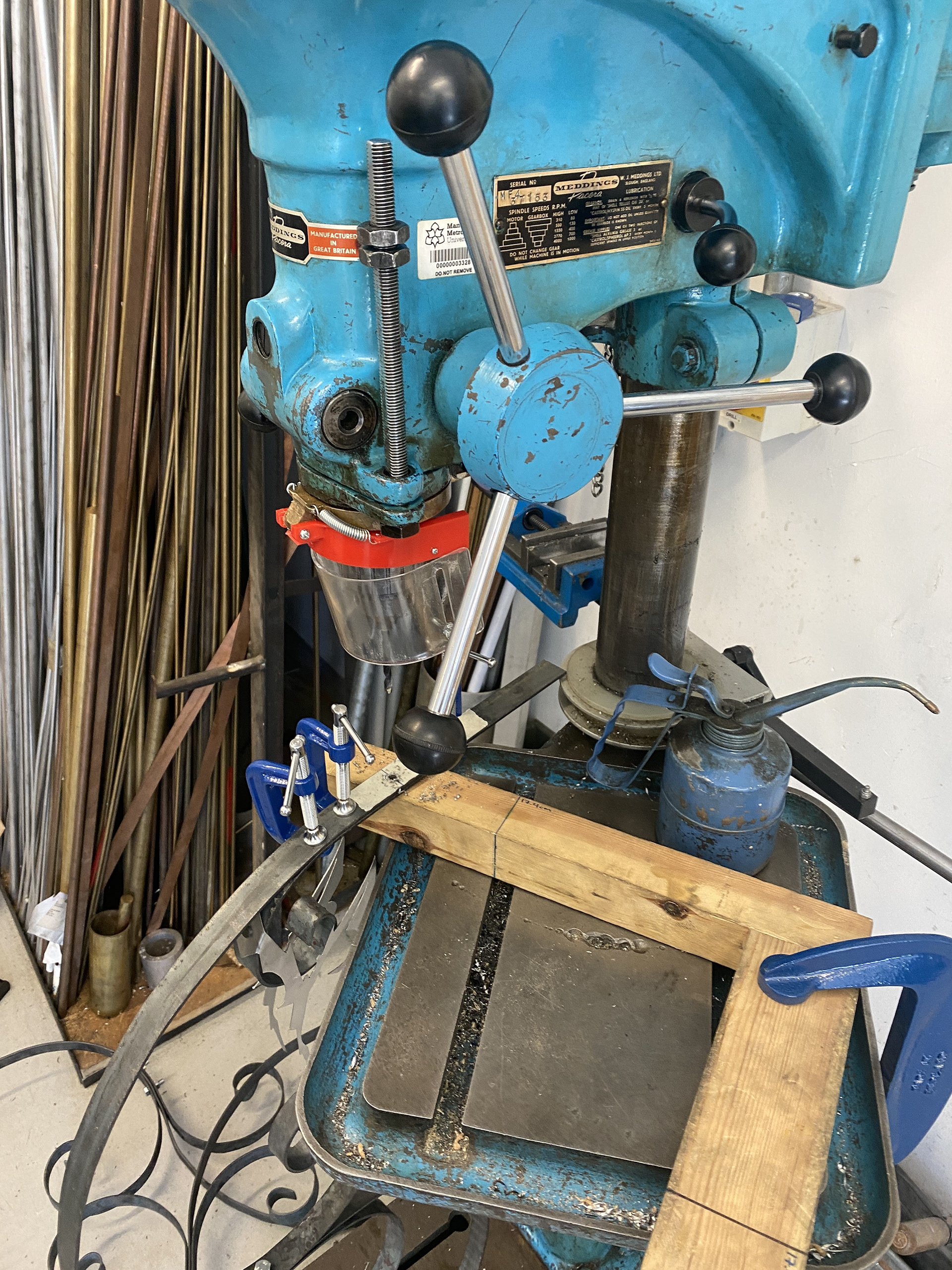
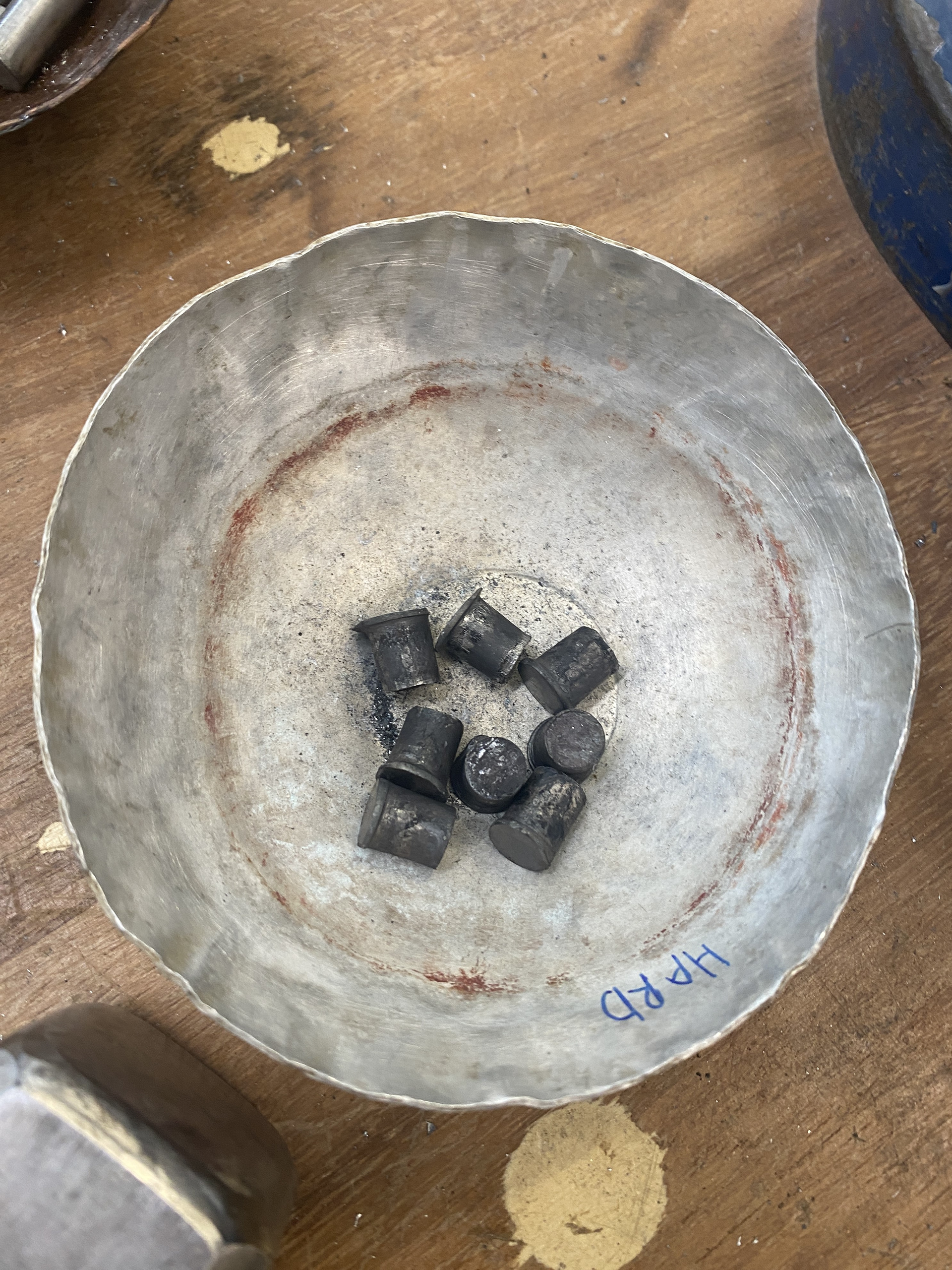
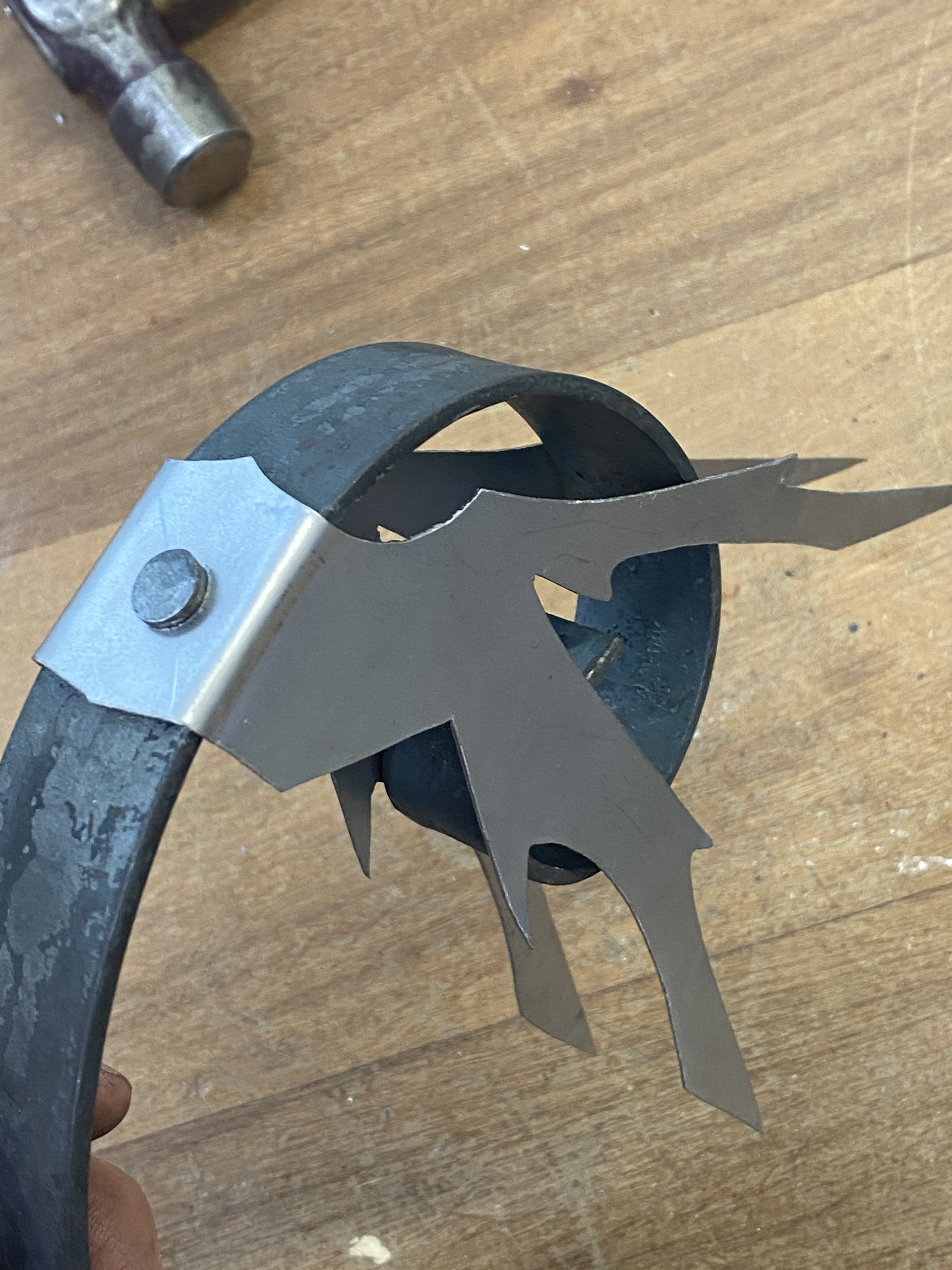
To join all the components, I marked the locations of the rivets and drilled them on the drill press. I had to slowly increase the size drill bit up to 8.5mm so that the piece wouldn't overheat or break the bit. I then hammered the preformed rivets using the horn and face of the anvil.
Refining the base
Reflecting on the Renderings of my CAD design I found that the base was unconsidered and an afterthought. Therefore, I explored other options through designing in CAD.
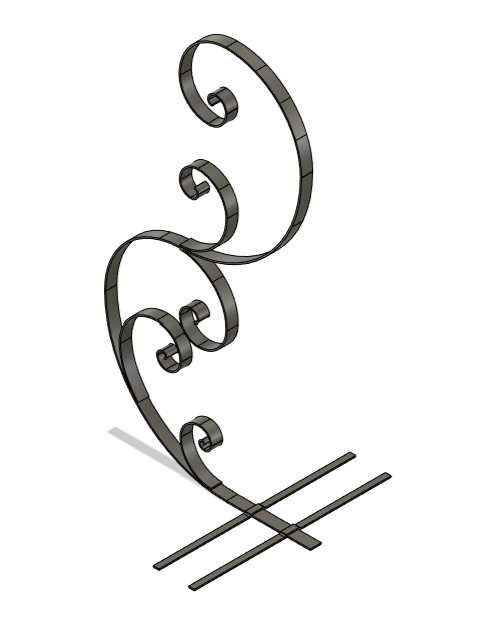
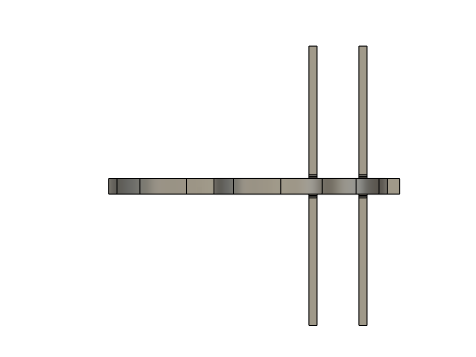
I looked at using steel to create a homogeneous design, with a cross to stabilise. However, the addition of multiple planes distracted from the initial structure.
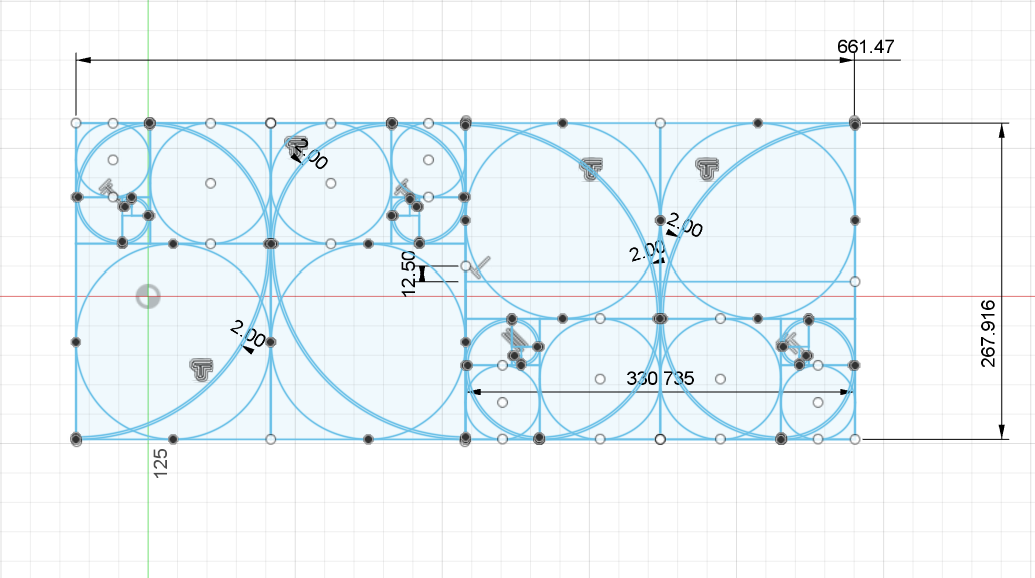
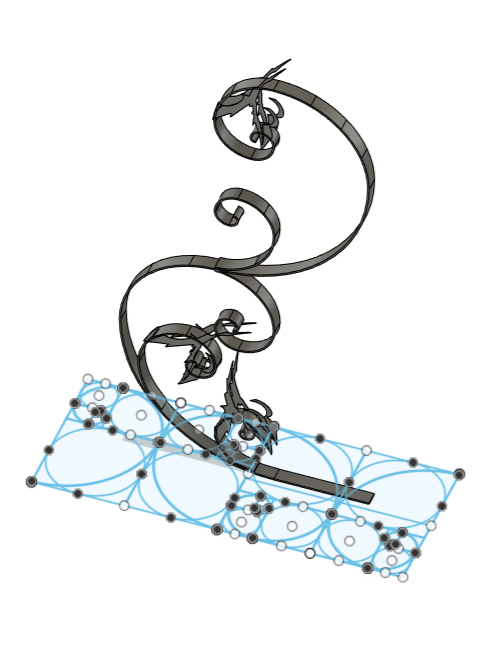
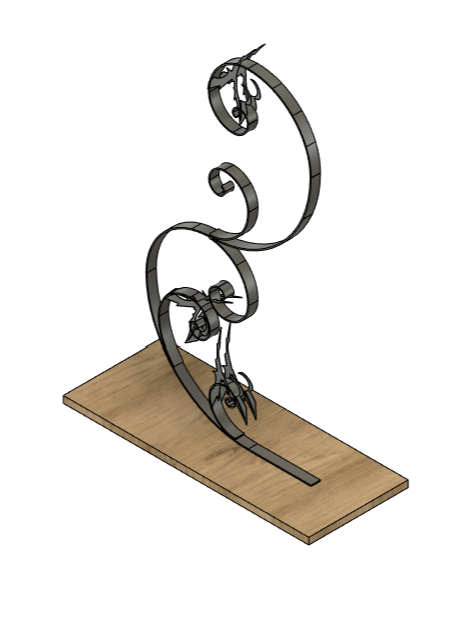
I returned to using the Golden Ratio so that the base was proportional to the ironwork.
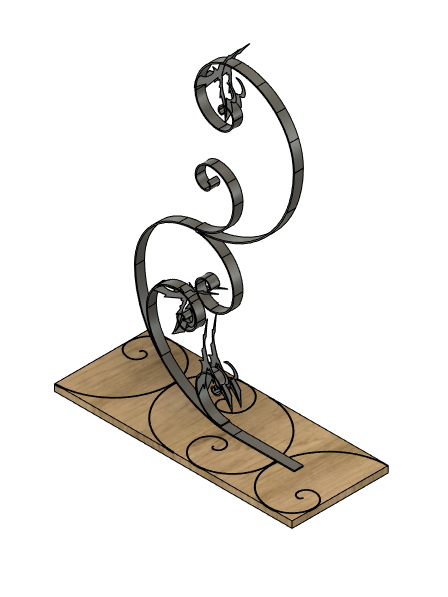
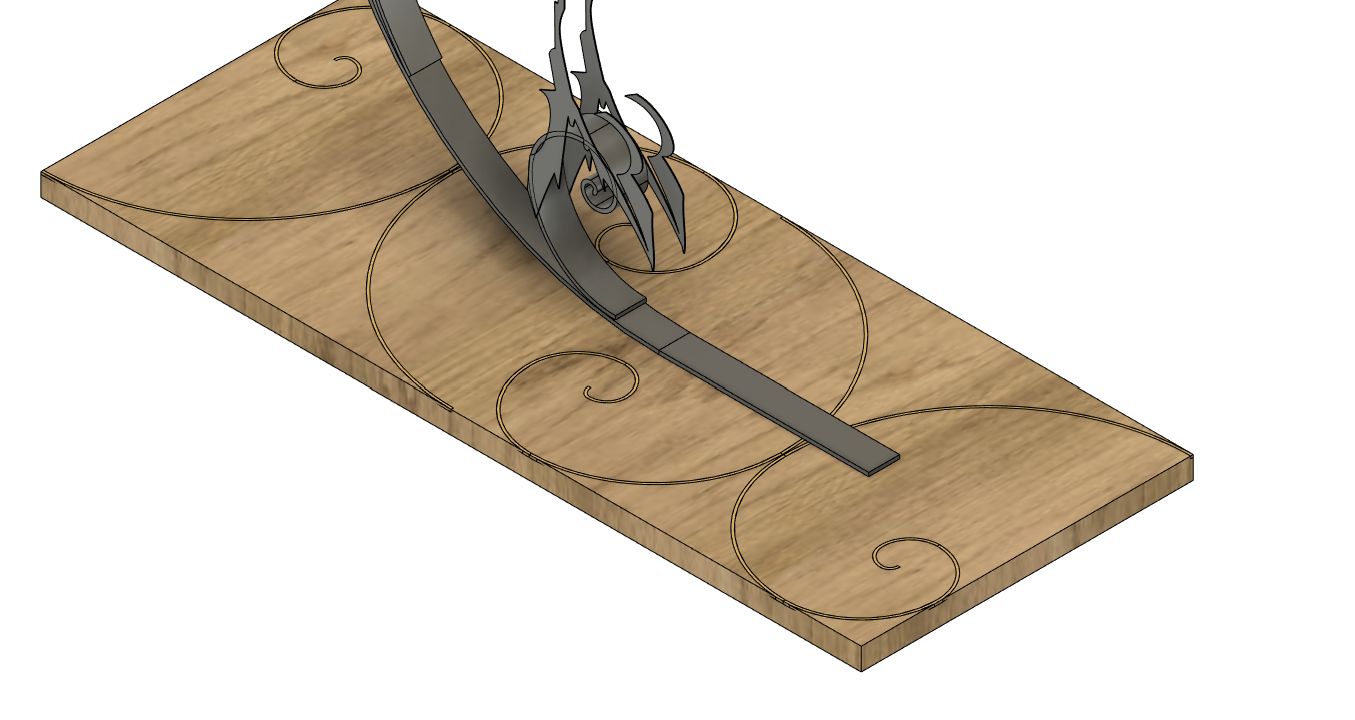
I investigated bringing the Golden Ratio scrolls onto the base through brass inlay. However, I found that this felt too simple and forced.
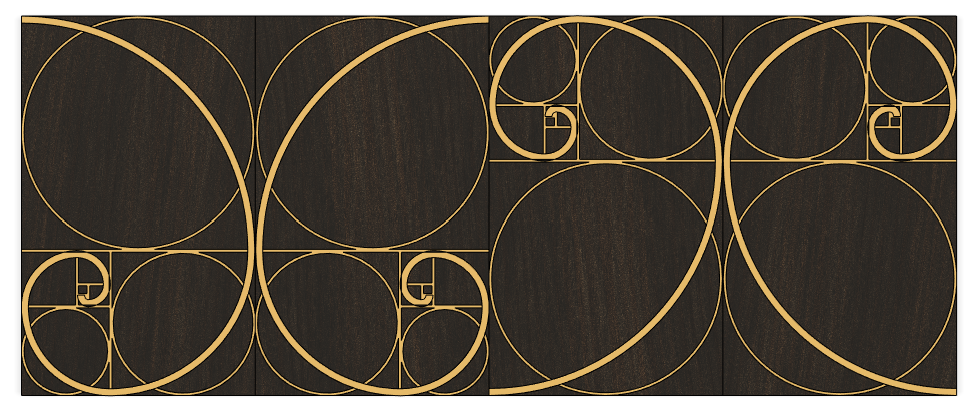
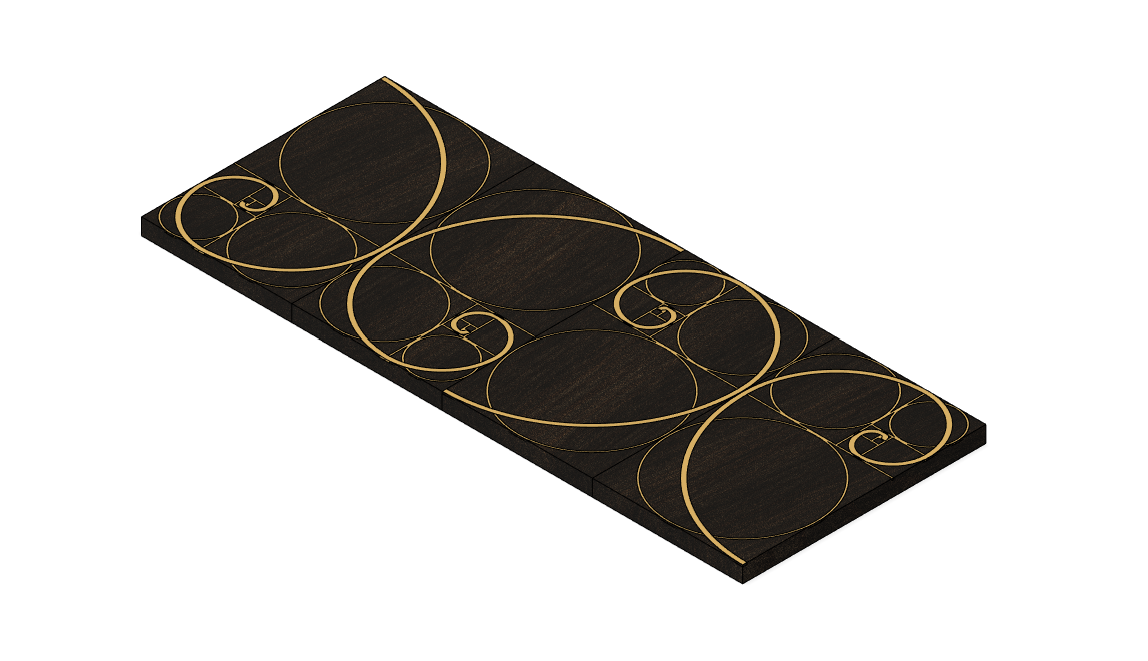
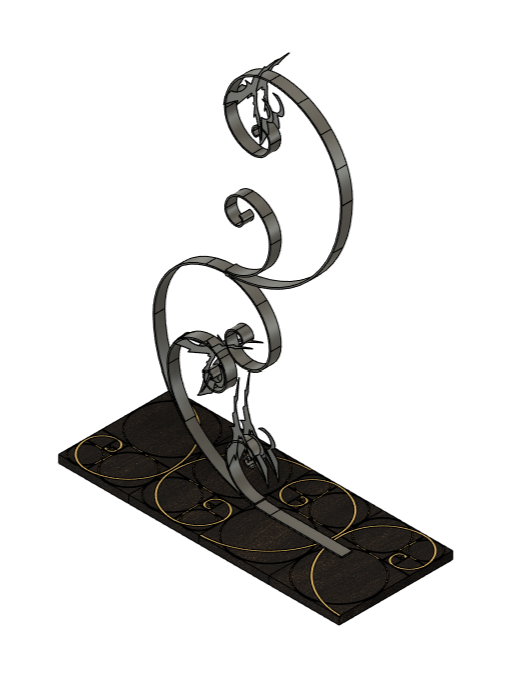
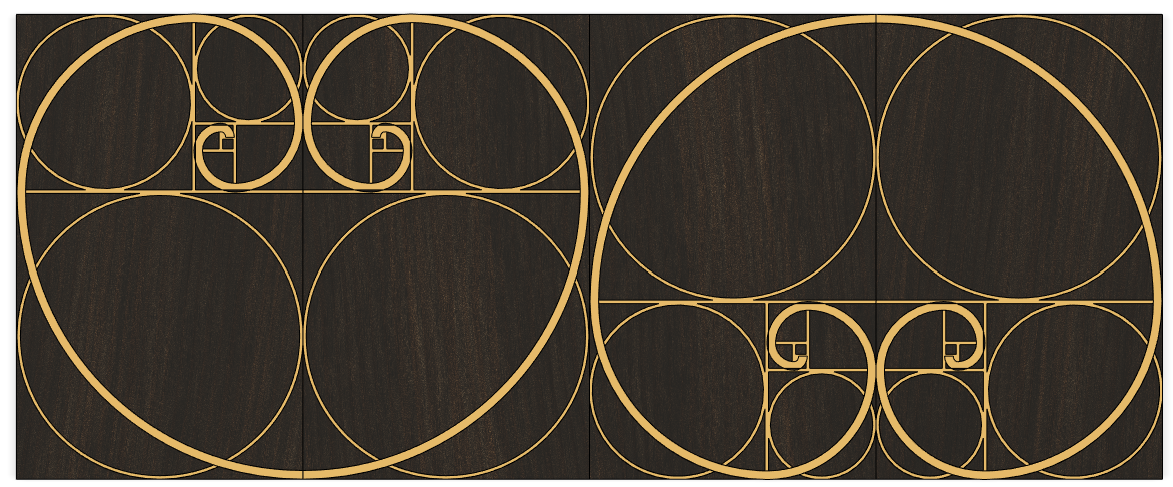
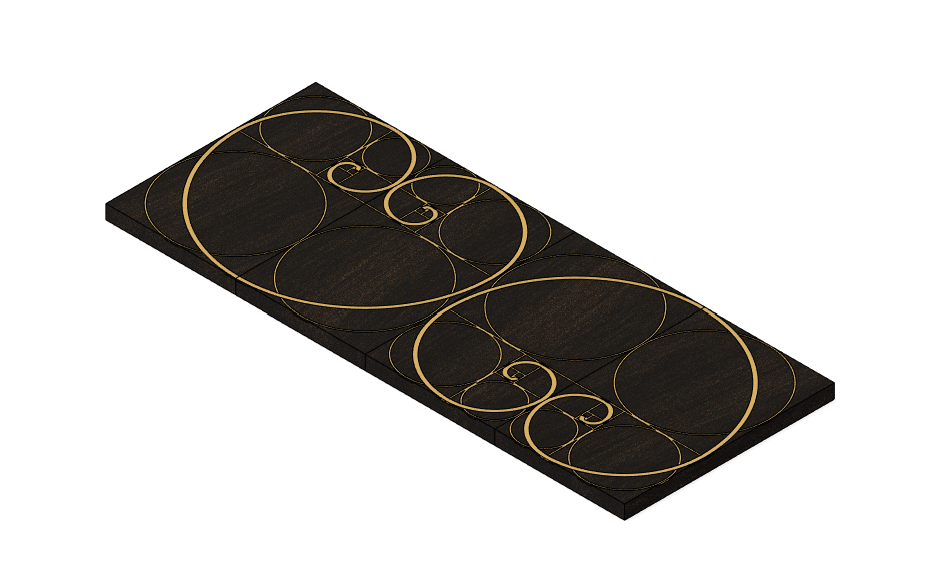
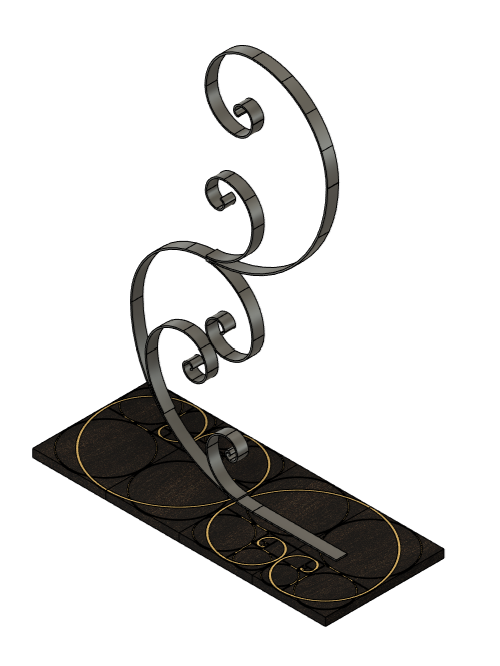
I experimented with introducing the mathematical construction lines into the brass inlay design. However, I felt that all the designs that added pattern or detail to the base distracted from the ironwork.
CAD rendering of final outcome
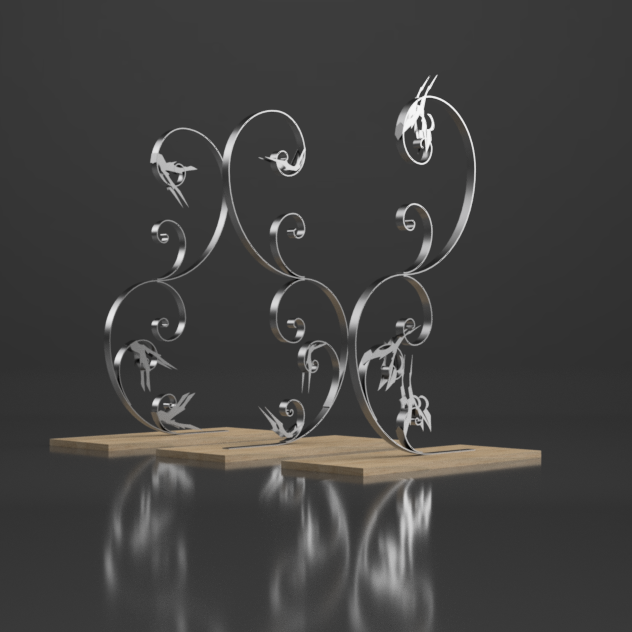

For the base I decided that a simple ash veneered MDF rectangle was the best option. I would have liked to use real hardwood but this was too expensive.
Recording the manufacturing process through sound
Throughout the making process I recorded the sounds and layered them over my audio tapes from the Parsonage. I looked at curating an experience that chronologically follows the production of the piece capturing the energy that it takes to make ironwork.
Despite this being a solo project, collaboration was a major way that my process developed and adjusted over this part of the project. I found the group crits and tutorials a great way to explore other approaches toward the development of my pieces. I think that the variety of different practice coming together introduced me to many different angles and directions that I wouldn’t have previously explored. One major influence was the importance of narrative to the illustration students and their desire to direct or manipulate a story. I think this pushed me to explore how I could direct and enhance my own narrative from the Parsonage through the introduction of sound and light; elements that I haven’t previously utilized.
Additionally, looking at how the textile students extracted forms and colours and transformed them into pattern, encouraged me to investigate abstraction. Initially I was hesitant to do so as I felt this would drift too far from the original inspirations of the Parsonage. However, I saw my abstractions as my interpretation of the source material and looked to introduce narrative through sound and light. I explored a variety of different ways to create new abstractions from my initial photography and felt that this process could have been perpetual, continuously producing new and unique forms. I enjoyed experimenting with light, capturing an object’s shadow rather than the physical form.
I utilized these abstractions as decorative details to enhance as simple curved structure. I explored the use of the Golden Ratio as a naturally perfect system to incorporate the concepts of repetition and rotation from the ironwork at the Parsonage. This produced a design that investigated movement, drawing the viewer’s eyes around and through the piece. The repetition and rotation of three pieces invites investigation and movement around the space.
The design was intended to explore simplicity through form and manufacturing, using simple blacksmithing scrolling techniques. However, through my material testing I found that the Golden Ratio wasn’t compatible with this technique. Therefore, I developed a series of jigs that allowed me to consistently and repeatably forge the scrolls. Additionally, I made tooling to assist with making the steel rivets that I used to join all the ironwork together. This process of developing and refining tooling is an area that I haven’t explored much in the past and feel that it would be a good way to improve my practice moving forwards.
During the manufacturing and practical refinement of my design, I captured the audio of each step and explored editing my own soundtrack. I followed the chronological production of the piece and sought to portray the energy required to create Ironwork. I also layered the birdsongs from the Parsonage to link back to the two-sided atmosphere of harmony and oppression.